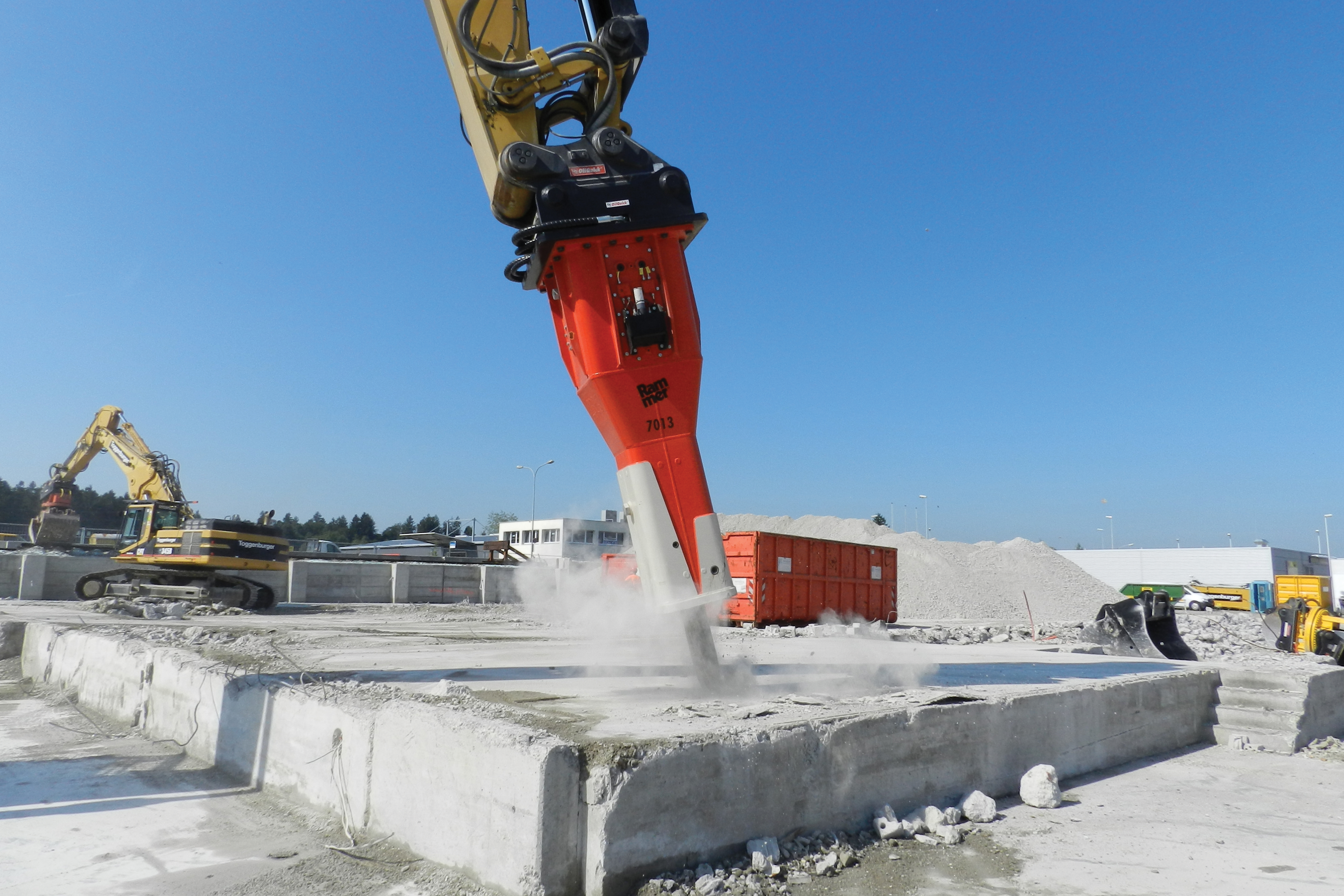
A
A range of specialised equipment, including the hammer, was used for demolition. Some of the heaviest beams were over 1m thick and the contractor was also required to process around 10,000m³ of concrete and 1,000tonnes of steel.
A total of 77,000m³ of material was demolished and, where possible, recycled by specialist contractor Toggenburg of Winterthur, who put its newly-delivered
In the pre-planning and realisation of the project, Toggenburg’s Marcel Stadler and his team relied on the experience of long-time partner, Avesco, which has supported the company for several decades.
The resulting cooperation ensured that the new DEM100 machine was prepared for the site with attachments including a concrete cutter weighing over 10tonnes; a ripper tooth almost 2m tall, and a 5.8m3 capacity bucket.
To remove the massive 3m x 3m x 1.5m machine foundations from the old factory, a newly-acquired Rammer 7013 was deployed. Weighing 7tonnes, the hammer delivers optimum demolition power and performance, with Toggenburg reporting that the constant blow energy of the Rammer 7013 afforded by its FBE system was a key consideration in its use.
The unit’s noise and vibration damping is said to have ensured maximum protection of the carrier machine, and low noise levels.
“Further efficiencies were derived from a permanently filled energy accumulator, with this feature fully utilising the energy from the excavator, and keeping this part of the hydraulic hammer maintenance-free,” says Rammer.