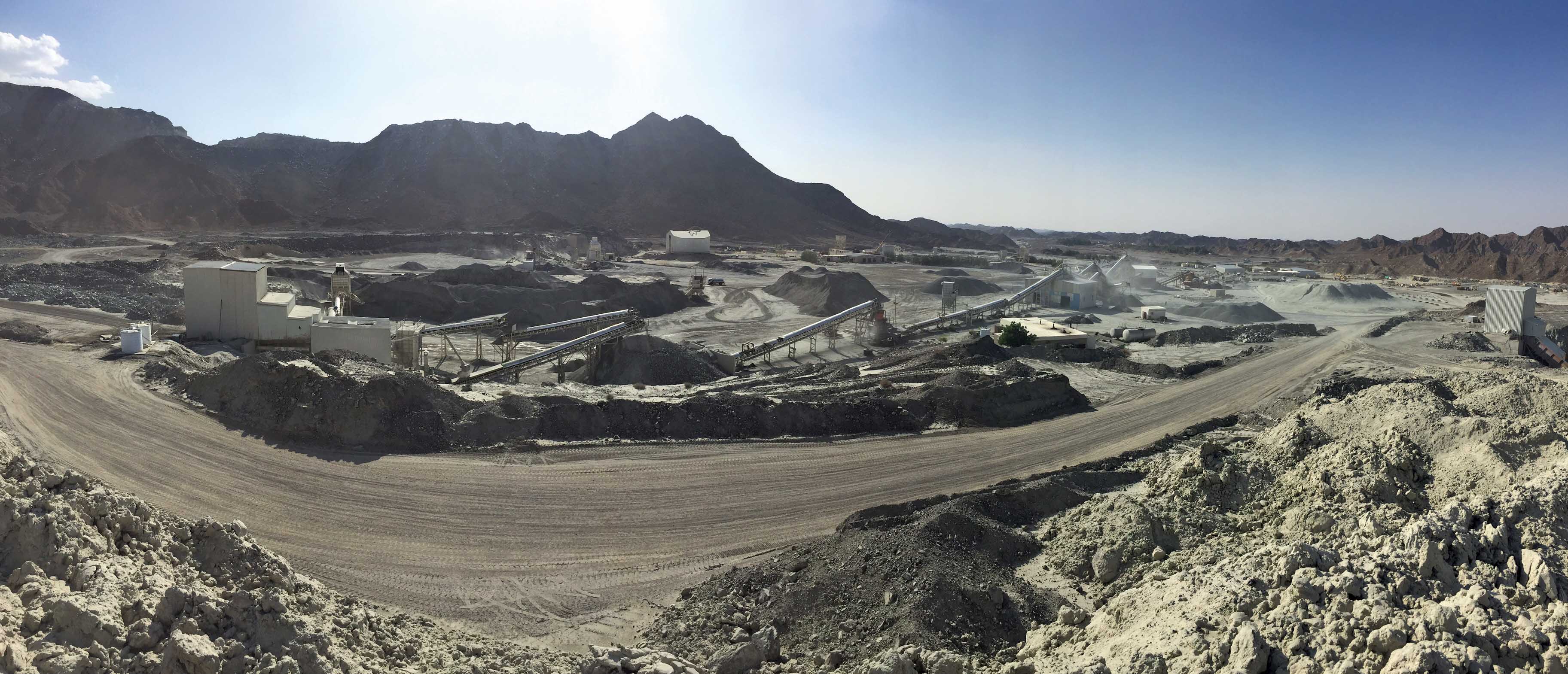
A high-performing Sandvik Construction cone crusher is said to have revolutionised production at a prominent aggregate supply firm in the United Arab Emirates. Guy Woodford reports.
National Quarries had a problem. The company’s existing crushing plant was doing satisfactory work, but its management felt performance was lacking. This led the UAE-based firm to approach
On its arrival, National Quarries put the CH660 to work as its key secondary crusher in its traditional three-stage crushing process – which allows the company to produce the large amount of accurately sized aggregates demanded by the local construction and ready-mixed concrete industries. The CH660 is sandwiched between a primary 1066mm x 1219mm jaw crusher, and two impact crushers operating in a tertiary capacity.
“We were quite happy with the performance of our old plant but I had the feeling we didn´t get the most out of it. The plant was producing well, but it was clear that the secondary cone was a bit of a bottleneck, but I couldn’t dream of the big improvements achieved by only changing one machine,” says Thair Aziz Muslem, general manager of National Quarries, who has been with the company since its foundation in Siji, Fujairah in 2002.
National Quarries is today considered to be one of the leading aggregate suppliers in the UAE with approximately 150 employees, and an annual production of 3.5-4 million tonnes of high-quality aggregate which is produced in a variety of sizes. The products produced are supplied to construction and ready-mixed concrete companies in the UAE and the surrounding area.
It was back in 2012 when National Quarries first started looking seriously into what could be done to improve its existing plant.
The research undertaken by Muslem and senior colleagues at National Quarries was said to have been taken to another level when Sandvik Construction in the Middle East was invited to take a look at the existing operation.
“It was clear from the beginning that the Sandvik team had a very good technical knowledge and took the task very seriously. The way they approached the problem gave me confidence that they would recommend the most beneficial solution for National Quarries”, says Muslem.
“Since I am an engineer myself I like to understand the technical details, so it was easy to work with Ashwin Prajapati and the other team members from Sandvik.
Ashwin and his colleagues looked at every aspect of the plant and tried to find out what could be done to upgrade the plant and get the most out of the invested money.”
In order to be able to propose the best solution possible for National Quarries, Sandvik was able to use a simulation tool that has been producing results for aggregates suppliers across the world. “We used our PlantDesigner tool together with the production figures we had from the existing machines to try to find the optimal solution in order to increase the capacity.” says Sandvik Middle East’s Ashwin Prajapati.
“We checked different scenarios, changing different machines and our findings were quite interesting. The secondary cone crusher was a bottleneck, as Mr Muslem believed, in terms of capacity, but also the reduction ratio was quite poor, which led to a coarse feed to the tertiary impactors and an unnecessary amount going in closed circuit over the impactors.”
Using the PlantDesigner simulation tool enabled Sandvik to propose a simple and cost-effective solution. “We could see that changing the secondary crusher to a Sandvik CH660 would not only increase the throughput in the secondary stage, but also the net production in the impactors due to the decreased percentage going in closed circuit,” says Ashwin.
In 2013 National Quarries replaced its existing cone crusher with the CH660, with PlantDesigner being spot on as to the dramatically improved production.
“The results have been amazing and our investment paid off much quicker than we thought possible. The total capacity of the plant has increased by 25%, which is great. Another positive result is the fact that the reduction ratio produced by the Sandvik machine is so much higher, leading to a lot of other benefits,” says Muslem.
“The output from the old cone crusher was around 0-75mm, while with the CH660 we are able to reduce the output to 0-63mm.
This has led to a reduction of the close circuit on the tertiary impactors, resulting in increased lifetime of the wear parts in the impactors by 65%. We are also using 20% less fuel in our generators due to less power consumption. On top of that the 0-5 mm production, which is a less valuable product, has decreased about 5%. In this competitive market it has meant a lot for us to be able to reduce our operational costs,” Muslem concludes.
At the beginning of 2015 it was time for National Quarries to invest in a new crushing plant, and due to the success of the CH660, Sandvik was the favoured company to supply the new plant. During the evaluation process, Sandvik and National Quarries teams worked closely together to find the right solution.
In May 2015 National Quarries placed an order with Sandvik Middle East for one CJ615 jaw crusher, two CI532 impact crushers, one primary feeder and three product screens for its new crushing plant.
Better by design
Sandvik Construction’s PlantDesigner has become a key tool for the Swedish firm’s crushing and screening customers in the quarrying and aggregates industry. Used throughout the industry, as well as by consultants and universities, over 600 licensees worldwide now use Plant Designer to calculate quantitative and qualitative material flow, enhancing the productivity of their crushing and screening operations.
Developed 20 years ago at Sandvik Construction’s crushing and screening factory in Svedala, Sweden, PlantDesigner was initially created as an internal tool for crushing and screening experts, but, due to customer demand, the novel features of the software were soon made available to all quarrying and aggregates professionals.
PlantDesigner uses a simulation engine drawing on years of experience gained by quarrying and aggregates industry’s leading process experts, including their longstanding relationships with customers.
This means that users receive detailed, accurate equipment performance analysis, together with cost estimates, that enable the accurate planning of operations. This helps to ensure optimal productivity, offering a view of any investment prior to actual equipment purchase and installation.
The accuracy and other features of PlantDesigner have been continuously improved as both software and equipment have developed over the last two decades, enabling crushing and screening plant simulations to become even more accurate.
With shrewd quarry and aggregates sector customers globally constantly looking at options to boost operation efficiencies and productivity, PlantDesigner in some form is likely to be used for another 20 years. When combined with other developments such as Optiagg, Sandvik Construction is well stocked with smart software-led solutions.
CJ615 Jaw crusher
Sandvik Construction’s CJ615 jaw crusher is said to be ideal for tough quarrying and mining applications due to its heavy-duty design.
Offering large feed acceptance capability, high capacity, high reduction and low jaw plate, the robust jaw crusher is designed and built on well proven technology to offer claimed highest possible reliability in relation to price and performance.
The 53tonne primary crusher model has manual and semi-hydraulic options available on the setting regulation to suit the different needs by the user.
Along with its 200kW engine, the 4.11m x 3m CJ615 boasts a feed opening of 1500 x 1070mm.