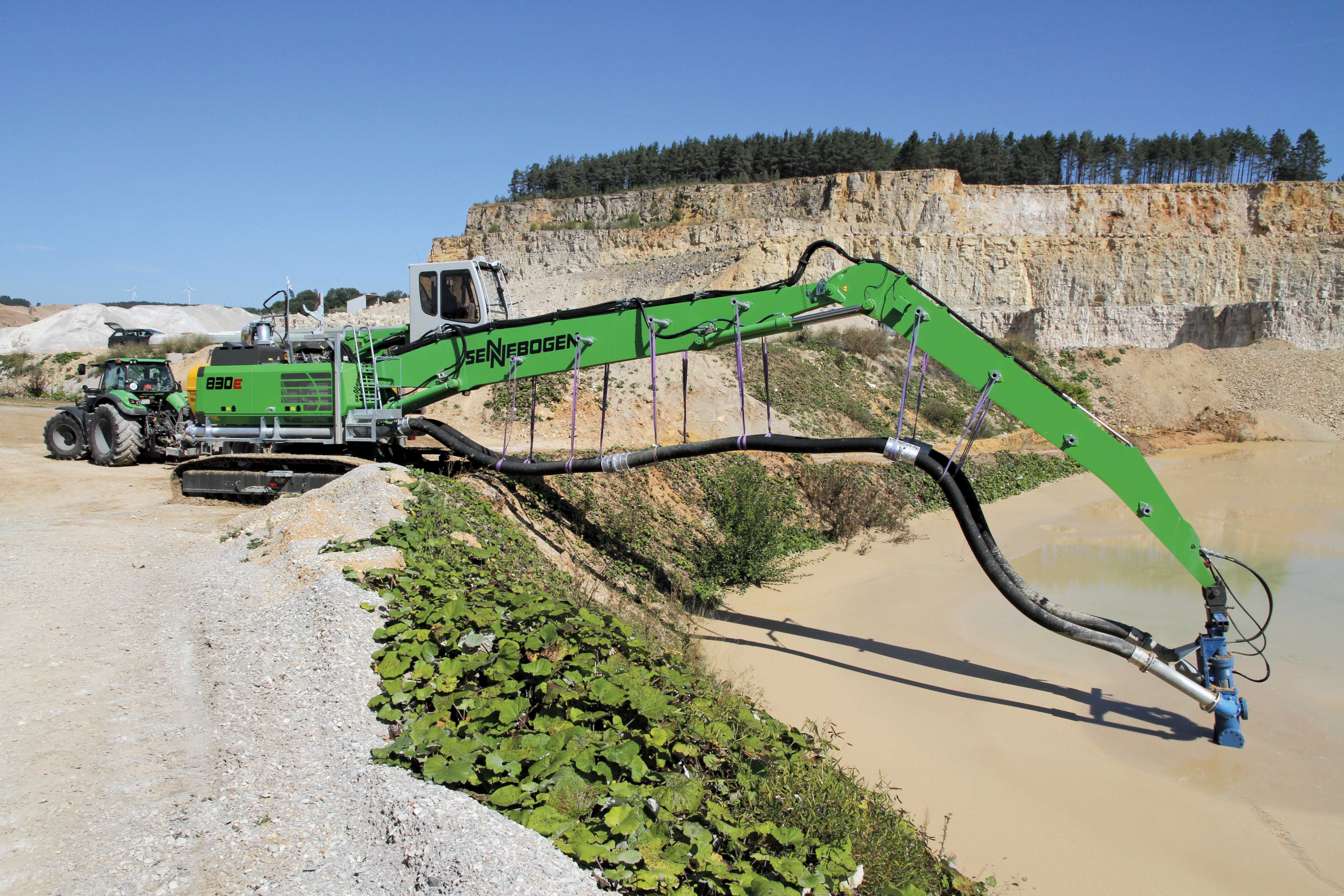
In the Bavarian town of Lauterhofen, southern Germany, Hermann Trollius has been processing limestone and dolomite for three generations.
Aside from traditional marketing, the company is now taking unconventional approaches. In order to conserve resources efficiently, Trollius is now for the first time making use of the leftovers of washing crushed dolomite. Using a
Since 1942, Hermann Trollius has been processing limestone and dolomite and refining it for a variety of uses in the agricultural, building, and industrial sectors. Manager Hermann Trollius is the third generation to run the family-owned company of 60 employees. Trollius states that he constantly strives to efficiently combine tradition and modern spirit to create value for man and nature. It’s no wonder then that he has started to develop the oft-discarded dolomite slurry with the help of a Sennebogen material handler. Trollius calls it “total resource utilisation”. While traditionally limestone and gravel are produced at the quarry for the industrial sector, for example as additives for steel and glass manufacturing, its use as fertiliser and animal feed for agriculture also accounts for a considerable portion of output. The company sells its products as animal feed throughout Europe while supplying regional industry.
Washing the crushed dolomite rock produces a slurry by-product composed of extra-fine dolomite dust. This mixture of water and dust, which previously had no use and was dumped in large quantities, will now be included in a natural recycling loop as fertiliser. “We’ve been looking for a way to use valuable raw dolomite material for a long time. Limestone has been used as fertiliser for a while now – why not use the dolomite slurry in the same way? After extensively sampling and testing slurry extraction, we decided to implement the project professionally. The solution ultimately was to use a Sennebogen material handler with a powerful suction pump,” said Trollius when explaining the idea.
Together with his employees, Trollius developed a concept that uses a Sennebogen material handler with a progressing cavity pump to move the material through a pipe and into a conventional manure tank. The dolomite is ultimately taken out to the fields where it is sprayed as manure.
The Sennebogen 830 crawler provided and supported by sales and service partner IBS Baumaschinen Service is the carrier for the progressive cavity pump and extensive piping. The machine houses the pump drive and the controller for the tube arm. The hose lines and piping were largely developed and constructed by Trollius.
The Sennebogen material handler, with a crawler undercarriage and 164kW diesel engine that would usually be used at scrap yards or ports, acts as a carrier for the pump and hose lines. The deciding factor for choosing the Sennebogen 830 was its range of 17m for positioning the pump at the edge of the landfill basin and the excellent service from Sennebogen sales partner IBS. With this solution, operator Bernd Kuhn has centralised control of all components and an ideal view of the pump and work area from the Maxcab comfort cab, which can be extended up to 2.7m.
The manure tank driven into the quarry several times a day for a few weeks now by contractor Tobias Guttenberger is filled in just four minutes. It is then taken to the surrounding fields, where the liquid dolomite dust is sprayed as fertiliser. While distributing the material, Kuhn and Guttenberger explained that, with a particle size of just 0.007mm, the dissolved dust is 10 times thinner than a human hair, allowing it not only to penetrate the soil in the form of fertiliser, but also to be absorbed directly by plants. Guttenberger is also putting his money on the pale yellow liquid for manure refinement. A mixture of just 10% dolomite to manure not only reduces the odour of the manure dramatically, but the field is fertilized and its lime preserved in just one pass.
“With the combination of the Sennebogen material handler and progressing cavity pump, we have a professional solution for pumping the dolomite slurry out of the basin. This combination and application have certainly never been seen before,” Kuhn and Guttenberger exclaim.