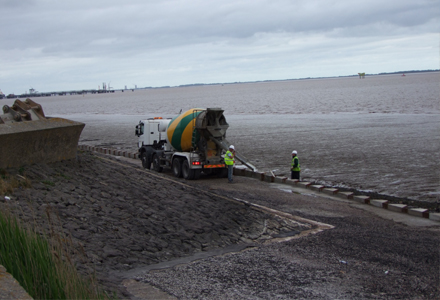
Coastal defence work is a race against the changing tides, requiring heavyweight engineering answers and on-site technical support, as well as high quality materials
Rising sea levels mean that coastal defence schemes are becoming increasingly important to many seaside towns and villages. While the technology to track the rate of change in sea levels is advancing, so are the materials to provide the engineering solutions.
In the UK, a £7.7million (€8.9million) project is underway to protect up to 10,500 people from the North Sea and is using hi-tech materials to not only provide long term protection, but also to speed up work on site.
Led by the
Stallingborough is the first of the five schemes and will see the replacement of 1.6km of aging flood wall protection on the shoreline between Grimsby and Immingham Docks, North East Lincolnshire. Central to the Stallingborough project is 3,000m3 of
Birse Coastal and Tarmac previously worked together on sea defence schemes in Blackpool. For the Stallingborough scheme, Birse has specified Topforce, a high strength, fibre-reinforced concrete, ideally suited to coastal defence work. According to Birse Coastal site agent Alan Smith, the product is already proving its worth.
"Typically, mesh fabric is used on sea wall defence schemes, but the macro-synthetic fibres within Topforce have allowed us to reduce the use of steel mesh fabric on the overall scheme by around 35%," said Smith. "Mesh can easily get exposed and can quickly corrode, so using a material with added fibre is beneficial."
Saving time was a key consideration of Birse Coastal's product specification decisions. "Every day we are working against nature's clock and only have a six hour tidal window in which to operate. Using Topforce has delivered both cost and time savings, because using mesh fabric typically requires significant onsite preparation time. I believe we are saving around a week compared with the time we would have had to set aside for mesh-based material. We have also found that the concrete delivers an even distribution when discharged," he added.
High technical standards and rigorous testing are vital, both at Tarmac's concrete batching plant in nearby Immingham and on-site to assess the delivered product. This ensures that the product offers the optimum strength and workability that the contractor team requires.
In order to offer long-term strength and durability, the Topforce used at Stallingborough consists of 20mm gravel aggregate from Tarmac's Langford quarry, near Newark, combined with a specialist blend of fibre, Portland cement and ground granulated blast furnace slag.
"We are currently delivering between 30 to 60m3 of concrete a day to site and our technical team conduct regular slump tests as well as taking cube samples of cured concrete to check the product strength," said Tarmac national special products manager James Freeman. "Long-term durability of the sea wall is critical and the concrete has to deliver a strength of over 50N. Because of chlorides in the sea water we have to ensure that the concrete can meet an exposure class of XS3."
The Stallingborough project is set to be completed by October 2009. The next project in the Humber package of works is the replacement of the flood wall at Swinefleet, near Goole. The project team will then move to Halton Marshes, near East Halton, Donna Hook, near North Somercotes and onto a location on the north bank of the Humber.
It is estimated that all five projects within the Humber Estuary Flood Risk Management Strategy will be completed by July 2011.