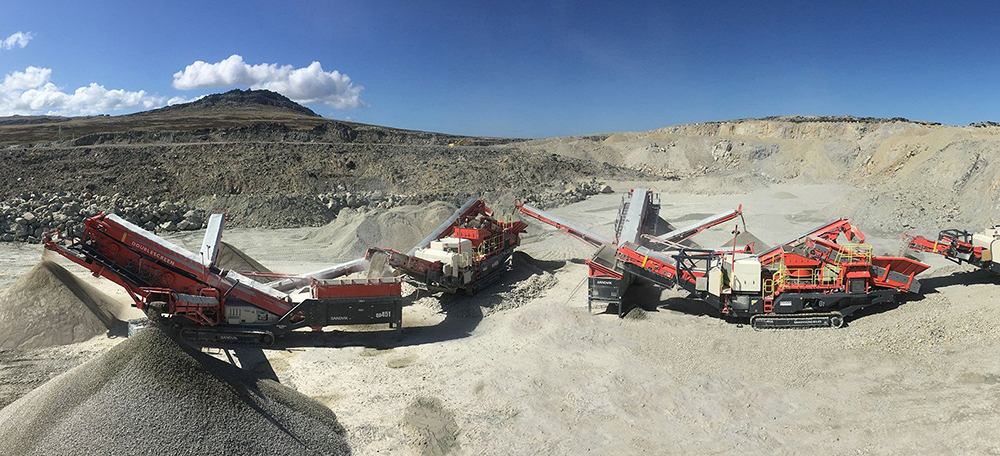
Pony’s Pass Quarry in the Falkland Islands has invested in three new crushers, an impactor and two triple deck screens. Despite its isolated position on East Falkland, the quarry is a booming site which annually produces 160,000 tonnes of quartzitic sandstone using a state-of-the-art mobile crushing and screening train.
Sandvik Mobiles has advised the quarry on a train of equipment to best complement the uptime required for an operation of this scale. The chosen crushers and screens have been deployed since the start of 2020 and comprise a UJ440i jaw crusher, two UH440i cone crushers, a QI442HS impactor and two QA451 triple deck doublescreens.
Pony’s Pass currently provides perfectly sized aggregates for road construction and infrastructure development projects as well as supplying an on-site asphalt plant. Future developments are likely to see the current 160,000 tonnes annual production increase to over 300,000 tonnes per year.
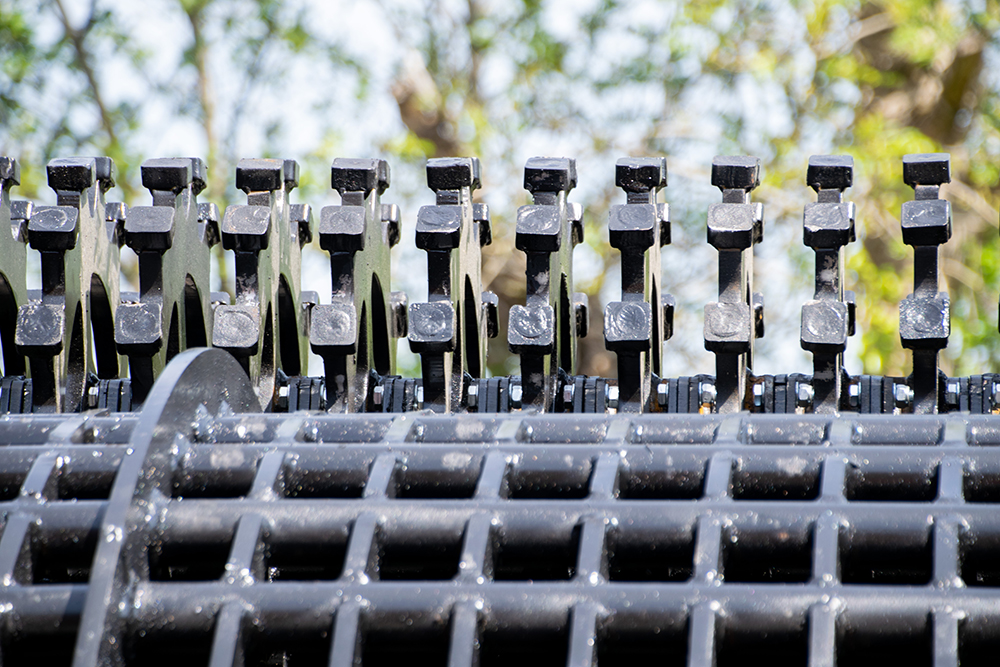
Due to the isolated geographic position, over 300 miles from the mainland of Latin America, and the extreme weather conditions that are frequent, this meant that the solution chosen had to tackle all potential challenges. As the only Falkland Islands quarry, almost every project on the island requires aggregates from Pony’s Pass, meaning service and aftermarket support is also a vital component to keep operations running smoothly.
The new equipment has performed with output levels always meeting expectations, according to Pony’s Pass quarry manager Marc Short, who added: “We currently use our mobile crushers to produce three small end materials: these being 10/20mm, 5/10mm and 0/5mm crusher dust. However, we have the ability to produce type 1 (all in 0/32mm) and secondary crusher run (all in 0/75mm). These machines are tracked up to the blast site (currently located in the bottom of the quarry) where they are fed with as-blasted material.”
The feed material is crushed quarzitic sandstone, with a maximum feed size of 700mm.
The abrasive nature of the rock and the need for machines that can deliver maximised uptime meant that it was essential for the quarry to have a durable and productive primary jaw crusher before the material is passed through to the secondary crushing stage.
The heavy duty UJ440i jaw crusher provides jaw settings that can be adjusted hydraulically with a choice of jaw plates to suit the needs of the operation. This means that the crusher can work at optimum levels for longer periods, with all impact zones having a rubber lining to reduce wear and noise. In addition, the 62.5 tonne crusher has a 1,200 x 830mm jaw opening enabling it to deal with Pony’s Pass’ 700mm feed. The UJ440i can crush at a throughput of 250mtph.
Following on from the UJ440i jaw crusher, the rock is then fed into the UH440i cone crushers and the doublescreens for precision sizing. Sandvik claims that its QA451 is the world’s first triple deck doublescreen, whilst the 50 tonne UH440i cone crushers are specifically aimed at large-scale aggregates producers’ requirements. The result is the production of fractions the quarry’s customers require.
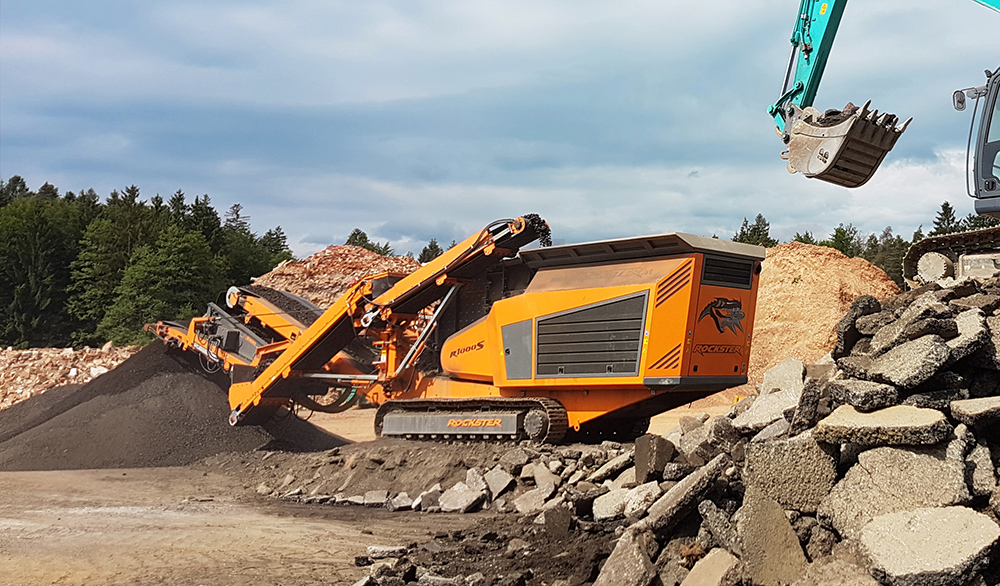
“0/5mm, 5/10mm and 10/20mm is used for concrete and asphalt production,” said Short. “Type 1, secondary and crusher dust is used for road construction. Some of the larger products are also used to build up sites with fill etc.”
He added that one of the main reasons for choosing Sandvik was the fact that the quarry already has the same type of cone crushers on the site which is beneficial for compatibility.
“We also already use two Sandvik drill rigs on site which adds to this,” said Short. “A lot of research was carried out prior to committing to Sandvik, they proved to be a good return in investment. The procurement of a mobile crushing train was a huge commitment and investment which took a lot of research. In the end, these particular machines best suited our requirements.”
In addition to the above, the highway’s section acquired a QI442HS impactor to provide primary and secondary crushing and screening in one unit. The features include a new rotor position and locking device, innovative hammer-locking wedges for quicker removal and fitting, as well as a new wedge removal tool to provide safer installation and removal. This means that it is also able to deliver a wide range of high reduction ratios, superb product shape and outstanding uptime which are essential to the requirements of the island’s authority.
UK trommel screen and accessories manufacturer MDS says its new drum cleaner is a “game changer” for the trommel market.
The trommel drum cleaner features a cog wheel-style configuration that meshes with the drum openings and punches out the holes to keep them clean. The cleaner is designed to replace the traditional method of trying to brush trommels clean.
MDS says the drum cleaner is at its happiest when punching out the soils and clays that traditionally blind over scalpers in both quarries and recycling yards.
Luke Jones, quarry manager for Whitelock Developments, near Skipton, North Yorkshire, England, said: “Without the [MDS] drum cleaner we wouldn’t have been able to screen our wet and sticky recycled products. It gives us a competitive advantage in the market when others can’t produce clean aggregate material.”
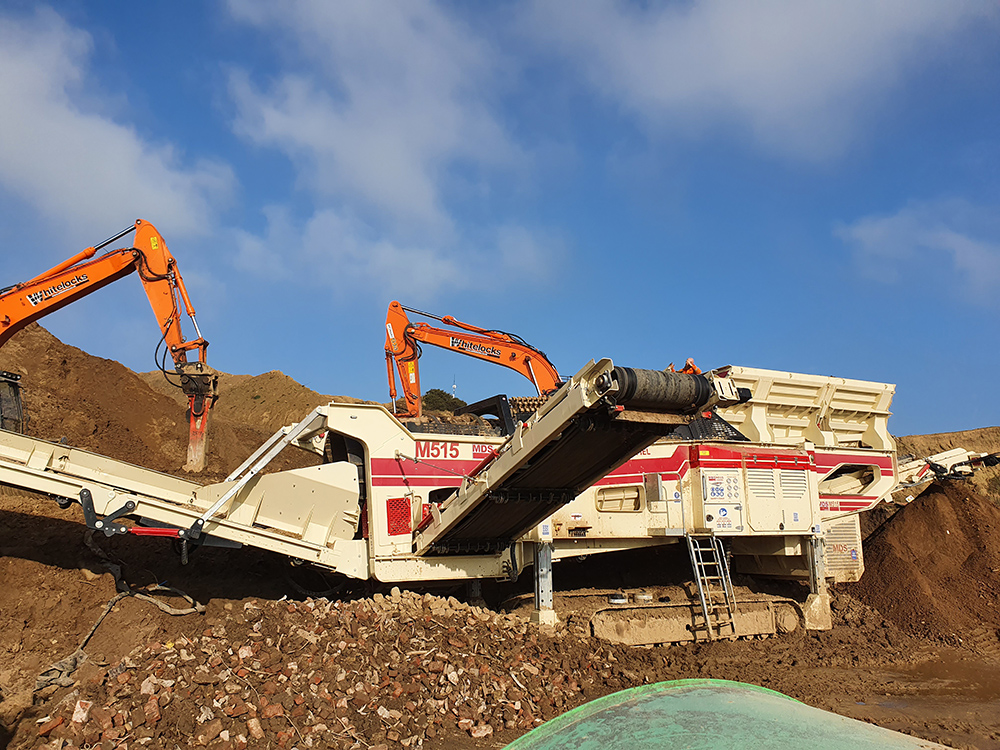
All the current MDS trommel range can be fitted with the drum cleaner. This includes the tracked range (M412, M413, M515 two or three split, and M518R) and the static range (M615, M620, M720, M820 and M925).
MDS says its business has continued to grow despite the global pandemic, and the company has made a 15,000 square feet extension adjacent to its current factory.
The new unit will provide increased production capability for the existing range in addition to extra capacity for new product introductions such as the M518R and other trommels that are planned for launch in 2021.
The company says business growth and an increasing worldwide demand for its products has meant the new facility is a necessity to maintain its existing lead times.
Jason Purllant, MDS UK and EU sales manager, commented: “We needed to maintain our target of 6-8 weeks lead time on all products whilst introducing new products into the range.”
MDS CEO Liam Murray added: “We are really excited about the continuing growth of our business globally with new dealers being appointed all around the world.
“We plan to have an open day towards the end of the year to celebrate the opening but also give future and current customers the chance to see first-hand what we do at MDS.”
Austria-based Bauhof Deutschlandsberg is a major player in the country’s provision of high-quality recycled building materials. As part of its recycling activities the company has deployed a Rockster R1000S closed-circuit impact crusher with a screening system & air blower since the beginning of 2020.
In addition to a trommel screen, excavators, loaders and road rollers, Bauhof has also previously used a rented crushing plant which processed around 40,000 tonnes of debris, asphalt and concrete per year.
At the end of 2019, the company decided to replace this rented plant with a new closed-circuit impact crusher R1000S from Rockster.
The company says the crusher has three major assets in terms of guaranteeing high quality of the end-product in one workflow: a screening system for a precisely defined size of end-product; a magnetic separator for removing iron and other metals, and an air blower for separating non-aggregates such as polystyrene, wood, plastic, paper and similar.
“To be honest, we were surprised at how well the Rockster Air Blower works, especially when it comes to recycling debris, it brings a huge increase in efficiency,” says Pistolnig.
Since being deployed in January, the R1000S has already produced 16,000 tonnes of concrete 0/80, 8,000 tonnes of asphalt 0/18, 600 tonnes of wall ballast 0/16 and 500 tonnes of construction debris 0/20.
“We are extremely satisfied with the quality of the end-product,” Pistolnig adds. “The mixture of coarser and fine grain is just right for further use in the concrete mixing plant or on construction sites.” Rockster’s hydrostatic crusher drive is particularly responsible for the sizes of the final product to be precisely adjusted to the desired quality.

Bauhof’s processing capacity is 80,000 tonnes per year - which corresponds to a saved landfill volume of 55,000m³ - and it has a recycling rate of 98%. Its principle expertise is in building demolition, container services and the recycling of all types of construction debris.
Pistolnig commented: “The management of construction waste is of growing interest for both the construction industry and waste management. Residual building materials that do not end up in a landfill but are returned to the economic cycle as high-quality RC [recycled] building materials are an ecological necessity.”
Lars Bräunling, director of product technology at wire screen manufacturer MAJOR, says that self-cleaning screen media offers a number of benefits, including the elimination of pegging and blinding for aggregate and mining operations. However, certain design characteristics, such as limited opening sizes, leave producers with little option on where to employ self-cleaning screen media in their operation. Because of this, self-cleaning screen media is often thought of only as a bottom deck solution.
Bräunling adds that, recognising the opportunity to take the principles of self-cleaning screens a step further, engineers looked for ways to increase durability and provide application-specific customisation for a productivity-boosting solution producers could use on any deck. The result was a new category of screen — high-performance screen media.
In terms of what makes high-performance media different, Bräunling says: “One of the biggest drawbacks of using traditional self-cleaning media on upper decks is that it cannot stand up to the impact and abrasive forces of larger material. High-performance screen media addresses these issues by incorporating enhanced wire and a unique structure to maximize durability and wear life.”
It begins with the wire, according to Bräunling. Wire quality plays an essential role in screen performance, and he says many manufacturers choose their wire based on current market prices, resulting in fluctuating wire quality and inconsistent performance. “Some manufacturers, on the other hand, rely on high-quality wire in their screen media to ensure consistent quality and durability. It offers improved molecular structure over other techniques for optimum tensile strength, hardness and ductility, resulting in the highest quality, longest-lasting wire.”
High-performance screen media’s strategically engineered wires are held together with polyurethane strips, eliminating the need for cross wires with high wear spots. This innovative design maximises open area and extends wear life as much as five times longer than wire alone — even on top decks.
Taking advantage of these design benefits, Bräunling says that producers who employ high-performance screens on the top deck are able to realize the screen media’s payoffs earlier in the screening process, as well.
He adds that stratification is one of the key benefits. “High-performance screen media wires vibrate independently from hook to hook under material contact, supplementing vibrations from the screen box with additional frequency to accelerate the stratification process.,” says Bräunling. “This added frequency can be as high as 8,000 to 10,000 cycles per minute — up to 13 times higher than the standard screen box vibration — helping fine material to stratify and pass through the screen faster.”
Optimising stratification at the very start of screening results in faster screening and optimal throughput, according to Bräunling. Greater quantities of fine material pass through the screen media’s open area earlier in the process, which increases the effective capacity of the machine and virtually eliminates carryover. Some aggregate and mining producers have shown as much as a 40% increase in overall production with high-performance screen media.
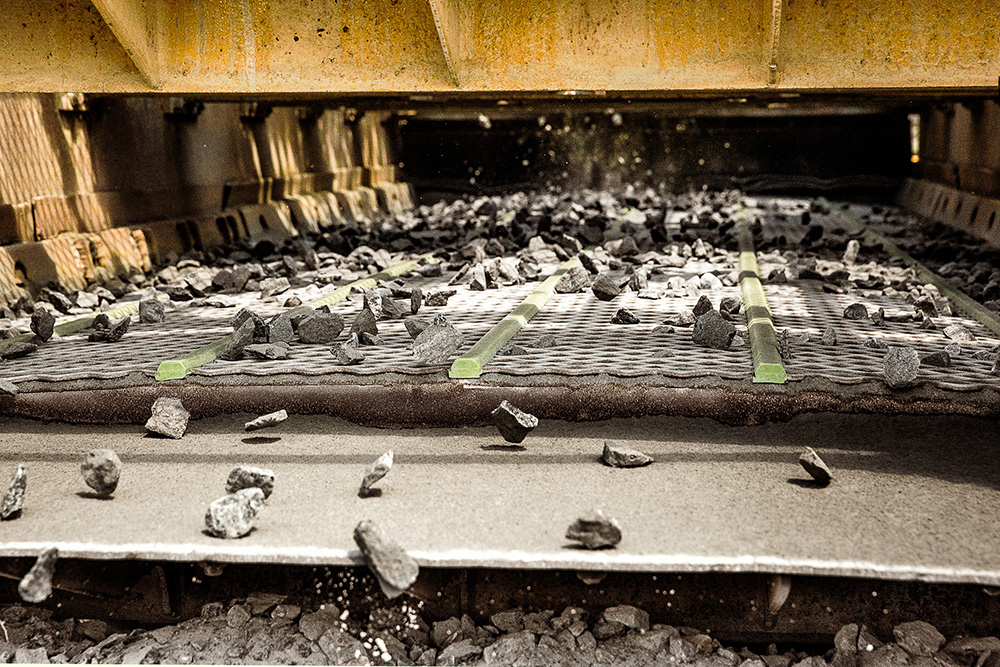
UK plant hire company P&L Barton - based in Carnforth, Lancashire - has reconfigured its EvoQuip Colt 1000 scalping screen to meet the requirements of the latest project it is involved in. The application has been to produce limestone walling stone for one of its regular clients where space was limited.
P&L Barton set about reconfiguring the Colt 1000 so that both conveyors discharged out the same side into segregated areas, maximising the area available and eliminating double handling.
Richard Barton, plant manager at P&L Barton, commented: “The Colt 1000 is the perfect machine for us due to its flexibility. Being suited to scalping and fine screening and the ability to quickly convert from 3-way to 2-way split and to swap conveyor configurations means it’s suitable for many applications and job sites.”
P&L Barton purchased the Colt 1000 in June 2019 from equipment supplier Blue Central, and since then the machine has been on hire contracts in multiple configurations to suit the required job sites. “We have been able to run the machine in 2-way split on one project then convert it so that mids and fines are discharged on the same side on a really compact site, and in standard set-up on another site,” said Barton. “With the range of media options available I don’t think there is any job she can’t do.”
P&L Barton started out in 1972 when Peter Barton invested in his first digger, a JCB 3C, and set up P Barton Plant Hire. Almost 50 years later the company remains a family-run business and has evolved and expanded working on a vast array of projects. Its clients include private households and businesses, local councils and large multi-nationals. It provides plant and services on a sub-contract or hire only basis, offering a wide range of services to the quarrying, construction, groundwork, civil engineering, recycling and haulage industries.
The Colt 1000 is able to operate in both heavy-duty scalping and precision-screening applications and is designed to manage the most difficult of materials. Flexibility is enhanced with configurable conveyor options and two-way split conversion. It features an aggressive double deck screen, variable screening angle with numerous screen media options, broad fines conveyor, quick set-up time and tall discharge heights.