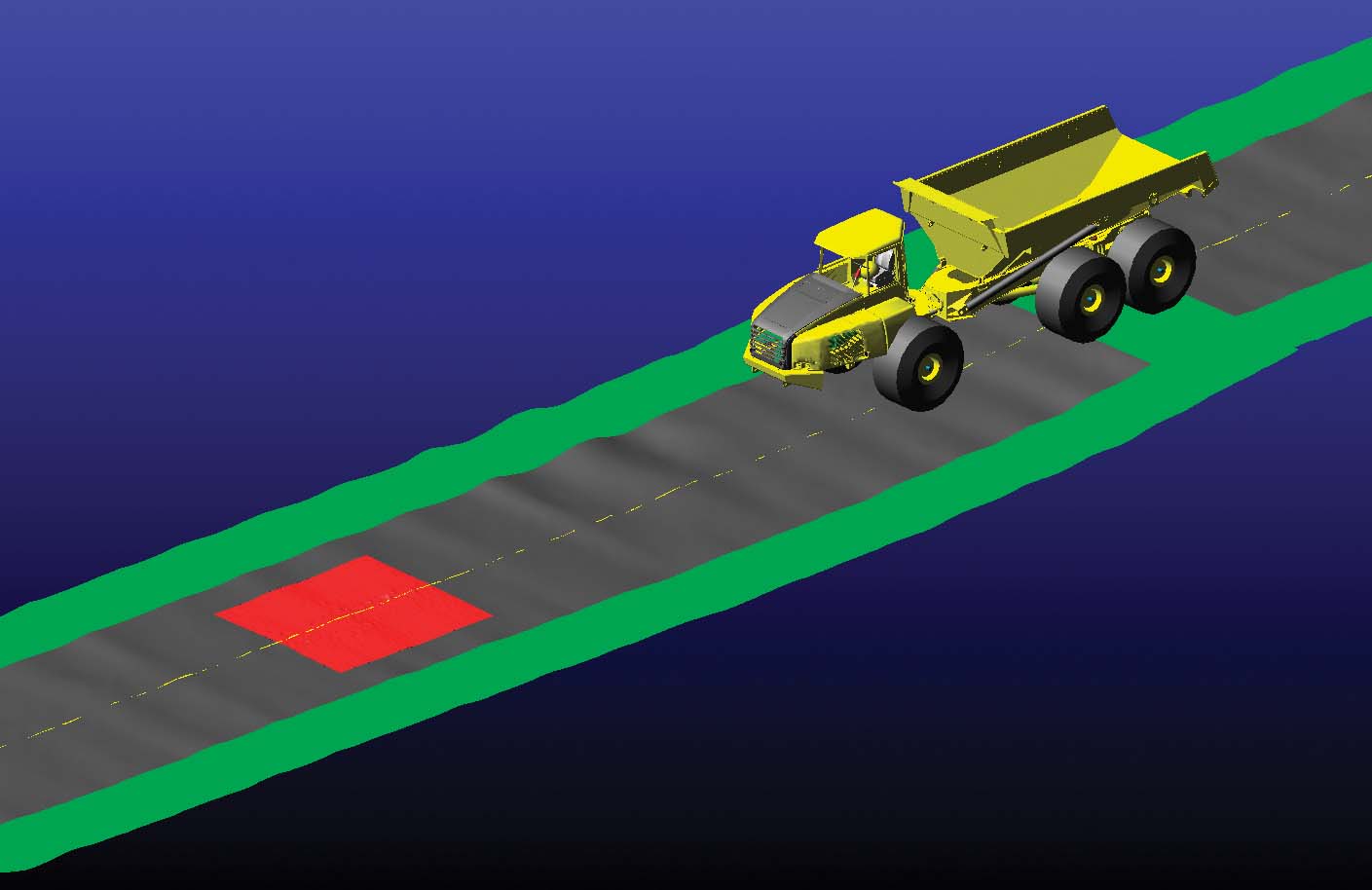
Building prototype machines involves a lot of time and resources, so engineers at Volvo Construction Equipment’s Technology Function are developing new methods to increase the amount of virtual testing and simulation that can be conducted before the first prototype is built.
The company says this shortens the development cycle and ensures that when prototypes are built they are much closer to the final product, thus reducing costs.
Virtual testing and simulation is not new to
However, a recent breakthrough by the engineers is allowing more early stage simulation than ever before. Until now the structure and dynamics team required a prototype to test the strength of machine components such as frames. Now, the early simulation team can use computers and simulation to provide the structure and dynamics team with the forces they need to analyse structural integrity and performance.
This allows the team to establish how strong parts need to be one year earlier than was previously the case, all before any money is spent building prototypes.
Currently this method can only be applied to Volvo CE’s articulated haulers, but the company’s engineers plan to adapt the technology for use on all Volvo CE machines.
“If an articulated hauler is working on an uneven road and the wheel hits a bump, forces are created in the hauler and distributed from the tyre to the framework,” says Lennarth Zander, manager of the VPD team.
“Through simulation and mathematical calculations we can accurately measure this force which allows the structure and dynamics team to determine structural response and the required strength of parts. Previously this was established with a prototype on a test track but now we can achieve the same results faster using a computer. We have created an accurate 3D model of an articulated hauler in the computer which is equipped with everything the real machine has. The movements, such as braking and turning, are exactly the same: watching the animated 3D machine is like watching a movie.”
Another advantage of this technology is said to be that virtual measurements can be taken in locations where it is not possible to do physical measurements. For example, there is not room for a physical sensor in confined areas, such as on a bolt, but now forces in these places can be measured via simulation. The simulation model can also be used to determine how the machine would behave in different environments, from freezing temperatures to the blistering heat and at high altitudes where there is much less oxygen in the air.
“It’s becoming increasingly important to shorten the development cycle and use computers to carry out as much virtual testing and simulation as possible,” says Zander.
“With this new Volvo CE technology we will increase efficiency and enhance the product development process without compromising accuracy, and that’s a big breakthrough. In the future we should be able to skip early prototypes and build a more mature model with a higher level of accuracy that’s much closer to the final machine, saving both time and money.”
Crack-free concrete mix
Civil engineers at the University of Wisconsin-Milwaukee (UMW), USA, have developed a concrete mix that could leave roads and bridges free of major cracks for up to 120 years.
The mix, superhydrophobic engineered cementitious composite (SECC), contains unwoven polyvinyl alcohol fibres, each the width of a human hair, which are strong enough to let the concrete bend without breaking.
If normally porous concrete does not absorb water, liquid cannot get inside, freeze and cause it to crack. The concrete's unusual characteristics means that cracks that do form do not propagate and cause failure.
“Our architecture allows the material to withstand four times the compression with 200 times the ductility of traditional concrete,” says Associate Professor Konstantin Sobolev, whose laboratory created SECC.
The engineers doped their mix with superhydrophobic additives based on siloxane, a compound that forms the backbone of silicones, mixed with superfine powders. Together, these form a microscopic spiky surface nearly impermeable to water.
A test slab, embedded with sensors, was laid in August 2013 and the team is now analysing whether the SECC it installed shows the performance improvement seen in the laboratory.