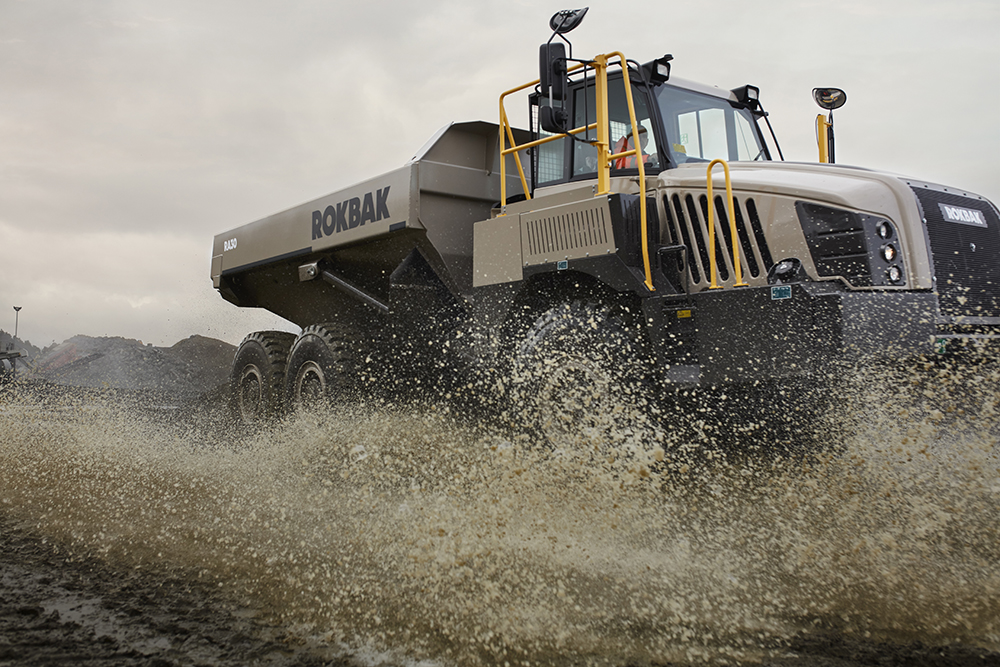
The global articulated hauler market is continuing a general expansion with strong demand in all regions.
The total global market was around 8,200 units in 2021 and this year could be as high as 9,000 according to Guy Wilson, global sales director at articulated hauler manufacturer Rokbak.
Wilson adds that the US is leading articulated hauler demand with huge infrastructure spend. A large amount of construction activity around house and road building means that North American customers currently account for about half of the total market.
The UK is the second-biggest market for articulated haulers, says Wilson: “Demand is increasing here thanks to the High Speed 2 (HS2) major infrastructure project that will connect towns and cities in the South, Midlands and North.
“It’s [been] one of the most important economic regeneration projects in Great Britain for decades and it’s already helped the UK articulated hauler market go from an average of around 400 machines a year to over 700 in 2021 – and it’s expected to increase further this year.”
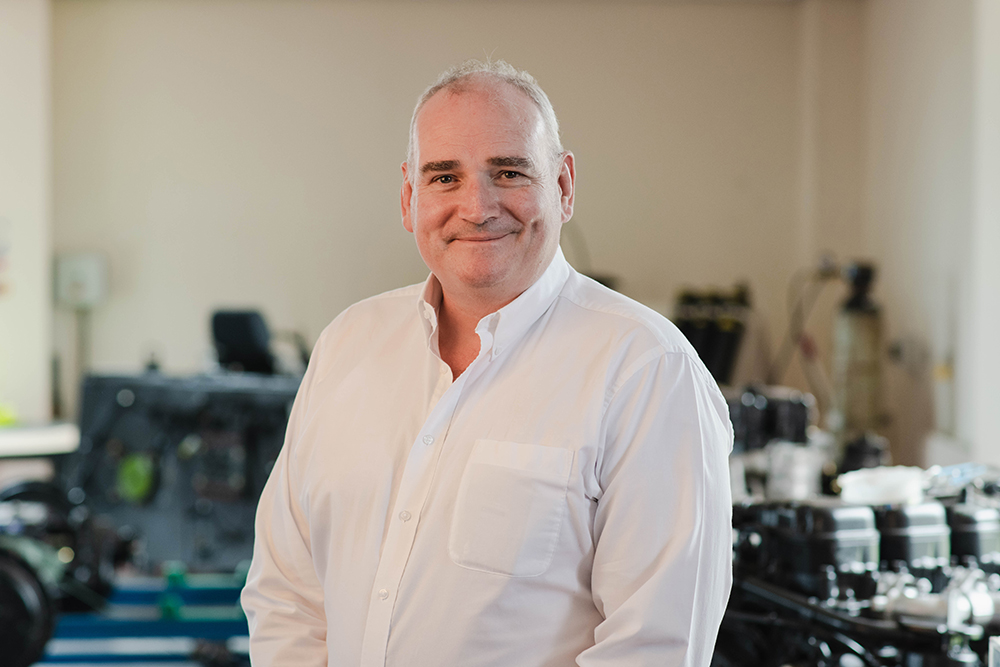
Wilson adds that the Scotland-based, Volvo-owned Rokbak is seeing huge demand for its RA30 and RA40 articulated haulers, with both dealers and customers enthused by the new machines.
“On the HS2 project, the RA30 and RA40 are needed for preparatory work and transporting materials,” he says. “This includes vegetation clearance and earthwork for tunnel portals and compound facilities. The project will also lead to an increase in the demand for UK aggregate production, which will again create a positive impact on articulated hauler sales.”
Rokbak has been celebrating winning the Marketing and the Young Person of the Year categories at the CeeD Industry Awards 2022.
CeeD (Centre for Engineering, Education & Development) is a national body that supports a range of industry sectors in Scotland, bound together by a common aspiration to improve operational efficiency, effectiveness and profit through peer-to-peer knowledge exchange.
Rokbak’s entry for the Marketing category focused on the company’s successful global rebrand campaign. Judges were impressed with the passion shown by the marketing team, who worked in unison with other Rokbak teams, to help devise and drive the campaign – which also included direct feedback from both dealers and customers. This ensured Rokbak (formerly Terex Trucks) and its robust RA30 and RA40 haulers received extensive coverage in the national and international trade press, as well as across social media.
Rokbak’s evening of success continued as Rhys Dingwall was announced CeeD’s Young Person of the Year.
The 19-year-old joined Rokbak through the company’s partnership with local authority, North Lanarkshire Council and their No Limits Scheme. The initiative is linked to the Supported Employment Scheme, which matches jobseekers who have additional support needs and/or disabilities to recruiting companies.
Sharing Rokbak’s plaudits was also Ross Mitchell, who was shortlisted for the Young Person of the Year category. The 23-year-old joined the company in 2017 and has excelled working with the New Product Introduction teams, helping to implement quality processes and inspection documentation for Rokbak’s new haulers being distributed around the world.
Volvo Construction Equipment (CE) is continuing to evolve its range of articulated haulers, with enhancements designed to make them smarter, more efficient and easier to operate. The manufacturer says the improvements mean uptime is maximised, whilst maintenance costs are kept to a minimum, reducing total cost of ownership.
Volvo CE’s Haul Assist suite of tools is designed to get the most out of the company’s articulated haulers. Powered by a 10” Volvo Co-Pilot monitor – which is available on a variety of machines from haulers and excavators to pavers – it provides insight to help customers optimise the efficiency of their haul cycles and boost profitability.
A new addition to Haul Assist is the tyre-pressure monitoring system, which enables monitoring of tyre pressure and temperature from the comfort of the cab. Volvo CE says that, with inflation pressure having a marked impact on tyre wear, proactive monitoring is invaluable to optimise tyre life as well as fuel efficiency, machine performance and operator comfort.
Map provides a real-time overview of the on-site traffic to help navigate more effectively. The whereabouts of every machine and vehicle – irrespective of the type or brand – as well as visitors on site are now visible, so long as they are connected to the map application. Alongside haul roads, Map also shows load and dump zones, and flags single-lane sections, restricted zones and speed-restricted areas, helping to anticipate operating decisions and reduce unnecessary stops.
Volvo CE says that operator comfort has always been at the heart of its hauler design – from the centrally-positioned operator seat offering excellent visibility, through to user-friendly controls. It adds that a range of automated functions is now offering even more support to enhance ease of operation and performance.
Terrain Memory is a useful feature of the intelligent Volvo drivetrain that identifies and remembers slippery road segments to ensure optimised traction control and off-road mobility. OptiShift enables fast and smooth directional changes, whilst the downhill speed-control function automatically maintains a constant speed when operating on downward gradients; both these, and the cruise control function, have been fitted as standard since 2019 and are available for retrofit on older haulers.
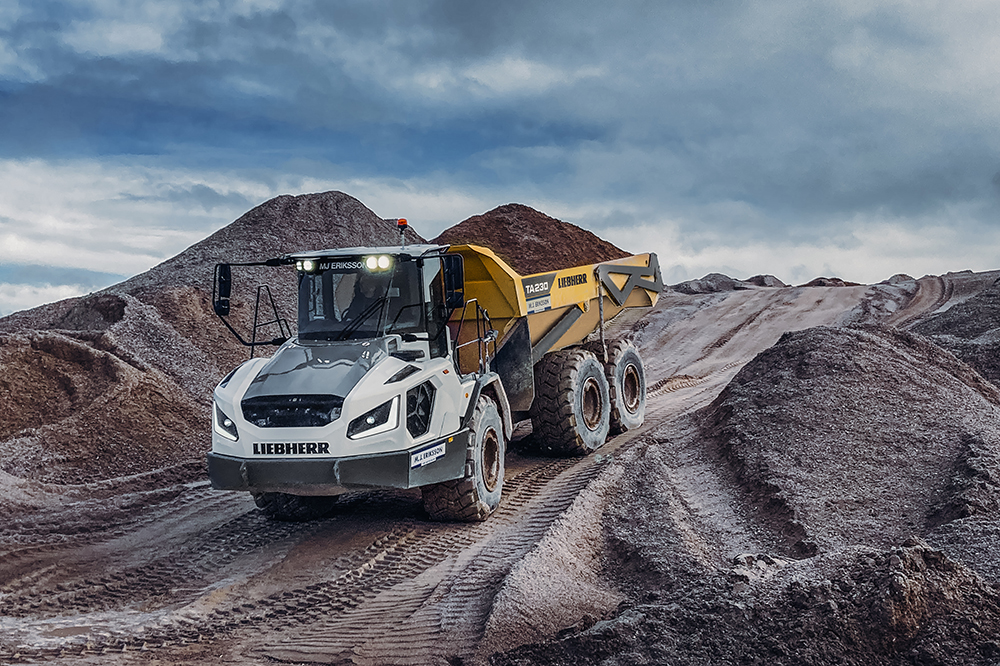
Volvo’s articulated haulers are also designed to be easy to service. Instead of daily or weekly greasing, its haulers now require the process every 250 hours, which the manufacturer claims is the longest time interval in the industry. In addition, there are long engine-service intervals – up to 1,000 hours on Stage V and Tier 4 Final models – and what Volvo claims is less than half the fluid volume of most of its counterparts when measured over the lifetime of the machine. It says the result is reduced maintenance requirements and consumables, helping to keep the machine at work while lowering maintenance costs and environmental impact.
One of Denmark’s largest construction companies, M.J. Eriksson, says it is reaping the benefits from deploying a Liebherr TA 230 Litronic articulated dump truck.
The company uses the new truck for large infrastructure projects in Denmark and southern Sweden. The articulated dump truck is the 300th Liebherr machine purchased by Eriksson over the years. For over 40 years Liebherr, the construction company and the sales and service partner Johs. Møllers Maskiner A/S say they have maintained a close working relationship based on trust.
M.J. Eriksson specialises in general civil engineering, special civil engineering and track construction work. The company claims to have the most advanced and largest machine fleet in the country. Over half of the machines are from Liebherr. It has been operating the TA 230 since 2021 and is using it successfully in various road construction projects. It is responsible for the movement of materials in remediation work of existing infrastructures or the creation of new infrastructures.
Eriksson says it is impressed by the overall concept of the TA 230, with the machine moving up to 28 tonnes of material per loading. A powerful drivetrain combined with the automatic traction control gives the machine excellent driving performance and combined traction. This increases the operating efficiency and ensures higher handling capacity as well as greater cycle times on the construction sites.
The company uses the TA 230 at different locations with a radius of up to 500 kilometres. Another advantage of the Liebherr dump truck is that, thanks to the optimal transport width of under three metres, it can be transported quickly and without a costly special permit.
Arusha is Tanzania’s picturesque safari capital with Africa’s largest and fourth-largest mountains, Mount Kilimanjaro and Mount Meru, as its backdrop. The city is also the headquarters of Willy Enterprises, a multi-faceted business involved in construction, drilling, mining/quarrying and plant hire, among other activities.
The company was founded in the late 1980s by Wilson Mgonja, a civil contractor and entrepreneur with over 30 years of experience, who says: “Growing our equipment fleet with premium machines has been critical to our growth and today we have a substantial fleet that includes graders, dozers, backhoe loaders, rollers, excavators, wheeled loaders and articulated dump trucks. We have 12 Bell machines in our fleet, having bought our first Bell ADT in 2012 through the previous Bell dealer in Tanzania.
“After a reference by a business partner we tried purchasing a B20E for a small project. Seeing how it outperformed other brands of ADTs we were happy to settle with it. After we landed a bigger project, we simply upgraded the size and will now never look back.”
Mgonja says his company was impressed by the quality, durability, efficiency and overall cost-effectiveness of the Bell machine.
Willy Enterprises’ newest Bell ADTs are two B30Es and two B40Es that were delivered in May 2021. They were bought from Bell Equipment’s dealer, Kanu Equipment Tanzania, with a standard warranty of 12 months/2,500 hours. They currently work at a major cement factory in the Tanga region of the country where Willy Enterprises has a production target of about 210,000-378,000 tonnes per annum. The ADTs haul limestone and red soil from the mine to feed the conveyor and crusher on a round trip that varies between 2,8km and 5km. “It’s steep terrain, which quickly turns muddy after a rain shower, but these vehicles have excellent traction control and work without any problem, no matter the underfoot conditions,” Mgonja says.
Each truck works two 12-hour shifts per day and averages about 423 hours of operation per month.
Bell’s Fleetm@tic telematics system ensures that Mgonja knows that production averages between 69.3 and 83.6 tonnes per hour and fuel burn is 12.9 to 16.1 litres per hour.
Bridgestone is launching a 3-star rigid dump truck tyre as an expansion of its 24.00R35 product portfolio, a line-up specially developed for mid-sized rigid dump trucks to carry hefty loads on flat terrain, often at quarries and mines. Featuring a 3-star rating, the new 24.00R35 delivers 8% greater payload capacity along with a deeper tread depth to provide excellent tyre wear and improved traction. Additionally, the tyre provides a high resistance to cuts and heat as trucks transfer larger hauls between long distances at high speeds.
"As demand continues to strengthen in the construction and quarry segments, we remain dedicated to helping maximise productivity for our customers by pairing intelligent products with best-in-class services and integrated technology solutions," said Rob Seibert, president, off-the-road tyres, Bridgestone Americas. "We are meeting growing industry demand with a superior product that features new technology and enhanced performance to optimise productivity."
Bridgestone is scheduled to begin production on the new 24.00R35 rigid dump truck tyre with an all-new traction pattern in late 2022, followed by a new hard-rock pattern.
US truck body design company Philippi-Hagenbuch is now offering in-stock inventory of its most popular sizes of rear-eject bodies for trucks. The manufacturer says this reduces the rear-eject lead time for 35- to 45-tonne truck models to six weeks or less, in most cases.
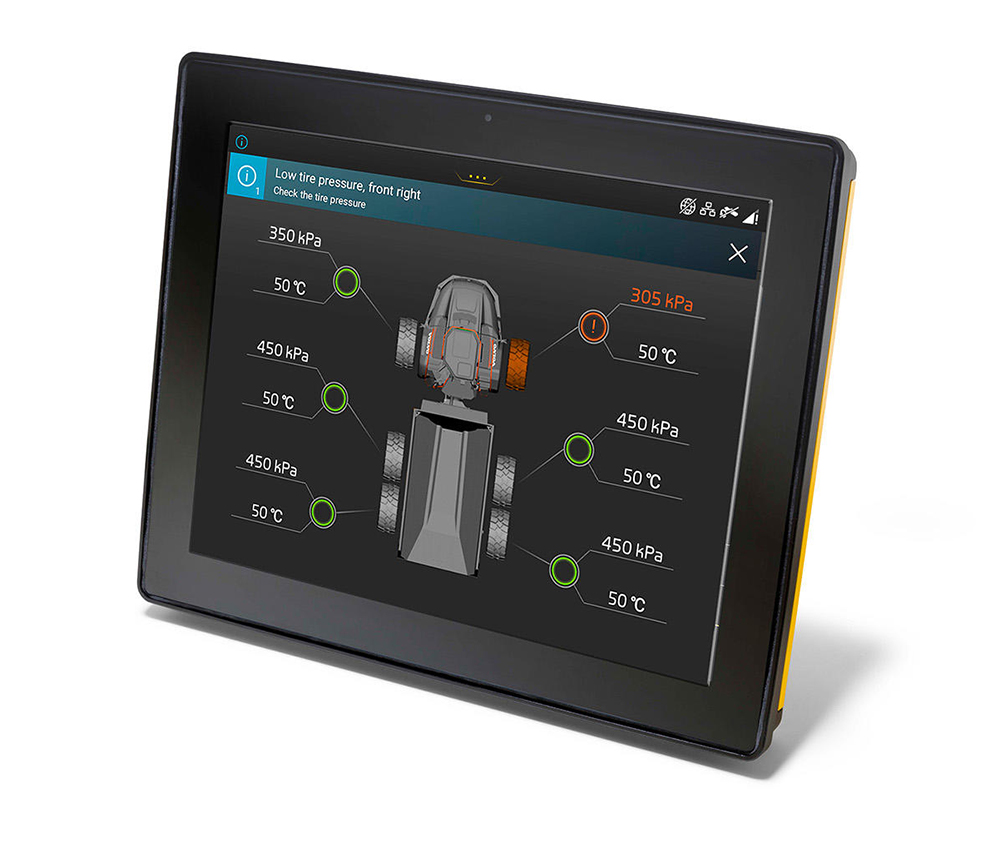
Over the past 23 years, Philippi-Hagenbuch (PHIL) says it has manufactured hundreds of rear-eject truck bodies to help customers increase their productivity, safety and stability for off-highway operations. Rear ejects are engineered and manufactured to fit the specific truck body chassis and are easy to operate in the cab, reducing dumping and spreading time by eliminating the need to stop and raise the truck body.
A variety of industries, including aggregates, general construction and mining, use rear-eject bodies and trailers to significantly improve their productivity when dispensing material and overcoming situations where overhead barriers inhibit traditional dump bodies.
“We are dedicated to offering our clients the equipment they need, tailored to increase the productivity of their specific haul trucks,” said Josh Swank, Philippi-Hagenbuch vice president of sales and marketing. “We remain committed to offering customised solutions for our customers, including our rear-eject product line. However, we have found that the majority of our rear-eject bodies are for 35- to 45-ton trucks and we can now offer a faster turnaround time for those customers by maintaining an inventory of our most common models. This is especially beneficial with so many of our clients facing the current supply-chain and lead-time challenges.”
Philippi-Hagenbuch says it continues to custom engineer and build rear-eject bodies and trailers for a variety of makes and models of off-highway trucks to provide solutions for each customer’s unique needs. Beyond its in-stock sizes, the company manufactures rear ejects that can fit 25- to 60-tonne haul trucks. The rear-eject bodies are manufactured exclusively with high-strength, abrasion-resistant Hardox 450 steel for the greatest structural strength and durability. Due to their all-Hardox construction, which PHIL made as a commitment through SSAB’s ‘Hardox In My Body’ campaign, PHIL says its rear ejects are proven to last up to 20 years and are often put on a second truck after the first chassis has worn out.
“Over the last few years, we have made it a priority to evolve and update our rear ejects based on feedback to offer an even better product for our clients,” said Swank. “We had a vision to further develop not only the operation of both the ejector blade and the rear tailgate mechanism, but to reduce the number of parts, evolving the track design to strengthen the body sides and to decrease the need for maintenance or replacement.” AB