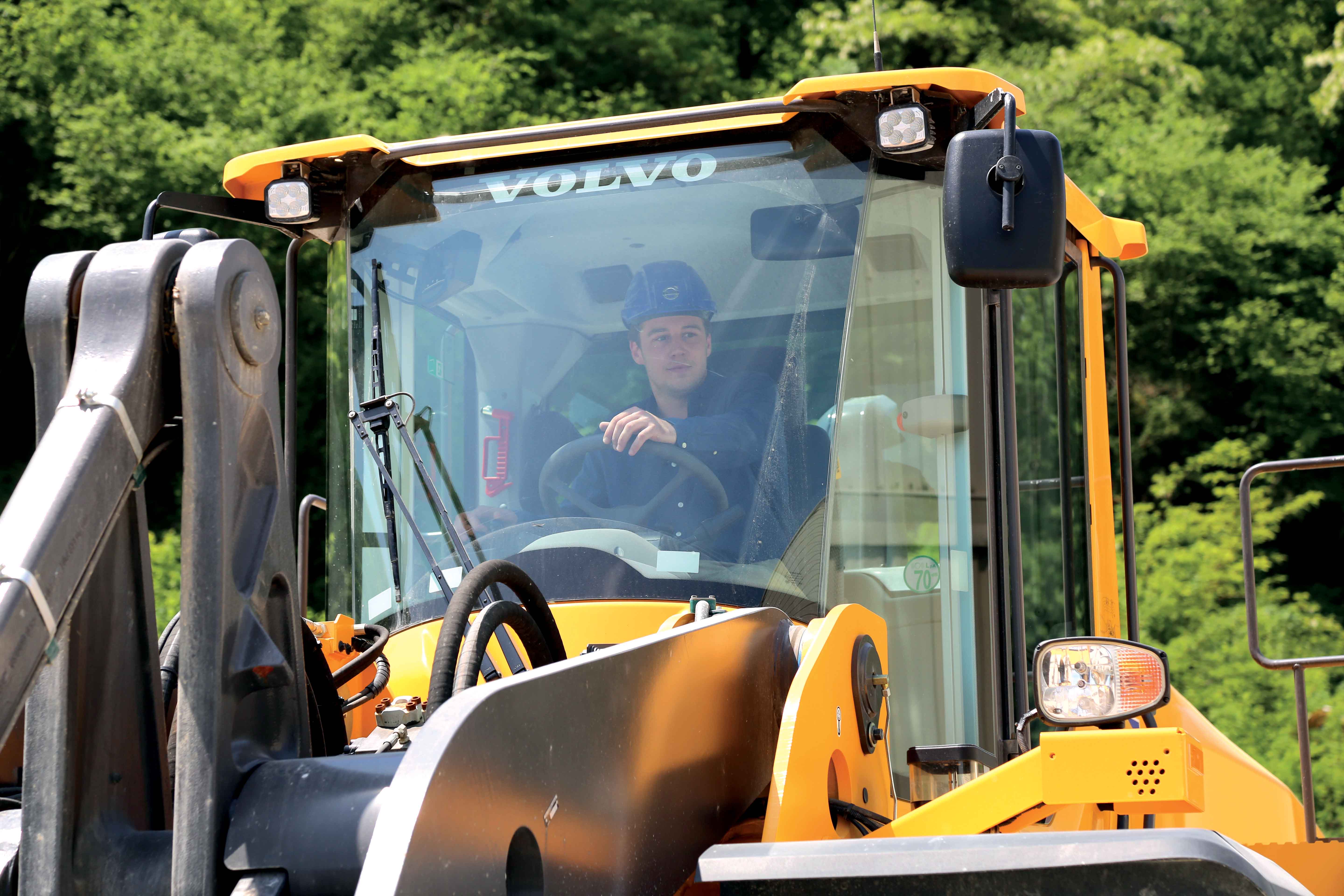
A pair of L220 wheeled loaders from Volvo Construction Equipment are proving up to the delicate task of transporting huge blocks of marble for a family quarrying business in the French Pyrenees. Guy Woodford reports
Joseph Laplace was in London recently and was delighted to see the marble decorating the facades of boutiques in Piccadilly as coming from the Arudy quarries in the French Pyrenees, where his family has mined for generations.
The Tokyo showroom of French fashion giant Hermes also boasts marble from Arudy, as do the Dutch Council of State building in The Hague and the entrance hall to the Mandarin Hotel in Paris. It adorns the columns of the Place de la Concorde, the French capital’s largest public square. Closer to home, Arudy marble also graces altars at the shrine of Lourdes, a major Catholic pilgrimage site since the mid-19th century, visited by millions of people every year.
These are just a few of the many destinations for Arudy marble, its quality having long enhanced the reputation of both the region and of France across the world.
An exceedingly dense and shatterproof material, marble resists frost and can last for thousands of years.
“Each deposit has its own identity and nuances, rather like a signature,” says Laplace, whose grandfather started mining marble deep in the forests of the Pyrenees in 1929. Experts like him are able to recognise the origins of a specific marble at a glance, each one characterised by its individual colour, swirls and veins. “It is a noble substance,” he declares.
The three Laplace quarries – Sainte-Anne, Henri IV and Paloma – are renowned for their grey marble, currently in both fashion and demand. The colour and patterns of the marble cut from each quarry are distinctive, of different shades to each other and with distinguishing markings.
Nestled against the Pyrenees, the marble quarries of Arudy were opened in the 1800s and once provided employment for hundreds of people. In the 1950s, there were still 20 active quarries, but the industry has slowly declined over the years. Laplace, along with his son Pierre and a workforce of nine, each with their own specialty, is one of the few still excavating these deposits of natural stone.
Pierre Laplace, 27, the fourth generation of his family to go into the business, handed down from father to son, explains that choosing the raw material is an artisanal skill and needs a good eye, which comes from experience.
The stone is extracted from the quarry in three stages – first cut horizontally with a diamond wire saw that makes the most of any natural fault lines, so that as little as possible of the material is lost. The second stage involves cutting the marble vertically, leaving a giant cube of stone. This slab is washed and smaller blocks of different shapes and sizes are cut according to colour and direction of the grain.
The Laplace family bought their first wheeled loader, a
“The type of work they do is very demanding,” says Hawryliszyn. The Volvo L220 wheeled loaders transport huge blocks of marble from the quarries to a storage area; from here the blocks are loaded on trucks to be taken to their next destination. The versatile wheeled loaders are also used to tidy the quarries and keep them clear of debris.
Pierre Laplace says they opted for Volvo again because the machines suit the specialist aspect of their work. Thanks to the machine’s high lifting capacity and parallel lift arm, the blocks are always positioned horizontally, which significantly increases safety during transport. The machine’s compact proportions work to advantage in the confines of the quarries. Low fuel consumption was also taken into consideration.
“It is vital that the blocks of marble don’t get damaged during transport, and the Volvo machines are very well adapted to this kind of work,” he says. “It is important to be able to see clearly what we are doing from the cabin. We need to be able to see the end of the fork at all times and have continuous good visibility.”
A machine operator himself, he adds that the new machine is comfortable and feels secure. “It is also very quiet,” he says. “The minute the operator is in the cabin he can hardly hear the motor and can really concentrate on his work.”
The quarries are quiet and peaceful, situated as they are within a protected area of outstanding natural beauty and subject to stiff environmental regulations to do with noise and pollution – an element that makes it increasingly difficult, but not impossible, to compete with marble produced in less regulated parts of the world.
Most of the marble mined by the Laplace family is transported for export worldwide, much of it via Carrara in Italy. The US is a voracious market, and Arudy marble is also popular in Italy, Japan and China, although the end-users for the Laplace product tend to opt for quality over quantity. Put into service both inside and out, it is destined for the facades of buildings, for kitchens and bathrooms, crafted into floors and staircases, chimney-pieces and tombstones, statues and monuments – its uses are endless and its longevity assured.
The Volvo L220H wheeled loader
The Volvo L220H wheeled loader has an operating weight of 31.2-33.1tonnes. Fitted with a Volvo D13J Tier 4 Final/Stage IV compliant engine, the model has an impressive 2.7m³-9.5m³ bucket capacity with its tipping load at full turn coming in at just under 21tonnes. Along with its fellow H series wheeled loader models, the L150H and L180H, the L220H has a titling cab that can be tilted at either 30° or 70° for better service and maintenance access. Crucially, this leads to more uptime and increased machine availability. The H series’ cabs also feature ergonomically placed controls, low internal noise levels, vibration protection and ample storage space.
The L220H is equipped with a Boom Suspension System (BSS) said by Volvo to improve productivity by up to 20% by absorbing shock and reducing the bouncing and bucket spillage that occurs during work at speed on rough ground.