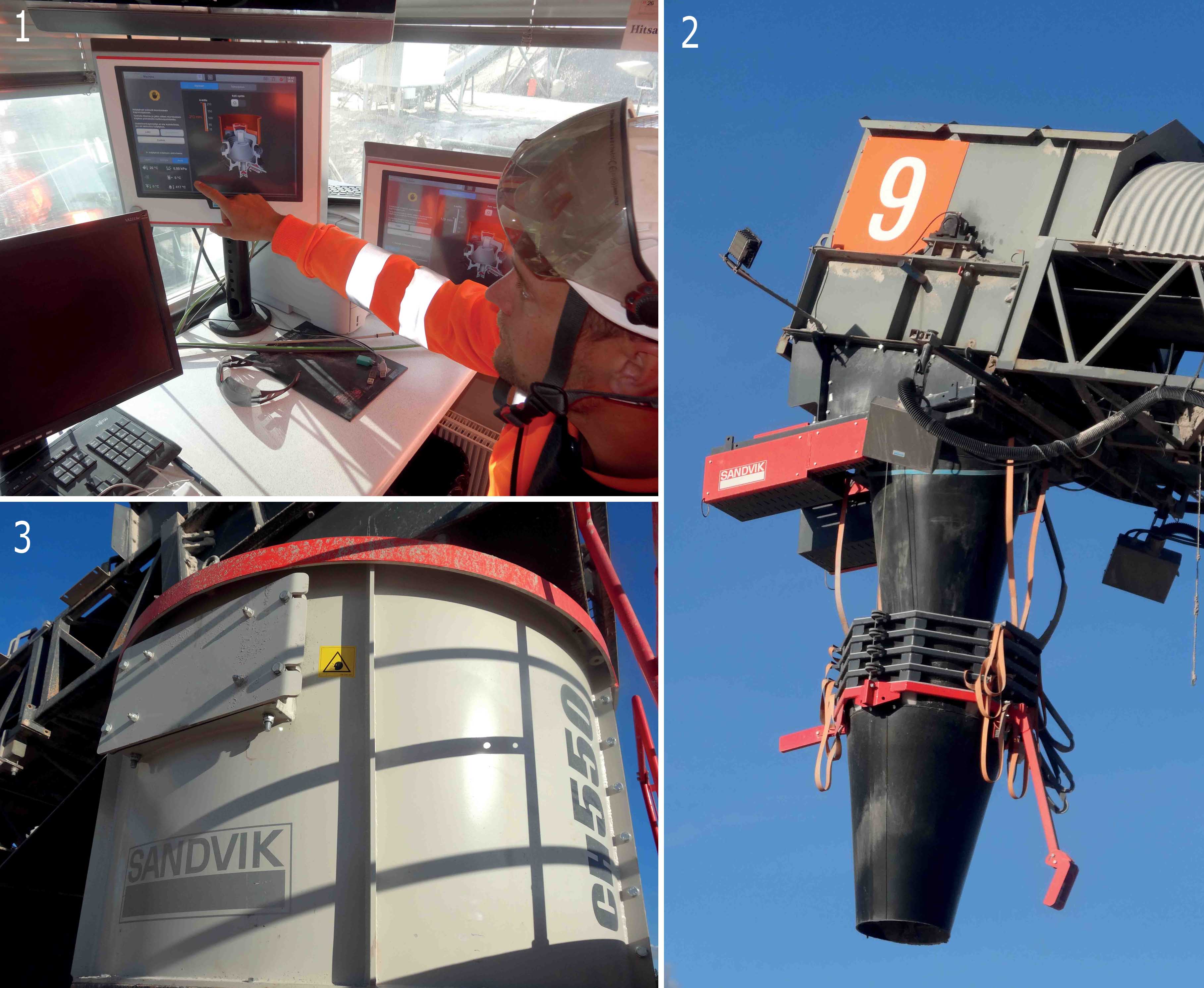
Seepsula’s Senkkeri quarry near Helsinki is the largest quarry in Finland and one of the largest in Europe, producing 2.2 million-2.5 million tonnes of granite rock aggregate a year. The site is successfully running two production lines after a major investment in early 2016 in new Sandvik Mining & Rock Technology crushing and screening models. Guy Woodford reports.
Seepsula remains very much a family affair. Founded by the Sjoblom brothers- Kaarlo, Illari, Juhani, Seppo and Alpi - in the 1970s, the multi-quarry business is now owned by Seppo, Juhani and Juhani’s son, Karl. The company’s name comes from the brother’s jocular use of a young neighbour’s mispronunciation of their surname
The trio are keen to invest in the latest crushing and screening models to ensure the company continues to grow through more efficient and productive aggregate material processing. This has led to two 400tonnes/hour capacity CH550 cone crushers, an SS1633H and an SK1862 screen, and four HC series conveyors, all manufactured by
The new equipment models have been added to what was already an all-Sandvik crushing and screening plant line-up, which includes a CJ615 jaw crusher, a CS660 cone crusher, a CH440 hydrocone crusher, another SS1633H screen, and three CS126 screens. Senkkeri quarry also uses a
“We needed more production capacity with less units. We had four cone crushers and now we can do more with just three,” says Timo Pyykkinen, Senkkeri quarry site manager. “The CH550s produce better-shaped end products and are easier when it comes to spare part installation. They process between 200-230 tonnes an hour working with the rock in this quarry. The new Sandvik screens are high quality and similar to our previous screens.
“Sandvik’s servicing engineers and spare parts facility is also very close to us – only around 40 kilometres away. That’s a big advantage. The company is also well known for the reliability of its equipment.”
Seepsula Senkkeri quarry’s customers are a mixture of earthmoving companies and contractors, roadbuilders, and asphalt and concrete plant operators, all within a 50km radius of the quarry. Senkkeri’s main granite rock and sand product sizes are 0-3mm, 3-6mm, 6-16mm, 0-16mm, 0-32mm, 16-32mm, 0-55mm and 0-90mm, but there are more than 20 products that are produced onsite.
Blasting for material is carried out two to three times a week by a sub-contractor, with a call being made to the Control Tower at nearby Helsinki-Vantaa Airport prior to every blast. This is part of the quarry’s and the wider Seepsula company’s pro-active approach to health and safety, an approach that includes all company staff attending four safety training courses a year. Material is also initially won at Senkkeri quarry by another sub-contractor using a Sandvik DX870 surface drill rig.
After blasting or drilling, the secured granite rock is reduced in size by a Rammer BR 3088 breaker attached to a further sub-contractor’s excavator. The material is loaded by the sub-contractor’s
All final sized products are loaded on trucks by six
Pekka Jauhiainen, a Sandvik sales manager, worked closely with Seepsula on the firm’s February 2016 purchase of its new Sandvik equipment for Senkkeri quarry. He has also been a regular visitor to the site to check on its performance. “I’ve enjoyed very good co-operation with Seepsula. There was a lot of discussion prior to the purchase on how we could help meet their production targets. And still every day we are talking to them about product sales, servicing and spare parts needs.”
Senkkeri quarry has built a number of grey buildings onsite which help reduce production noise levels. The laying of 300,000m² of asphalt on access and haul roads earlier this year by another company working within the quarry’s boundaries has also helped significantly with noise reduction, as well as helping to reduce quarry dust levels. Aided by its Sandvik-supplied high-pressure heated water system, Pyykkinen says Senkkeri quarry also uses a giant water tank and up to 100m coverage cannons to reduce haul road dust. Meanwhile, a Sandvik WE6000i telescopic chute attached to the end of the Sandvik HC series conveyor used on the main production line is lowering the drop height of the final product material onto the stockpile, further supressing dust, and reducing material spread.
Working across two shifts – 6am-1.30pm and 2pm-10pm – five-days-a-week, Pyykkinen and his colleagues at Senkkeri quarry also use Sandvik’s SanRemo remote crusher productivity monitoring service available via a web portal. Based on production, performance and maintenance status reports supplied by the system, quarry operators can quickly detect any changes in efficiency and machine utilisation, allowing them to accurately measure and forecast projects and make precise maintenance schedules, without leaving the office.
“We use it daily on the two CH550 crushers on our main production line. It’s very easy to use,” says Pyykkinen. “It gives us more opportunity to check performance against targets. We’re planning to connect all our cone crushers to it from this winter.”
With more than 100 years of granite rock reserves to process and having invested in ultra-efficient and productive crushing and screening plant, Senkkeri quarry is well set for long-term success. “Business is currently stable and we are looking to increase our aggregate sales. Perhaps we may one day run an even bigger plant,” concludes Pyykkinen.