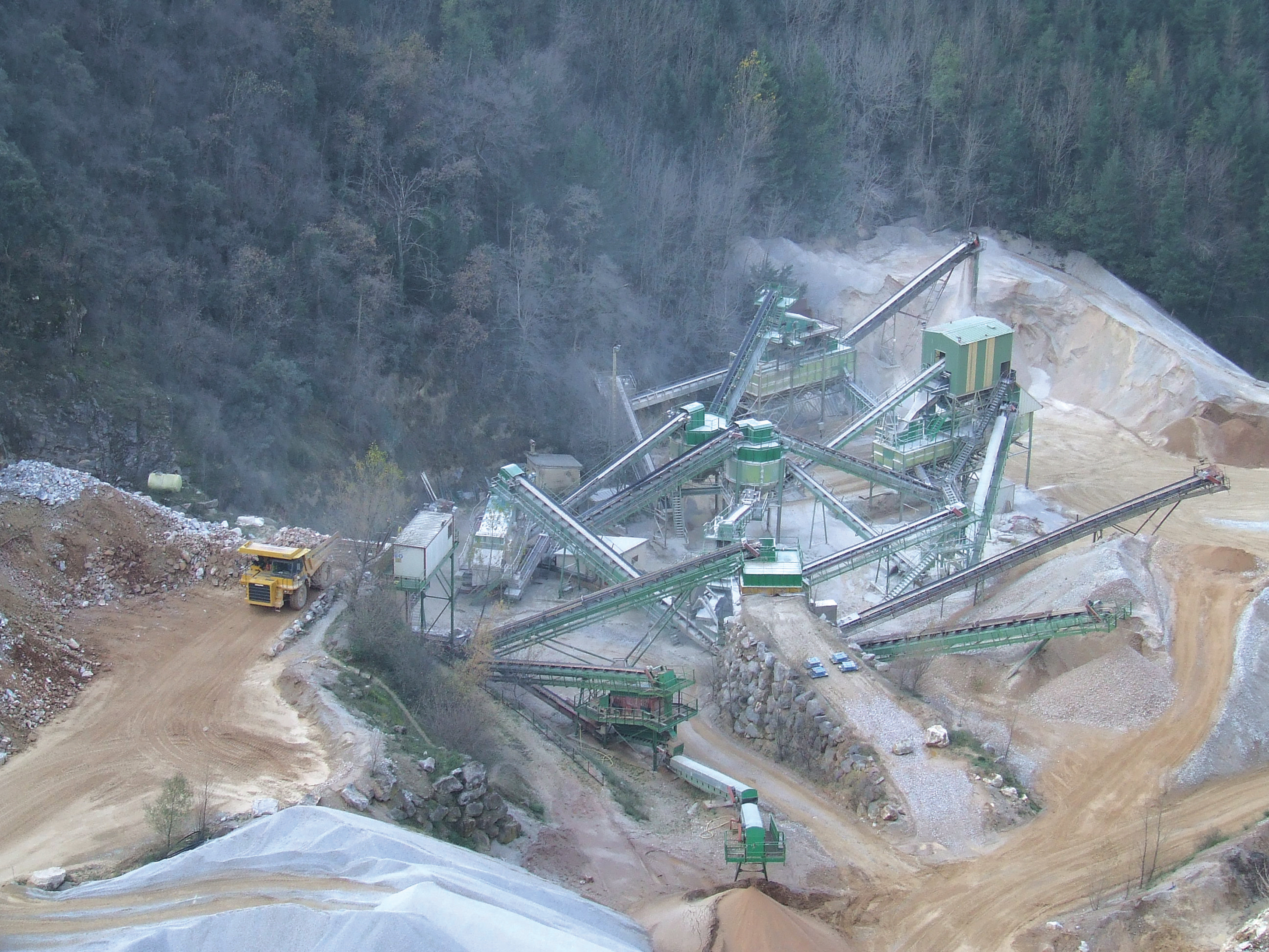
The weight of material loaded into haul trucks has a direct impact on not just production but also on performance of equipment. Under load a truck and production does not reach its full potential, but overload it and you risk excessive wear and increase the risk of accidents.
Development
"The first study started in Germany in May 2008 after some customers asked for helped with carrying out a production study," said Cat's Malaga-based demonstrator and instructor Karl Marlow. "Such studies are a way to check equipment after delivery and ensure the site is getting full efficiency and look for any areas that could be further improved. It helps demonstrate the value of the investment to the customer.
"In some cases, we have added side boards to the trucks to allow them to carry a full capacity load because the specific gravity of the rock is lower than average. On others we have suggested that they load one pass less to stay within the weight limits." The truck analyses the loads and cycle times using on-board computers linked to mobile scale pads that form a weighbridge that can weigh up 250tonnes per axle. The study normally lasts two days during which time 60 to 70 loads are measured.
According to Cat, 90% of payloads should be less than 110% of the truck capacity. The target payload is 100% and trucks should never be 20% overloaded.
Under test Carriers de St Amancet is managed by Patrick Vidal, who has worked at the site for 26 years and helped the site move from building stone production to crushing and screening the limestone for construction aggregates.
"The quarry opened in 1900 and all the houses in the village are built from stone that came from the quarry," said Vidal. "Today the quarry produces 12 products and has a 320tonne per hour crushing capacity." The site has just had its permit renewed to allow up to 400,000tonnes of material to be extracted each year and has another 30 years of permitted reserves.
The site uses drill and blast every two to three weeks to extract the rock and has two rigid dump trucks to haul material to the fixed crushing and screening plant near the bottom of the valley.
Results
Secam was pleased to help Cat with its study as they were looking to understand the optimal number of passes for efficient production at Carriers de St Amancet. Particularly as the steep haul road could present a safety issue if trucks were overloaded.
After the scale study is completed, Cat's on-site staff talks to the customer about the initial findings and then prepares an in-depth report with recommendations to improve operation.
Initial observations at Carriers de St Amancet have brought the suggestion that the haul road layout is altered as currently the truck have to go up a gradient before travelling down to the crushing and screening plant.
According to Cat, the in-depth study will give Secam a clearer picture of changes that could be applied to improve production. Marlow also said that fuel meters will be added to the system this year which will enable fuel efficiencies to be added into the calculations.