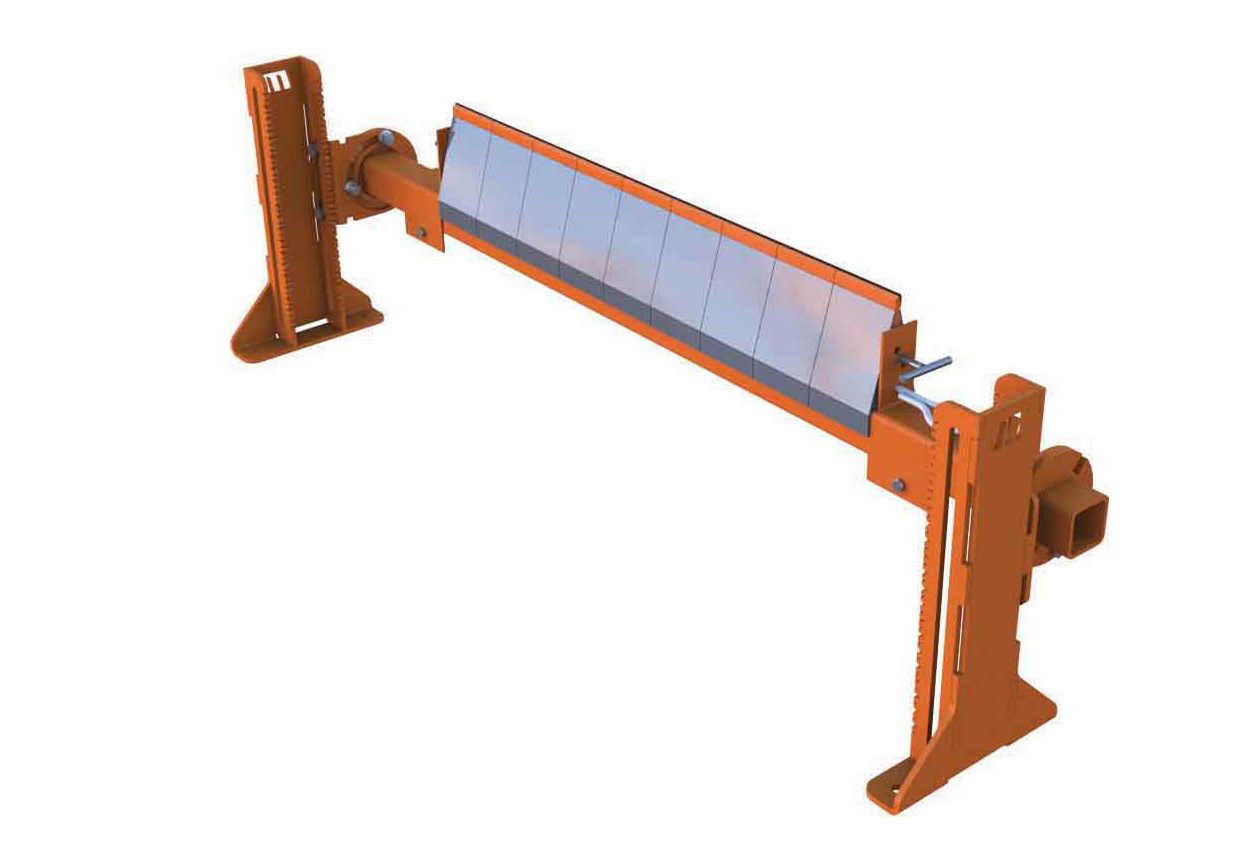
A global leader in bulk material handling technology has announced the introduction of its new Pin Latch Secondary Belt Cleaner, a tungsten carbidetipped secondary cleaner that slides in and out for service without requiring any tools. The design from US firm
The new product’s pin latch design provides adjustable tension for varying conditions, such as belt speed, material being conveyed and belt cleaner position relative to the head pulley.
It will handle belt speeds up to 5.1m/second, and the versatile unit accommodates belt rollback. The carbide tip is acid- and abrasion- resistant, and the assembly is well suited for use on belts with mechanical splices, smoothly adapting to and riding over the splices without damaging the splice, belt or blade.
“The maintenance-friendly design of the new Pin Latch Belt Cleaner is engineered for a wide range of global applications,” said Martin Engineering South Africa sales manager Pieter Opperman. “It can drastically reduce downtime for service or replacement, since no alignment or setting of the blade is required. Inventory is reduced to a one-part blade and buffer, without bolts, nuts or other fasteners.”
Opperman said that blade replacement can be performed with a greatly reduced risk of errors, and the narrow blades conform readily to conveyor belt profiles. “The quick replacement of this design means shorter shutdowns and reduced maintenance time. That translates to more productive and profitable operations, with personnel able to concentrate more on core activities.”
The Martin Pin Latch Secondary Belt Cleaner is said to deliver excellent cleaning performance with quicker blade recovery, and provides the versatility to adjust blade performance to match a wide range of application characteristics. It is considered a preferred upgrade for Martin SQC2 and SC16 Secondary Cleaners.
“Matching the blade performance to the unique conditions of a specific application is a key to maximising efficiency,” Opperman added. “And servicing these units simply requires sliding the pin out and removing the old blades by hand. New blades are slipped onto the mainframe, and the pin is re-inserted through the new blades. That’s all there is to it.”