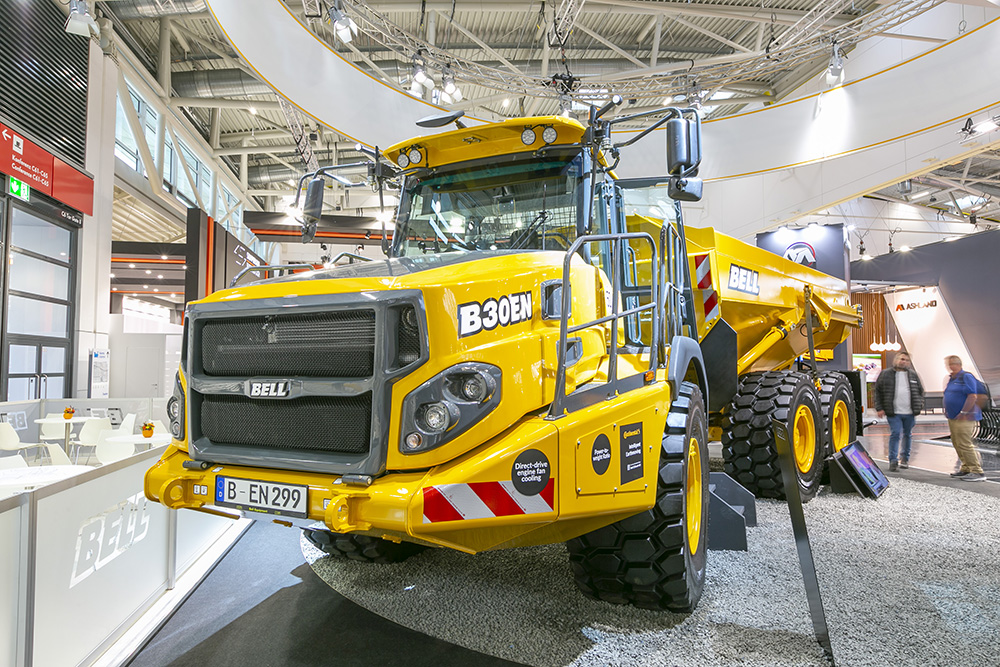
At bauma Munich 2022 (24-30 October), Bell Equipment showcased its new generation, two-axle B45E 4x4 ADT and a Bell B30E with a vehicle width of less than three metres. The South African-headquartered articulated hauler giant also highlighted its eye-catching and extensive autonomous articulated hauler testing programme.
As reported by Aggregates Business earlier this year, as an addition to its range of seven ‘traditional’ 6x6 ADTs, with payloads from 18 to 45.4 tonnes, Bell Equipment is the only global ADT manufacturer to offer a parallel three-model (B60E 4x4, B45E 4x4 and B30 4x4) range of two-axle ADTs for the past six years. Each ADT is aimed at a different market segment and represents a strong operating offer thanks to the advantages of the 4x4 ADT concept. In the right applications, Bell Equipment says the models outperform conventional rigid dump trucks (RDTs) that need good haul roads and the three-axle ADTs are designed for extreme off-road mobility.
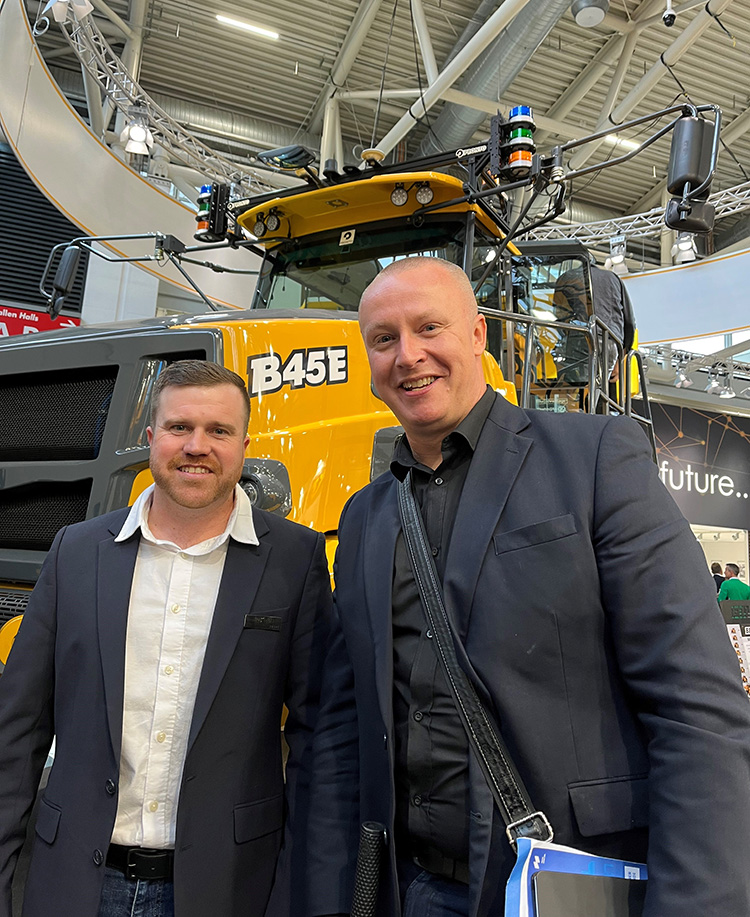
Speaking to Aggregates Business at the exhibition, Brad Castle, territory manager at Bell Equipment, said: “You don’t always need a 6x6 ADT in a quarrying environment. In a B30E, for example, the 4x4 version has a 13% smaller turning circle than its 6x6 equivalent. That makes a big difference when you need to turn around on-site. The 4x4 haulers also reduce tyre wear and road maintenance costs, as you don’t have middle tyres like a 6x6 dump truck, which causes scuffing.”
Castle says the fact that Bell Equipment and Doosan Infracore are the only two ADT manufacturers offering 4x4 articulated haulers has facilitated adoption by quarrying customers. “It is a niche product line but one that is very much needed. The 4x4 models have been developed through our Specials [applications] department in [Richards Bay, KwaZulu-Natal], South Africa. The truck’s power head is the same as the 6x6 equivalent, with the rear end being the difference. Our 4x4s have become known in the US as a ‘quarry’ truck. It doesn’t replace our 6x6 ADTs; it competes against [40-tonne-class] rigid dump trucks.
“The fact that our 4x4s have drive on both axles, compared to RDTs with drive on one axle, gives it a capability edge. The B45E 4x4 now comes with full suspension as standard, rather than the previous rigid rear with no suspension on the back. This offers more operator cabin comfort. We also offer a narrow or standard bin option, with the narrow bin preferred when operating under a crusher feed hopper.”
Castle stresses that fuel consumption and tyre wear are the two biggest costs linked to running an ADT fleet, with Bell Equipment “known” to offer the lowest articulated hauler fuel burn globally. Now, with its 4x4 ADT range, Castle says Bell Equipment also has a great offer on reducing fleet tyre wear compared to 40-tonne class RDTs.
“We had a quarry customer in South Africa running B60E 4x4s. They calculated their tyre wear costs against their rigid trucks, and they narrowed it down to how much in rands and cents the B60E 4x4s’ tyres were saving them – and it was 2 rand 28 per tyre per hour. You add that up over many working hours across a fleet, and it’s a huge saving.”
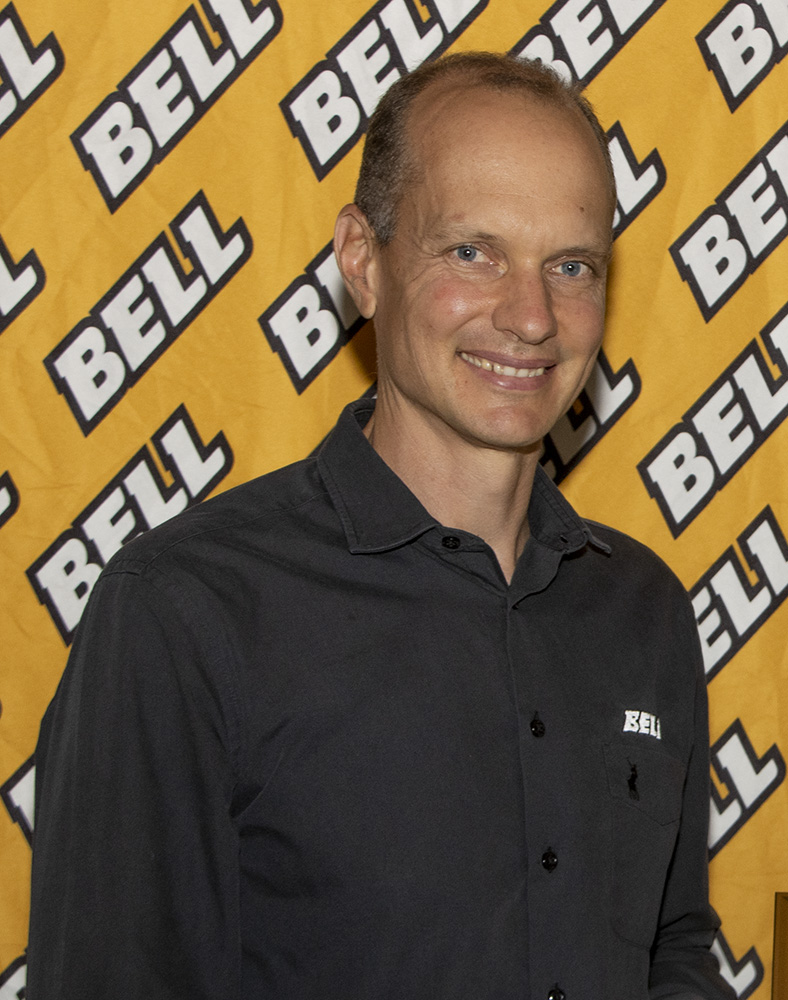
In 2019, Bell Equipment completed a €17mn facility at its Eisenach-Kindel assembly plant in Germany. The new production complex makes ADT components for the Northern Hemisphere. With around 12,000m² of floor space, the facility tripled the available space at the Eisenach-Kindel site. The new site directly adjoins the main factory hall. It provides in-house manufacturing of truck components in Europe for all seven Bell ADT models (B20E to B50E) assembled in Germany. Emphasising the commercial advantage this gives Bell Equipment, Castle says: “Like any heavy equipment, our ADTs are only as good as their support. You must keep the machines running, or customers lose money, so having a factory in Germany closer to our [Northern Hemisphere] customers is hugely important. We expanded the factory significantly two to three years ago, and it’s now three times larger.” Bell Equipment announced earlier this year that it would increase its ADT manufacturing at Eisenach-Kindel due to the strength of the company’s North America and Western Europe sales. Kiesel, Bell Equipment’s German dealer, reports that its strongest ADT demand comes from quarrying businesses, particularly keen on the 4x4 haulers.
Since 2020, Bell Equipment has been working closely with xtonomy and Voestalpine at a lime quarry site in the Alps, where xtonomy has fitted its iTruck autonomous haulage system (AHS) on two Bell B30E ADTs with great results.
A link-up with Pronto AI, an American safety and automation technology developer, followed, including the official launch of Pronto AI’s autonomous haulage solution at MINEXPO 2021 in Las Vegas last September. A full test site has since been established in Reno, California, where three autonomously operated Bell B45Es and a Bell B50E are working in a sand mine. A second US test site, at a Texas sand mine, has also been created in recent months.
“We now offer an autonomous-ready articulated hauler, with our partners’ technology talking to the machine,” says Castle. “We have customers talking to both xtonomy and Pronto AI about real-world applications.
“I visited Pronto AI’s Californian quarry test site last month [September], and it was quite something to see the ADTs driving around the site with nobody inside. We are actively talking to customers in America about this technology. It is very software intensive and hardware minimal, with the autonomous haul truck app controlled. We have videos playing here [at bauma 2022] of our test sites, and you see the driverless ADT stop when someone gets near it. Where site connectivity allows, the autonomous hauling solution in quarries will really take off over the next year.”
Joining Castle in conversation with Aggregates Business, Tristan du Pisanie, Bell Equipment’s head of product development, highlights the articulated hauler major’s development on making its machines compatible with alternative fuels.
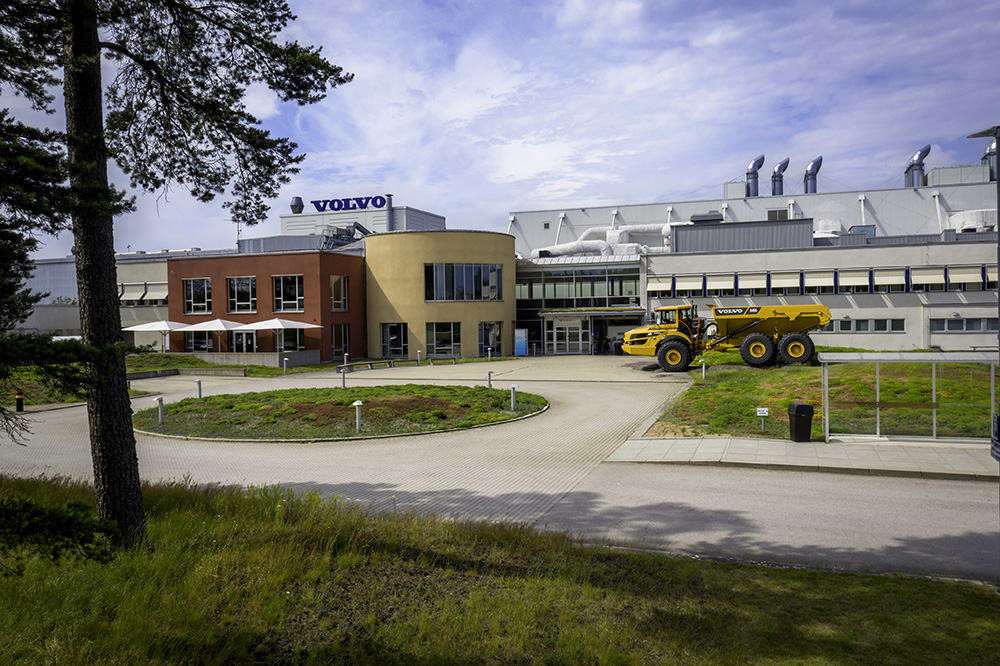
“All our ADTs are fully compatible with HVO (hydrotreated vegetable oil). We believe HVO is a very good low-carbon solution, provided it’s using the right input material. The biggest controversy I have heard recently is people who get palm oil from countries where it is unsustainably grown. That can give HVO a bad name. If you use the right raw material, it is a great solution for our customers that are carbon-reduction minded.
“Longer term, the size of our machine range is probably not compatible with where batteries are today; they are too big, and the energy cost is too high, making them too expensive. So, we are looking at alternatives, and the only two things that look feasible are hydrogen fuel cells and hydrogen internal combustion engines. Both will need a lot of investment around production and supporting infrastructure. The challenge with hydrogen is how to store it on the articulated hauler, as it takes up a lot of space, considerably more than conventional fuel, like diesel. You need around twice the size of a diesel fuel tank to run on hydrogen for four hours at a time. It must be said, though, that we don’t know for sure the direction our low-carbon journey will end up taking us, and I believe that this is true for all OEMs. Technology is changing every day, and we don’t know which solution will advance faster than the rest.”
Volvo Construction Equipment (Volvo CE) has announced its intention to invest SEK 360mn (€33.05mn) into its production facility in Braås, Sweden, between now and 2027.
The facility in Braås, long recognised for its environmental credentials, specializes in the design and manufacture of articulated haulers for the global market. It produced a fossil-free construction machine that was the first in the world to be delivered to a customer - an A30G which is now in use on customer NCC's worksite.
The decision of AB Volvo's board of directors to invest in Braås means that the factory will be adapted over the coming years to enable it to produce a larger range of articulated haulers with different powertrain types, reflecting the shift in demand towards equipment with more sustainable power sources.
The investment will be used to extend production capacity at the 45,000 m² site in southern Sweden to broaden the product range going forwards, with the addition of new buildings and production equipment. Setting its sights firmly on the future and in line with its purpose to build the world we want to live in – and workplaces we want to work in - Volvo CE will also invest in automation and ergonomics to both reduce the need for employees to engage in repetitive tasks and create a safer work environment.
Pioneering manufacturing techniques is nothing new for Braås. Since producing one of the world's first series manufactured articulated haulers, the ‘Gravel Charlie’, a 10-tonne hauler, in 1966, the facility has been at the forefront of innovation. The site is most famous for producing the largest articulated hauler in the world, the 60-tonne class A60H, a real feat of engineering.
As well as constructing the world's first articulated hauler made from fossil-free steel, the engineering talent based here has also been instrumental in the building of the world's first prototype articulated hauler powered by hydrogen fuel cells – the concept Volvo HX04 – which is currently the focus of testing to develop future hydrogen solutions.
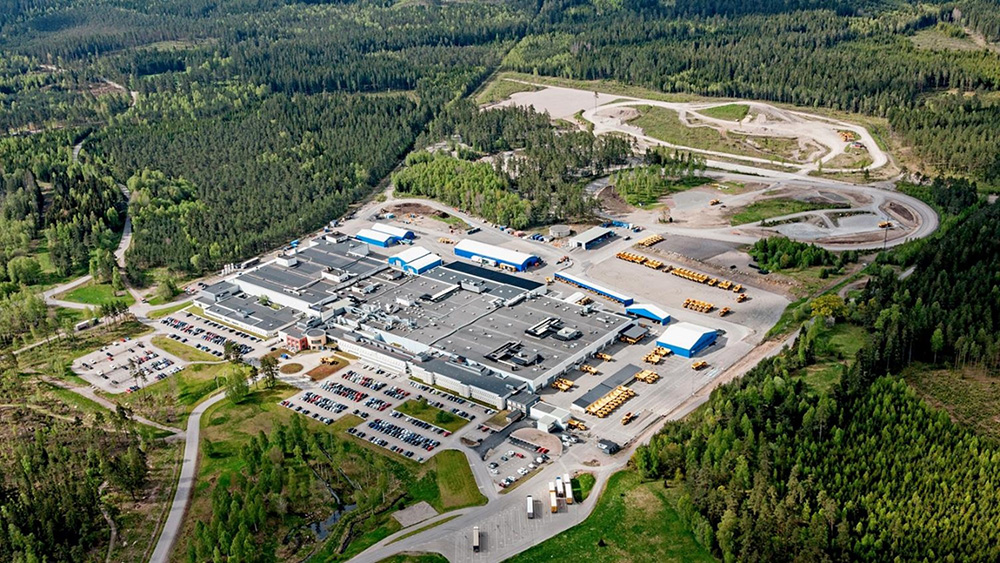
Braås is also leading the way in environmental protection and was the first in the construction industry to achieve a carbon-neutral operation powered entirely by renewable energy. In 2018, the site also became a zero-landfill facility.
"The transport and construction industry is undergoing a transformation with, among other things, an increasing number of electrified vehicles," says Jonas Lakhall, site manager at Volvo CE in Braås. "This investment will enable us to adapt and extend our production facility so that we can offer a broader range of machines – with different powertrains – to our customers and help them meet their emission reduction ambitions.
"It is important for us to continue to be at the forefront and make clear decisions to meet our Science Based Target commitment to achieve net-zero value-chain emissions by 2040. By adapting our production for electric machines, we are progressing along our electrification roadmap.”
Hyundai is now offering two ADTs, the HA30 and HA45, with capacities of 28 tonnes and 41tonnes respectively. The machines may be new to the Hyundai brand but feature proven designs and technology.
The machines are the well-accepted Doosan models built in Norway and now being offered in Hyundai branding following the tie up between the firms.
The firm claims equal weight distribution due to the sloping rear chassis frame design, which is said to deliver stability by distributing more load towards the centre of the machine and resulting in a low centre of gravity. The machines also have the proven tandem rear-axle bogie configuration, which is said to offer a higher degree of articulation than competing designs and optimises ground contact to maximise traction. The machines also feature the articulation joint-turning ring mounted close to the front axle, which further helps to equalise load distribution between the front to rear and across the front axle during steering.
The trucks are powered by Stage V-compliant Scania diesels. The HA30A uses a five-cylinder, 9.3-litre, DC9 turbocharged diesel, developing 276kW and 1,876Nm of torque. The larger HA45A employs a six-cylinder, 12.7-litre DC13 diesel engine, producing 368kW and 2,476Nm of torque.

Both engines drive through eight-speed ZF automatic transmissions, with integrated retarders. The torque converter has lock-up in all gears, reducing fuel consumption and increasing efficiency. Fuel, AdBlue diesel engine exhaust fluid and a standard auto-lube greasing system can all be easily accessed from ground level. The engine canopy tilts forward for access to filters and fill points, while the cab structure can be tilted to provide access for repair and maintenance.
Hyundai’s Himate telematic monitoring system is fitted standard, with satellite and GSM connectivity. This allows customers to monitor productivity, fuel consumption, system warning and maintenance status remotely, reducing downtime and improving fleet utilisation.
Italian company Perlini has launched the new DP265WD dump truck for the quarrying, mining and public works sectors.
Referred to by the manufacturer as “the little one” in its range, the 26.5-tonne truck features new control electronics, modern GPS monitoring and electronic weighing systems.
The width of less than 3m allows for road transport without the need for special transit permissions or escorts.
The vehicle’s features include a brake/retarder system with oil-bath brakes, oil-pneumatic suspension, and a Stage V Scania DC09 engine and an Allison 4430ORS transmission with update electronics.
Showcased at bauma 2022, the DP265WD also features a new digital electronic system which enables real-time monitoring of all system parameters, including remotely.
The on-board GPS available in the new dump truck connects to the vehicle’s power supply and constantly collects the status of its main parameters including position, speed, direction, panel status check on/off progressive mileage and on-hours of the panel. It then transmits them via GPRS to a web-monitoring platform.
Requiring a robust, reliable articulated hauler to remove overburden for ten hours a day, five days a week, Erdbau Schrader found the perfect solution with Rokbak and its RA30.
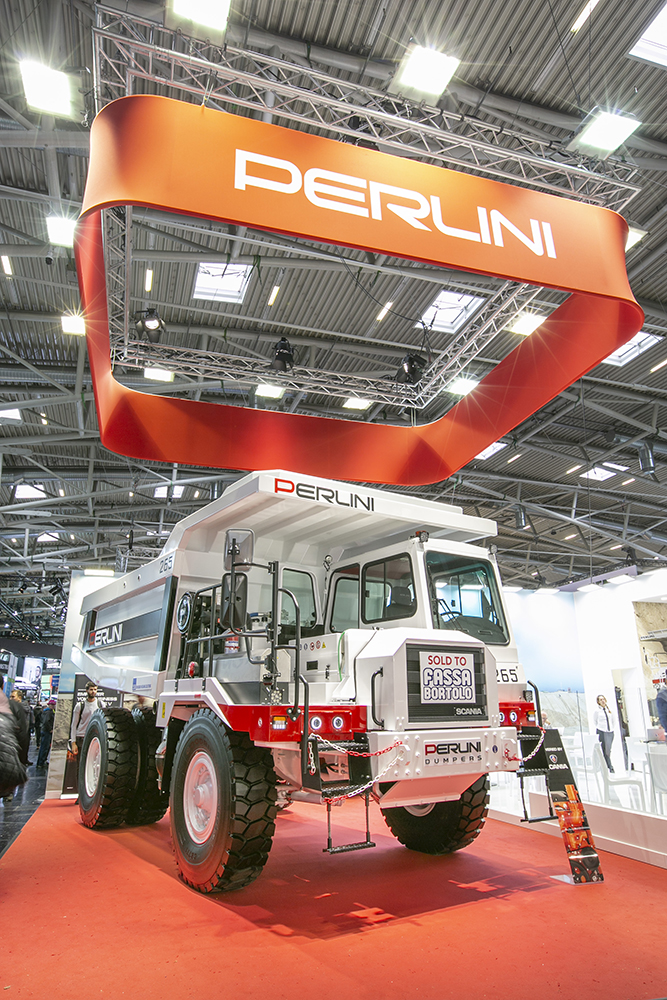
In a pit near to Calbe, a town in the district of Salzlandkreis, in Saxony-Anhalt, Germany, around 6,000 tons of gravel is removed daily by earthworks specialist Erdbau Schrader. Gravel extraction started at the site around 30 years ago and it’s expected to continue for another three decades. Now navigating this tough terrain, up and down steep inclines to unload around two kilometres away, is the Rokbak RA30, the latest addition to Erdbau Schrader’s fleet.
"We chose Rokbak because of its reliability and the price-performance ratio, as well as the hauler’s ability to cope with our long, heavy off-road operations,” says Ines Schrader, managing director of Erdbau Schrader. “We also wanted to ensure that our experienced operators would be able to work with maximum comfort.”
Erdbau Schrader was founded in April 2011. The company specialises in removing overburden for gravel extraction and renaturation, utilising its machines at several locations near its bases of Staßfurt and Brumby. Erdbau Schrader already owned four Terex Trucks TA300s – which it bought before Terex Trucks rebranded to Rokbak in September last year. In July, the company added the RA30 to its fleet, purchasing the machine from Rokbak dealer Klarmann-Lembach. Three other articulated haulers are working alongside the RA30 at the pit near to Calbe.
“The Rokbak RA30 is a strong, reliable and high-performing machine – which is exactly what Erdbau Schrader needed,” explains Klarmann-Lembach salesman Thomas Keil, who recently visited the Calbe site with Rokbak to see the RA30 in action. “Our confidence in the Rokbak brand and the haulers is such that, when we were approached, we could assure our customer that the RA30 was the ideal addition to their fleet.”
Erdbau Schrader’s articulated haulers move at full power five days a week, for ten-hours from 6am until 4pm. Materials from the site are transported over sandy and spongy ground for two kilometres before being unloaded at a railway loading station. The RA30 has to navigate tough terrain, prove its durability over long shifts and be a machine that employees want to operate.
With the capability of transporting a payload of up to 28 mt (30.9 t), the RA30 has a maximum engine power of 276 kW (370 hp) with a heaped capacity of 17.5m3 (22.9yd3) and a maximum torque of 1880 Nm @ 1400 rpm. All Rokbak haulers can be relied upon to operate effectively and efficiently, with optimal traction in difficult terrain, combatting steep inclines with ease. Routine maintenance is as quick and efficient as possible, keeping service time and costs to a minimum. Furthermore, the factory-approved parts are backed by a two-year/6,000-hour warranty – one of the most comprehensive guarantees in the industry. Operational comfort is also at the forefront of the RA30 design. A spacious, ROPS//FOPS-compliant, pressurised cab with excellent heating, ventilation and air conditioning (HVAC) keeps the operator comfortable and focused.
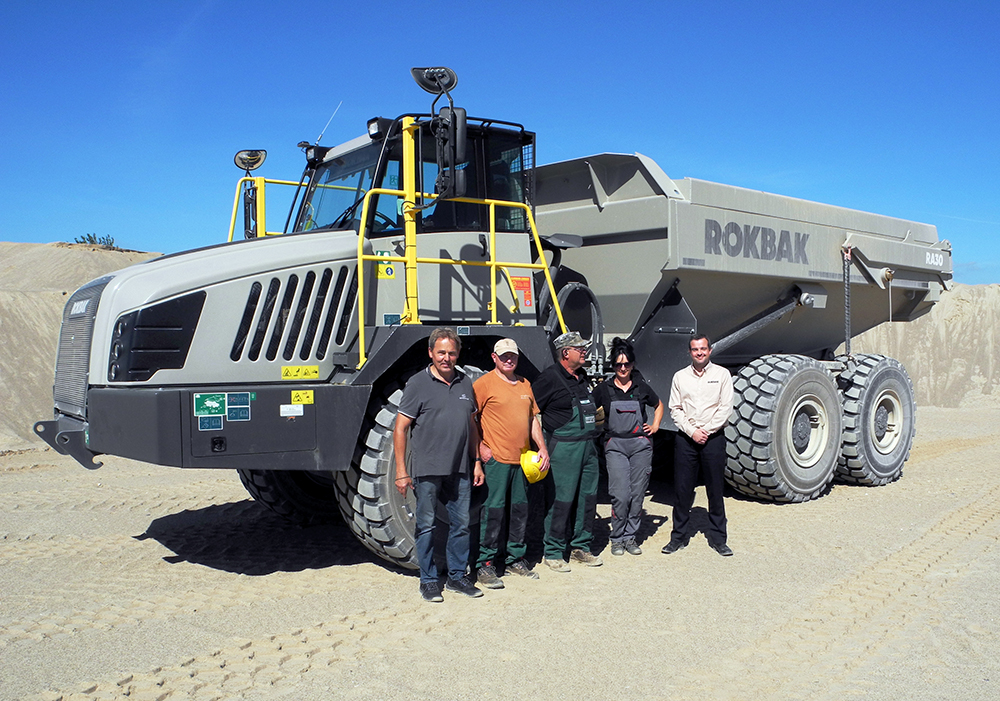
“Our operators have highlighted to us that they have found the RA30 to be extremely reliable and easily adapted to our heavy, difficult working conditions,” says Uwe Schrader, who oversees machine usage at Erdbau Schrader. “The notable construction of the front axle, with true independent front suspension, offers a very high level of operator comfort across a comprehensive ten-hour working day, which is further elevated by the fully automatic eight-speed transmission.”
The RA30’s EP320 transmission comes with eight forward gears as well as four reverse gears and features a top speed of up to 55 km/h (34 mph), high overall gear-ratiospread, equal ratio steps between gears and optimised gear shifting with partial load shifts. All of this means that the RA30 offers lower fuel consumption with smoother gear shifting and thereby higher levels of operator comfort as well as faster cycle times and reduced carbon emissions.
Overall, the entire drivetrain helps the hauler deliver class-leading rim pull for superior performance and productivity. It also ensures the machine offers excellent navigation and fast haul cycles. The RA30’s long-life transmission fluid increases the length of time between oil maintenance intervals to 4,000 hours. This helps customers achieve increased productivity and uptime, as well as lower cost per tonne.
“The RA30’s transmission strikes the perfect balance between efficient power, effective gearing and weight distribution, allowing the hauler to move more loads quicker,” concludes Thomas Schmitt, Rokbak’s customer support manager for Europe. “The RA30 is simple to operate and easy to maintain, it delivers low total cost of ownership with a fuel-efficient performance and high productivity – so it’s no wonder the Erdbau Schrader team are so happy with it.”