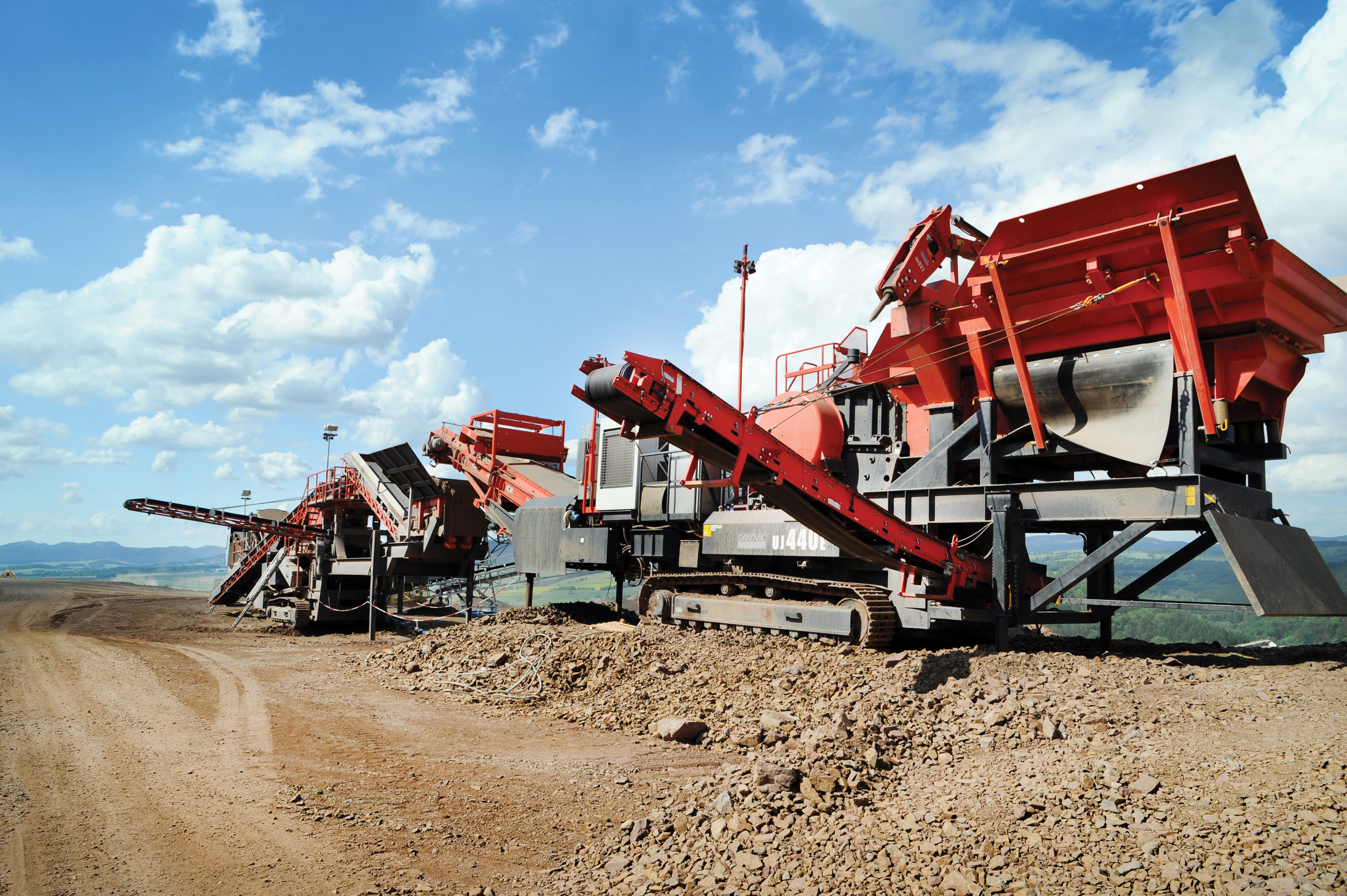
Increasing demand for high quality aggregate has seen a major investment in a state-of-the-art Polish quarry. Patrick Smith reports
What has been described as the most productive and modern quarry in Poland has started production.
When fully operational, the quarry near the small town of Tlumaczów, will be capable of producing up to 2.4 million tonnes of material each year.
The Tlumaczów Melaphyre Quarries (Tlumaczów Gardzie and Tlumaczów Wschód) are two melaphyre deposits located at the village of Tlumaczów, Klodzki County, Borough of Radków near Nowa Ruda.
Large melaphyre (a basalt composed of compact black or blackish-grey igneous rock, consisting of a matrix of labradorite and augite in which are embedded crystals of the same minerals, and sometimes uniaxial mica, hornblende and iron pyrite) deposits have been quarried since 2010.
The deposits were discovered over 100 years ago, and there was an operational quarry near Tlumaczów until the 1930s. Recently however, and due to the increasing demand for aggregate possessing the high quality of the Tlumaczów deposits, quarrying has resumed.
A modern stationary plant, together with related mobile screening and crushing equipment, supplied by
The plant will be one of the most advanced, efficient and productive operations in Poland.
The principal mover behind the redevelopment of the Tlumaczów Quarry was
Its success has been rapid, as in 2009, utilising the two melaphyre deposits as the basis of operations, Strateg Capital launched the Tlumaczów Melaphyre Quarry (TMQ).
The initial stages of quarrying operations saw the construction of the local railway line, which has allowed shipments of melaphyre aggregate to be resumed to customers throughout Poland.
The need for the construction of the railway line was identified at the outset of operations, as local government authorities did not grant approval for the transportation of the aggregates by trucks, a move it is claimed that would paralyse local traffic, increase the risk of road accidents and destroy the roadways.
The compromise agreement reached was to rebuild the mine railway siding together with 8km of track stretching from Tlumaczów to cinawka rednia.
Current production has until recently been in the region of 1 million tonnes per year, with the aggregate being produced by a mobile crushing and screening train, supplied by Sandvik Mining and Construction’s Polish distributor,
The train consists of a QI430 impact crusher, together with a UH640 cone crusher and UJ440E jaw crusher as well as other equipment.
According to Sandvik this modern, efficient and highly productive processing line has proved to be perfect for the initial stages of the operation, as the use of mobile crushers and screens has ensured that the produced material is of the highest quality, while minimising environmental harm and at the same time meeting the demands for the aggregates.
However, from the start of the redevelopment project it was decided to invest in the construction of a modern aggregate plant as the Tlumaczów plant needed to possess high levels of production quality, effectiveness and operational efficiencies to ensure profitable operation.
It was soon realised that the highest quality of material produced could only be guaranteed by not only high levels of technical quarrying expertise, but also through the use of some of the most advanced crushing and screening equipment.
As the melaphyre resources are estimated to last for 40 years, the investment in production capabilities has been assessed on the basis of a very long term plan.
After the first phase, which consisted of the construction of the railway line, it was essential to resume production as soon as possible, and hence production was based on the mobile crushing and screening train.
The next step however reinforced the long term objectives of the project, and underlined the major investment that has been required.
“The investment plans of Strateg Capital have always assumed construction of a modern stationary plant, which would achieve the required output of 2.4million tonnes with optimised costs, and at the same time focus on product quality. This is essential for the customers for our aggregate so that they can be assured they are dealing with a reliable partner," says Andrzej Kamierczak, sales, marketing and development manager at Strateg Capital.
With the stationary plant commissioned, and following a trial period to ensure that technical parameters are met, production targets achieved and product quality assured, the two operational mobile crushing lines will be decommissioned and removed. This will leave only the Sandvik mobile compound-aggregate plant (consisting of tracked UH640 and UJ440E cone and jaw crushers) in order to manufacture railway grade breakstone. A Sandvik DP1100 crawler drilling rig has proved to be “perfect for shot hole drilling,” and will continue to play an important role at the quarry.
Drilling and blasting at the quarry is performed by EPC Polska, a specialist business partner of the company with the Sandvik DP1100 drill rig. The rock is transported to the jaw crusher from the excavation site using a fleet of five
According to Sandvik, the Tlumaczów Quarry now operates the largest jaw crusher in Poland, the Sandvik CJ615, which was recently delivered, commissioned and made operational. The giant crusher was chosen specifically for its production capacities that currently exceed demand, and it is at the centre of the production process, and thus at the heart of the production line.
Andrzej Kamierczak explains: “We cannot afford any risk of choke points which would interrupt the production process, or decrease the product quality. This is why we have decided to erect a stationary plant.”
After loading the jaw crusher until loading ready goods onto railway wagons, the transport of rock is done automatically with the internal transport taking place in tunnels or covered conveyors.
Crushing
1 x Sandvik C65 jaw crusher
1 x Sandvik CH660 cone crusher
1 x Sandvik CH440 cone crusher
1 x Sandvik CH430 cone crusher
1 x Sandvik CV217 impact crusher
Plus
1 x Sandvik UJ440E jaw crusher
1 x Sandvik QI430 impact crusher
1 x Sandvik UH640 cone crusherScreening
1 x Sandvik CS173 two-deck
circular motion screen
1 x Sandvik two-deck SC2782 screen
2 x Sandvik CS173 circular motion
three-deck screen
1 x Sandvik three-deck SC2783 screen
1 x Sandvik SG1842 grizzly screenHauling
1 x Sandvik 815m long belt conveyor
(plus other conveyor systems)
5 x Caterpillar 772 trucksThe production process includes a buffer stock of 60,000tonnes after the jaw crusher. Underneath the buffer stock, rock material is taken through the tunnel via the conveyor system to the second stage (cone crushers); third stage (impact crushers) and fourth stage (special cubic impact crusher).
The material is screened and automatically transported to a buffer stock. Charging boxes over conveyors in tunnels beneath every pile are able to be set precisely to produce quality controlled grit mixes for sale.
Finished products are stored in the 16,000tonne buffer stock, and as with the first buffer stock, these are taken from each pile either directly to fully automatic self-moving loading machines with an effective loading capacity of 1,000tonnes/hour or to the ready goods warehouse, which is equipped with fully automatic stockpiling machinery. It also has an underground tunnel system with conveyors connected to loading machinery located on the rail tracks some 2km from the warehouse.
In addition to the CJ615 jaw crusher, the configuration of the stationary plant from Sandvik includes SH1661 reciprocating feeder; SG1842 grizzly screen; BR2064 hydraulic hammer; BB350 breaker boom; CH660 cone crusher with ASRi [Automated Setting Regulation intelligent] control system; CH440 cone crusher with ASRi; CH430 cone crusher with ASRi, and a CV217 impact crusher with third and fourth stage vertical crushing shafts (for grain formation).
Also included are a variety of screens: a CS173 two-deck circular motion screen; CS173 circular motion three-deck screen equipped with rubber screening media; a three-deck CS173 circular motion screen; three-deck SC2783 screen (newest circular motion screen generation); two-deck SC2782 screen (also the newest circular motion screen generation), and a 815m long belt conveyor.
Sandvik says the stationary equipment was chosen as it is engineered for maximum productivity offering advanced, customer-focused solutions for any material size reduction: essentially a total solutions package.
The extended offering includes such items as wear parts, extended warranty and retrofits, “with the focus on customer’s productivity and profitability.”
The company says that comprehensive knowledge of customer’s raw materials supported by an in-house laboratory with a full-scale test plant enables it to deliver plant-crusher optimisation audits at customers’ own sites.
This is accomplished through a dedicated engineering and quality team whose overall objective is to achieve zero defects in the supply chain processes, but at the same time never lose focus on the environment, health and safety.
Using the new equipment the quarry is now able to supply a wide range of products.
These include crushed sand 0/2mm; fine grain aggregate 0/5mm; grits 2-5, 5-8, 8-11, 11-16 and 16-22mm; key aggregate 5-31.5mm; railway breakstone 31.5-50mm; road breakstone 31.5-63mm; continuous grain size aggregate 0-31.5mm; continuous grain size aggregate 0-63mm; blends for frost-resistant layers 0-31.5mm; blends for frost-resistant layers 0-63mm, and hydro-technical stone.
“Crushing efficiency and environmental protection are often seen as mutually incompatible, but Sandvik places equal emphasis on both. For example, dust encapsulation improves the work environment, extends the life of equipment, and reduces clean-up costs thus improving process efficiency. This has proved to be essential at the Tlumaczów Quarry operation as the local authorities have stressed the need for tight environmental controls,” says Sandvik.
The resumption of quarrying at Tlumaczów has seen a major capital investment in the locality, infrastructure and production capabilities.
The high quality of the aggregate deposit has allowed TMQ to develop markets throughout Poland, and the use of Sandvik stationary and mobile equipment is said to have ensured flexibility of operation, achievement of production goals, and minimal environmental effects.