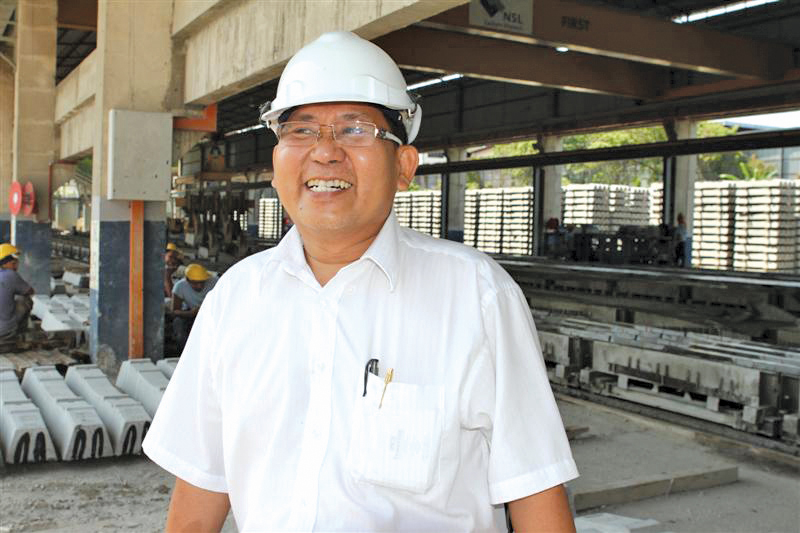
Concrete is the most widely used construction material in the world and after water is the most widely used material of any kind. Western economies have used it for years and developing countries now have an insatiable demand for it as they build infrastructure. Patrick Smith reports
Produced ready-mixed and fresh, for sale to contractors; for the production of precast elements in factories or on site; concrete has many assets.
For example, it has a life span often over a century; it can be recycled into road materials or new concrete while concrete’s thermal mass can cool buildings in the summer and make them warmer in the winter, reducing energy needed for heating and cooling.
However, while the raw materials required for mixing concrete are readily available in many countries, in some they are not. Those lacking materials such as cement are making efforts to address this by importing the material or opening plants to produce it.
The growth in the construction market worldwide is giving rise to a surge in demand for concrete products, concrete pipes and shafts as well as precast components.
This demand is in turn boosting developments among the manufacturers of the machinery and plant that is used to produce these components, say the organisers of
The German Engineering Federation (
For 2012, the federation predicted 5% growth in sales in both building materials machinery and construction machinery.
A recent survey of selected German building materials machinery manufacturers, carried out by the Weimar-based Institute for Applied Research in Building (IAB – Institut für Angewandte Bauforschung), revealed that sales growth is expected to come in particular in the markets abroad. Demand was especially strong, it noted, in the emerging markets: China, India, certain countries in Eastern Europe and some of the former Soviet republics.
The report identified strong interest in turnkey production systems where manufacturing expertise and services were also included in the package.
For example, Vollert Anlagenbau of Weinsberg claims that it has delivered India’s first modern pallet circuit system, used by construction company Precast India Infrastructures at its production plant in Pune, western India, outputting up to 120m² of precast concrete walls/hour per hour, as well as precast concrete floors and hollow-core slabs for the subcontinent’s booming building industry.
At a new aerated concrete factory in the Ukraine, systems manufacturer Masa of Porta Westfalica has increased daily output at the factory in Dnepropetrovsk from 1,000m³ to 1,400m³.
The IAB survey is also said to reveal a general rise in market interest in the wetcast production process where wet concrete is poured into flexible special moulds which have patterned inner faces. This pattern is retained on the surface of the concrete after curing. The technique enables companies to produce high-quality products with an individual look.
At the world’s biggest land reclamation site, the Eko Atlantic project in Lagos, Nigeria, the Great Wall of Lagos is designed to be a shield to protect the project from the force of the sea waves.
The wall, on completion, is expected to be about 18km long and should be made up of about 100,000 concrete blocks (accropocles) that weigh about 5tonnes each.
The wall will be home to the Eko Atlantic ground which will be the new habitat to 250,000 people and the workplace of 150,000 people.
The project requires so much concrete that the site has its own factory to produce it. Only recently, Finnish company
The near €40 million order has been placed by South Korea’s Hanwha Engineering & Construction, which has signed a reconstruction agreement with the government of Iraq to build a satellite city in Bismayah, near Baghdad.
Precast construction was chosen as the construction method mainly for its quality, speed and cost efficiency.
“Elematic is known around the world as a strong developer of precast technology, and we have been operating in both the Middle East and Korea for a long time,” says Elematic CEO Mats Jungar.
“This is a very significant contract for us, and it inspires us to press on with the intensive development of our business. The plant is an important reference, enhancing our position.”
The first deliveries will leave for Iraq in three months’ time, and the plant is set to be completed in 15 months.
Jungar says the company is expecting further orders.
Meanwhile, prestressed concrete specialist
The West Coast line runs from Padang Besar, on the Malaysian-Thai border, through the peninsula via Butterworth and Kuala Lumpur, to Singapore, a total distance of 350km.
Originally built by the British, improving the rail line involves double tracking and electrification, and it is currently one of Malaysia’s largest infrastructure projects.
Upgrading is being undertaken using concrete sleepers supplied by prestressed concrete specialist NSL Eastern Pretech (Malaysia). The company has a contract to supply the sleepers for 200km of the project.
To achieve the necessary quality and productivity within its manufacturing plant,
Eastern Pretech was formed in the mid-1980s as a specialist manufacturer of precast concrete elements, including hollow core slabs, planks, double tee slabs, beams, columns, staircases, walls, facades and railway sleepers.
The company’s operations manager Yeoh Peng Seah says that the decision to replace the existing vibratory pokers was taken before the railway contract got underway.
“We decided that we had to have faster and more efficient pokers for the project, and to upgrade our production for subsequent projects.
“The Atlas Copco installation represented a significant investment, because we have installed 25 units of AX40 electric pokers and 15 units of AY47 pneumatic pokers. The two systems between them cover all our vibratory concrete needs.”
The AX series is designed for medium to high-slump concrete, and although it is a fast working poker it has a low absorbed intensity that requires only small converters. The AY47 pneumatic model is said to be an economical alternative, with few moving parts and consequently long service life.
Yeoh says that the pre-stressed concrete sleepers for the 1m gauge rail line are 2m in length and have a weight of 210kg. They are designed for an axle load of 20tonnes and will be placed at intervals of 600mm along the track. Train speeds on the line will reach 160km/hour.
“We are working to Australian Standard AS 1085.14. Obviously, for a high-speed, high-capacity railway line, quality and reliability are paramount,” said Yeoh.
In total 550,000 sleepers are required for the contract.
The way the production line has been configured, and using a workforce of no more than 50, NSL Eastern Pretech is producing around 1,000 sleepers per day.
“We are progressing very quickly, and are ahead of our schedule,” said Yeoh.
The production line is working primarily with the AX40 electric pokers. The AY47 units are brought in during downtime.
“We shall of course be working on other projects in which the pneumatic units are more suitable,” said Yeoh. “But for this project we are finding that the electric model gives a superb finish, in addition to its speed of working.”
The AX40 has a frequency in concrete of 12,000 vibrations per minute, and a tube diameter of 40mm, with the AY47 having the same frequency but a slightly larger tube diameter of 47mm.
Research and development
The concrete industry is also one where wide-ranging research and development is constantly being carried out to further improve its considerable capabilities.
For example, tyre granulate from French used tyre recycling organisation
This is according to two studies (launched in 2000 and 2007) and financed by Aliapur, tyre manufacturer
In 2010, a partnership was formed between Aliapur,
As engineers around the world are busy working out ways to reduce the carbon footprint of concrete, which accounts for somewhere between 3-7% of global carbon emissions, it is reported that a Nova Scotia, Canada start-up company, CarbonCure, is already on line with a very direct approach.
This involves injecting waste carbon dioxide into the concrete-mixing process, which by nature takes CO2 and sequesters it as calcium carbonate.In another development, the lightweight aggregate (LWA)
The material has been used on some of the most high profile projects around the world in the UK, Spain, Africa and Middle East including The Shard, the Gherkin and the extensive redevelopment of St Pancras Station, all in London.
“This is an exciting development for Lytag. Our products have brought benefits to many projects around the world for more than 40 years, and we have now made these materials, and the benefits that come with them, available for construction and civil engineering projects in South Africa,” says Richard Baldry, commercial director at Lytag.
“I am excited about the opportunities to apply this material in South Africa. Looking at the great projects that have benefitted from Lytag LWA around the world, I am looking forward to helping bring similar success to some iconic African buildings,” says the business’ new South Africa agent, Johan van Wyk, based in Pretoria, Gauteng.
According to the manufacturers, Lytag LWA is commonly used in a range of construction applications including structural and precast concrete; floor and roof screeds, and green roofs, and it is said to weigh approximately 50% less than natural aggregate.
Manufactured from pulverised fuel ash, the by-product of coal-fired power stations, its use is said to reduce demand on quarried aggregate and diverts waste material from landfill.