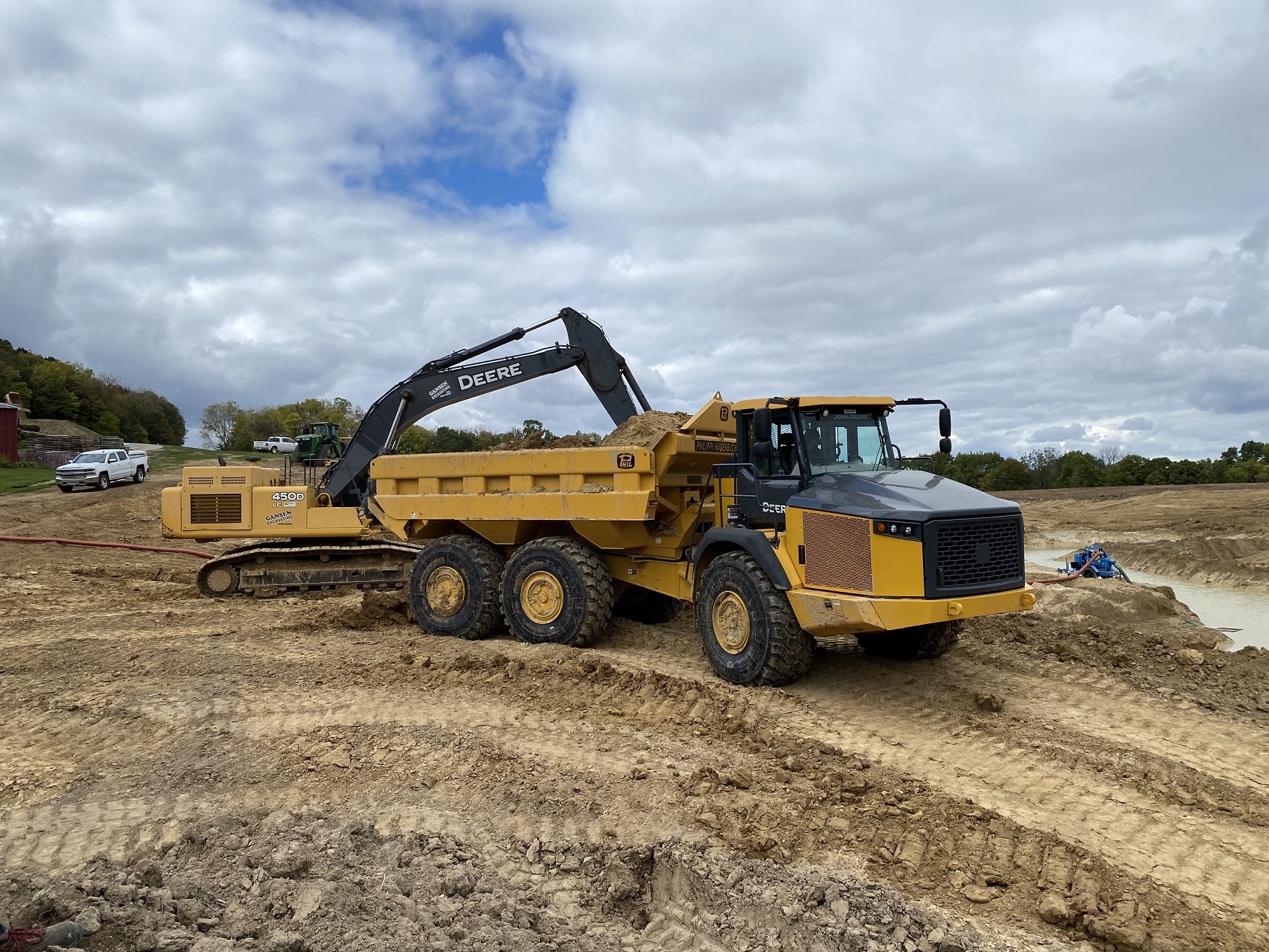
Philippi-Hagenbuch, Inc. is now offering in-stock inventory of its most popular sizes of rear eject bodies. In most cases, this reduces the rear eject lead time for 35- to 45-ton truck models to six weeks or less.
Over the past 23 years, Philippi-Hagenbuch has manufactured hundreds of rear eject truck bodies to help customers increase their productivity, safety and stability for off-highway operations. Rear ejects are engineered and manufactured to fit the specific truck body chassis. They are easy to operate in the cab, reducing dumping and spreading time by eliminating the need to stop and raise the truck body. Various industries, including general construction, aggregates and mining, use rear eject bodies and trailers to significantly improve their productivity when dispensing material and overcoming situations where overhead barriers inhibit traditional dump bodies.
"We are dedicated to offering our clients the equipment they need, tailored to increase the productivity of their specific haul trucks," said Josh Swank, Philippi-Hagenbuch vice president of sales and marketing. "We remain committed to offering customised solutions for our customers, including our rear eject product line. However, we have found that the majority of our rear eject bodies are for 35- to 45-ton trucks, and we can now offer a faster turnaround time for those customers by maintaining an inventory of our most common models. This is especially beneficial with many of our clients facing the current supply chain and lead time challenges."
Philippi-Hagenbuch continues to custom engineer and build rear eject bodies and trailers for various makes and models of off-highway trucks to provide solutions for each customer's unique needs. Beyond its in-stock sizes, the company manufactures rear ejects that can fit 25- to 60-ton haul trucks. The rear eject bodies are manufactured exclusively with high strength, abrasion-resistant Hardox 450 steel for the greatest structural strength and durability.
Due to their all-Hardox construction, which PHIL made as a commitment through SSAB's 'Hardox In My Body' campaign, PHIL's rear ejects are proven to last up to 20 years and are often put on a second truck after the first chassis has worn out.
"Over the last few years, we have made it a priority to evolve and update our rear ejects based on feedback to offer an even better product for our clients," said Swank. "We had a vision to further develop not only the operation of both the ejector blade and the rear tailgate mechanism but to reduce the number of parts, evolving the track design to strengthen the body sides and to decrease the need for maintenance or replacement."
Philippi-Hagenbuch upgraded its rear eject design with a single, newly-engineered, three-stage, double-acting hydraulic cylinder that is robust enough to keep the rear ejects operating in extreme cold or in equatorial warm-weather locations. This cylinder has been specifically designed for horizontal movement. It will not buckle or bind as it is fully extended while operating in the dynamic environments where the rear ejects will be used.
Operations can effectively and safely dump material with a rear eject even when a truck is out of position, driving up a hill or under overhead barriers with low clearance, such as power lines, roof lines, pipelines or bridges. Additionally, the ejector blade of a rear eject pushes material toward the rear of the truck while the tailgate mechanically lowers down, and material is completely ejected. When trucks may be travelling on soft surfaces, rear ejects offer a constantly low centre of gravity and stabilisation. This effective dumping action eliminates further downtime and significantly increases jobsite safety and productivity.
"We envision the use of our rear ejects to remain and grow as an important part of the construction, aggregate, mining, refuse and scrap steel handling landscapes as they offer more safety and efficiency to any operation," said Swank. "With many developments in our rear eject product line over the last three decades, Philippi-Hagenbuch is excited to continue that growth and consistently set the standard in providing custom hauling solutions for our clients and revolutionise the way work is done."