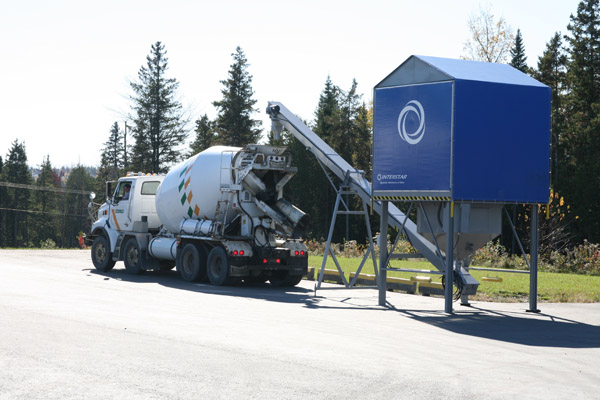
Concrete is no longer a low budget construction material that is hidden behind cladding but has become popular with architects for its aesthetics. The rising demand for exposed concrete has driven development of fair faced concrete and also coloured concrete.
Canada-based concrete additive specialist Interstar has unveiled a new pigment mixing system for the ready mixed concrete market, which the company claims is the first of its kind. The fully automated Megastar batching unit is aimed at the decorative concrete market and can produce 300 different colours at the touch of a button.
"The unit holds four types of dry pigments which are stored in separate hoppers and discharged directly into the concrete truck in the right quantities to make the specified colour," explained Interstar managing director Zachary Gillman. "The discharge takes about two minutes and the system uses the mechanical action of the mixer en route to the construction site to mix the colour into the concrete." The system uses a patented encapsulated pigment for colouration, which differentiates it from other colouring methods already available, according to Gillman. Other systems available often use liquid colourings, which can cause problems with cross-contamination in the mixing chamber.
"The encapsulation ensures that the pigments remain pure until they are mixed with the ready mixed concrete," explained Gillman. "The pigments used in the system have been fully tested to ensure they are inert and are not affected by UV radiation." While the Megastar has 300 pre-stored colour mixture combinations held in the computer controls, it can also be configured to produce bespoke colours for specific projects. The control system for the Megastar is currently available in three languages - English, French and Spanish - and can be used to specify mixes in either metric or imperial units. The control system is also web-enabled to allow for online software updates and maintenance.
"Concrete is fast becoming an architectural material rather than just a construction material," said Gillman. "Demand for decorative concrete is growing worldwide - currently the fastest growth is in the US but we think there is a large untapped market in Europe, particularly in the Mediterranean region.
"The pigmentation of the concrete does not impact on the structural properties of the material and has been fully tested in conjunction with admixtures and fibre reinforcement. The main technical requirements for use are that the mixer truck must be clean and the concrete must have a slump of between 89 and 100mm and, if air-entrained, it needs to be in the 5 to 7% range." The mechanical system for the Megastar has been specially designed by Interstar and has just five moving parts, which Gillman claims makes the system reliable and durable. He added that the system does not need time to start up or shut down at the end of the shift and requires no heating to operate all year round.
Gillman also said that the pigments are easy to handle. "The pigments are delivered in 900kg super sock bags, which can be lifted into position over the hoppers by a telehandler or excavator before the bag is opened." According to Gillman, Interstar provides full training during installation and technical support for the equipment as part of the after sales service.
Development of the Megastar system started two years ago and the prototype took 12 months of research. The development stage was followed by field testing of five units and 15 systems are now in commercial operation.