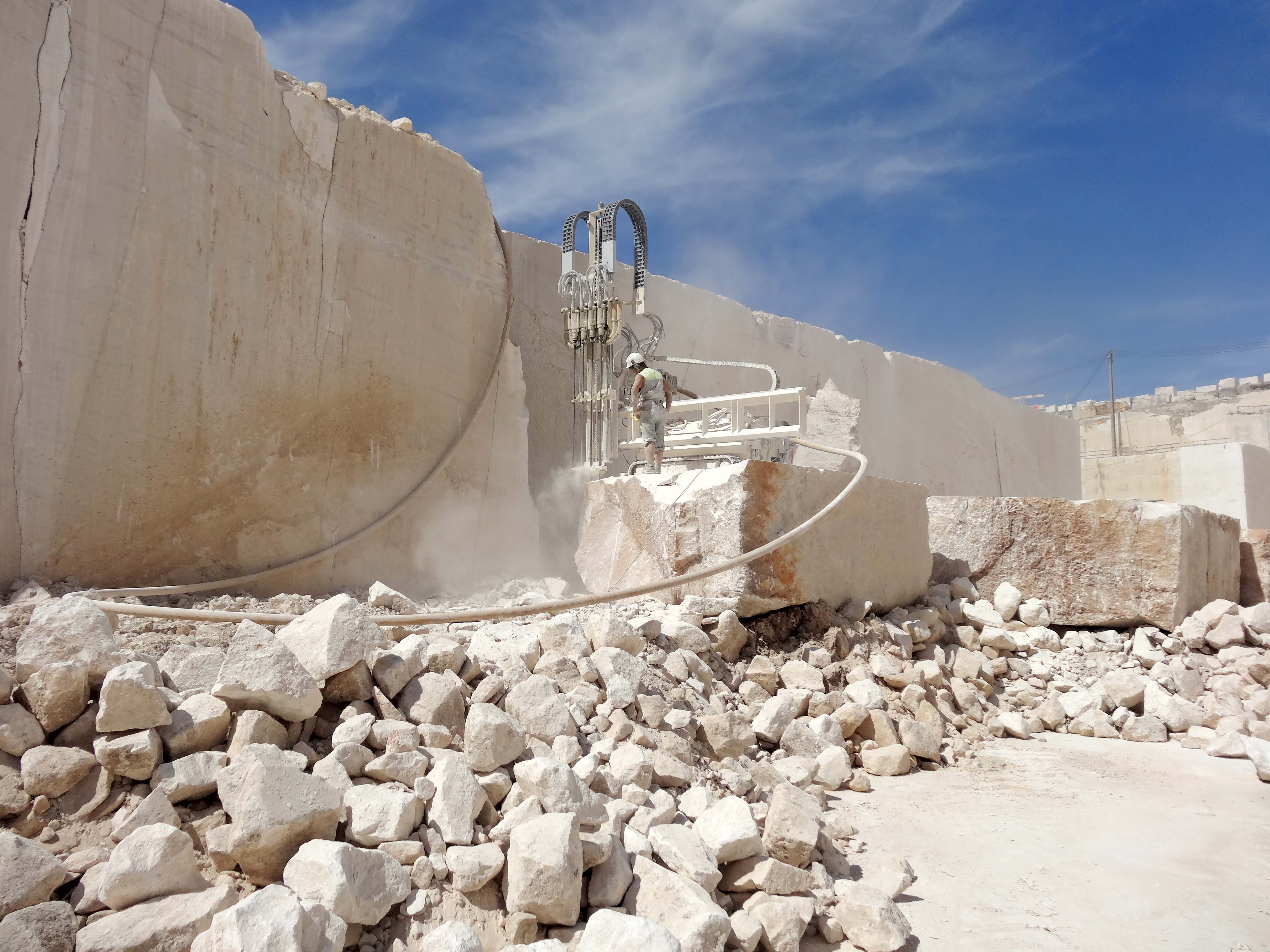
Successful Portuguese stone product firm Solancis is using proven and highly efficient Caterpillar wheeled loaders, excavators and articulated trucks for its crucial quarry-based limestone block loading and hauling. Guy Woodford visited the company to see them in action.
Other than both heralding from Portugal, world football giants Benfica and tailor-made stone product business Solancis may not appear to have much in common. But both have earned an enviable global reputation in their respective fields since 1951, when Solancis furnished the stone work in Benfica’s first Estádio da Luz (Stadium of Light) in Lisbon. The 120,000 capacity footballing mecca was demolished and replaced in 2003 by a new 65,000 capacity stadium of the same name, but Solancis will always be proud to have played a key part in the first Stadium of Light’s construction.
While Benfica are still regularly contesting UEFA Champions League games against Europe’s best clubs, Solancis, a fourth-generation family company, now owned by Samuel Delgado, is seeing great global demand for its high-quality limestone quarry-sourced products for buildings such as hotels, offices, department stores, sports stadia and residential properties. Around 95% of Solancis’ sales are exports to customers in 57 countries. France, England, the US and China area the company’s four biggest export markets.
Five three-strong teams work across Solancis’ nine quarries in the stunning Serra De Aire region of central Portugal, extracting around 80,000tonnes/year of limestone blocks in the same efficient way.
Horizontal cuts made with a 7.2m blade length chainsaw at the top and bottom of the wall are followed by vertical cuts using the same chainsaw. Vertical holes are then drilled from the top down to the bottom of what is now a visible block within the wall. When the holes are completed, wire with diamond cutters is put through the holes to enable vertical cuts at the back of the limestone block. Next, gravel and loose material is placed in front of the block, to be used to cushion its fall when the excavator pushes the cut block away from the wall onto the quarry floor.
When the block is on the floor, it’s marked and divided into segments depending on texture, colour and overall quality. Based on these markings, holes are drilled into the block for cutting out smaller blocks weighing around 20tonnes each. The blocks are then picked up by a wheeled loader with forks and loaded onto an on-highway truck.
The trucks then transport the blocks to Solancis’ state-of-the-art factory. Here, they get processed as final façade cladding, outdoor or indoor paving, moulding or as unique stone item products. Solancis’ employees often work closely with architects on bigger customer projects.
To ensure the safe and efficient onsite loading and hauling of its highly prized limestone blocks, Solancis runs an extensive
“The Caterpillar machines are reliable. We had one 966 wheeled loader for 22 years and a 330 excavator for 25 years and could still get original spare parts for both,” says Delgado, during a conversation at Solancis’ impressive factory HQ near Leiria. Cutting fuel consumption across his quarrying machine fleet is one of Delgado’s biggest priorities.
“Previously, the fuel consumption of the Caterpillar machines was not good. But the fuel consumption of our latest Caterpillar excavators and wheeled loaders is very good,” says Delgado. “We use 10% less diesel fuel with our 980K than the previous Cat 980H, and around 8% less with our 349E compared to our previous Caterpillar 345D excavator.”
Delgado says that his latest five-strong 980K wheeled loader and five-strong 349E excavator line-up are saving around 3,000litres of diesel fuel a month, compared to the previous Caterpillar fleet, reducing his fleet’s diesel fuel bill by €3,750 a month.
He’s also keen to stress how Caterpillar’s VisionLink tele-matics is helping him run the quarrying side of his family business. “It’s important to see machine utilisation and VisionLink helps a great deal with this, particularly in tracking idling time. I compare my different teams and see whose machines are idling more and address any problems through the team leaders, who each receive the comparison data through WhatsApp. We have reduced idling time with VisionLink and our target is 8%. Overall, VisionLink has helped improve machine operating efficiency at our quarries by 15-20%.”
Solancis bought its first Caterpillar machine in 1978, a 950 wheeled loader, but after purchasing further wheeled loaders and excavators switched to models from another leading OEM from 1998-2008. Delagado says part of the reason he opted once again for a Caterpillar machine fleet eight years ago was due to the financing options available to Solancis through CAT Financial Services. Most of Solancis’ current Caterpillar equipment fleet is around three years old with around 4,000 hours on the clock. All models are supplied and serviced by its Portuguese dealership, Barloworld STET, headquartered in Lisbon. “Our relationship with them is very easy,” continues Delgado.
“We have a full service contract on all our Caterpillar machines and their technicians are regularly coming to our quarry sites. Having the full service contracts maintains the resale value of my machines. Over the past six years I’ve seen an up to 40% higher resale value on my Caterpillar models compared to models from other OEMs.”
Luis Pedro has been the foreman at Salgueira Quarry, Solancis’ biggest, since 2000, having started work at the site in 1988.
Given his long service at Solancis, he’s a good person to talk about the company’s Caterpillar wheeled loaders and excavators. “They are easy to operate. The load capacity of the excavators and break out capacity of the wheeled loaders are very good,” says Pedro.
Solancis’ five quarry-based teams work 8am-5pm Monday to Friday. None of their quarried material is wasted, as any surplus limestone that is not cut into specific customer order blocks is sold locally to construction materials’ companies or building contractors.
Pedro has seen great change in working practices at Salgueira Quarry. “When I started here we used explosives and worked with hammers by hand. Today we can produce a finished product for a customer in one day, which would have previously taken a week. The technology we use has changed a lot for the better. The size of machines we use are also bigger – like going from a 25tonne to a 50tonne excavator.”
The quarries of Serra De Aire region employ a lot of local people, and Pedro’s son does voluntary work alongside his father in school holidays. Securing the next generation of quarry workers is of crucial importance to companies like Solancis. Of why he’s built a career in quarrying, Pedro adds: “I only know this job. I started very young as a kid.”
An environmentally-minded business, the roof of Solancis’ factory is covered with solar panels, which produce around 25% of the electricity needed to run the site. Additionally, 98% of the water produced there gets recycled and reused.
With its prized limestone, efficient Caterpillar quarry machine fleet and green-minded production methods, Solancis’ is well equipped for future success. “I have a very positive outlook,” says Delgado “We are a business with a high specialism that works closely with many top architects, and there is a big world market for our limestone products.”
HAULING
1 x Cat 730x articulated dump truck
LOADING
5 x Cat 980K wheeled loaders
1 x Cat 980H wheeled loader
5 x Cat 349E hydraulic excavators
1x Cat 320E hydraulic excavators