An expert team at Terex Trucks is hard at work across three key projects. During a recent visit by Aggregates Business magazine to the Volvo Construction Equipment company’s Motherwell, Scotland HQ, Paul Douglas, Terex Trucks managing director, explained how new Scania Stage V emissions-compliant engines for European customers would be introduced on the firm’s 28-tonne TA300 and 38-tonne TA400 articulated haulers in mid-2020, with a new state-of-the-art transmission on the TA400 also set to be introduced in the future. Longer term, work is also well underway on Terex Trucks’ next-generation articulated haulers.
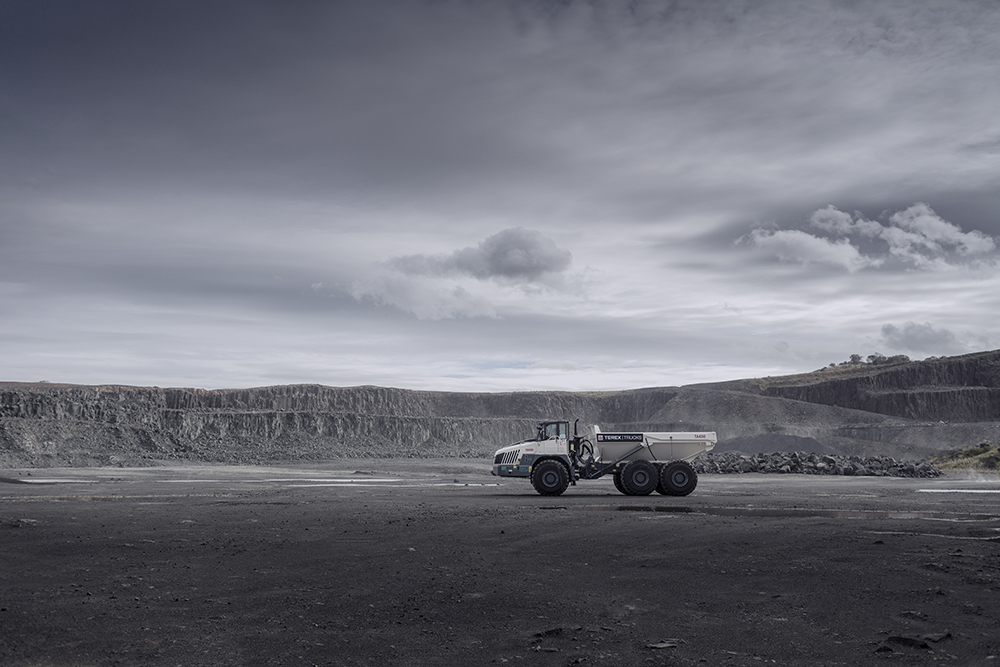
“We’ve already installed a new high-performance transmission on the TA300, which offers 5% better fuel efficiency than its predecessor as well as improved performance, productivity and operator comfort. As far as the new transmission for our larger articulated hauler platform goes, our development work and tests show that we are on track to deliver similar efficiency savings as the TA300. We’ve been developing the concept layouts and key component specifics of the next-generation models. They will continue to be robust machines with a strong emphasis on operator safety and comfort as well as total cost of ownership. Our customers like our machines because they are simple to operate and easy to maintain, so our future products will stick to this philosophy.”
Douglas says that Terex Trucks is lucky to be part of Volvo CE, where engineers are focusing on key areas for future development such as electromobility, connectivity and autonomous machines. But although he says the company will capitalise on the Volvo Group’s advances in these areas, there are no plans for this to happen in the immediate future. “Our next-generation ADTs will be connected machines, but they will have a diesel engine. We won’t be leading the way when it comes to testing future technology. It’s not what our customers are telling us they currently want, and their requirements always come first.”
Another big focus for Terex Trucks is expanding its dealer footprint. “We currently have 88 dealer partners across the world, and we’ve been working to expand this in key territories such as France, Germany and the US,” Douglas explains. “We are working with strong partners who understand the local customers and can provide them with high-quality support and solutions, with the backing from us here at the factory.”
Five years on from Volvo CE’s acquisition of Terex Trucks, Douglas believes the integration of the brand into the Swedish construction and quarrying equipment giant’s portfolio was a turning point. Since then, there has been significant investment in the product, people, processes, equipment and the site itself.
During the trip to Motherwell, Aggregates Business had a first-hand look at the extensive improvements made to the site’s factory, as well as the strong emphasis Terex Trucks places on quality control and testing all the articulated haulers that come off the production line.
“Our facility here is nearly 70 years’ old. When Volvo acquired the site, there were investments they wanted to make around safety, quality, environment and efficiency.
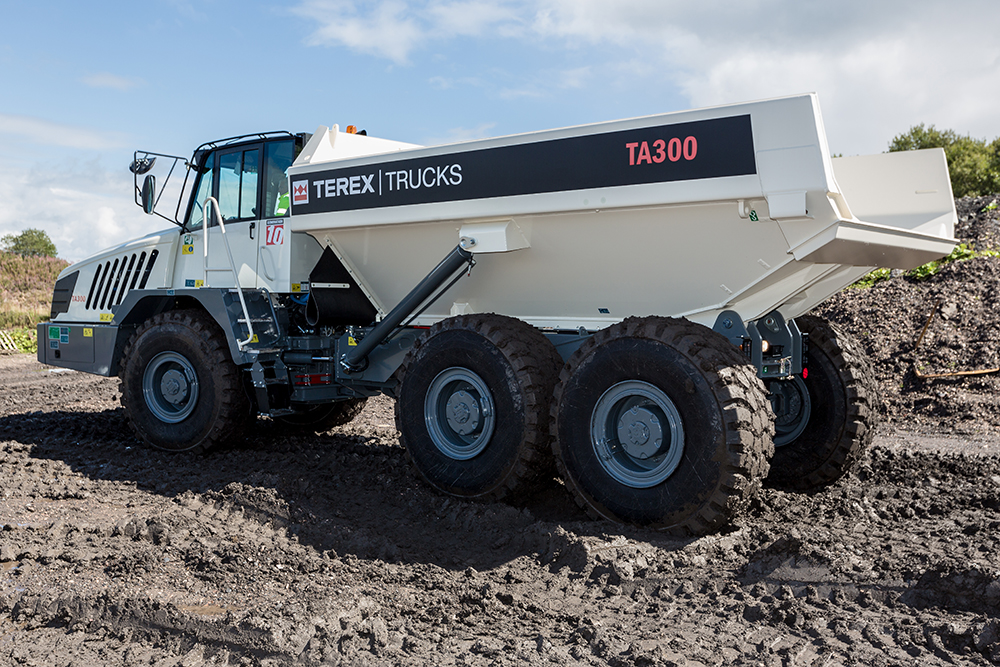
“Under Volvo CE’s ownership, there has been a capital expenditure flat-rate spend on this site of about £2 million a year – so we’ve spent £10 million so far. On top of that, there’s been exceptional spend on one-off projects totalling £7 million, including a heat treatment plant. We’ve also ordered £2.5 million worth of welding robots. These are two huge welding robots that can weld hauler bodies and frames and will improve safety, quality and throughput from our fabrication facility. We are excited about seeing them in full production, which will be during the middle of next year. It takes a long time to install and commission these robots, each one is 15 metres wide, 10 metres tall and 30 metres long.”
Douglas says Terex Trucks has also been changing its Motherwell factory layout to make it more compartmentalised and, as a result, efficient.
“Five years ago, when you walked into the factory, you could see all four walls from any vantage point. It was completely open. Welding, metal cutting, machining, assembly and inspection was all under one roof.
“Now we’re sectioning off each part of the production process. We started two years ago and have just finished sectioning off articulated hauler production. Each sectioned-off area costs around £1 million. We’ve put in things like new heavy-duty industrial curtain walls and speed doors, plus installed new lighting, flooring and tooling. This has improved air quality, energy efficiency, quality and safety, as well as instilling a sense of local ownership and creating a more pleasant working environment for employees.”
During our visit, Aggregates Business heard how Terex Trucks’ articulated hauler testing and inspections process at the Motherwell facility has also been comprehensively reviewed and updated.
Assembly line inspections start at the goods inwards point – when materials or parts from external suppliers are delivered to the site – with the thorough final inspections being the seventh and final assembly line stage. At this point, the ADT is thoroughly checked to see if it is built to the correct specifications. This includes a static inspection, speeds and pressures check, running check, running check rectification, four-hour test, four-hour test rectification, washing, unit paint touch-up, safety critical decals, a shipping inspection, unit waxing and after all this they are then ready to ship. During this process, checks are being made to ensure components are fitted as they should be, no parts are loose, there are no fuel or hydraulic fluid leaks, and that lights, indicators, windscreen wipers and other parts of the vehicle are functional. Each hauler is put through four hours of rigorous function testing at the Motherwell site’s purpose-built test track. This may occasionally result in engineering tweaks being made to the model, which is then retested, and, if no further tweaks are necessary, signed off as ready for customer delivery.
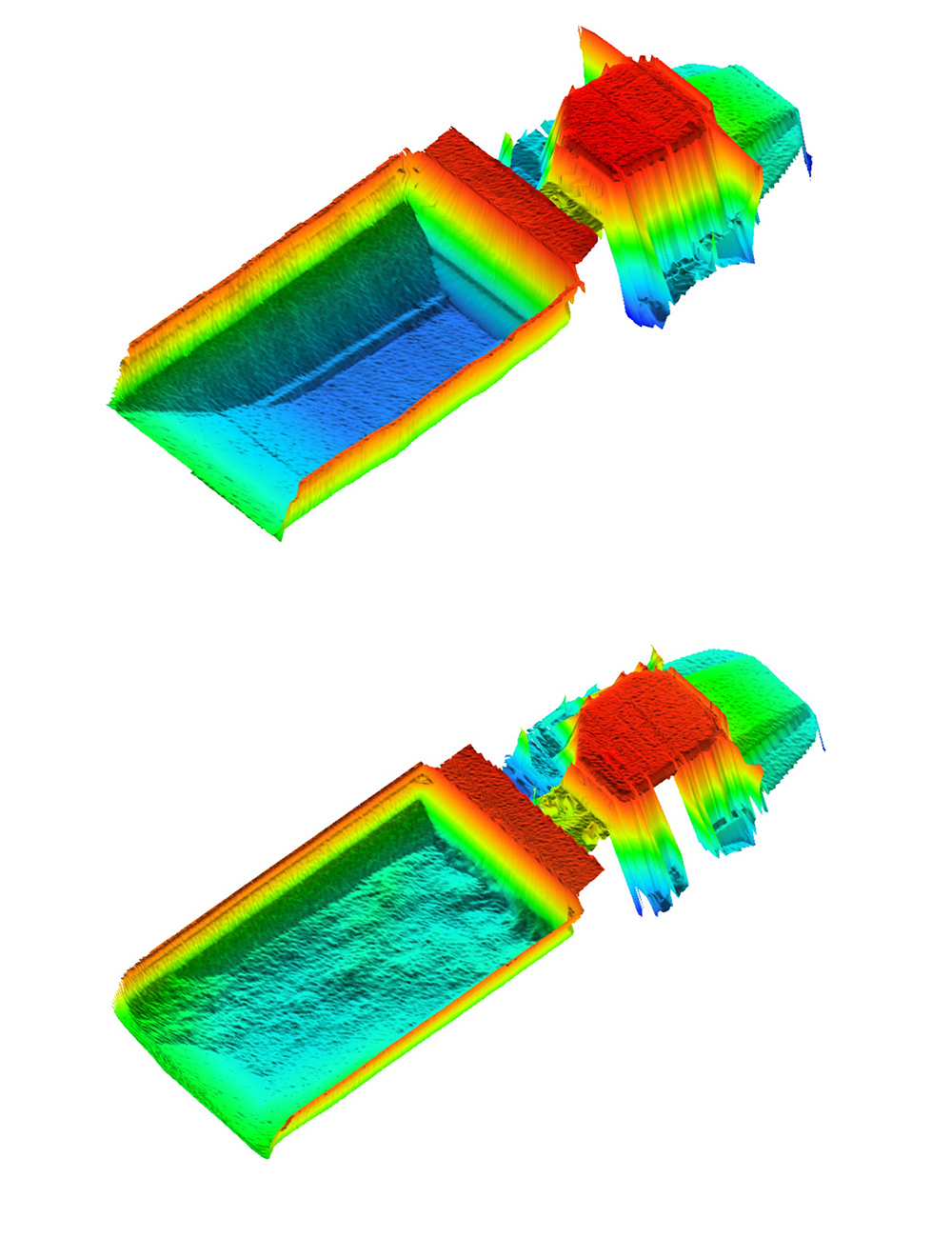
Bottom: Hauler carry-back identified by Loadscan’s innovative LVS system
Terex Trucks is also now benefiting from the use of a fault analysis tool. If a fault is found during final inspections, the fault is plugged into the analysis tool so the system can support the inspection team by helping them to identify what further checks to make. It also advises on potential solutions by looking at other logged instances of how the same fault was rectified previously. All of this helps to contribute to and drive a superior quality product from the manufacturer.
Rodney Aggregates Supplies (Rodney Aggregates) has been using a Loadscan load volume scanner (LVS) in its Whangaripo Quarry north-east of Warkworth, New Zealand, to minimise profit loss due to carry-back on their overburden stripping programmes.
Daniel Le Roux, business manager at Rodney Aggregates, says: “The scanner was measuring significant amounts of carry-back by the contractor, especially this season where the material was sticky and wet compared to previous years. This was often up to 5mᶾ per load, which on some trucks is 20-25% carry-back — obviously a huge saving for us.”
The Whangaripo Quarry is a regular supplier of high-quality greywacke products (asphalt and concrete aggregates through to base courses and bulk fill) to the North Auckland region.
They strip up to 2,500mᶾ of overburden material a day and if Rodney wasn’t using the Loadscan LVS the company wouldn’t be aware of the carry-back in the truck bins, which influences the final payments to the contractor. In the years that the firm used the surveyed volumes compared with truck load count, carry-back was never considered although it was present, therefore there was a discrepancy between survey and truck count volumes. In terms of financial cost, if 20% of a truck load is haul-back then the business suffers a $3,250 per day cost for material not hauled. Over their six-day working week that’s $19,500.
Hypothetically, if the LVS unit has a conservative lifespan of five years (though being a touchless system with no wear parts it’s proven to last much longer!) that’s a saving of $4,875,000 in carry-back alone.
Loadscan’s LVS system utilises laser scanning combined with proprietary software that creates 3D model images of trucks to measure the exact volume of material loaded in a truck or trailer bin. Every system includes an RFID reader for the automatic identification of each vehicle, every load.
Not only does an LVS system enable proper management of loading and carry-back, having highly accurate measurement of every load also gives users an auditable trail of transparent data.
For Rodney Aggregates that data has eased invoicing tensions. Le Roux says: “In the past we used to rely on an aerial survey to calculate volumes moved. This meant that during the season the payments/measures were based on load counts and the final payment was sorted at the end of the season after completing the final flyover. There were usually arguments over final amounts, so final payment was often agreed up to three months after completion of the works.”
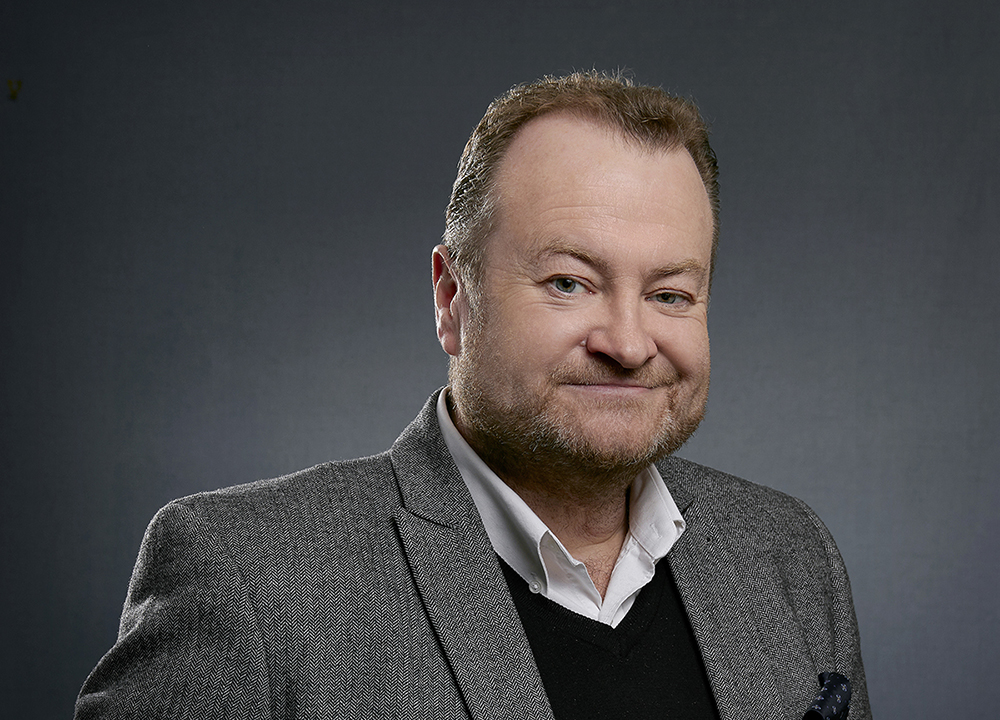
Loadscan’s LVS system is completed by a load-management reporting system called Overview. Overview provides Rodney Aggregates with the full picture of material movements on-the-fly. The firm is now equipped with the real-time actionable intelligence to monitor exactly how much product has been stripped by its earthworks’ contractor.
Le Roux says: “Another great benefit is having the data of loads/volumes real-time in front of me. It makes monthly payments accurate and reliable — no arguing with the contractor on volumes moved.”
The LVS model used by Rodney Aggregates is Loadscan’s mobile truck-scanning solution (LVS-3TMM). The fully self-contained mobile truck-measurement unit is driven to site and fully set up and operational in as little as 45 minutes. There are a range of power options, plus the ability to transmit truck-measurement load reports via Wi-Fi, cellular modem or network cable.
The scanner, with extended rigger, is set up to measure the 40-tonne articulated dumpers removing overburden from the quarry. Rodney Aggregates’ LVS is equipped with a built-in kiosk so that it’s fully self-contained. Overview reporting software is used to process and sort scan data and to generate custom load reports. And the office is equipped with LVS remote control functionality via network cable/WiFi/cellular modem.
Liebherr has been carrying out rigorous semi-autonomous testing of a trio of pre series next-generation TA 230 articulated haulers on the state-of-the-art site test track at its facility in Kirchdorf an der Iller, Germany.
The German construction and quarrying equipment giant put its new 30-ton (27-tonne) model, due to come on to the global market in April 2020, through its paces during the company’s annual International Construction Trade Press Information Tour on 24-25 October 2019. The well-attended event was co-hosted at the Kirchdorf an der Iller site and Liebherr’s facility in Nenzing, Austria.
During a press conference, Liebherr revealed that the TA 230 would be one of a three-strong new articulated hauler series. The company plans to unveil its new 40-ton (36-tonne) and 45-ton (41-tonne) machines at the 2022 edition of the bauma exhibition in Munich.
Aggregates Business readers can read in more detail about the next-generation Liebherr TA 230 articulated hauler in the January-February 2020 editions of ABE and ABI.