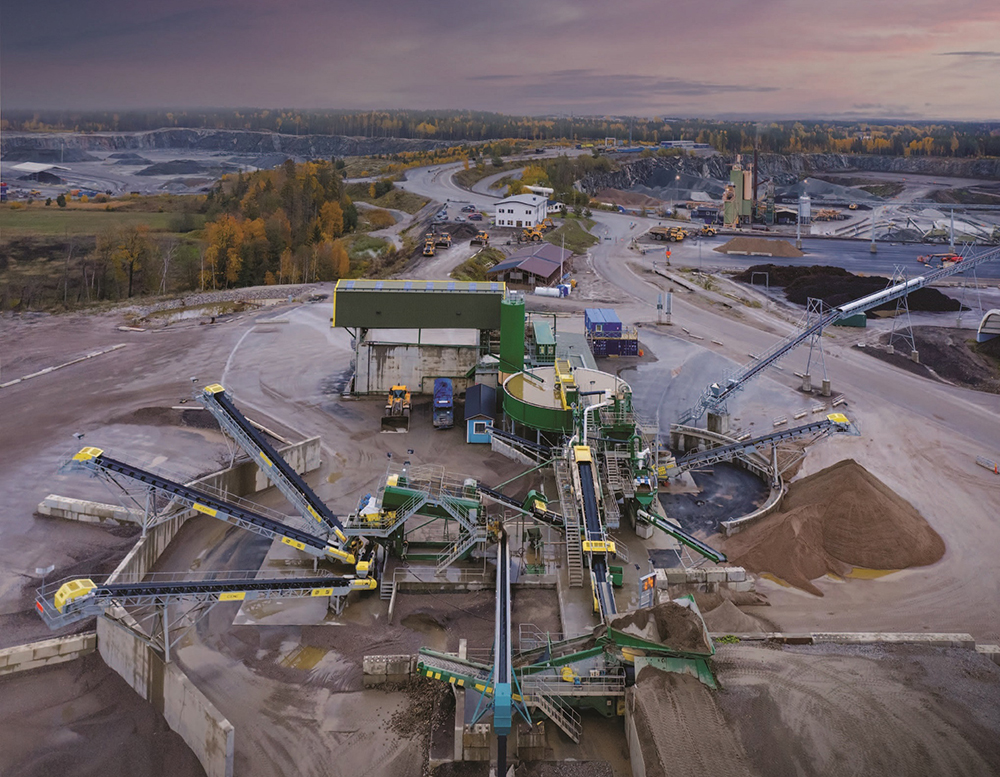
CDE, the global provider of sand and aggregate wet-processing solutions for the natural processing and waste-recycling sectors, will highlight the role of its technology in supporting the circular economy and zero-waste agenda at this year's bauma exhibition in Munich, Germany (24-30 October).
As the construction sector continues to cope with the availability and cost of raw materials, CDE says it will demonstrate the potential of construction, demolition and excavation (CD&E) waste to address the challenges facing the sector.
On October 26 and 27, it will be joined on stand by a number of its European customers for a series of round table discussions on the future of recycling, and, as part of the bauma exhibitor forum on 24 October, will deliver a lecture on the topic of Creating valuable in-spec products from CD&E waste.
CDE's head of business development for North West Europe, Eunan Kelly, comments: "In the current economic and social climate, with materials costs rising, resources depleting, and regulations calling for the adoption of sustainable solutions, we should look to the technology of today to produce the sustainable construction materials of tomorrow; how CDE's waste-recycling solutions in their trademark blue can support the industry to transform CD&E waste into certified, in-spec sand and aggregates."
Earlier this year, a package of European Green Deal proposals was presented with a view to making sustainable products the norm within the EU internal market. The revised Construction Products Regulation (CPR) emphasises the value of construction to the EU as a key employer and economic contributor. However, it also highlights the adverse impacts the sector has on the environment, as one generating some 30% of the EU's annual waste and contributing significantly to its domestic carbon footprint and emissions.
The construction industry is a major economic driver; in the EU alone, 25 million people are employed across five million companies, according to data from the revised CPR. So, when the COVID-19 crisis gripped economies and construction output fell to some of its lowest-ever levels, it was no surprise that robust recovery plans with a clear focus on investments in infrastructure were announced by nations around the world to rebound and stimulate economic growth.
However, the cost of raw materials and their availability remains a deepening challenge for the sector.
Materials shortages and their rising costs are not entirely symptoms of the pandemic but they have been exacerbated by it and have become more acute, CDE's business development manager for the DACH region, Christoph Baier, explains: "Every day we continue to extract our fast-depleting natural resources to support rapid urbanisation and our modern, technological lifestyles. Essential to this is sand, the second-most consumed natural resource after water and the most-consumed solid material on earth.”
In April, the UN Environment Programme (UNEP) published 10 recommendations to avert the impending sand crisis. It referenced how the use of sand, gravel, crushed stone and aggregates has tripled in the last two decades, reaching an estimated 40-50 billion metric tons per year (UNEP 2019).
"This, in the context of projected increases in global populations and urban living," Baier continues, "demonstrates how demand will only rise, while resources will only deplete, unless we adopt long-term attitudinal, regulatory and technological change to ensure not only the sustainability of companies within the construction sector – and with it the livelihoods of those employed within it – but also the sustainability of the very planet.”
While COVID-19 economic recovery packages may help to stimulate growth, they must be conditional on building back greener, more sustainably, Baier adds.
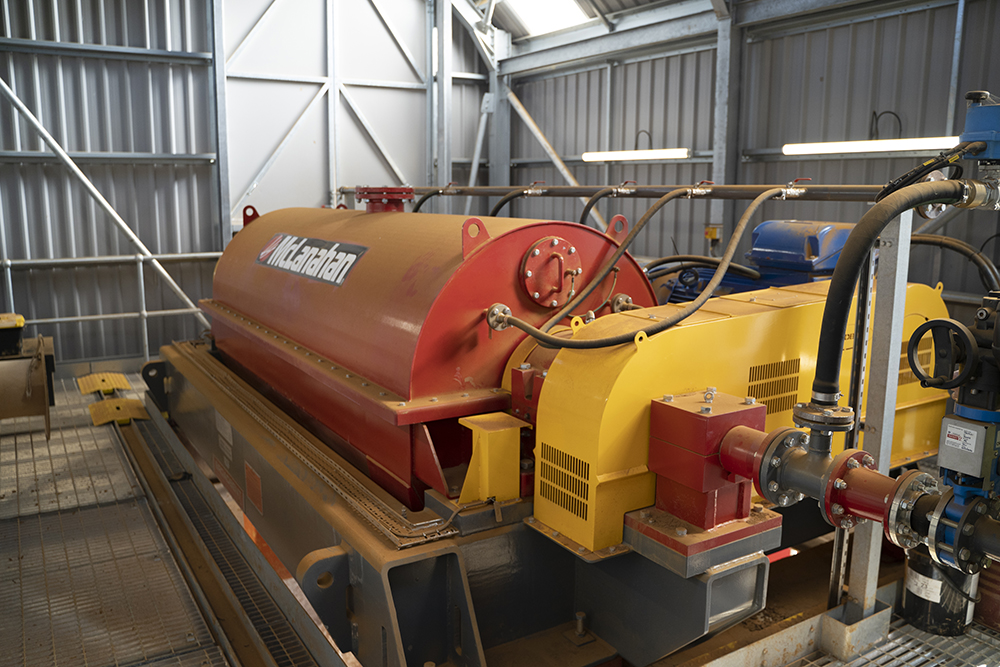
A circular approach is the only answer, Kelly corroborates: "It can be the means to equip us with the resources needed to supply a sector charged with a key role in the economic recovery while addressing our collective environmental footprint by reducing waste-to-landfill volumes and extending the lifespan of precious natural materials.”
He says the technology needed to extract recycled sand and aggregate resources from CD&E waste that are equivalent to their virgin quarried counterparts is already in operation throughout Europe.
To date, CDE solutions have supported companies around the world to divert over 100 million tonnes from landfill.
Kelly says: "Many material processors utilising CDE technology are successfully producing CE- and BSI-certified concrete products, including competitive concrete for non-structural – but still high-value – construction projects, with some applications successfully achieving beyond C45 spec."
DA Mattsson, based near Stockholm in Sweden, diverts almost 100% of its incoming CD&E waste from landfill through its CDE wet-processing operation. The company produces high-quality sand and aggregates that meet EN 12620 specification, and it supplies these concrete materials to the Stockholm construction market.
McLanahan – the US-headquartered dry and wet materials processing solutions manufacturer for quarry and mining customers - says that aggregates producers have several mechanical options to choose from when it comes to dewatering tailings for improved handling, settling pond elimination, water recovery or meeting environmental regulations.
One of these options is a decanter centrifuge, which is used to separate solids from liquid in a variety of applications. In agregates processes, one use for decanter centrifuges is to handle the tailings in the waste stream. With high centrifugal forces to induce sedimentation, decanter centrifuges separate the solid particles from the liquid in a typical waste stream coming from a wet-processing plant.
Decanter centrifuges discharge two products: a liquid that can be reused as process water upstream, and a solids cake that is suitable for mechanical handling. McLanahan says that their main benefit for processing tailings in aggregate applications is that they make handling the waste stream easier and more efficient. Processing the waste stream through a decanter centrifuge has even allowed some sites to eliminate their settling ponds or lagoons, which can be costly and time-consuming to maintain as well as taking up valuable land space.
Decanter centrifuges consist of a feed pipe that goes inside a helical screw conveyor that is surrounded by a bowl assembly. These components are then enclosed in a casing, which helps improve housekeeping and reduce noise. Discharge chutes at the bottom of the casing collect the discharged materials
Decanter centrifuges are supported on a heavy-duty base frame mounted on vibration isolators to minimise vibration and maintain balance. Other main features include the motors and gearbox, which impart the rotation of the conveyor and bowl assembly necessary for liquid-solid separation.
“A decanter centrifuge uses centrifugal forces to separate solids from liquids at high Gs ,” McLanahan comments. “The waste stream in the form of a slurry enters the inside of the helical conveyor through the feed pipe. The slurry is then released into the space between the rotating conveyor and the bowl, which is rotating at a higher speed than the conveyor. The solids in the slurry are forced to the wall of the bowl, while the liquid moves freely toward the liquid-discharge end of the machine.”
The conveyor moves the solids toward the solids discharge at the opposite end of the machine. The conveyor and bowl are tapered conically at this end to further dewater the solids before they are discharged. The solid cakes are low moisture, and they can be handled with a loader and transported via a truck to a final resting place.
A decanter centrifuge operates in a continuous process, meaning material is continuously being fed into it and material is continuously being discharged from it.
Decanter centrifuges come in a variety of sizes to handle a range of capacities. Like many aggregates- and mineral-processing machines, Decanter centrifuges are sized based on the feed and process requirements. The larger the centrifuge, the higher capacity of feed material it can handle and the more tons per hour it will discharge.
Other factors that affect sizing include the speed of the conveyor, the speed of the bowl, the angle of the tapered beach area and the pitch of the conveyor.
McLanahan states that, because of the range of sizes and capacities they come in, the cost of a decanter centrifuge can vary enormously depending on the type needed to fit the application requirements. Once a duty is determined, the manufacturer will be able to select a suitable model and provide cost and cost-benefit information accordingly.
The operational costs can vary depending on the size of the machine and how much power is necessary to process the material to the desired outcome. Power costs, too, can vary depending on location and energy supplier.
Depending on the material being processed and the goals of the site, chemicals may need to be added to the feed to aid sedimentation.
Decanter centrifuges are fully automated, meaning they require minimal operator intervention, so labour costs will be less with these machines compared to other mechanical dewatering devices such as belt presses. They are relatively low-maintenance machines. For the most efficient operation, McLanahan states that they should be regularly inspected and maintained according to the manual.
Inspections should be carried out before the centrifuge is started up every day, and more in-depth inspections should take place every 2,000, 4,000, 8,000, 16,000 and 40,000 hours of operation (or every three months, six months, year, two years and five years, respectively).
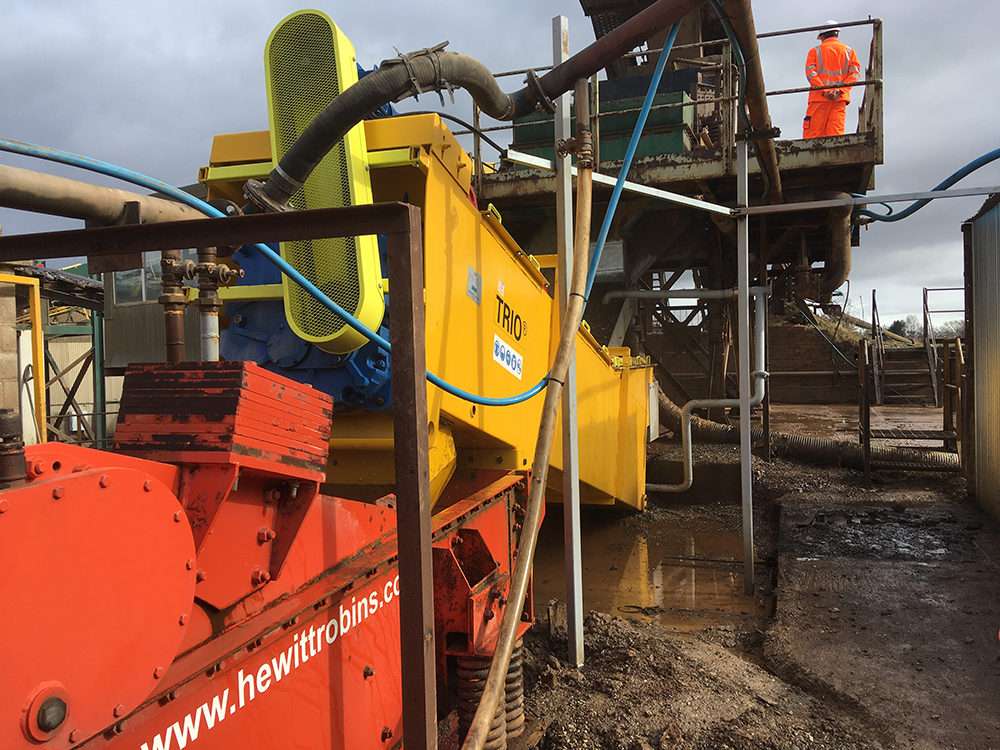
If inspections reveal components need to be repaired or replaced, do so immediately by following the replacement procedures listed in the manual. Be sure to follow all safety guidelines outlined in the manual and to heed all machine warning labels and site-specific safety measures.
“Also, be sure to keep a stock of spare parts at your facility to minimize downtime when replacement of a component is necessary,” McLanahan comments.
“Decanter centrifuges are a great option for dewatering tailings in aggregate applications to a low-moisture content suitable for mechanical handling. They are fully automated, low-maintenance, compact machines that can be adjusted to improve the solids dryness or liquid clarity, depending on the goals of the site.”
Washing plant manufacturer Weir Minerals says that its Trio coarse washer has unlocked a 12% increase in production at the Tudor Griffiths Group, a leading UK independent supplier of construction materials, building supplies and most recently, waste management and recycling services.
Established in 1874, the Tudor Griffiths Group utilised steam engines to increase production and continues to innovate, evolve and grow to enhance its operations for a sustainable future. During a regular site visit, the Tudor Griffiths’ team discussed its need to improve plant reliability, availability and product quality.
Tudor Griffiths’ process included a barrel washer. This ageing technology was inhibiting the plant’s overall production by around 30,000 tonnes (when compared with the production achieved in the previous year). Breakdowns became more frequent, occurring at least once per week over a period of six months, which had a negative impact on the plant’s availability and the costs incurred.
Using the incumbent barrel washer, Tudor Griffiths experienced the equivalent of a months’ downtime over the period of a year. In addition, there was limited access for the Weir Minerals Europe team to install the Trio coarse washer. There was limited space available for the new equipment to fit in and the Trio was a perfect fit, while at the same time removing any contaminants from the aggregates.
The team at Weir Minerals specified a Trio TCW3618 coarse material washer to help Tudor Griffiths achieve its required operating parameters and increase the amount of saleable product. The design of the Trio TCW coarse material washer allows the deleterious material from the overflow to be floated off and removed, thus improving the quality of the product and efficiency of the process. In addition to supply, Weir Minerals supported in the removal of the old barrel washer and installation and commissioning of the new Trio TCW coarse material washer.
The TCW3618 reduced power consumption by around a third, from an estimated 55kW to 22kW at the same time as maximising plant availability. A potential of 170 TPH of mixed sand and gravel are produced and approximately 40 to 80 TPH of stone are washed, depending on the dig. A paddle change was undertaken after six months of use, achieving a total of 1,200 hours of wear life.
Following the installation of the Trio TCW3618 coarse washer, Tudor Griffiths saw production increase by 50,000 tonnes per year (12%) and a reduction in downtime of around 26 days per year.
Jason Pritchard, quarry manager at Tudor Griffiths said: “The Weir Minerals team worked with us to understand our objectives and proposed a solution which was capable of meeting our needs. The Trio washer has not only increased our plant capacity but also improved the overall cleanliness of our end product. We have been thoroughly impressed by the quality of the equipment provided by the Weir Minerals’ team, who have been proactive in proposing further adjustments and optimising our washer’s performance.”
The Trio coarse washer cleans coarse material containing very water-soluble silts and soft clay. Material rolls and tumbles while carried up the spiral shaft. Cast paddles abrade and separate aggregate from dust and soluble clay. The waste material absorbed by the water is discharged over the adjustable weirs at the back of the machine. Classifying is accomplished when material containing deleterious matter that has a specific gravity less than the coarse material is floated upwards and carried over the adjustable weirs. The water velocity to float the deleterious materials comes from the manifold on the bottom of the tub. The cleaned product is discharged at the inclined section of the machine.