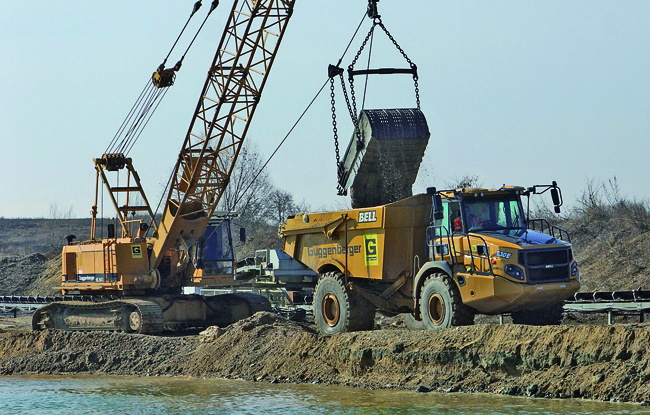
A Bell Equipment B30E 4x4 articulated dump truck (ADT) is proving a valuable hauling all-rounder in production, material handling and overburden removal at the Guggenberger gravel plant in Mintraching, Germany. Guy Woodford reports.
Guggenberger Mintraching gravel plant’s versatile
With stationary aggregates, asphalt and ready-mixed concrete processing facilities, the production of construction materials was expanded in the 1960s and has subsequently been modernised. Today, around 20 employees are working on site, predominantly to meet the company’s own demand for construction materials in the region. Guggenberger extracts 200,000tonnes of river gravel/year in Mintraching. The suction dredger excavates to a depth of six metres. The material is then transported on a land conveyor to the processing plant. When working with the dragline excavator, during stripping of the 60 to 70cm overburden layers, or in the restoration of exhausted pit areas, conventional loading and transport equipment is used with excavators, wheeled loaders and articulated dump trucks. This equipment also works in production and material handling at the processing plant.
For 12 years, up until mid-2017, a Bell B25D accumulated 13,500 hours performing a range of functions in the pit, doing overburden stripping, silo discharge and stockpile work. When it came to replacement, Guggenberger chose to remain with Bell Equipment and, following a detailed evaluation with the regional Bell distributor, Beutlhauser Baumaschinen, the company decided to invest in the two-axle Bell B30E 4x4 truck, which promised best value and better long-term cost efficiency under specific local conditions.
“On the short cycles between material boxes and stockpiles within the plant we regularly transport up to 200 tonnes per hour. Depending on the material, our records for the former and recent Bell ADT generations indicate fuel consumption values of barely 12 litres per hour,” says Harald Birk, Guggenberger Mintraching site manager.
For the longer cycles (up to 1,500m) on the well-maintained roadways in Mintraching, haulers do not require 6x6 traction. Accordingly, the 4x4 two-axle truck scores with very low tyre wear. It also shows off its strengths with a relatively short total length and small turning radius in a traffic network that is often narrow. In direct comparison with the three-axle Bell B30E, the 4x4 offers a turning radius of 14.6m, some 1.3m smaller than the traditional 6x6 ADT. The shorter rear chassis with redesigned dump body makes manoeuvring much easier. Without the scuffing middle axle tyres, the roadways between the stockpiles, which accommodate the conventional tipper trucks that also run there, are spared.
“Especially in our stockpiling area where we have in excess of 100,000 tonnes of different products, the two-axle Bell truck scores with its better manoeuvrability, which has substantially improved the loading operations from the piles,” explains Birk.
The front of the truck is identical to the conventional B30E, including articulated steering and the oscillation joint, while the rear axle comes with reliable B40 and B50 componentry. The 246kW Mercedes-Benz turbodiesel engine with
“Our operators always appreciated the good visibility and fully inclusive standard features of the Bell ADT cab. Implementing the new series, Bell Equipment has once again attached great importance to the drivers’ comfort,” adds Birk.
With a nominal 28tonnes, the two-axle truck offers the same payload as its 6x6 30tonne equivalent – the high strength, solidly mounted 36tonne rear axle is fitted with 29.5R25 tyres (front: 23.5R25). The redesigned bin with a flat floor offers a capacity of 18.5m³ (SAE 2:1), one cubic metre more than the dovetail 6x6 body. In Mintraching, the B30E 4x4, fitted with an automatic tailgate, gives easier and faster loading of easy-flowing sands and gravel from the silo tanks to the shorter bin.
During tipping, the shorter hydraulic cylinders translate into faster dump cycles while the low tipping height of the B30E 4x4 is important for specific applications such as tunnelling or underground mining. The standard 70° tipping angle can be electronically set to a smaller angle.