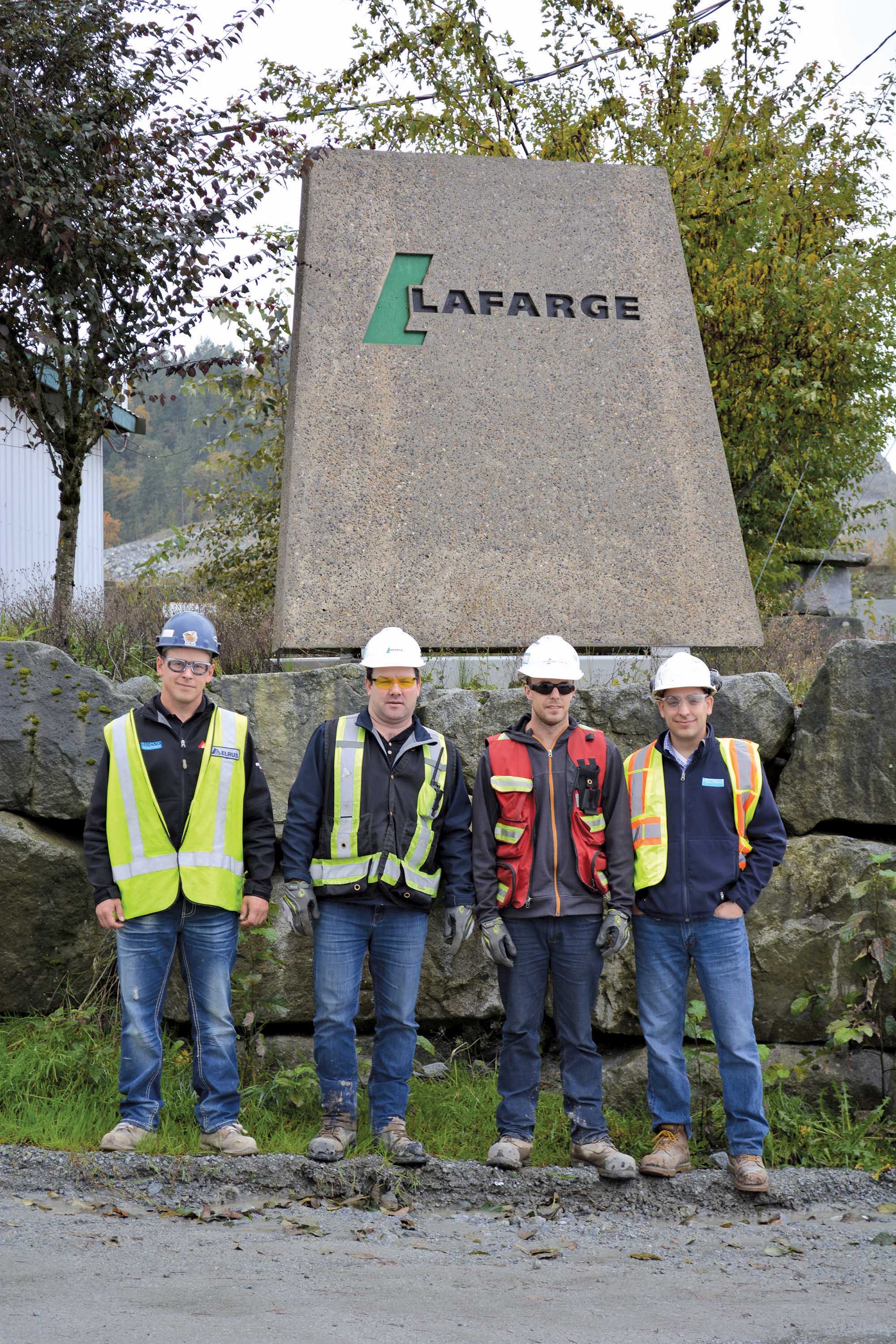
The facility in Pitt Meadows, 50km west of Vancouver, a big market for the granite quarry, is near the banks of the Pitt River. It ships out 1.5-2 million tonnes of aggregate/year, loading river barges or trucks with the prized product.
Reserves at the quarry are expected to last for the next 50 years. While operations at the granite quarry were running smoothly, producing 900tonnes/hour of high-quality aggregate used in Superpave, asphalt, and concrete applications, a main frame cracked on its existing cone crusher.
Manager Robert Brakes sought solutions to replace the quaternary unit, and among the solutions was one provided by ELRUS Aggregate Systems, authorised
ELRUS representative, Mike Wikdahl, believed a common platform unit to the S6800, the Sandvik CH660 stationary cone crusher, would be a perfect addition to the crushing system, but after studying several flow sheets he proposed that the quarry rearrange its line-up of machines to take advantage of the CH660’s “finer product.”
He suggested the company’s tertiary crusher be relocated to replace the broken cone crusher, and the CH660 to replace it in third-stage crushing, predicting an increase in production of at least 10-15% from the added capabilities of the CH660.
“The CH660 produces aggregate of a good size for the next stage of crushing,” Brakes says.
“Now the quaternary crusher is not dealing with 100-115mm rock, but with 65mm rock. The result is no plug ups and a good flow.”
Quarry assistant manager, Shayne Daum explains Wikdahl’s analysis showed clearly that the existing quaternary crusher produced an operational bottleneck as 100-225mm crusher feed would overflow and be dumped to the ground, requiring additional handling.
“With the CH660, the unwanted by-product has gone from 1,000tonnes a day to zero,” he says.
Since the CH660 went on line as a tertiary crusher the quarry says it is experiencing a 30% increase in aggregate output, reaching 1,200tonnes, double that predicted by Wikdahl.
“Before, it was hard to hit 1,000tonnes. The cost per tonne was the deciding factor. We typically were running a shift and a half to get the same tonnage as we now are doing with regular shifts. That’s huge when you add it all up: wear on belts, fuel, man hours, and other costs,” says Brakes.
Because of increased production rates, the quarry can afford regular planned maintenance interruptions, which also avoid costlier overtime repair work, and the company says the CH660’s design adds to the maintenance good news, with CLP manganese liners “easier and faster to change.”
The CH660 is also said to benefit from more efficient power transfer to the crushing chamber, deriving from Sandvik’s Hydroset technology coupled with the ASRi automation system that maintains optimum reduction despite wear.
“These features ensure a customer can maximise reduction and reduce the amount of recirculating material, freeing up space to process more material,” says Stephen Dobler, Sandvik Construction’s business line manager for crushing and screening in Canada.