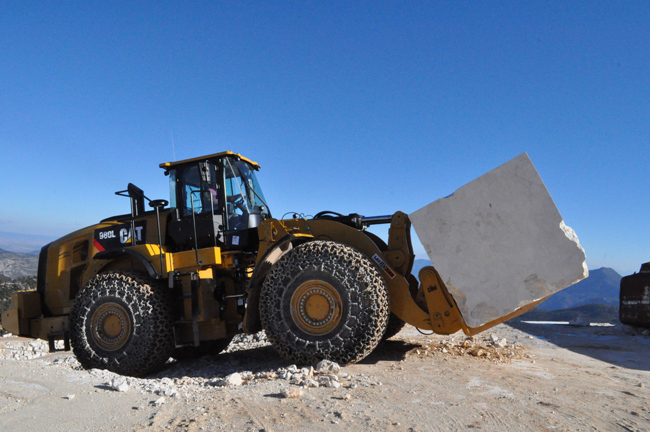
Loaders from a leading global market manufacturer are playing a key role in the Turkish marble production sector, while other key models are proving their worth in busy quarries. Guy Woodford reports.
Turkish marble producer Imsa Mermer, headquartered around an hour’s drive north of Antalya, a city on Turkey’s south-west coast, has a well-earned reputation for the high quality of its travertine marble.
Founded and run for many years by Abdurrahman Tekin and his two brothers, Imsa Mermer marble was used to build some iconic Turkish buildings, including Sabanci Towers in the late 1980s. The giant twin-tower structure is the headquarters of
Imsa Mermer is now co-owned and managed by Abdurrahman’s son, Ahmet. “My father was a very well-known and respected marble producer,” he tells Aggregates Business during a visit to the region. “Before going into marble production, he worked in the general construction sector in and around Antalya. It gave him a lot of insight into building materials production in this area.”
Tekin says Imsa Mermer has seen notable productivity and efficiency improvements in its quarry site loading work over the past year thanks to its two Cat 980L block handlers, purchased in 2017 through
Imsa Mermer has been using the Cat 980Ls alongside a previously purchased Cat 980G wheeled loader and other premium original equipment manufacturer (OEM) machines for marble block movement and hauler loading work at three of the firm’s 22 quarries in and around Antalya, Burdur, and Isparta.
“We heard about the qualities of the Cat 980L block handlers from some of our sub-contractors. Their durability is very good and their power very high compared to competitor models,” says Tekin. “Our two 980L block handlers do the marble block handling work of three wheeled loaders. This saves a lot of money on fuel, labour and other operating costs.
“The 980Ls with fork attachments can be used to push initial 300tonne blocks of marble away from the quarry face. This allows more primary quarry face diamond-wire cutting to take place as the blocks undergo secondary cutting. This is very efficient working. Before, it took three wheeled loaders to do the same job.
“The fuel consumption of the 980L block handlers is around 20 to 22 litres per hour. This is also very good.”
Imsa Mermer’s final marble block products tend to be sized 14-27tonnes. The bulk of export customer blocks are shipped out of Antalya or Izmir ports.
“Nine of our 22 quarries are currently active. We operate three and six are rented to other marble quarry producers,” explains Tekin. “Renting out some of our quarries reduces our trading risks and operating costs. It is hard to get new quarry licences from the national mining ministry, especially if you are a smaller company, so we are also helping others do business.”
Around 150,000tonnes of marble blocks were produced last year at Imsa Mermer’s nine active quarries, 90% of which was exported in block form to Chinese customers. “There are huge building projects in China that require consistent high-quality marble. Chinese customers like the colour of our marble blocks. China is one of 11 countries we export to.”
Turkish marble producers only close their quarries two to three days a month to keep up with export and domestic customer demand. As a result, their block handlers, wheeled loaders and haulers rack up 3,000 operating hours/year, with their excavators also clocking up around 2,000 working hours. Given such long working hours in such tough environments, it is not surprising that Turkish marble producers place great stock on quality servicing support from their local machine dealers. Borusan Cat technicians service all Caterpillar marble-producing customers’ wheeled loaders and excavators every 500 hours.
Tekin says Imsa Mermer always has its Cat block handlers and wheeled loader serviced by Borusan Cat, which always uses Cat original parts for any necessary part replacements. He says the company is looking to invest in two more wheeled loaders and an excavator this autumn, and he is keen to hear more about what Caterpillar has to offer.
The 2018 version of
The new DL580-5 is the latest model in the high-performance Doosan wheeled loader range, comprising 13 models with operating weights from 12 to 36tonnes.
With a bucket capacity of 6.4m³, the DL580-5 has a similar look to the existing DL550-5 model. Its robust structural components and an advanced sophisticated double circuit axle cooling system are said by Doosan to make the wheeled loader an ideal solution for applications such as block lifting and other heavier material-handling needs in quarrying, mining, recycling, construction and industrial applications.
To meet these requirements, the DL580-5 has an operating weight of just over 36tonnes and higher static tipping loads (straight/full turn 40°) of 29.7 and 26.2tonnes, respectively. The overall size of the DL580-5 is almost the same as the DL550-5, but the new model is equipped with a series of features that are said to make the machine extremely reliable and durable.
Doosan’s new DL420CVT-5 is the first model in the manufacturer’s wheeled loader range to be equipped with a continuously variable transmission (CVT). A CVT transmission is composed of a hydraulic motor combined with a hydraulic pump which provides a smooth and continuous speed variation.
The CVT design combines the benefits of a mechanical transmission and a hydrostatic transmission in the same machine. It allows the DL420CVT-5 to automatically transition from hydrostatic power at low speed to the mechanical system to operate at higher speeds.
By combining the two types of transmission, the new CVT technology ensures high loads can be carried at low engine speeds with high dynamics for an optimum wheeled loader operating cycle. The DL420CVT-5 therefore provides an increase in machine performance for operators working in digging, loading and lifting applications.
With a maximum bucket capacity of 4.2m³, the new Doosan DL420CVT-5 wheeled loader is intended to meet a wide range of material-handling needs from loading and transporting granular material (such as sand and gravel) to quarrying, mining, construction, industrial and demolition applications.
For most tasks, operators will utilise the hydrostatic part of the transmission, said by Doosan to offer greater fuel efficiency in low-speed applications. The combination of the two transmissions is automatic and fully transparent for the operator.
The DL420CVT-5’s complete driving range, forwards and in reverse, is controlled by the CVT system. Low engine speeds ensure a high efficiency and the highest driving comfort irrespective of the traction speed. The power-splitting continuously variable technology facilitates moving off softly and hydraulically. Furthermore, with the CVT, Doosan claims a fuel saving of up to 15% can be achieved.
Doosan’s new DL280-5 wheeled loader is said to offer high performance and high productivity with outstanding breakout force, tipping load and enhanced output. The front lift arm is powered by a closed centre hydraulic system with a 210l/min axial piston pump. This system provides maximum hydraulic performance, without producing excess capacity, thus saving on fuel and extending the lifetime and reliability of vital components.
The DL280-5 features Z-bar kinematics with a simple lifting piston system designed for heavy-duty applications. The 145kN breakout force is combined with a constant bucket angle maintained throughout the range of movement. Bucket angles are also optimised in the travelling position and at ground level.
Hills Quarry Products of Swindon, Wiltshire, England, has added four new
“We’ve been operating Volvo equipment for a good many years and, in particular, the L150 model since it was introduced back in 1991,” says divisional director, Andrew Liddle. “The L150H is the optimum-sized loading shovel for most of our sand and gravel operations and has proved to be a good performing all-rounder as an extraction tool as well as loading out high-sided bulkers,” he continues. “Our Volvo machines give good service life too and we certainly expect them to achieve 15,000 hours as a minimum for the main powertrain components.”
Two of the new 25tonne arrivals have been deployed at the company’s Upwood and Mortimer quarries. The other pair are being deployed on a new extraction project in Cotswold Water Park where one million tonnes of material is being processed over a two-year period.
The machines are powered by Volvo 13litre 224kW engines coupled to Volvo-designed powertrain components. This combination, along with other fuel-saving devices such as the Volvo Eco-pedal encouraging the operator to run the machine at its optimum rpm in the engine’s torque curve, and optishift with torque converter lock-up found in the larger L150H, are said to make these highly efficient and productive loading shovels in their size range.
All four loading shovels have been supplied with an enhanced Blue Volvo service agreement, ensuring that they will be regularly maintained at the correct service intervals by Volvo-trained service engineers using genuine Volvo parts.
Hills Quarry Products is a premier supplier of high-quality sand, gravel, stone, decorative aggregates, construction aggregates and ready-mixed concrete in southern England.
From its network of six quarries and five concrete plants, the company has long-standing relationships with customers across the UK in a wide variety of industries.