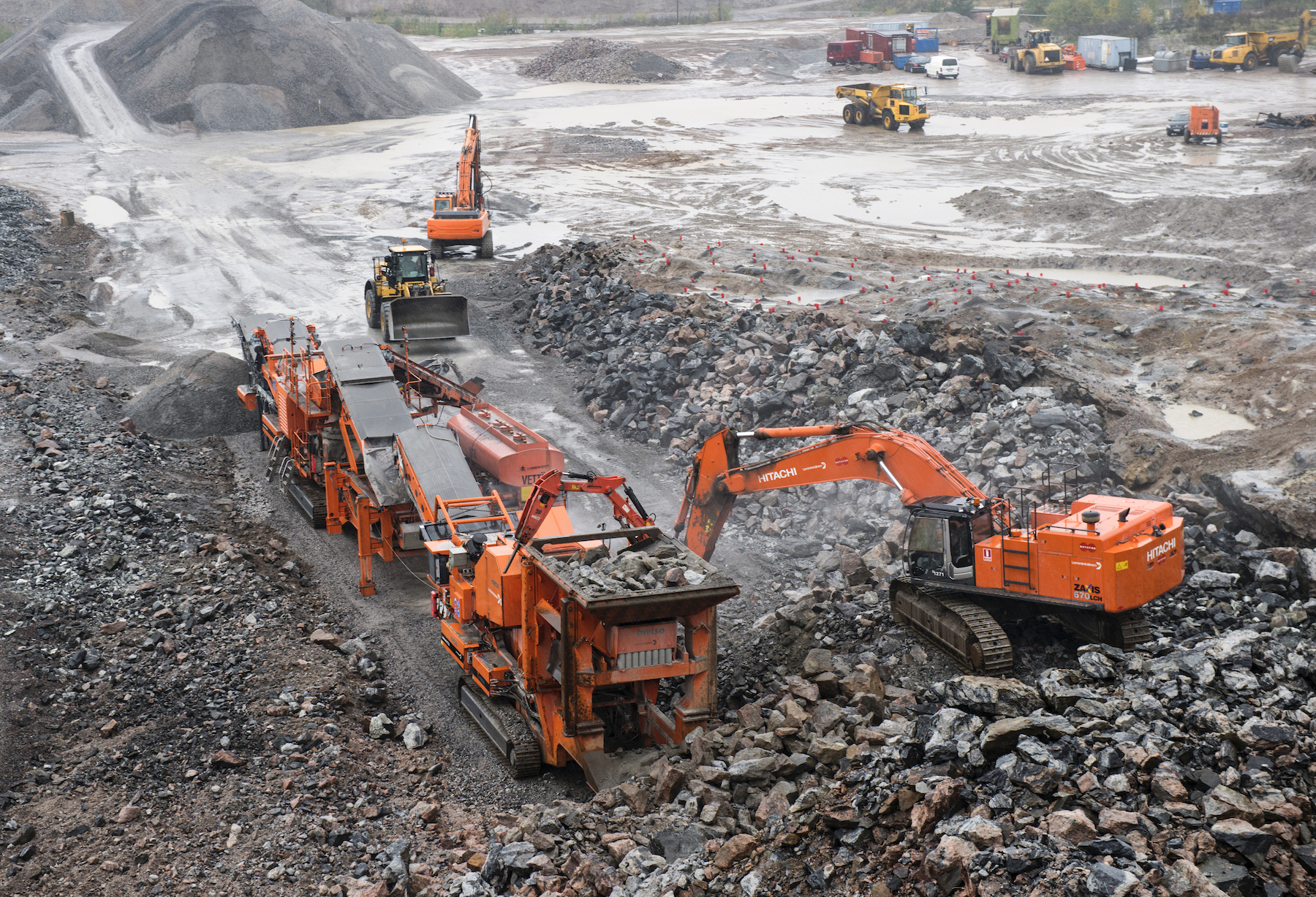
A vital source of aggregates for transport infrastructure and construction projects in and around Helsinki, Finland, Lemminkäinen’s Myllykylä quarry in Vantaa, near Helsinki International Airport, is said to be reaping the efficiency and money saving benefits of deploying three Metso track-mounted crushing and screening plants. Aggregates Business Europe Editor Guy Woodford visited the quarry.
Myllykylä quarry site manager Mika Salmelainen is a busy man. With the
Having opened in the early 1980s and with annual aggregate processing levels now at 600-800,000 tonnes, Myllykylä’s mineral riches have been drawn to such a point that the site will close in a few years. Lemminkäinen will then switch production to a new aggregates deposit also in Vantaa, thus keeping their own and customer logistics costs down and enabling them to continue to comply with tough EU environmental regulations for quarry site operations. Currently open 14 hours a day, five days a week, Myllykylä quarry is already being turned by its incoming owners into a motor racing circuit, with its distinctive straights and bends taking shape around the hard at work crushers and screeners, loaders, and haulers onsite.
Salmelainen says that operating three highly mobile track-mounted
“Operating track-mounted crushers means we can operate at one level and always move the unit to the right place. It’s the most cost efficient way,” explains Salmelainen. “The crushing always takes place where the material is. The dump trucks only move the end product.”
Introduced at Myllykylä in 2011, the Lokotrack LT125 jaw crusher and LT550GPF cone crusher are capable of producing aggregate material sized 0-30mm, 0-56mm, and 0-90mm. With the tertiary crusher, the LT300GPB, also introduced at Myllykylä in 2011, aggregate material can get down to as small as 0-16mm.
“Lemminkäinen and Metso have a long history, going back several decades. We also buy equipment from them because they are near - a domestic manufacturer. The Metso aftermarket services, wear parts and spare parts are also near. Running a 100% crushing and screening contracting business, you never know what will happen. With Metso we feel we are not alone.”
The cooperation between Lemminkäinen and Metso also includes the development of new prototype crushers and screens. “This includes the GP550 cone crusher, Metso’s second biggest, which is now available globally. Lemminkäinen has eight of these,” says Salmelainen proudly.
The challenging machine operating conditions at Lemminkäinen, where temperatures can fall to as low as -20°C, help to make it an ideal testing ground for fledgling crushing and screening systems. The toughness of the rocks at Lemminkäinen provides another good equipment quality benchmark.
Having such productive quarries, including Myllykylä, has helped Lemminkäinen consistently produce more than 10 million tonnes of different aggregates a year. Metso’s biggest crushing and screening customer in Finland, the firm operates nationally with more than 20 mobile, wheel-mounted and track-mounted crushing fleets, each normally consisting of two to three separate crushing plants.
Working alongside the Lokotrack crushing and screening equipment at Myllykylä is a wealth of loading and breaking equipment including
“All Lemminkäinen sites, including Myllykylä, handle almost everything themselves. There is little sub-contracting. We clean the rock deposits; we drill the holes for blasting; we blast ourselves; we hammer oversized material with breakers; we crush, screen and load material for customers; and, in some cases, we transport the material to them. By controlling nearly the whole process, it’s easier to plan and operate.”
Day-to-day work at Myllykylä is also made more efficient through the deployment of several automation solutions. “The Lokotrack crushers we use come with IC Series intelligent control, which controls the level of material in the feeder. If the feeder is too full, the IC Series intelligent control system stops or lowers the material going into the crusher. This gives an even load going through the crusher. We also use Lemminkäinen’s Lemset radio remote control system for breakers.”
Unlike many other used up aggregates quarries, Myllykylä’s rebirth as a motor sport racing hub will see it maintain its vitality long after the final graded tonne of material is produced. It’s a thought that pleases Salmelainen as he continues to plan for Lemminkäinen’s switch to their new Vantaa quarry home. However, it’s the present aggregates market that is foremost in his mind.
“We are seeing more demand for special grades to help stop water pressure going up in the material. This helps concrete building and asphalt-based applications,” explains Salmelainen, who has worked for Lemminkäinen for more than 30 years. “The overall [aggregates] market is difficult at present but the upturn will come. The main thing for Lemminkäinen, as a contractor, is to have first-class competitive equipment so you can be ready for it.”
Despite his satisfaction with his Metso Lokotrack crushing systems, Salmelainen believes they can become even better. “I’d like them to be even more versatile. As I’ve said, customers are asking for lots of special grades and we need to meet demand in a cost efficient way.”
Cat’s versatile loading star
Among a wide variety of loading equipment models used at Myllykylä quarry is Caterpillar’s versatile 980K wheeled loader. Launched in 2011, the 980K is said by the US construction equipment industry giant to be designed to improve operator comfort, performance, and productivity.
Coming as standard on the 980K, the model’s Performance Series Buckets – from 4m³ to 12.2m³ - enhance visibility and decrease cycle times.
On its launch three years ago, Caterpillar referred to the 980K’s “unmatched, revolutionary world-class cab” which, the American manufacturer says, creates a comfortable, efficient, safe, and productive operator environment. The innovative Cat C13 ACERT engine on the 980K is said to be optimised for maximum fuel efficiency and increased power density while meeting Tier 4 Interim/Stage IIIB emissions standards.
Load-sensing hydraulics said to automatically direct the right amount of flow to the implements based on operating conditions, and a 25% increase in lift force and a 16% increase in tilt force over its 980H predecessor are said to be other important qualities in the 980K. The loader also features electro-hydraulic steering with joystick or steering wheel control, plus an optional lock-up torque converter.
Additionally, the model’s fuel consumption is reduced because its hydraulic pumps only produce required flow. The 980K’s heat generation is also reduced, which decreases cooling requirements and average fan speed, resulting in additional fuel savings.
Like all Cat K Series wheeled loaders, the 980K retained the convenient, one-piece tilting hood introduced with the G Series.
However, a clamshell design introduced on the rear portion of the hood is said to allow quick access to the engine oil dipstick, oil fill, fuel fill and cooler cores for cleaning.
Overall, Cat describes the 980K as a productive and cost-effective tool in quarry, aggregates, construction and other high volume applications.
EXCAVATORS
Hitachi Zaxis 670
Doosan DX 420
WHEELED LOADERS
Caterpillar 980H,
Caterpillar 972H
Caterpillar 980K
Volvo 220F
CRUSHERS & SCREENS
Metso Lokotrack LT125 jaw crusher
Metso Lokotrack LT550GPF cone crusher
Metso Lokotrack LT300GPB cone crusher
BREAKERS
Sandvik Rammer
Metso’s crushing giant
Metso claims its Lokotrack LT125 mobile jaw crusher, the first stage crushing model at Lemminkäinen’s Myllykylä site, is the world´s most popular unit in its class for primary crushing in quarries.
Its heavy duty design is said to guarantee years of reliable service, and as well as being ideal for efficient primary crushing in quarries, the LT125 is also perfectly suited for use as a stand-alone unit or as part of a multistage process. As at Myllykylä, it can easily be connected to a mobile conveying system, such as an LL Series mobile conveyor system, to avoid trucking of the primary crushed material.
Said to be ideal for rapid installation, the LT125 ‘Split’ version is described by Metso as the ultimate primary crusher for contracting purposes. This special version is equipped with hydraulic legs for dismantling the crusher and feeder units. The unit can be set up within hours without the need for a crane.