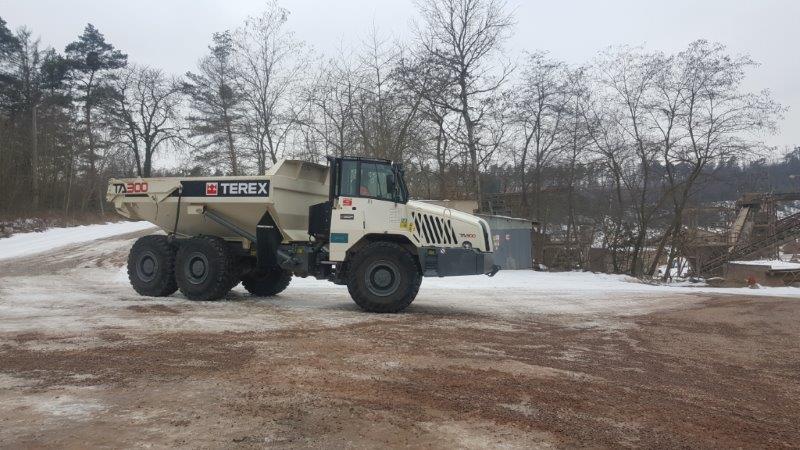
Haulers are proving their worth in quarries worldwide as many new and upgraded models appear. Patrick Smith reports.
Among the Czech Republic’s ancient territories is Bohemia, home to the rural community of Zdechovice, where leading aggregate supplier Kamenolomy operates a quarry.The company, founded in 2005, is a part of the
It looked no further when
“We chose to go with Terex Trucks’ TA300 because in the past we have had a good experience with the brand,” says Pavel Houdek, engineer at Kamenolomy.
“As a company, it is important to secure a permanent increase in the scope of production to keep our customers happy, and we knew we could rely on Terex Trucks’ articulated hauler to offer us maximum return on our investment.” Created at the Motherwell factory in Scotland, the ADT will be in operation 12-hours-a-day transporting reddish biotite granite around the quarry.
With fully independent front suspension as standard, tyre/ground contact is maintained regardless of the terrain, increasing tractive effort and reducing cycle times while also providing operators with a comfortable haul.
Powered by a fuel-efficient five-cylinder
In addition, the transmission retardation system in combination with engine exhaust brake support the fully-enclosed oil-cooled multi-disc brakes for enhanced protection, resulting in less maintenance and a longer life span for the brakes.
“The dump truck is simple to use and its fuel consumption is great but another key aspect of the machine is how well it is supported by ABM,” says Houdek.
“We have had a good relationship with the dealer for five years and we are consistently impressed by the team’s flexibility and willingness to help us out.”
In the UK, two new
When Yarrows started its quarry operations at Little Catwick, it acquired two second-hand Volvo articulated haulers to get things up and running, and more recently it has hired in haulers on a regular basis to move and re-handle the extensive types of material on site. “This has been especially so since we commissioned our recycling plant just two years ago and consequently we came to a rapid conclusion that investing in our own machines would become far more cost effective in the long run, says John Bird, managing director.
“In the end, the overall package on the table and machine specification and high residual values coupled to our good experience all round operating Volvo equipment, became the deciding factors for choosing the A30Gs.”
The A30G hauler from Volvo meets the requirements of Stage IV final emissions legislation, being powered by an electronically controlled, six-cylinder 264kW turbo-charged Volvo V-ACT diesel engine.
The two A30Gs supplied to Yarrows Aggregates feature some significant upgrades that have been applied to the Volvo articulated hauler product for 2017. For example, the A30’s payload has been increased to 29tonnes, as has its heaped volume by 05.m³ to 18m³, and the body material has been upgraded from HB400 to HB450 for improved wear characteristics.
Other features include Hill Assist as standard, whereby the hauler can be held on a slope until sufficient torque to move the machine is detected.
The haulers now include Volvo dynamic drive for smarter gear shifting, which takes the environment and payload conditions into consideration, and finally, an on-board weighing system which can log all transported loads for complete payload management that can be accessed remotely via Volvo’s CareTrack telematics system.
“Volvo’s on-board weighing solution was another major reason for choosing the new A30Gs,” says Bird.
Meanwhile,
This new function, incorporated as standard on all ADTs manufactured after 1 January 2017, is also available as a software update for all -5 machines produced before that date if requested by customers.
Another new standard feature is the engine auto shut-down function, also incorporated in all new Doosan ADTs and available on customers’ requests as a software update for machines produced before 1 January 2017.
The operator can set a time after which the engine will automatically shut down if the computer does not detect any activity in the machine.
All new Doosan ADTs are now equipped with an electronic transmission oil level sensor (instead of a dipstick system), which will make oil level checks a much simpler and more reliable process to carry out. Like those available in the automotive industry, Bluetooth radios are now a standard feature on all Doosan ADTs, resulting in improved safety levels.
“Safety can also be increased by the additional hand rails for service and maintenance work that can now be installed on the DA30-5 and DA40-5 ADTs,” says Doosan.
“The fuel consumption of the DA30-5 and DA40-5 ADTs is down to a combination of features including
The Doosan DA30-5 and DA40-5 ADTs are powered by Scania DC9 276kW and DC13 368kW diesel engines, respectively, meeting the Stage IV/Tier 4 Final emission regulations by using SCR and EGR technologies, with an electronic engine brake system, one of four brake systems on the trucks.
The Stage IV/Tier 4 Final ADTs do not need a diesel particle filter (DPF) to meet the emission regulations.
Detailed interactions with customers, operators and the Bell sales team enabled design engineers to enhance the specification of the B40E to provide more effective on-board diagnostics and user warnings, advanced operator comfort and the ability for customers to remotely monitor their B40E from anywhere in the world using the upgraded Bell Fleetm@tic on-board fleet management tool.
In response to customer requests, Fleetm@tic has been developed to report when unsafe tip conditions have been reached and the premium package allows customers to view load by load data on the website.
“The five-year research and development programme this machine has undergone has given us the time to be meticulous with its evolution,” says Richard Higgott, sales manager at Bell Equipment.
Comparative testing between the B40E and the B40D has shown that, taking all variables into account, the B40E delivers up to 10% lower cost per tonne than the B40D.
The B40E is powered by a Mercedes Benz OM471LA engine, optimised for off-road use by MTU, and Bell Equipment UK says the B45E will follow towards the end of the year with a powerful new engine; a rated payload of 41,000kg, and a bin volume of 25m³.
Both trucks feature a Komatsu SAA6D170E‐7 engine with its power increased to 578kW, and an optional Komatsu Traction Control System (KTCS), which automatically applies the brakes independently to achieve optimum traction in varying ground conditions.
“With the integration of the latest Komatsu engine technology, and increased power, the new HD465‐8 and HD605‐8 are designed to offer maximised productivity and low operation costs” says Jeroen De Roeck, product manager at Komatsu Europe.
“The new spacious and ergonomic operator cab, with fully adjustable, heated and ventilated operator seat, provides a first‐class comfortable work environment”.
The latest KOMTRAX telematics, and the Komatsu Care maintenance program, are said to offer fleet management and support; protect the machine against misuse, and guarantee maximum efficiency and uptime.