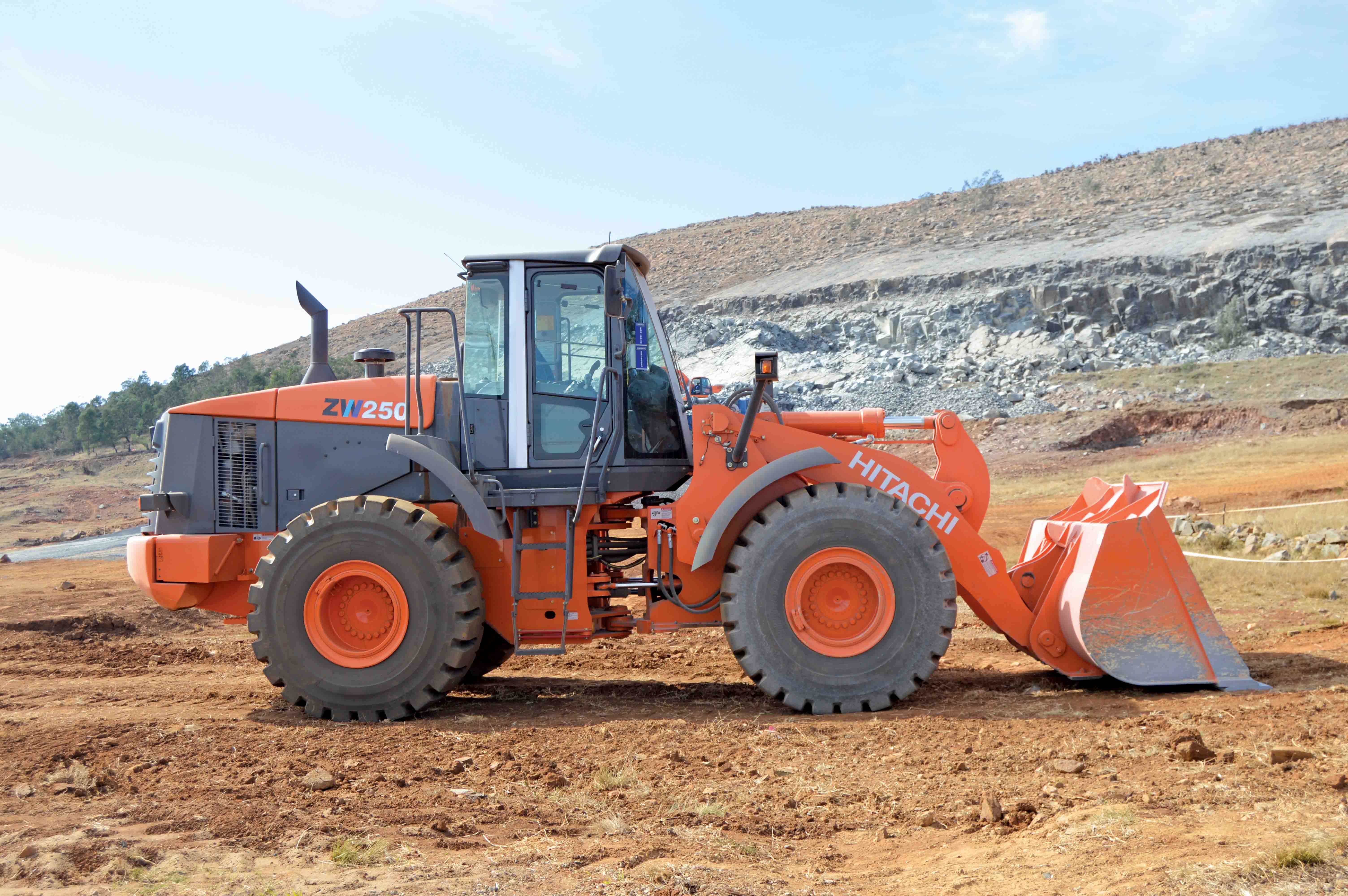
To kick-start its business, a South African start-up quarrying company has invested in a premium fleet of equipment helping it win a sizeable share of the Nquthu, KwaZulu-Natal aggregates market, writes Munesu Shoko.
Based on the understanding that a premium product offers premium returns in the long run despite the large capital outlay required, Real Stone Quarries, a start-up quarrying company based in KwaZulu-Natal, South Africa, has purchased a premium fleet of
The mobile train comprises the MC 110R EVO jaw crusher, MCO 9S cone crusher and the MS 16D triple-deck screen. It has been deployed at Real Stone Quarries’ Nquthu Quarry, the first in a line of quarry operations the company intends to establish. Dr Zakhele Buthelezi, managing director of Real Stone Quarries, says opportunity abounds in the area, especially on the back of new road and maintenance projects lined up.
This is complemented by social infrastructure projects in the pipeline, including schools and housing projects to be built under the country’s Reconstruction and Development Programme (RDP). Nquthu Quarry is strategically located to service the nearby villages of Mondlo and Nkandla, considering that there is no other commercial quarry within the 70km radius.
Despite a limited quarrying background, Real Stone Quarries’ management team is passionate about its business. It has done its research on the basics of running a successful quarry operation. Right from the start, Corporate Affairs director Dr Vusi Sibeko investigated the right type of equipment to run a successful quarrying business. After proper due diligence, the company eventually opted for Kleemann’s EVO crushers for its first crushing and screening plant.
Despite the fact that this range of crushing and screening equipment isn’t the cheapest around, Sibeko says they were not deterred by the big capital disbursement. Instead, they were impressed by a range of innovative features from which they could benefit. This is in stark contrast to the general belief that start-up companies, for a number of reasons, because of a lack of access to funding, always look for cheaper plant options to break into this sort of business.
“We went into quarrying with a clear mind that we would always look at tried and tested machinery for our plant needs. We want to spend most of the time in production rather than fixing the plant,” says Sibeko.
While reliability was a principal factor when looking for a prospective equipment supplier, Sibeko adds that aftersales support also played a major role in influencing the buying decision. Both Sibeko and Buthelezi were impressed by Wirtgen SA from the start. “After delivery, they were here for more than two weeks for commissioning and training of our personnel,” says Buthelezi. “They also brought a product specialist from Kleemann in Germany who was here for a month to set up the process.”
Innovative features also played a big role in influencing the decision to buy this range of machines. The Kleemann MC 110 R EVO mobile jaw crusher is said to combine the advantages of a professional stone crushing plant with those of a recycling crusher. “One of the biggest benefits of the MC 110 R EVO is continuous crusher utilisation through the Continuous Feed System (CFS) which keeps the cavity full for best production and wear cost,” says Lantie van der Merwe, Kleeman sales executive based at Wirtgen, SA.
The CFS maximises efficient material flow via an ultrasonic probe above the crushing jaw which measures the crusher’s fill level. This detects overloading and the material feeding speed is regulated accordingly. “Therefore, as a general rule, the feeder elements do not come to a complete standstill (vibrating feeder and pre-screen), and this translates into the jaw crusher always maintaining an optimal fill level,” says Kevin Burger, sales consultant at Wirtgen SA.
Meanwhile, the MCO 9S EVO can be used either as a secondary or tertiary crushing plant. Due to the low total weight, it is possible to change locations without great difficulty using a flat-bed trailer. The machine also benefits from an on-board generator which generates power for all the conveyors and vibrating motors, making it more fuel-efficient.
“This machine has very good fuel consumption figures due to the fact that only the tracks and adjustment to the CFS is done with the hydraulics. All other drives are electrically driven,” adds Van der Merwe.
The MS16D triple-deck screen completes the train. Offering a feed capacity of up to 350 tonnes per hour, it is suitable for feed material of up to 150 mm. The plant is suitable for processing natural stone and recycling applications. “One of its biggest benefits is the large feed hopper for high flexibility in feeding by means of a wheel loader, excavator or crushing plants,” says Van der Merwe.
Meanwhile, quarry manager Thatho Morare, is especially impressed by the ease of access to the main servicing components on the MS16D screen, affording simple maintenance and screen surface changing thanks to an all-round platform.
When we visited the site, the quarry had been in operation for about six weeks. The production team was still doing trial runs with the crushing and screening plant. “We haven’t pushed the plant to full capacity yet,” says Morare. “We are still doing size grading for the various products we have orders for. We are still waiting for sampling before we can embark on full production.” Initially material sizes of 19mm, G2, ballast and gabion stone are being produced.
These product sizes are a clear indication that the initial target market is the road sector. This will be extended to cater for block-making and concrete-making industries at a later stage. Production starts with drilling and blasting, and is outsourced to a contractor. Bearing in mind that the quarry is situated close to a residential area, blasts are kept relatively large at about 20,000 tonnes per blast to avoid regular disturbances.
Considering that load and haul is one of the biggest cost drivers for any operation of this nature, the management team has opted for in-pit crushing to cut down related costs. A
Apart from the Kleemann range, Real Stone Quarries has also invested in a premium fleet of other equipment pieces. These include a
A 30 tonne
EQUIPMENT ON SITE
LOADING
1 x 225 Doosan excavator
1 x Hitachi ZW250 front-end loader
HAULING
1 x Komatsu HM300 articulated dump truck
CRUSHING
1 x Kleemann MC 110R EVO jaw crusher
1 x Kleemann MCO 9S EVO cone crusher
SCREENING
1 x Kleemann MS 16D triple-deck screenOne of the key challenges of the newly-established quarry is its proximity to a residential area. The closest homes are just some 200 metres away from the pit. This poses a set of challenges as far as blasting is concerned. To address this, management understands that community relations are crucial. Before blasts, people living closest to the quarry are advised to leave the area to avoid the potential danger of flyrock. The quarry operates under the auspices of the Inkosi Molefe Traditional Council, and to cement relations with the community, Real Stone Quarries has allocated a stake of the company to the local community.
Operationally, one key challenge is the sloping nature of the mining area. The pit is located in a mountainous area, and access to the mountain was a challenge from the start. This called for blasting the slope off first. “This area was mined by the Department of Transport before as a borrow pit. They left a challenging face which we had to contend with. We still have to get the benches sorted out as well,” says Buthelezi.