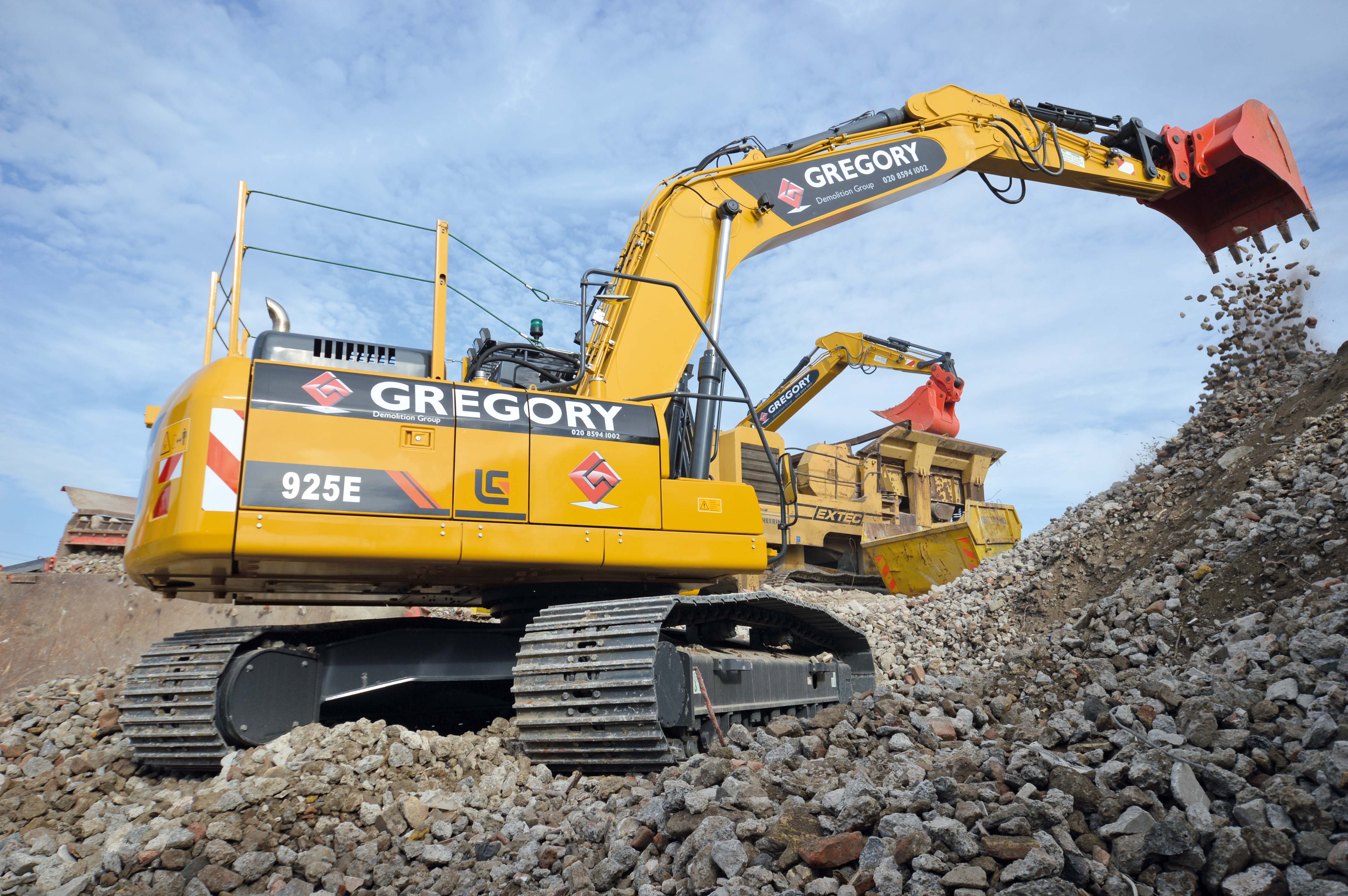
The importance of how quarry trucks are loaded, and the impact on productivity and fuel consumption, has been emphasised many times. Get it right and the figures can make pleasing reading, but get it wrong and it costs money and can make machines carry out unnecessary manoeuvres, thus increasing maintenance requirements.
This was emphasised by
Eight tough challenges tested safety, accuracy and versatility skills on a wide range of Cat construction equipment including a loading element involving the Caterpillar 950K wheeled loader.
In the load and carry exercise, the 950K was driven from a parking area to a gravel heap where the bucket was filled before travelling along a course to load a Cat Certified Used articulated dump truck. The loader bucket travelled at no more than 1m from the floor and could not be raised until it reached a marked area. Four loads were placed in the truck before the machine was driven back to its starting position.
In the carry element, a Cat 725C ADT was driven along a marked course, reversing behind the loading wheeled loader to an exact marked position. The operator then drove forward through a rough terrain course at the end of which, he reversed into a simulated dump area before being allowed to drive forward and complete the course.
“What we were looking for was how the operator handled the tasks, including the loading section involving the 950K loader,” says Caterpillar.
“While all the finalists are highly skilled operators, they do not always drive on a regular basis the vehicles involved in our challenge.”
Sebastian Behr from Cologne, Germany, who normally operates a Cat 329 hydraulic excavator, won after completing the series of timed challenges. He also won the 2008 title when the competition was last held. Runner-up was Michel Abderhalden from Switzerland and Cristian Tanera from Italy claimed third place.
Caterpillar says that development of the new optimized Z-bar linkage on the 950K was done in conjunction with the Performance Series buckets, Fusion coupler and the Fusion family of work tools to ensure that all components function together to enhance visibility, performance and fuel efficiency.
“Load sensing hydraulics produce flow and pressure for the implement system upon demand and only in amounts necessary to perform the needed work functions, enhancing machine productivity and fuel efficiency,” says Caterpillar.
The 950K is powered by a Cat C7.1 ACERT engine that meets all Tier 4 Interim/Stage IIIB emissions requirements.
Meanwhile, also in the UK, having exclusively used Caterpillar equipment since 1971, County Yorkshire-based aggregate specialist, Rotherham Sand & Gravel has bought the new Cat 938K wheeled loader from Caterpillar distributors
Supplying aggregates, sand, gravel, concrete and decorative stone throughout Counties Yorkshire, Nottinghamshire, Derbyshire, Lincolnshire and Leicestershire, the company has a rapidly expanding operation.
“Upturn in the construction sector has led to a dramatic increase in demand for our products. It is therefore vital we have the fleet of machines to match this rise in operational activity. As we already have the Cat 938G and two 938H wheeled loaders on site, investing in the newest 938K model was the next logical purchase. Our drivers are already looking forward to the next M series release in March 2015,” says Paul Scholey, managing director at RS&G.
Meanwhile, German manufacturer
In April, 2014, the Japanese group started fitting Deutz TCD 3.6 engines to its ZW100 and ZW120 series of wheeled loaders. The cooperation with HCM will allow Deutz to successfully expand its international presence, particularly in the Japanese market.
Starting in April 2014, the ZW100 and ZW120 wheeled loader series are fitted with the TCD 3.6 engine manufactured by Deutz.
The water-cooled four-cylinder in-line engine generates an output of 55.4kW-90kW at a rated engine speed of 2,300rpm.
The TCD 3.6 engine series has a modular exhaust after-treatment system (DOC) which can be mounted on the engine as an optional extra, and it is fitted with a charge air cooler and meets the EU Stage III B and US EPA Tier 4 Interim emissions standards using an oxidising catalytic converter.
“We are delighted that Hitachi Construction Machinery is relying on Deutz to deliver the engines for its wheeled loaders,” says Michael Wellenzohn, the board of management member responsible for sales at Deutz.
“The partnership underlines the versatility and robustness of our engines, which are used in the most diverse application segments.”
Chinese company
Gregory Demolition, which is based in County Essex, southern England, recently made a significant investment in LiuGong machinery with equipment supplied by Construction Plant & Machinery Sales, the UK dealers for LiuGong equipment.
The order for 11 LiuGong machines consists of four 922E hydraulic excavators (operating weight of 22,000kg and powered by Stage 3B emissions-compliant
A number of the new LiuGong machines were immediately put to work in the company’s recycling yard in Barking, Essex, adjacent to the River Thames, where the company, in partnership with Thames Recycling, is producing between 1,000-1,500tonnes of recycled aggregates/week. The company is heading towards a target of producing up to 5,000tonnes of aggregates/week for its new concrete and aggregates partners in 2015.
It estimates that the London construction market is in need of a strategy to supply somewhere in the region of 3–5 million tonnes of recycled material/year and armed with new LiuGong machines, Gregory Demolition aims to be at the forefront of that supply chain.
“From what we have seen so far and the excellent support we receive from our local dealer CPMS, it is not a question of if, but when we will order more LiuGong machines,” says Dean Gregory, Gregory Demolitions’ managing director.
Following its launch at the recent
The 32tonne loader replaces a five-year old L220F and joins a G series L220 and a Volvo L150G which was bought two years ago for the company’s soil blending operation.
The L220H features a 13litre stage IV final engine, and has Volvo designed and manufactured driveline components, including
In order to produce around 2,000tonnes of material/day at Bathgate, the L220H has been fitted with a 6.1m³ straight lipped bucket and Volvo’s optional ride control or boom suspension system together with
“So configured, the new arrival is capable of extracting from the face and carrying bucket loads of up to 11tonnes on one way hauls of up to 400m to field hoppers, strategically placed in the quarry feeding a conveyor system,” says Volvo, which has also provided a substantial package of equipment to the
The package includes three Volvo EC220D (22tonne) excavators; two of the latest E series EC250E excavators with operating weights of 25tonnes and a Volvo L150H loading shovel complete with a 4.2m³ general purpose bucket.
The EC220D excavators will be deployed in an aggregate quarry, a sand and gravel pit and a recycling facility belonging to Raymond Brown, while the all-new Volvo EC250E excavators and L150H will be engaged on long-term contracts which the group specialise in: the processing of incinerator bottom ash (IBA).
The EC220D is said to benefit from the use of Volvo’s Stage IIIB D6 engine, delivering 129kW of power and 849Nm of torque, coupled to an improved hydraulic system with larger pumps which in turn significantly improves hourly fuel consumption with shorter cycle times. The larger EC250E excavators are equipped with Stage IV final Volvo 8litre engines.
The new Volvo L150H wheeled loader features a Volvo Stage IV 13litre engine which is subsequently enhanced by the “perfectly-matched” Volvo powertrain and intelligent hydraulics, which supply power only on demand.