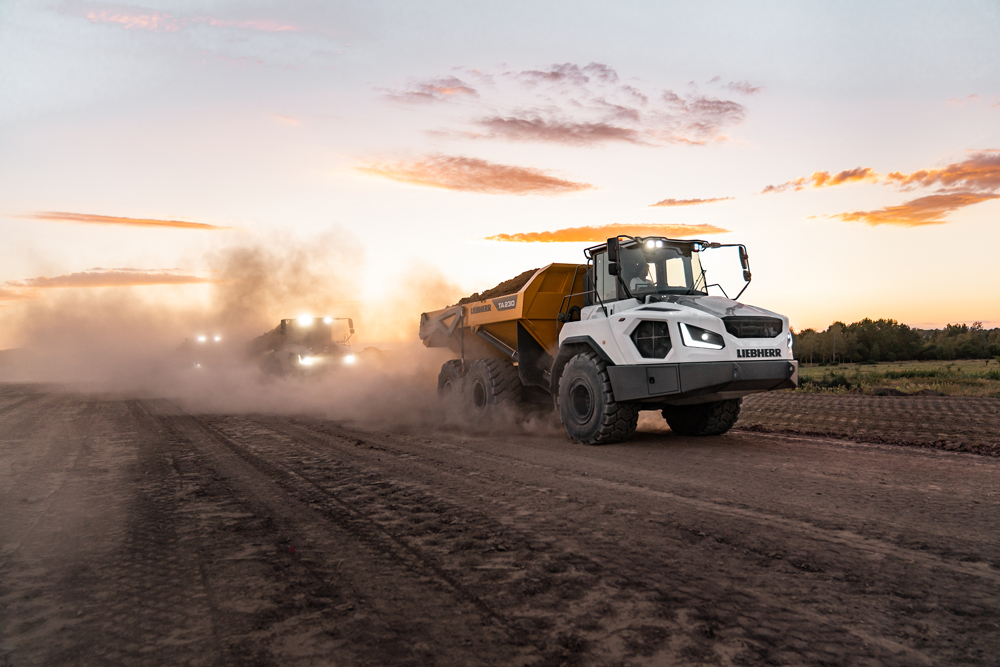
Liebherr has launched the TA 230 Litronic articulated dump truck (ADT) which the German manufacturer says means it now provides a full line of earthmoving equipment. The new TA 230 Litronic, which was unveiled in a digital presentation, is primarily designed for overburden transport, the mining industry, and larger infrastructure projects. Its optimal structure gauge means it can also be used for special applications such as tunnel construction.
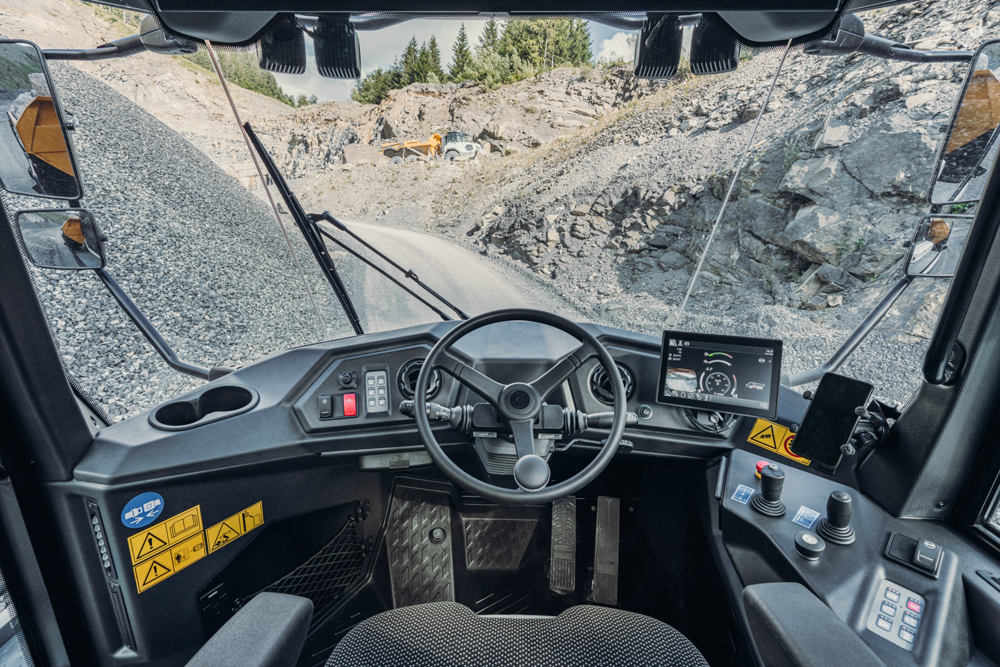
The TA 230 Litronic features a newly designed front-end area, creating maximum ground clearance for performance in challenging off-road environments. For example, the powershift transmission is positioned safely and compactly under the operator’s cab. In addition, the exhaust gas after-treatment is safely installed behind the operator’s cab in a space-saving manner, whereby a large slope angle could be generated.
The newly designed, solid articulated swivel joint creates excellent off-road capability and allows independent movements of front and rear end to enable maximum manoeuvrability. The robust and positive-locking swivel joint with tapered roller bearing is suitable to meet the shear stresses arising during use, withstand maximum loads and provide optimal force distribution.
The front and rear axles of the machine are secured via sturdy A-rods at the articulated swivel joint and at the rear end. The focus was placed on maximum ground clearance during the development process. Both the front axle suspension with A-rods and shock absorbers at the articulated swivel joint and the position of the separate and oscillating A-rods of the rear axles at the rear end provide maximum ground clearance.
A powerful 6-cylinder construction machinery engine with 12-litre displacement and 265 kW/360 hp is installed in the new TA 230 Litronic, which complies with Stage V exhaust emissions standards. A robust drivetrain with automatic 8-speed powershift transmission is designed to ensure optimal force distribution.
With the actively controlled longitudinal differential locks, automatic traction control is also available for the TA 230 Litronic. As soon as slip occurs at an axle, the torque is transferred to the axle or axles with traction.
Liebherr says the new dump truck provides enormous pulling force, even in the most difficult ground conditions and on challenging gradients. It adds that maximum safety is guaranteed thanks to optimal adhesion.
The large trough of the new TA 230 Litronic can carry a 28-tonne payload and a range of improvements have been made for quick and efficient loading, unloading and safety. The front of the trough is straight and the sills are low so that loading with a wheeled loader is easily possible across the entire length. A weighing system shows the current payload during the loading process on the display in the operator’s cab. An optional loading light on both sides at the back of the operator’s cab shows the loading level outdoors. To accelerate the release of material during unloading, the inner edges of the new trough are tapered. During transportation the long chute at the end of the trough is designed to ensure minimal material loss. The trough volume can be increased with the optional tailgate.
The newly developed operator’s cab of the TA 230 Litronic features panoramic windows without any struts, in addition to a short and inclined bonnet to ensure the driver always has an optimal view of the driving, working and articulating area of the machine. A touch display with integrated rear camera also increases transparency in the rear area. In the soundproof cab ergonomically arranged control elements facilitate intuitive operation of the machine.
In addition to a hill-start assist, a speed assist is also available. With the hard stop function, the end-position damping of the trough-lifting cylinders can be activated or deactivated by a button. The trough lift is limited for work in a height-critical area with the aid of the height limit.
The TA 230 Litronic also features intelligent machine check-up and a service-oriented machine design. The dump truck automatically performs the daily check itself through the use of sensor technology. The machine runs through an inspection catalogue at the start, where levels of engine oil, coolant, the central lubrication system are checked with any deviations being shown on the display in the operator’s cab.
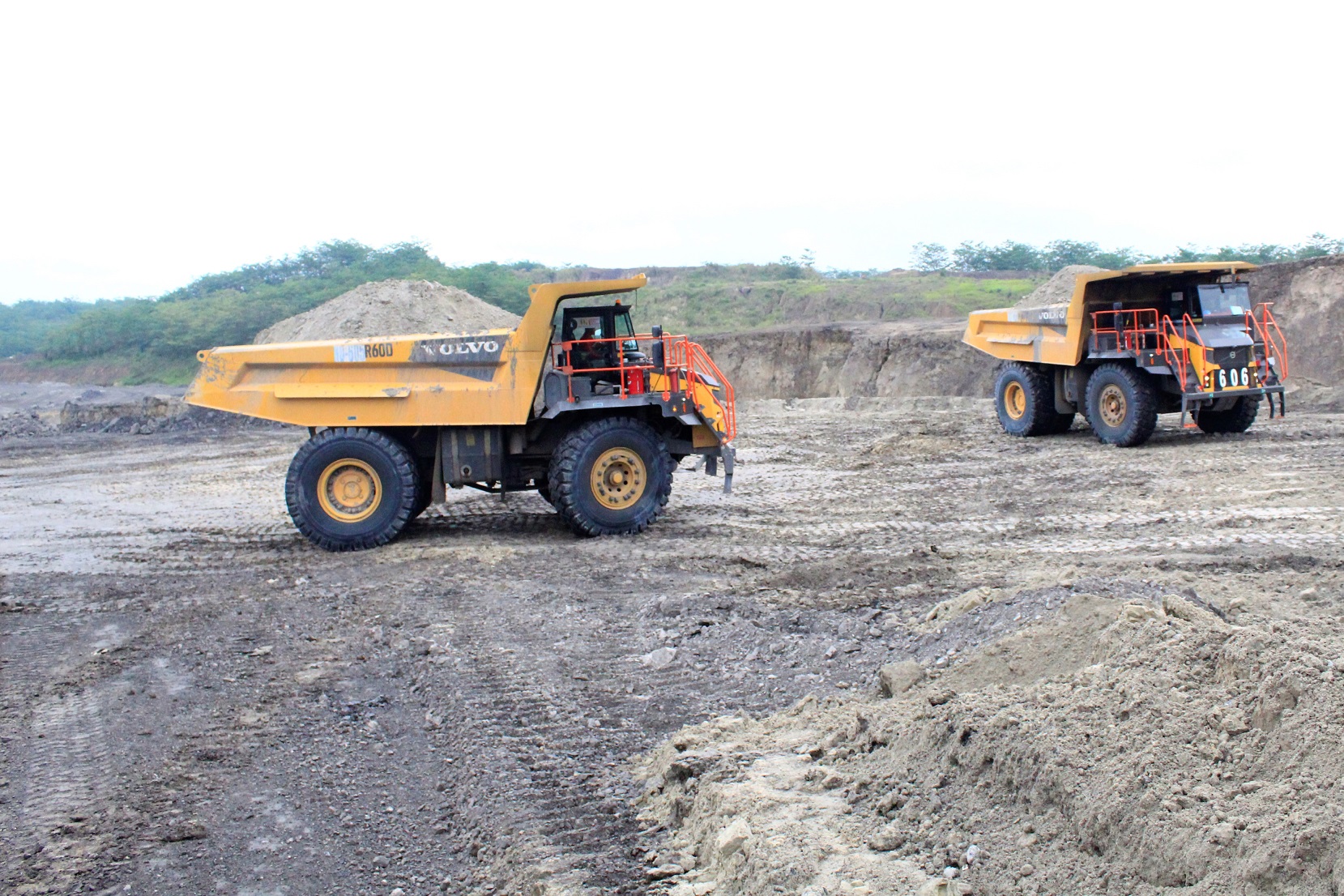
The standard version of the TA 230 Litronic has an empty vehicle weight of 24,600kg, a payload of 28,000kg, a maximum trough capacity with tailgate of 18.1 m³, engine power (ISO 9249) of 265kW/ 360hp, and a maximum driving speed of 57kmph (forward) and 16kmph (reverse).
Indonesia-based PT Manado Karya Anugrah says a fleet of Volvo Construction Equipment (Volvo CE) machines, including 16 haulers, that it has been using since last year is delivering exceptionally profitable operations.
PT Manado Karya Anugrah, a coal mining contractor, has been using the machines since April 2019 at its coal mine in East Kalimantan.
The fleet consists of 10 R60D rigid haulers, six A40G articulated haulers and three EC750DL excavators and PT Manado says the machines are proving profitable due to their high productivity and uptime.
“Conditions at our site are tough and we know we can count on the productivity and reliability of Volvo machines to give us the lowest cost per tonne,” said Rafiuddin Djamir, owner of PT Manado Karya Anugrah.
The site has medium to high gradients with limited room for manoeuvring, and the Volvo CE rigid and articulated haulers have proved efficient in dealing with the slopes.
“Our operators particularly like the speed of the machines during a climb,” said Djamir. “They feel the machines have more power than others.”
The machines provide a high level of uptime and work 22 hours per day in two shifts, seven days a week. “The Volvos have a high availability for work, and we appreciate the machine features and dealer support behind this advantage,” Djamir said.
The fleet is served by PT Indotruck Utama, Volvo CE’s distribution partner in Indonesia. “So far there have only been a few minor issues but with the total support and quick response from our dealer, the problems were fixed immediately,” said Djamir.
PT Manado Karya Anugrah, which stockpiles ore at its gold mine in South Sulawesi, also owns Volvo L260H wheeled loaders.
Since Volvo Group acquired the off-highway truck product line from Terex Corporation in 2014 and formed Terex Trucks as a division of Volvo Construction Equipment, the Swedish manufacturing giant has invested around £35m in transforming the Scotland-based company’s articulated dump trucks. The investment over the last six years has seen substantial improvements to the quality and performance of the Terex Trucks TA400 and TA300 ADTs, as well as heavily investing both in the factory at Motherwell and in systems, employees, distribution network and aftermarket services.
Volvo CE has also committed to spend a further £10m-plus on improvements over the next two years, reinforcing its commitment to the Terex Trucks operation.
In 2014, Volvo CE took the long hauling heritage and product knowledge of Terex Trucks and combined it with its expertise, experience and financial backing to start an ongoing product renewal programme which has seen the launch of a new generation of Terex Trucks ADTs.
One of the key changes is a new drop-box on the TA400 – which now has heavier-duty parts as well as better lubrication lines and materials to improve durability. It also has two-stage gearing for tailored performance in all haul conditions, whether the operator’s requirement is for severe traction or high speed. There is also a new transmission on the TA300 with eight forward gears and four reverse gears, which is designed to help deliver a 5% improvement in fuel efficiency, a 5 km/h increase in speed to 55 km/h, an extended 4,000 hours oil change period and enhanced performance when compared with the previous model.
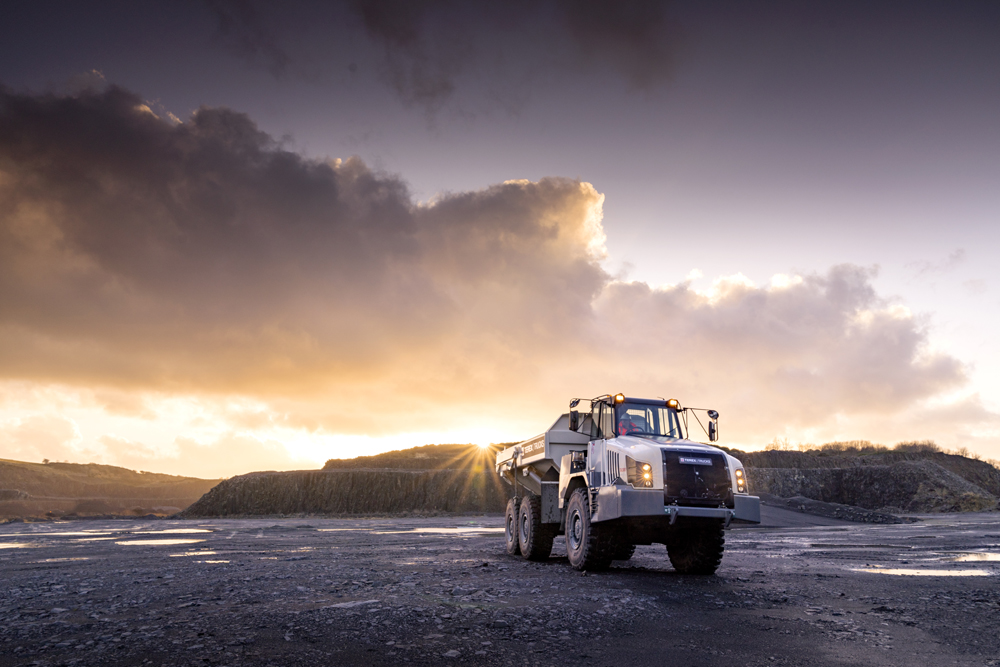
The hydraulic system on the trucks has also been upgraded – magnetic suction filters reduce the risk of component failure from environmental contamination, while improved over-pivot hose routing boosts performance in severe working conditions. Steering cylinder cushioning has been improved, with the intention of making operators more comfortable and reducing stress on components. Hydraulic oil replacement intervals have also been extended to 4,000 hours, with the TA400 transmission oil change now at 6,000 hours, helping to reduce operating costs.
Work has also been done to enhance life for the operator, with upgraded instrumentation, controls, layout, cab-sealing, heat-shielding and a high-performing HVAC (heating, ventilation and air conditioning) system – all increasing operator comfort, safety and productivity. Additionally, the introduction of telematics is helping owners to protect their trucks by monitoring location, performance, productivity and maintenance needs.
“Because the articulated dump truck is the only product Terex Trucks develops, we’re able to focus all our attention on this machine – and that’s exactly what we’ve been doing over the last few years,” said Paul Douglas, MD of Terex Trucks. “We’ve listened to our customers and, with the help of their feedback, they are now reaping the rewards of these investments and enjoying lower operational costs, higher uptime levels, fuel efficiency savings, extended service intervals, faster fault detection, top-quality customer service and industry-leading parts availability.”
Since the Volvo CE takeover, improvements have also been made at the Terex Trucks production site. New tooling and machinery include large welding robots, computer programmed CNC (computer numerical control) machines and heat-treatment capabilities, while factory enhancements include new work compartments segregating key areas, re-laid floors and a new LED lighting system.
Since the end of last year, Terex Trucks has been working with the Molson Group – the UK’s largest distributor of capital equipment – to strengthen its presence and reinforce its commitment to customers.
“Our partnership with the Molson Group is a big benefit to our customers,” said Douglas. “They are an experienced dealer with a strong reputation for service and support and they have a 360-degree product offering, meaning that customers can now buy our trucks together with complementary machines, such as excavators, from a single source.”