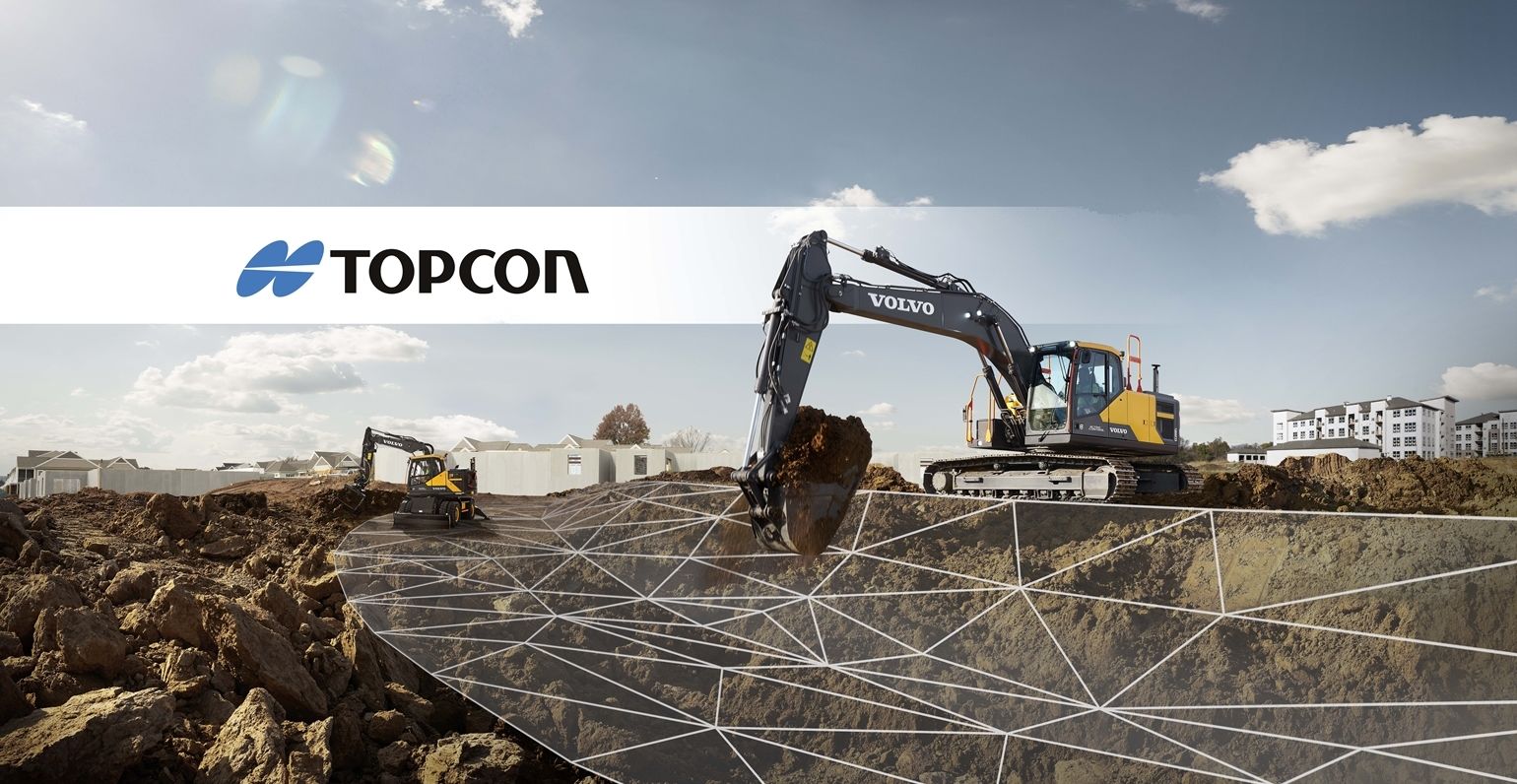
The Active Control function of the Dig Assist suite is designed to help operators of all skill levels by automating the digging process. Volvo CE says that integrating Active Control with Topcon's 3D-MC positioning systems will enable an abundance of new and more complex projects to be possible.
For Volvo customers in Europe, Oceania and Asia, Volvo Active Control is currently available on the Volvo EC220E, EC250E, EC300E and EC350E Crawler Excavators. For customers in North America, it is offered on three models, the EC220E, EC250E and EC300E. Volvo Active Control will be extended to additional models in 2022.
Volvo CE says that Japan-headquartered Topcon’s software seamlessly integrates with the Active Control menus, allowing operators to quickly customise how they want “Autos” to function - whether for digging trenches, grading slopes or creating site profiles.
The Swedish manufacturer adds that 3D software is the ideal choice for complex and larger infrastructure projects, providing more detailed, realistic visualisations and helping to improve efficiency and reduce costly errors. The latest updates to Topcon 3D-MC for Volvo include over-the-air access to Sitelink3D, support for LandXML files, a refreshed graphical user interface and an over-the-air remote support function.
The latest version of Volvo Active Control software supports auto-tilt feature for tilt buckets and Steelwrist tiltrotators, as well as a return-to-dig feature called Bucket Recall, and automated back grading. First introduced in 2019, this steer-by-wire machine control system guides the operator through functions to automate the digging process, producing results that are claimed to be up to 45% faster than traditional grading.
When using the Boundary Limits package, operators can automatically stop the swing motion at a set angle to assist in digging and truck loading. If working in a tight space, operators can pre-set boom and bucket elevation and swing to avoid side or overhead obstacles.