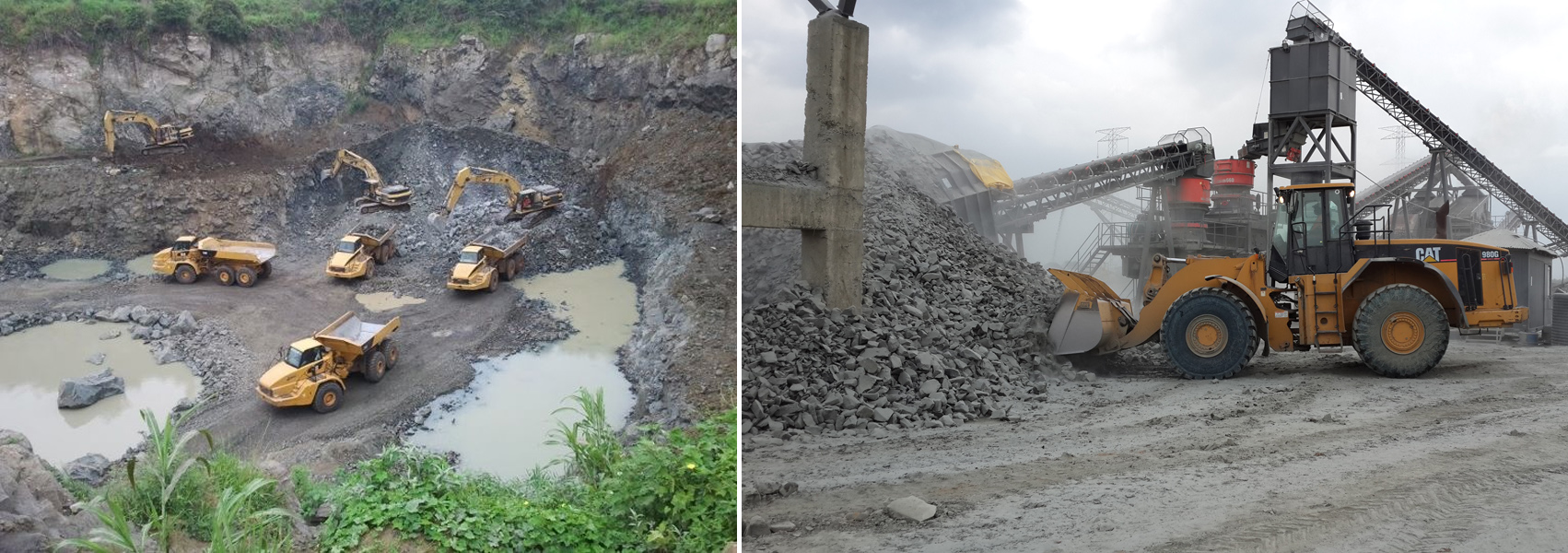
Recent data from Nigeria’s statistics office indicate that the country has surpassed South Africa as Africa’s largest economy.
Nigeria’s Bureau of Statistics said the country’s gross domestic product (GDP) for 2013 totalled US$509.9 billion, an increase from the $258 billion estimated before a rebasing calculation.
According to reports, Africa’s most populous country with 170 million people and the continent’s top oil producer has been growing as a destination for foreign investors owing to the size of its consumer market and increasingly sophisticated capital markets.
The new figure shrank Nigeria’s debt-to-GDP ratio to 11% for 2013, against 19% in 2012, says statistics chief Yemi Kale, who pointed out that the growing attention from foreign investors is forcing Nigeria to more accurately calculate its statistics, including GDP, adding that the base year would now be recalibrated every five years, in line with global norms.
And while the previous largest economy, South Africa, has the best infrastructure on the continent, most notably a power sector that generates ten times as much electricity as Nigeria, the west African country will be keen to catch up.
Analysts argue that the new calculations could increase the monetary size of Nigeria’s economy by as much as 60% or 70%.
And with the growing demand for construction materials in Nigeria, Asphalt Unity Construction, which has its headquarters in Port Harcourt, Rivers State, is increasing its production capacity at its quarry the quarry in Eziama Lokpaukwu Umuchieze, Umuneochi lga, Abia State in the east of the country.
To help achieve this expansion the company turned once again to
The history of the quarry started in 2010 when Mario El Fadi, the company’s managing director, had the idea of producing a big volumes of chipping granites to cater for the high demand for such materials for road construction in Nigeria. He convinced his partners to agree to buy a big crusher from Sandvik to produce up to 600tonnes/hour.
Asphalt Unity Construction is now a multifaceted civil engineering company which was formed when young, dynamic and vastly experienced engineers from different establishments came together to put their knowledge and experience to work.
Their aim was to deliver high quality civil engineering services for their clients, utilising competent personnel and good quality equipment. Now they have become one of the leading construction companies in the eastern region of Nigeria.
Work smarter
The company’s main material application is crushing basalt and granite to be sold on to building contractors for use as an aggregate in construction projects such as road base, concrete aggregate, asphalt pavement aggregate and railroad ballast.
With a focus on delivering high quality, in recent years the company has looked to work smarter and become more competitive.
Having already experienced what Sandvik stationary crushers can produce, it decided to consider the Sandvik Construction Mobile Crushers and Screens’ portfolio to help it achieve its annual production target, thereby meeting the industry demands in the Nigerian Delta State.
Mario El Fadi visited the Sandvik Construction Mobiles’ production facility in the UK in September 2013, where he was accompanied by Marshall John, business line manager for Sandvik Construction in Nigeria.
“During his visit, Mario El Fadi was able to clearly see the benefits offered by the mobile plant, and after seeking information from key product specialists at the factory, consequently placed an order for five tracked units,” says Sandvik.
“Sandvik Mobiles offer a huge amount of flexibility, with quick set up times and reliability and this is what Asphalt Unity Construction required.”
Mario El Fadi says: “We wanted a quick win situation in order to achieve our targeted capacity, and one of the huge advantages of mobile equipment is that no installation is required. We are able to quickly set the equipment up and start production almost immediately.”
With the mobile screens and crushers working alongside the stationary models, Asphalt Unity Construction will also benefit from using one set of parts, helping it to keep costs to a minimum.”
To meet the high capacity requirements of up to 700tonnes/hour, Asphalt Unity Construction chose from the Sandvik Mobiles heavy duty (HD) and extra heavy duty (XHD) portfolio, selecting the UJ640 jaw crusher (fitted with a CH660 crusher) together with the US440i and UH640 cone crushers to work alongside two QA451 Doublescreens.
The main required product sizes are 0-25mm and 0-35mm, although the company also produces the finished products sizes of 0-5mm, 5-15mm, 15-25mm, 25-32mm, 0-50mm, 0-300mm.
The combination of jaw and cone crusher means the abrasive material can be broken down easily to these levels, with the jaw breaking down the material and the cone providing the shaping.
The UJ640 is a tracked jaw crusher that has been purpose-designed for the global aggregates industry, and features the Sandvik CJ615 jaw. The crusher is a single toggle 1,500mm x 1,100mm piece of equipment which provides enormous rates of production due to it being able to accept a maximum feed size of 975mm. Working alongside the jaw are the US440i and UH640 cone crushers.
The US440i cone crusher is capable of accepting a feed size of up to 450mm, and is designed for the large mine or quarry operator. It allows Asphalt Unity Construction to maximise its primary jaw production by opening CSS for maximum throughput. It also features the Sandvik CS440 cone crusher, which is available with a wide choice of mantles and settings, making it suitable for a huge range of different applications worldwide.
Similarly, the UH640 is a flexible, highly productive secondary or tertiary cone crusher that is able to produce finished sized products thanks to an integral product screen and closed circuit operation. It also accepts a maximum feed size of 235mm.
Sandvik says one of the keys to the high productivity and efficiency of its cone crushers is the automatic setting system, ASRi, which optimises the crushing process. Hauling
15 x Caterpillar 740 articulated dump trucks (ADTs)
Drills
4 xTamrock Pantera 1100 wagon drills
Wheeled Loaders
Caterpillar 980G wheeled loaders
Loading
12 x Caterpillar 345B L series hydraulic excavatorsCrushers
1 x Sandvik UJ640 tracked jaw crusher
1 x Sandvik US440i cone crusher
1 x Sandvik UH640 cone crusher
Screening
2 x QA451 Doublescreens
Triple-deck Doublescreen
By continuously measuring and compensating for crusher liner wear, ASRi allows for optimal utilisation of crusher liners and enables liner replacements to be scheduled to coincide with planned maintenance stops.
The ASRi also assists in keeping the crusher choke fed in order to maximise rock-on-rock crushing, which helps ensure the highest quality end product.
Asphalt Unity also utilises a QA451, the world’s only triple-deck Doublescreen. This features two inline 3,048mm x 1,524mm screen boxes for and is designed specifically to work in closed-circuit with tracked crushers. The hydraulically folding fourth product conveyor slews and raises/lowers hydraulically to optimise the feeding position to these upstream units.
Utilising Sandvik’s patented Doublescreen technology, the advanced triple-deck Doublescreen system allows for individual changes to the drive, angling, vibration and meshes of each screen box, which allows for versatility in size and specification of the finished products.
Following the success of the mobile screens and crushers on its basalt application, Asphalt Unity Construction is looking to expand its fleet of equipment to help the company reach a new goal of 1,500tonnes/hour.
The quarry, which is up to 12 hectares, employs 150 people, and it is different because of the good quality of the stone and the low expenses involved in obtaining it through drilling and blasting.
The drilling and blasting is carried out twice a week providing some 30,000tonnes of basalt and dolerite, giving a total rock removal of about 120,000 a month. In total some 1.45 million tonnes/year is produced.
Asphalt Unity Construction operates four Tamrock Pantera 1100 wagon drills which were delivered in 2006. The Pantera 1100 is a hydraulic, self-propelled, self-contained, crawler-based surface drilling rig equipped with a cabin and a rod changer. It drills 89-140mm vertical, inclined or horizontal holes with 51mm and 60mm extension rods or 102-152mm vertical, inclined or horizontal holes with 76 and 87mm tubes.
It is equipped with HL 1010, hydraulic top hammer rock drill, and with high rotation torque, proper flushing and a sophisticated, ergonomic Rock Pilot control system the rig adapts itself easily into varying rock conditions.
The Pantera 1100 is designed for efficient production drilling in medium large to large quarries or open pit mines and construction work sites.
Following drilling and blasting, material is loaded into one of Asphalt Unity Construction’s
The company’s Caterpillar 980G wheeled loaders are used to load the finished products onto double trailers and short tippers, and for other duties around the quarry.
The company also operates a 180tonnes/hour Wibau asphalt plant for road repair and construction works which are carried out using a variety of equipment including Blaw-Knox and Marini pavers along with