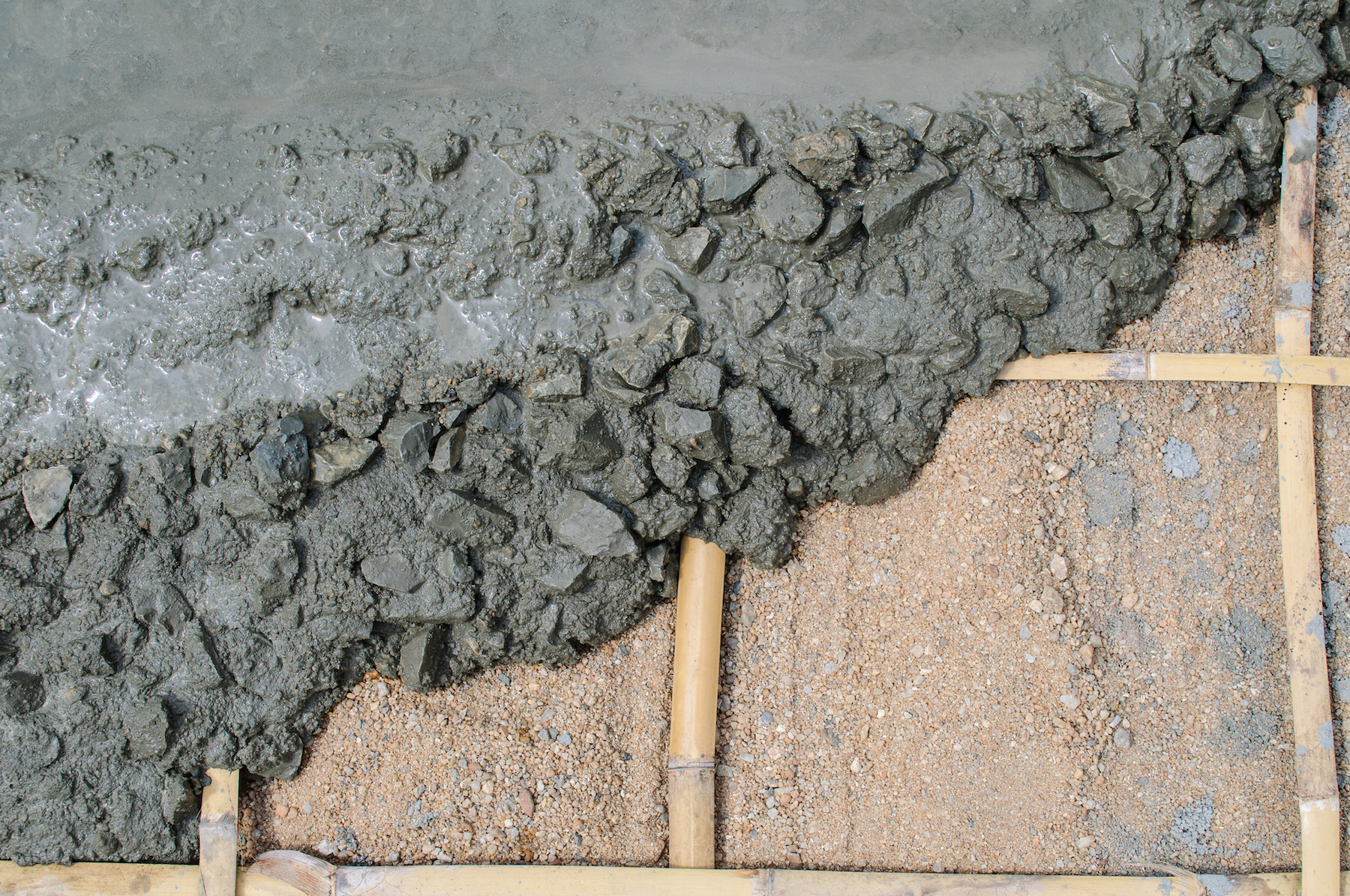
Companies across the quarrying industry are seeking every way possible to reduce carbon emissions. The
Recently, the
It says that as the cement industry’s global database of CO2 emissions and performance, the latest GNR data for 2011 shows that the industry has reduced its specific net CO2 emissions per tonne of cementitious product by 17% since 1990 (from 756kg/tonne to 629kg/tonne).
“Cement is the essential glue to produce concrete and concrete is the most used man-made material in the world, twice as much as the total of all other building materials. The ongoing trend of urbanisation in modern societies contributes to the increase in cement production and growth of the industry,” says CSI in the report.
Having said that, the GNR figures provide evidence of the gradual decoupling of emissions and cement output, which demonstrates the significant progress made by the industry: cement production by GNR companies increased by 74% between 1990 and 2011, absolute CO2 emissions increased by only 44% over this period. Between 2010 and 2011, while cement production volume covered by the GNR increased from 840 million tonnes to 888 million tonnes (cementitious volume), specific net CO2 emissions have in fact decreased from 638kg/tonne to 629kg/tonne of cementitious product.
“GNR demonstrates how an effective measuring, reporting and verification system can be developed and managed for and by an entire industry sector,” says Philippe Fonta, WBCSD (www.wbcsd.org) managing director.
“GNR has become established as a valuable source of independently verified emissions data, which is now used globally by the cement industry to improve energy efficiency and further reduce emissions. It is also accessed widely by policymakers, analysts and other interested stakeholders.”
The 2011 data also now comprises 55% of cement production outside of China, with 96% coverage in Europe spanning 967 individual facilities. Now in its seventh year of publication and the largest global database of its kind, the GNR is a voluntary, independently managed database of CO2 and energy performance information on the global cement industry. The most recent data released is for 2011 in compliance with anti-trust legislation.
The WBCSD provides a forum for its 200 member companies, who represent all business sectors, all continents and a combined revenue of more than US$7 trillion (€5 trillion), to share best practices on sustainable development issues and to develop innovative tools that change the status quo. The council also benefits from a network of 60 national and regional business councils and partner organisations.
A report in Business&Leadership says that
The reports says that Ecocem estimates 600-1,200 new jobs can result from the manufacture of low-carbon concrete for export markets within three to five years.
“The environmental benefits will also be significant. Harmful environmental and health effects of emissions from cement manufacture in Ireland have been independently estimated at €140 million, for 2012,” says the report.
Low-carbon cements could reduce this cost by up to 90%, according to a recent report by Stuttgart University, adds the report.
The move to reduce carbon emissions is also producing some innovative products and ideas, many from the large companies.
However, according to The New Indian Express, Trinity College, attached to the University of Dublin in Ireland, will soon collaborate with the VIT University, Vellore, Tamilnadu, to promote research on eco-friendly concrete technology.
“I am impressed with the research output, faculty and the laboratory facilities at VIT in the field of concrete technology,” said Dr Roger P West, associate professor at the Department of Civil, Structural and Environmental Engineering at Trinity College.
He is reported in the paper as saying a joint research programme with the Indian Institute of Technology Delhi had already been initiated recently, where a team of students and faculties has started working on developing bamboo reinforced concrete technology for building houses in collaboration with Trinity College.
The technology involves replacing carbon footprint-producing steel with bamboos and binding them using epoxy glues to cut down on the cost.
“With Indian collaboration, we are exploring the possibility of extending this technology to build two to three-storey buildings that would long last,” added Dr West in the report.
Since India is blessed with bamboo in abundance, its application in building technology would be appropriate and would cut down carbon footprint to a large extent. In Ireland, 30% of houses were built using timber-based concrete structures. While the bamboo technology could not be used in Ireland, its expertise in this field could be shared.