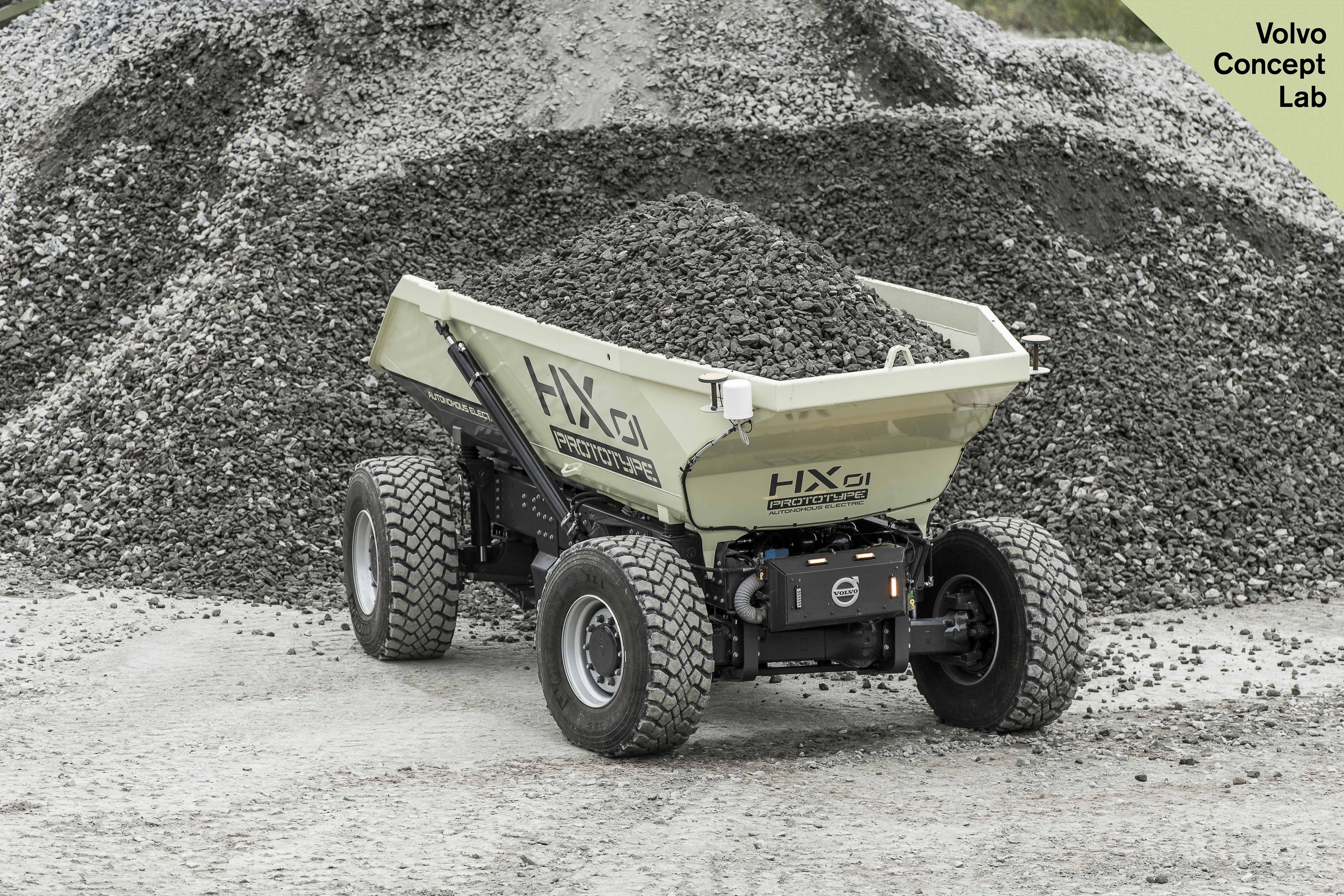
Volvo Construction Equipment’s electric site research project marks a new way of working, combining intelligent machines, automation, electromobility and total site solutions to help shape the quarries of the future.
Volvo Construction Equipment’s (Volvo CE) electric site research project aims to transform the quarrying and aggregates sector by reducing carbon emissions by up to 95% and total cost of ownership by up to 25%. The company first presented its electric site solution around a year ago when it unveiled its HX1 concept autonomous, battery-electric, load carrier and the LX1 prototype hybrid wheeled loader. Since then we’ve seen the second generation of the HX1 – known as the HX2 – and witnessed the LX1 achieve around a 50% improvement in fuel efficiency, compared to its conventional counterparts, during hundreds of hours of real-world customer testing in the US. But there’s still one more prototype machine
“The EX1 prototype will be unveiled soon,” says Uwe Müller, Volvo CE’s chief project manager for the electric site project. “But for now, I can tell you that its job at the electric site will be to load blasted rock into the mobile crusher before it’s transported to the secondary crusher and then processed. Because the machine will be relatively stationary, it’s ideal as a fully electric machine on a cable. This has allowed us to make it a zero-emission excavator.”
The EX1 prototype has been in development since the electric site research project started in October 2015. The project aims to electrify a transport stage in a quarry – from excavation to primary crushing and transport to secondary crushing. It involves developing new machines, work methods and site management systems – together these things form a complete site solution. New technology in the project encompasses machine and fleet control systems and logistic solutions for electric machines in quarries. At this stage, the machines and technology involved in the electric site solution are part of a research project and are not commercially available.
“The electric site research project is a step towards transforming the quarry and aggregates industry,” says Müller. “By using electricity instead of diesel to power construction equipment in a quarry, we have the potential to deliver significant reductions in fuel consumption, CO2 emissions, environmental impact and cost-per-tonne. The electrification of construction equipment will produce cleaner, quieter and more efficient machines – this represents the future of our industry.”
Optimising quarries
“Over the last few decades, there has been tremendous process optimisation in various industries, such as harbour handling,” explains Müller. “However, the process for gravel production in quarries has not seen the same progress. There is still huge potential to reduce waste in machine usage and material flow at quarries. This is in addition to increasing machine efficiency – which is the area we have previously focused on. Looking back, we can see that the machines being used today are more reliable, easier to operate and have greater efficiency than their predecessors. These changes have significantly improved productivity. However, as the quarry production process has not seen the same improvements, machine developments can only achieve so much. Therefore, what we’ve done at Volvo CE is adopt a ‘zoomed out perspective’ where we are looking at the inefficiencies on a higher level.
“Today’s quarries aren’t optimised or coordinated. For example, material is left on the ground between process steps, there is over- and under-production due to a lack of control, and there is extensive downtime. To tackle this, we have identified two paradigm shifts that work hand in hand: automation and electrification. Both these areas point towards process-orientated material flow with downsized, dedicated machines for each task – in some applications these will replace the versatile products that are used today for multiple jobs. It’s with this in mind, that we’ve created the HX2; it’s ‘from elephants to ants’ concept – a completely new way of working in the construction equipment industry. The HX2 prototype combines intelligent machines, automation and electromobility as a door opener to developing completely new solutions towards customer needs.”
The HX2 in focus
The HX1 electric load carrier was proof of concept but since then Volvo CE’s engineers have been busy developing the machine, so while it may look similar on the outside, the HX2 is completely different on the inside. Engineers updated the design requirements to incorporate shared technologies and components from the Volvo Group, such as electric motors, batteries and power electronics. A completely new drivetrain was integrated to take full advantage of the groundbreaking electromobility developments that are happening inside the Volvo Group. Another new feature is the addition of a vision system, which allows the machine to detect obstacles in its vicinity.
“Compared to a traditional load carrier which is directional, the HX2 delivers the same performance whether it’s going forwards or backwards,” says Müller. “The machine is extremely manoeuvrable, it is four-wheel drive with four-wheel steering. However, because of its modular design, it can easily be tailored to customer needs so it could be built with two-wheel drive and/or two-wheel steering. It’s vital that the machine is modular because it isn’t a one-size-fits-all solution; the machines, controls systems, charging systems etc. will need to be adjusted to each customer’s needs. The load capacity to machine weight on the HX2 is twice as high as it is on a standard load carrier. Energy efficiency is also higher, the HX2 recuperates energy when travelling downhill or braking.”
Hybrid technology
Another element of the electric site research project is the prototype LX1 hybrid wheeled loader. This machine – which will be used to load the HX2s – can deliver up to a 50% improvement in fuel efficiency, as well as significant reductions in emissions and noise pollution compared to its conventional counterparts. The LX1 is a ‘series hybrid’ that incorporates a driveline that consists of electric drive motors mounted at the wheels, electric driven hydraulics, an energy storage system, a significantly smaller diesel engine and new machine architecture, including a new design of the lifting unit. It’s this combination that enables the substantial gain in fuel efficiency. The prototype – which has 98% new parts and a fundamentally new machine design – can do the work of a wheeled loader that’s one size larger. The LX1 prototype recently returned to Sweden from the U.S. where it performed hundreds of hours of real work, in two applications, for Volvo CE customer Waste Management. Testing began at the Redwood Landfill and Recycling Center, a green waste composting site in northern California. Both fuel efficiency and greenhouse gas emission tests were conducted at the facility and, although the data is still being analysed, the results so far show an average improvement of 50% in fuel efficiency, equating to a reduction of 35% in fuel consumption and greenhouse gas emissions. The second test site was the Moreno Valley Transfer Station, a waste transfer site in the southern part of the state. Here, the LX1 achieved an average fuel efficiency improvement of around 45%. Both sets of results exceed the 35% fuel efficiency improvement target set for the project.
“We are pleased with the results from the field testing,” says Scott Young, electromobility director at Volvo CE. “Although we’d already seen the LX1 reach up to a 50% improvement in fuel efficiency in our internal tests, every application and operator are different. Because of this, we were aiming for a 35% improvement in fuel efficiency in this project. But we are happy to say that we’ve significantly exceeded this figure and achieved similar results to those recorded at our test site in Sweden. Now we’ve concluded the field tests, the machine will be updated and tuned based on what we’ve learnt over the last six months.”
Collaborating for a sustainable future
Volvo CE teamed up with its customer
“Volvo CE is committed to pushing boundaries and exploring the technology of the future,” says Müller. “We’ve set ourselves four key technology challenges that we call Triple Zero and 10x: zero emissions, zero accidents, zero unplanned stops and 10x higher efficiency. We believe that our clear focus on electromobility, intelligent machines and total site solutions will help us achieve these ambitious goals and pave the way for a sustainable construction industry. Research projects like the electric site demonstrate this focus as well as how Volvo CE wants to work with its customers early in the development phase to improve total site performance and sustainability, while also saving customers money. By integrating customers in the development process, we can design the best solution for a task, application and environment together.”