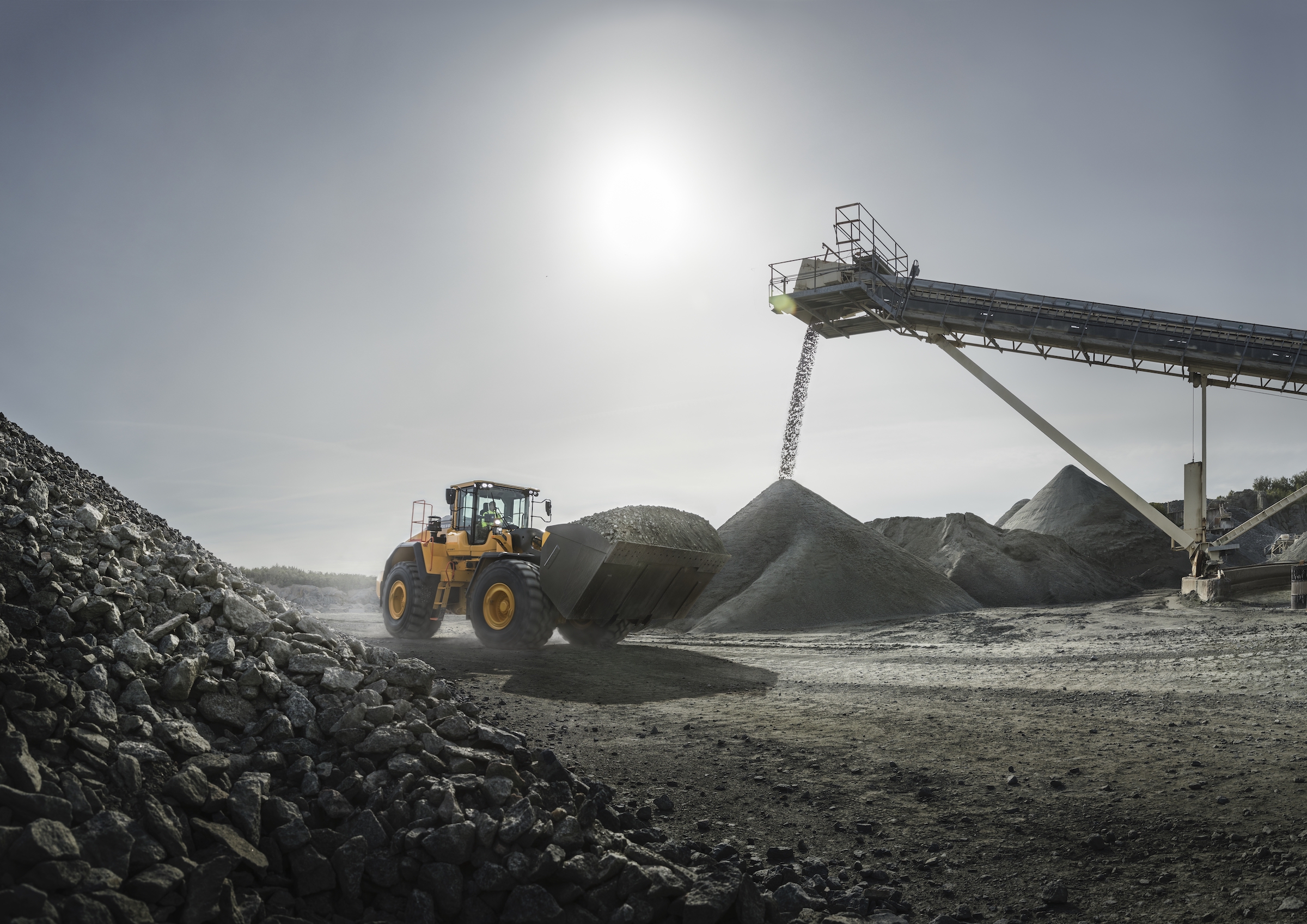
Volvo CE has added a new wheeled loader to its H-Series range, while other manufacturers also have new models. Patrick Smith reports.
The machine has been upgraded with the latest technology, and a redesigned wheel base, increased by 50mm, and the optimised weight distribution of the front frame and lifting arm system, allow for larger buckets to be used.
The L260H, powered by a D13 engine, delivers 6% more power and 5% more torque than the L250G, and next generation load-sensing hydraulics enhance the responsiveness of attachments and improve the lifting and lowering speed of the boom.
Volvo CE says fuel efficiency has been increased by up to 10%, thanks to a host of improved features, and the L260H comes with four new buckets: the Volvo Rock bucket, Volvo Sand bucket and two Volvo Rehandling buckets, specifically designed to fit the machine. The Volvo Rock bucket can hold 11.5% more material than before, and this is said to result in up to 25% greater productivity. For tunnelling applications, Volvo also offers Side Dump Rock buckets.
The 6.6m³ Volvo Sand bucket is optimised for handling sand or small fragments of aggregate, while the redesigned 7.3m³ Volvo Rehandling bucket has new convex sides to minimise spillage.
To optimise the L260H for load and carry applications, the optional Boom Suspension System automatically engages, to help reduce bouncing, and in addition, Volvo also offers a selection of Rehandling packages, while with Load Assist, customers can manage their work orders and monitor productivity.
The first L260H to be sold in Great Britain has been delivered to Lightwater Quarries of North Stainley, near Ripon, county North Yorkshire, an aggregates business that is increasing its production to around 600,000tonnes/year.
Meanwhile, Basalto La Spicca has replaced two of its
The new ZX350LCN-6s were delivered with five-year/10,000-hour HELP extended warranty and service contracts by the country’s official Hitachi dealer, SCAI.
In addition to two other Hitachi excavators, a ZX520LCH-3 and a contractor’s ZX470LCH-3, and two ZW250-5 wheeled loaders, the new Zaxis-6 machines are already said to be making a positive impact in the quarry near Orvieto.
They are equipped with double grouser shoes to enhance their stability on the quarry floor and 1.8m³ rock buckets, and one has a quick coupler as it uses a hammer attachment.
The quarry’s materials are currently used to produce stone to be laid around rail tracks and for aggregates used in the production of asphalt. A significant proportion of asphalt is now made from basalt as it helps to drain rainwater from the road’s surface.
Basalto La Spicca has always owned Hitachi machines and the arrival of the two latest models is set to strengthen its 30-year working relationship with SCAI even further.
“We are loyal to the Hitachi brand because of our relationship with SCAI, and also due to its close proximity: the SCAI office is only one hour’s drive away,” says Luca Dominici, quarry manager.
“Our machines don’t break down. We had no problems with the ZX350LC-3 after 12,000 working hours, and so the new models with HELP promise to be even better.”
Dominici and the operators on site have noticed several differences between the latest and previous generation of Hitachi Zaxis excavators. In terms of fuel consumption, the Zaxis-6 models use around 30% less fuel/ hour than the Zaxis-3.
“The -3 was a very good machine, but the -6 is quicker: for example, when it travels from one part of the quarry floor to another over short distances,” says operator Marco Maccaglia.
“It has more power, and is more stable and precise. There is also a high level of comfort and less noise in the cab, which allows me to enjoy my work even more.”
Hitachi says that by using its knowledge of the ZW-5 wheeled loader, and ongoing research of the European market, its development team has fine-tuned the ZW150-6 to better satisfy the needs of operators.
Ideal for a variety of applications, the ZW150-6 is powered by a new Stage IV-compliant engine for the same levels of productivity as the ZW150-5, but with reduced fuel consumption and running costs.
“Maintenance, operator comfort and versatility are extremely important to our customers,” says Vasilis Drougkas, Hitachi Construction Machinery (Europe), wheeled loader product manager.
“The ZW150-6 has evolved to exceed their increasing expectations. In addition, it can also be fitted with a range of specifically designed Hitachi genuine attachments and quick couplers to optimise its performance.”
Three types of lift arm, standard, high lift and parallel lift, are said to provide even greater flexibility.
It allows the DL420CVT-5 to automatically transition from hydrostatic power at low speed to the mechanical system to operate at higher speeds.
Doosan says that by combining the two types of transmission, the new CVT technology ensures high loads can be carried at low engine speeds with high dynamics for an optimum wheeled loader operating cycle.
With a maximum bucket capacity of 4.2m³, the new loader is intended to meet a wide range of material-handling needs, including loading and transporting granular material, such as sand and gravel; industrial; construction; demolition, and mining and quarrying applications.
“For most tasks, operators will utilise the hydrostatic part of the transmission, which offers greater fuel efficiency in low-speed applications,” says Doosan.
“Furthermore, with the CVT, a fuel saving of up to 15% can be achieved.”
“We have been judged against the very best in the world and the G-Series has emerged as a winner: this prestigious accolade crowns CASE wheeled loaders’ long history of excellence as we prepare to celebrate this product line’s 60th anniversary next year,” says Carl Gustaf Göransson, brand president for
CASE says it sees design as an important driver in the product development process to deliver the operator comfort and intuitive operation achieved by the G-Series.
In Germany, two
The near-29tonne loaders have a tipping load of 19.5tonnes, and are used for about ten hours a day.
With a Z-lift arm and a 5.7m² backfill bucket, they move up to 3,000m³ of sand, gravel and double-crushed chips/day, and work directly on the demolition wall, feed systems and load material in the gravel plant.
“This is where the advantages of the power-split XPower drive train come into play. This brings together the hydrostatic and mechanical drive which ensures full performance and high efficiency for all tasks,” says Liebherr.