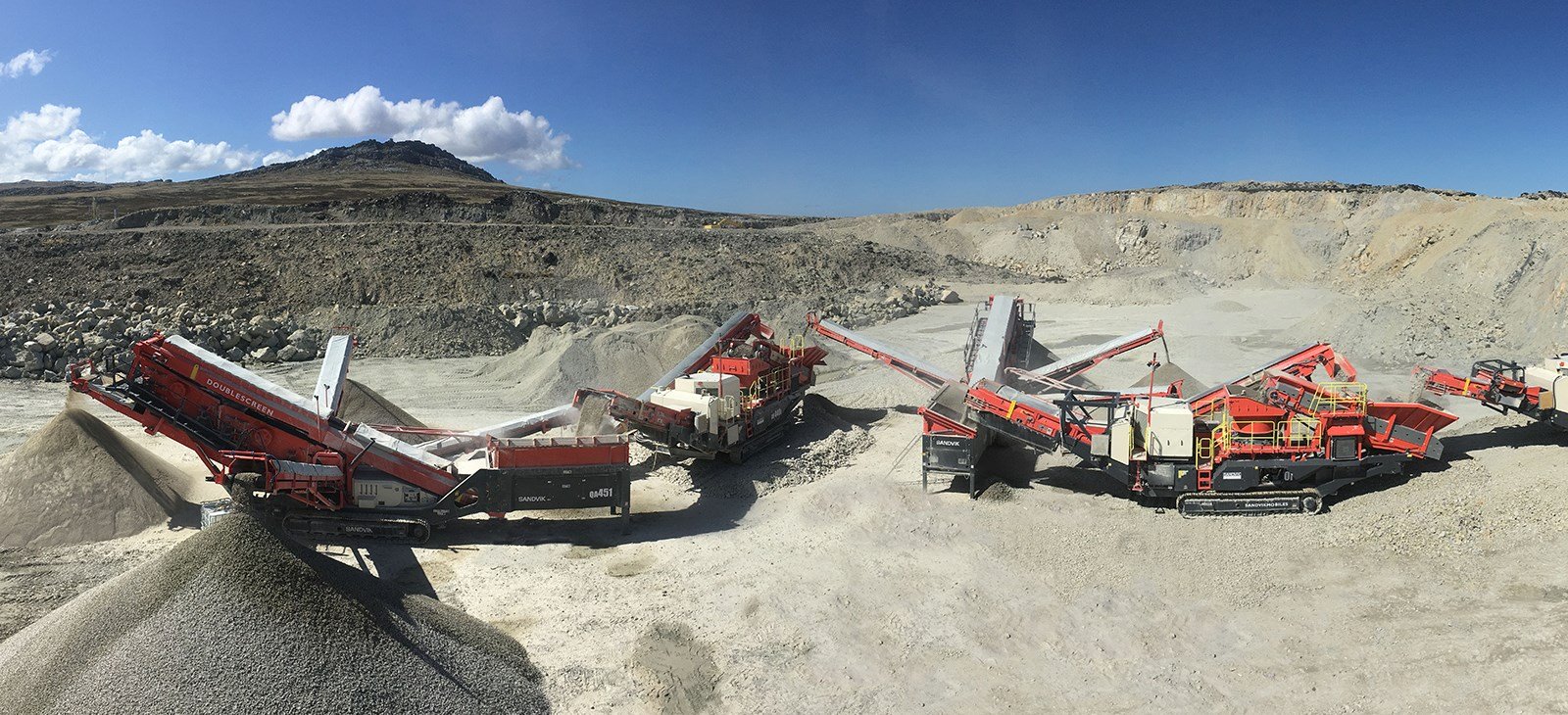
Despite its isolated position on East Falkland, Pony’s Pass quarry is a booming site which annually produces 160,000 tons of quartzitic sandstone using a state-of-the-art mobile crushing and screening train.
Sandvik Mobiles has advised the quarry on a train of equipment to best compliment the uptime required for an operation of this scale. The chosen crushers and screens comprise of a UJ440i jaw crusher, two UH440i cone crushers, a QI442HS impactor and two QA451 triple deck Doublescreens.
Due to the differing requirements by customers, the crushing and screening equipment has to guarantee productivity, be durable in design and offer the operators flexibility in what they produce. The quarry currently provides perfectly sized aggregates for road construction and infrastructure development projects as well as supplying an on-site asphalt plant. Future developments are likely to see the current 160,000 tons annual production increase to over 300,000 tons per year.
Due to the isolated geographic position, over 300 miles from the mainland of Latin America, and the extreme weather conditions that are frequent, this meant that the solution chosen had to tackle all potential challenges. As the only Falkland Islands quarry, almost every project on the island requires aggregates from Pony’s Pass, meaning service and aftermarket support is also a vital component to keep operations running smoothly.
The Sandvik equipment has performed with output levels always meeting expectations, according to Pony’s Pass quarry manager Marc Short, who added: “We currently use our mobile crushers to produce three small end materials: these being 10/20mm, 5/10mm and 0/5mm crusher dust. However, we have the ability to produce type 1 (all in 0/32mm) and secondary crusher run all in (0/75mm). These machines are tracked up to the blast site (currently located in the bottom of the quarry) where they are fed with as-blasted material.”
The feed material is crushed quarzitic sandstone, with a maximum feed size of 700mm.
The abrasive nature of the rock and the need for machines that can deliver maximized uptime meant that it was essential for the quarry to have a durable and productive primary jaw crusher before the material is passed through to the secondary crushing stage. The heavy duty UJ440i jaw crusher provides jaw settings that are easily adjusted hydraulically with a choice of jaw plates to suit the needs of the operation. This means that the crusher can work at optimum levels for longer periods, with all impact zones having a rubber lining to reduce wear and noise. In addition, the 62.5 ton crusher has a 1,200 x 830mm jaw opening enabling it to deal with Pony’s Pass’ 700mm feed. The UJ440i can crush at a throughput of 250mtph.
Following on from the UJ440i jaw crusher, the rock is then fed into the UH440i cone crushers and the Doublescreens for precision sizing. Sandvik claims that its QA451 is the world’s first triple deck Doublescreen, whilst the 50 ton UH440i cone crushers are specifically aimed at large scale aggregates producers’ requirements. The result is the production of fractions the quarry’s customers require.
“0/5mm, 5/10mm and 10/20mm is used for concrete and asphalt production," said Short. "Type 1, secondary and crusher dust is used for road construction. Some of the larger products are also used to build up sites with fill etc.”
He added that one of the main reasons for choosing Sandvik was the fact that the quarry already has the same type of cone crushers on the site which is beneficial for compatibility.
"We also already use two Sandvik drill rigs on site which adds to this," said Short. "A lot of research was carried out prior to committing to Sandvik, they proved to be a good return in investment. The procurement of a mobile crushing train was a huge commitment and investment which took a lot of research. In the end, these particular machines best suited our requirements.”
In addition to the above, the highway’s section acquired a QI442HS impactor to provide primary and secondary crushing and screening in one unit. The features include a new rotor position and locking device, innovative hammer locking wedges for quicker removal and fitting, as well as a new wedge removal tool to provide safer installation and removal. This means that it is also able to deliver a wide range of high reduction ratios, superb product shape and outstanding uptime which are essential to the requirements of the island’s authority.
Short said that the service and support from Sandvik has been excellent, with queries always answered immediately. He explained why good support is essential: “There are 24 employees on site consisting of operators, labourers, shotfirers, drillers, a laboratory technician, two foremen and two managers. This number of employees is required as everything has to be done on site; there is no opportunity to use contract shotfirers and drillers. They must all be trained internally.”
All the supplied equipment comes with Sandvik’s My Fleet remote monitoring system. My Fleet telematics helps customers know exactly how their machines are being utilised and helps to facilitate accurate production forecasting.
The Sandvik mobile crushing and screening equipment has now been operational since the beginning of 2020. Despite the hostile operating environment, it has consistently proved itself in one of the harshest and most isolated arenas in the world. Due to the robust and efficient design of the equipment and the excellent aftermarket support provided, Pony’s Pass quarry is now set to gear up to producing the extra aggregates the islands require. It faces the future with confidence that its new crushing and screening train is tough enough, reliable enough and productive enough. They are also confident that Sandvik Mobiles can offer expert professional service and aftermarket support if any challenges arise along the way.