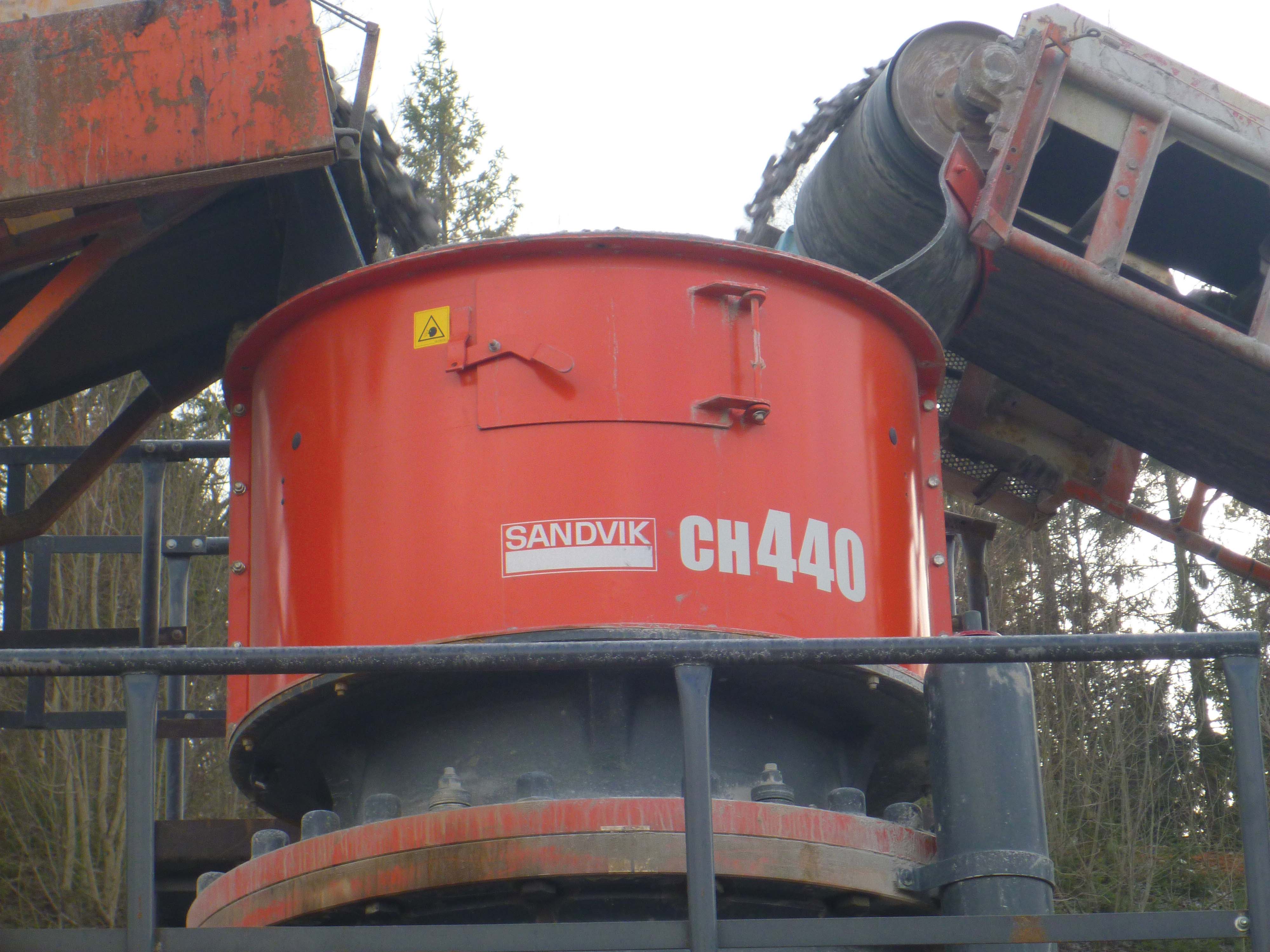
Swerock supplies a diverse product range from its quarry in Klippan, southern Sweden, for use as construction aggregate as well as in the manufacture of asphalt and concrete. In order to ensure that customer requirements are met, the quarrying company, part of the Peab construction group, has expanded vertically in the value chain through the development of its own transport company. More recently it provided itself with what it says is extra peace of mind through taking advantage of the newly-developed extended warranty scheme from Sandvik Construction.
The key to successful quarrying operations now encompasses expertise, professionalism and investment in equipment for production and distribution.
Swerock’s Klippan quarry has followed this mantra by developing its own distribution fleet and by acquiring the state-of-the-art
However, as customers become more demanding, and the market becomes more competitive, quarrying operations now require that little bit more to ensure that production interruptions, through equipment problems, are kept to the bare minimum.
In order to minimise the risk of interruptions to production through equipment problems, Swerock’s Klippan quarry recently took advantage of a new after-market package from Sandvik Construction, the Security+.
This has been done as “it is nice to have peace of mind,” says Bengt Svensson, plant manager of the Klippan quarry.
According to Sandvik Construction, the reasons why he was keen on the package are simple to understand as the essential premise of Security+ is that when in heavy use, such as at the Klippan quarry, even the best of equipment is bound to suffer from some unexpected failures. Thus in order to help protect against unpleasant surprises, Sandvik developed Security+. It essentially consists of a comprehensive insurance package for Sandvik jaw, cone (such as Swerock’s CH440) and VSI crushers, extending the standard 12-month warranty period up to ten years. During the coverage period a professional Sandvik service team repairs the covered components using only genuine Sandvik parts. Within the Security+ programme Sandvik also arranges professional inspections at agreed intervals to ensure the equipment is kept performing to the required levels.
Granitic gneiss
The Swerock Klippan quarry, which began its operational life in 1998 will certainly benefit as the quarry currently produces in excess of 500,000tonnes of rock each year. Approximately 50% of the production is used at the asphalt production plant close to the quarry with the balance of the material being used by
The rock found at the quarry comprises principally of granitic gneiss, and some diabase. The gneiss, due to its specific geological qualities, is highly valued by concrete and cement manufacturers while the diabase, which is unsuited for concrete and cement manufacturing, has proved to be ideal for aggregates used in road construction.
Material for production, which is crushed at the face, is gathered after blasting and this is carried out about 20 times a year, with holes drilled using a Sandvik DX780 hydraulic, self-propelled, self-contained and crawler-based surface rig with an ergonomic, high-visibility cabin and a rod handling system.
There are two
Current production requirements, due to customer preferences, are focused on the production of 8-11mm and 11-16mm fractions with a 4-8mm fraction also being produced when required. These sizes have proved to be ideal for cement and concrete manufacturing, whereas the 0-32mm, 0-45mm and 0-90mm sizes are ideal for road construction.
Starka, the main external customer of Klippan quarry, also has a requirement for different sizes of aggregate as it produces and prefabricates paving stones, which are used in the construction industry and for domestic gardens.
In order to produce such a wide variety of aggregate, for diverse applications, Swerock has invested in an impressive range of crushing and screening equipment.
This currently consists of a primary mobile
Sandvik screens
All screens are manufactured and supplied by Sandvik Construction, and are used to ensure that the fine fractions of 0-2mm, 0-4mm, 4-8mm, 8-11mm and 11-16mm are produced as accurately and efficiently as possible.
In order that the Sandvik equipment used by Swerock is kept in the best possible condition, the company utilised the Sandvik Security+ to ensure that the stringent production requirements of its customers are satisfied through increased up-time.
This is ensured as a key feature of Security+ includes regular proactive inspection and equipment maintenance. Thus a professional Sandvik service engineer performs machine audits at least once a year, according to an 80-point checklist. The audit provides an accurate estimation of upcoming wear part changes and expenses, which helps guarantee the crusher’s availability and safety.
As regular proactive maintenance is a key feature of the package, Swerock’s equipment is able to operate at full efficiency, as it provides with defence against the unexpected occurring, with the detection of problems that could cause large-scale damage being an essential feature.
Hauling
1 x Volvo A35 ADT
EXCAVATORS
1 x Caterpillar 365
1 x Caterpillar 336 Hybrid
WHEELED LOADERS
2 x Caterpillar 980K wheeled loaders
1 x Caterpillar 972K wheeled loader
1 x Caterpillar 972G wheeled loaderWashing
1 x CDE plant
Drilling
1 x Sandvik
DX780 drill rig
Crushing/Screening
1 x Metso LT125 primary mobile
1 x CM6800 Stinger
secondary crusher
(produced by Sandvik Finland)
1 x Metso G2610 spider
tertiary crusher
1 x Sandvik CH440
quaternary crusher
1 x VSI Sandvik rotor retrofitSecurity + thus focuses on preserving the operational bottom line, through enabling a more controlled operation, allowing Swerock to benefit from increased up-time, higher productivity, profit and peace of mind.
A key piece of equipment used by Swerock at the Klippan quarry is the Sandvik CH440, a cone crusher of advanced design, possessing a high capacity in relation to size; high reduction efficiency and able to produce excellent product shape.
With hydraulically adjusted closed side settings (CSS), optional automation, a choice of several different crushing chambers, and many other high performance features, the CH440 is versatile, user-friendly and highly productive, proving to be ideal for Swerock’s quaternary crushing requirements.
Enhancing the production of the Klippan quarry the CH440 possesses automatic overload protection, and is equipped with Sandvik’s revolutionary automatic setting system, ASRi. The system optimises cone crusher efficiency by automatically adapting the crusher to variations in feed conditions. By continuously measuring and compensating for crusher liner wear, ASRi allows Swerock to fully utilise crusher liners, and to schedule liner replacements in order to coincide with the planned maintenance provided Security+.
The ASRi also assists in keeping the crusher choke fed thus maximising rock-on-rock crushing, which helps to optimise the quality of the final product.
Reduced vibration and noise pollution also result as the CH440 is equipped with Sandvik lightweight polymer linings for wear protection and noise reduction, producing a better working environment and longer wear life.
Several standard crushing chambers are available for each model, which means the crushers may be easily matched to changes in production through selecting the right crushing chamber and eccentric throw. Such an essential piece of equipment to Swerock’s production process is also protected by the Security+ scheme.
Swerock has shown that the use of the best equipment, such as the CH440 cone crusher, is sometimes not enough to ensure that customers’ requirements are satisfied.