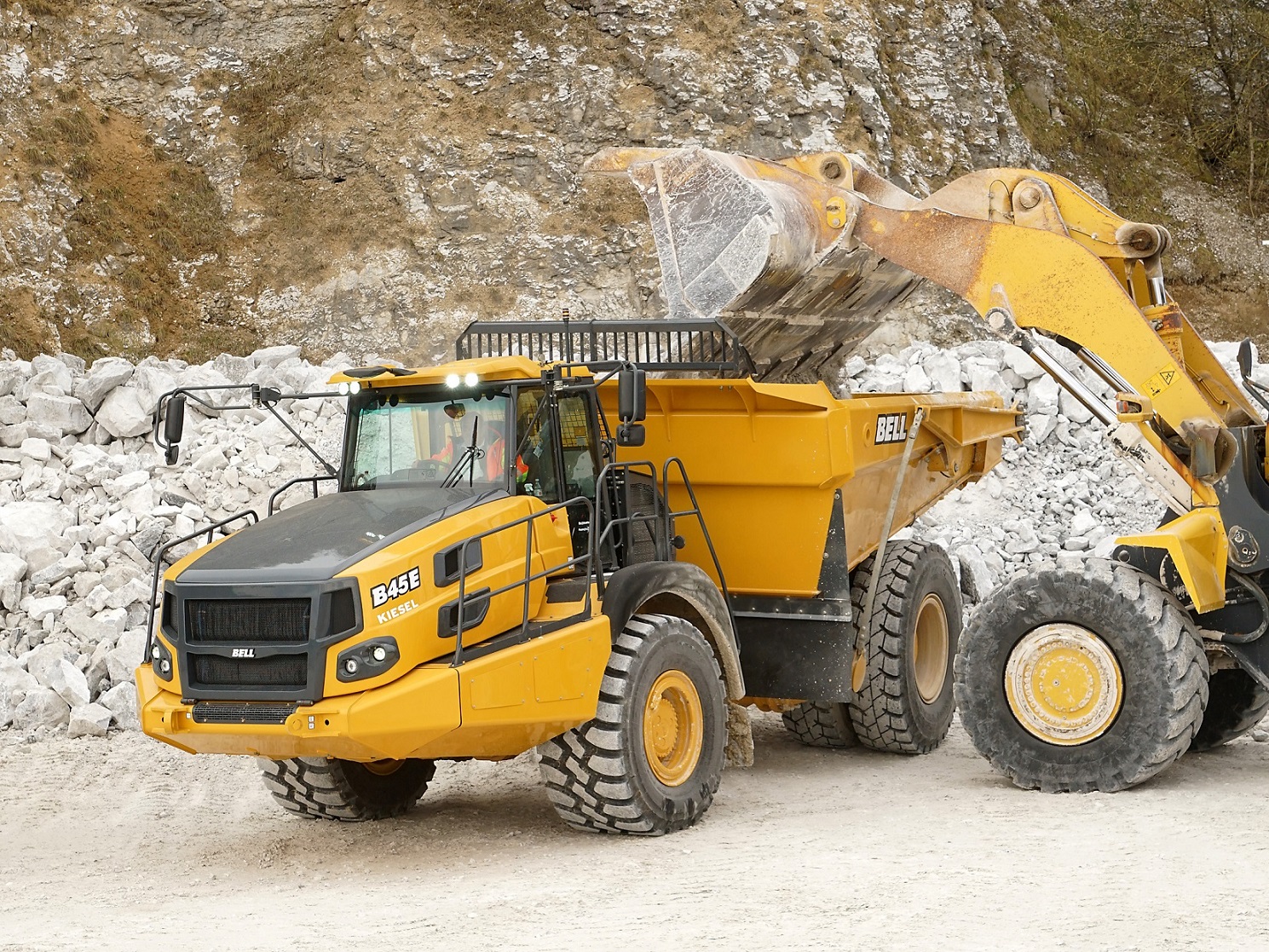
At bauma 2022 in Munich (24-30 October), this will be demonstrated by the South African hauling giant's new generation of the two-axle ADT Bell B45E 4x4 and a Bell B30E with a vehicle width of less than three metres. Both machines are said by Bell to offer a compelling advantage to customers with specific requirements.
As a supplement to its range of seven 'traditional' 6x6 ADTs, with payloads from 18 to 45.4 tonnes, Bell says it is the only manufacturer of articulated haulers globally to offer a parallel range of two-axle ADTs for the past six years. All three models are aimed at different market segments and are strong offerings thanks to the advantages of the 4x4 ADT concept. In the right applications, Bell says they outperform conventional rigid dump trucks that need good haul roads and the three-axle ADTs designed for extreme off-road mobility.
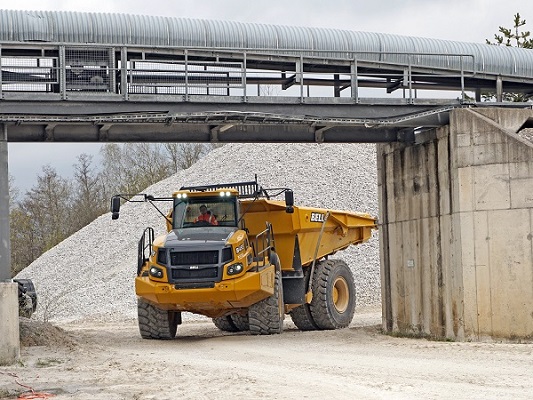
At the upper end, the Bell B60E 4x4, with a 55-tonne payload and 35m³ dump body capacity, is now a benchmark for all-weather operations on undulating ground in opencast mines or large quarries. At the bottom of the range, the Bell B30E 4x4 (28-tonnes; 18,5m³) is a convincing, compact and highly economical solution for sand and gravel pits, material handling or underground operations.
The second-generation Bell B45E 4x4 (41-tonnes; 25m³) is aimed at small to medium-sized quarry operations. Here it competes against rigid trucks in the 45- to 55-tonne class or 6x6 ADTs with payloads of 40 tonnes or more. Compared to both vehicles, the 4x4 truck shows its strengths to the full in typical hard-stone quarrying on rough ground with steep climbs and tight bends.
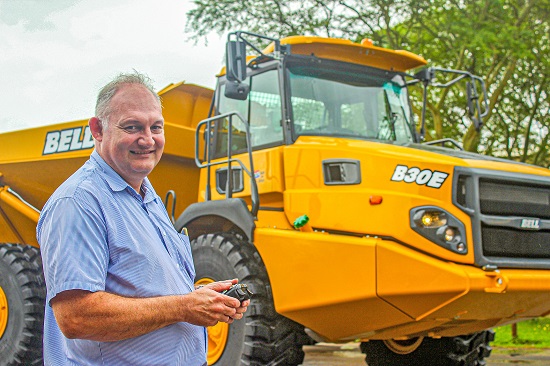
In wet weather, conventional 4x2 rigid tippers quickly reach their limits. The all-wheel-drive and oscillation joint of the Bell B45E 4x4 always ensure high traction, and the retarder and service brakes can be applied in a very controlled manner even under full load, thanks to constant ground contact by all tyres. The high power-to-weight ratio is said by Bell to keep cycle times low in difficult weather conditions and extends production times in exposed quarries. In addition, the Bell B45E 4x4 can also be used in overburden or new excavations. While this machine does not excel in soft underfoot conditions like its 6x6 counterpart, Bell says its twin-tyred single rear axle brings substantial advantages over 6x6 ADT tandem axles on hard roads. In tight corners, the tandem axle experiences significant tyre wear and wears the road down. In addition, there is greater manoeuvrability thanks to the shorter rear chassis, which, together with the rock bin typical of quarries, is said by Bell to result in faster cycles on the quarry faces or at the primary crusher.
At its first presentation at bauma 2019, the Bell B45E 4x4 generated great interest, especially among Central European quarry operators. The 4x4 two-axle vehicle suits their job sites and productivity requirements well. Bell's product and application specialists also recognised the potential in a segment characterised by a shrinking range of corresponding rigid dump truck solutions. Triggered by the company-wide transition of all Bell ADTs to EU Stage V, it was decided to revise the first generation. In addition to the Stage 5 improvements, several changes were incorporated based on user feedback from practical tests and initial customer placements.
The most significant changes relate to the rear end of the Bell B45E 4x4. The rear axle is now suspended, and the bin has been heavily modified. Despite this, the frame length and wheelbase remained almost identical, making the two-axle articulated truck highly manoeuvrable (max. turning circle: 17.31m).
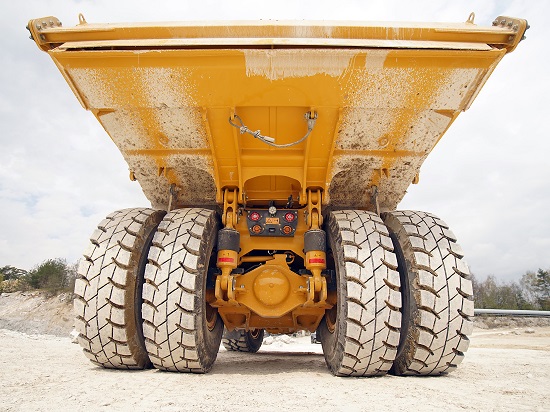
As with the 60-tonne Bell B60E 4x4, two oil/nitrogen hydro-pneumatic struts now take over the suspension of the rear axle from German manufacturer Kessler. Combined with the standard adaptive 'Comfort-Ride' front suspension, this provides significantly more driving comfort for a vehicle that weighs around 79 tonnes when loaded. In addition to a limited slip differential, the rear axle also features sensor-supported automatic traction control. The new suspension geometry and kinematics have been designed to allow the 21.00 R35 twin tyres to be fitted with snow chains.
The exhaust-heated rock bin with flat bottom of the Bell B45E 4x4 has been completely redesigned. For better matching with the wheeled loaders, often typical in small to medium-sized quarries, the standard bin has been lengthened and given a straight front wall. This provides a longer body top edge and better filling speed with wide 3.5 to 6m³ rock shovels (bin height: 3,485mm). Both the maximum tipping height (6,485mm at 55°) and the large ground clearance of the chute (890mm) remain almost unchanged. This means that the articulated 41-tonne two-axle truck can be fitted into existing infrastructures (e.g., crusher enclosures) much more easily than comparable 6x6 articulated trucks with a long earthmoving body but offers their advantages over conventional rigid tippers that have a low tip clearance when unloading quickly on any terrain. As an alternative to the 4,265mm wide 25m³ standard body (with tailgate: 26m³ / 4,639 mm), a narrower version of the same capacity is now available as an option, ensuring the vehicle width is under four metres with tailgate. The slightly longer 'narrow' body with raised bin height (3,671mm) can be loaded with heavy wheeled loaders but also works well with excavators.
The Bell B45E 4x4 has an almost identical front end to its 6x6 sister model, the B45E. This means that operators benefit from Bell's continuously developed 6x6 articulated large-series technology in drive, power transmission and intelligent vehicle control. Under the bonnet is the 390kW in-line six-cylinder OM471LA from Mercedes-Benz. Exhaust gas treatment to the requirements of EU Stage V is handled by a low-maintenance system consisting of controlled exhaust gas recirculation (EGR), SCR technology and a diesel particulate filter. Together with the 'self-learning' Allison seven-speed automatic 4700 ORS, the torque-optimised engine (2,460NM at 1,300rpm) ensures high fuel efficiency, which is reflected in low consumption rates. As with the other current Bell large ADTs, multi-disc wet brakes on both axles work in collaboration with the Jacobs engine brake to provide automatic retardation when the operator releases the accelerator pedal.
The workplace in the spacious Bell standard cab of the B45E 4x4 is said to offer good visibility, high comfort and a complete standard package of driver-related assistance systems. These include, for example, Hill Assist as well as loading and tipping routines that ensure productivity and safety in equal measure. All electronic assistance and status displays are based on real-time measurement data from the networked vehicle sensors (onboard scales, tilt and roll sensors, etc.). Much of this information is also available for computer analysis and tracking using Bell's satellite-based machine monitoring system, Fleetm@tic.
Achieving an autonomous ready platform was a natural progression after the ability to integrate Bell ADTs with pedestrian detection systems (PDS), and collision avoidance systems (CAS) was incorporated as standard in 2019.
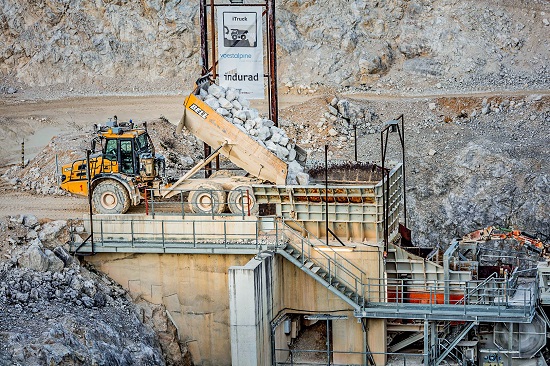
Bell first demonstrated that cost-effective articulated hauler remote control is achievable with the right building blocks when it successfully operated a B45E with a video game controller. Since early 2020 the company has been working with indurad and voestalpine on a lime quarry site in the Alps, where the industrial radar specialist has fitted its iTruck autonomous haulage system (AHS) on Bell B30E ADTs with excellent results.
A collaboration with American safety and automation technology developer, Pronto AI, followed, and they officially launched their product at MINEXPO 2021 in Las Vegas in September. In the next few months, a fully-fledged test site will also be open to the public near Orlando, Florida, where three autonomously operated Bell B45Es and a Bell B50E will be working on an established sand mine.
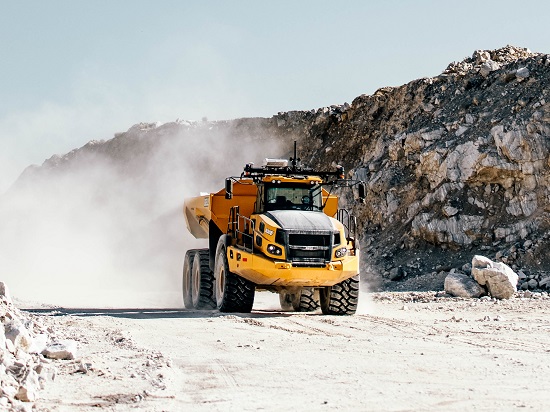
"Autonomous vehicle operation is an exciting space to be working in," says Eben Lemmer, Bell Equipment's manager: Electrical and Software. "Not only is it aligned with the Fourth Industrial Revolution's objective of achieving higher levels of automation for greater process efficiencies and cost reduction, but we believe it will deliver safer vehicle behaviour by reducing the instances of human error and negate the impact of whole-body vibration on operators in the workplace."
Lemmer continued: "In most cases, an autonomous operation will also need the end customer to set up their site to work differently; there may be special traffic control measures, berms or even different roads needed. At this point in time, Bell has an autonomous ready solution available for customers that are interested in doing proof of concept work in their application."