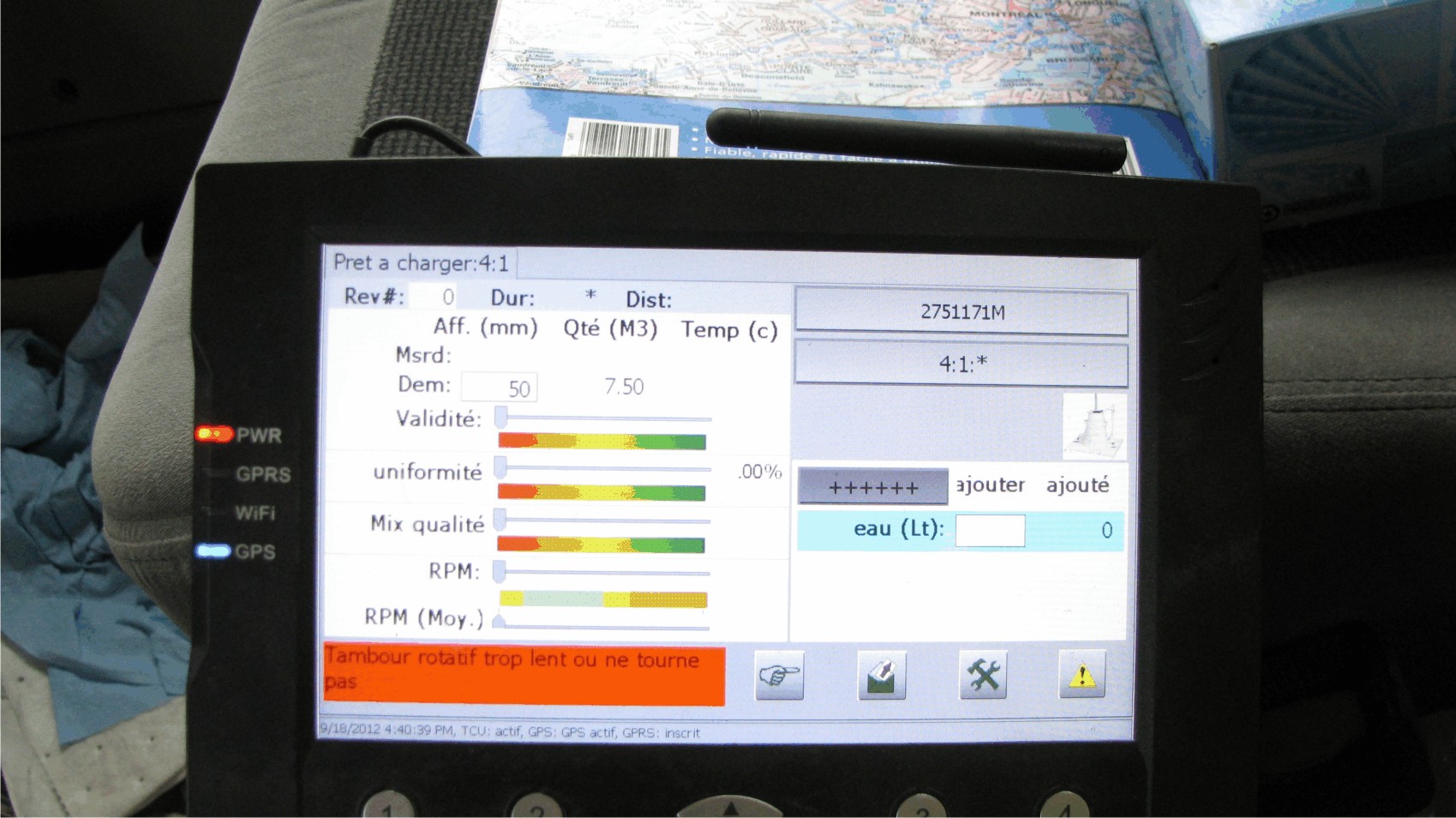
An award-winning concrete system from
The Concrete Optimizer technology, handled in Europe by SensoCrete’s dealer Polarmatic of Finland, allows the monitoring and adjustment of fresh concrete properties.
Invented by Berthold Berman, CTO of SensoCrete, it was one of four innovations selected by the Construction Innovation Forum (CIF) in late 2011 to receive its prestigious NOVA Award for outstanding innovation in construction.
“The Concrete Optimiser is the only online real-time monitoring and control system for fresh concrete delivery,” says SensoCrete.
“The system consists of four components, all of which are installed on the truck: truck sensor unit (TSU); truck control unit (TCU); SensoCrete Mobile Unit (SMU), which is the on-board computer, and liquids meter and valve.”
The computer includes a GPS receiver and a PRS modem, and the server provides communication with the on-board computer, where it analyses, presents and stores data on each load in a project.
“The producer can view data collected from concrete inside the drum (including temperature, slump, volume, mix quality, and potential for segregation) as well as current truck status and location; send new ticket data to a truck system; void a ticket; change truck status remotely; add water and/or admixture to the concrete inside the drum, and activate reports which include statistical graphs.
“Obtaining information on a concrete mixture from the moment it is loaded until it is discharged at the job site, allows the concrete producer to control the quality of the delivered product. Improvements in quality will translate into savings in time and production costs,” says SensoCrete.