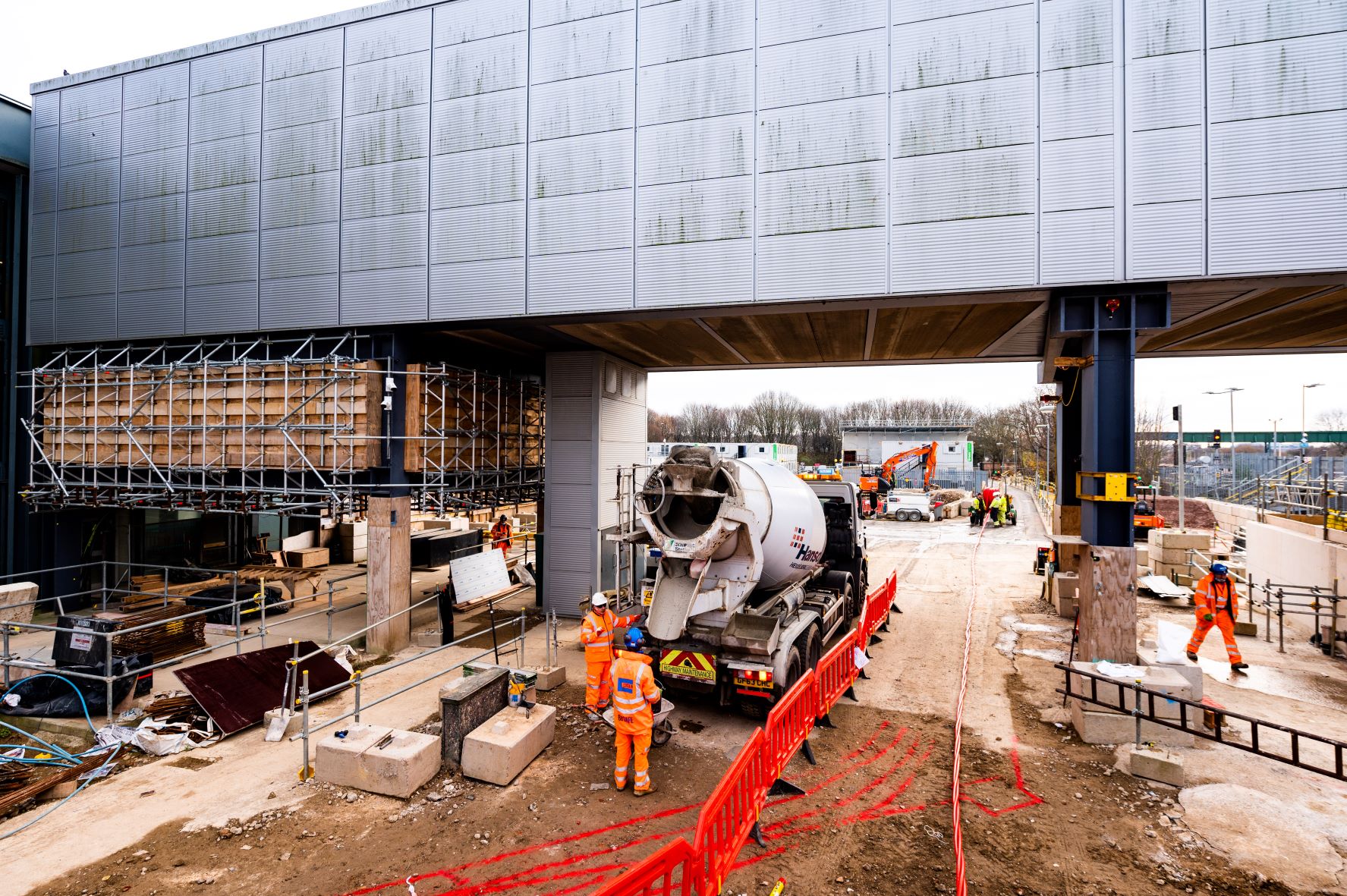
The company has supplied approximately 3,000m3 of low carbon concrete to main contractor Costain to refurbish the existing station concourse and build a second, bigger one, which will create a new entrance into the airport.
The concrete, which contains 70 per cent Regen GGBS (ground granulated blast furnace slag), provides the correct durability requirements while saving more than 500 tonnes of CO2 emissions over a standard concrete – the equivalent of 500 people making a return flight between Paris and New York.
Regen GGBS is used to replace some of the Portland cement (CEM I) content in concrete. GGBS is a by-product of the iron-making industry, and its manufacture requires less than one-third of the energy and produces less than 10 per cent of the CO2 emissions of CEM I. It also does not require the quarrying of new materials, and its use prevents material from being disposed of in landfill.
Calvin Blacker, Costain’s design manager for the Gatwick station project, said: “Hanson was chosen as our materials supply partner due to its proven track record for innovation in lowering the carbon footprint of concrete within its supply chain.
“We have worked closely together to deliver concrete that meets the challenging requirements of the project while adding to its low carbon credentials.”
Network Rail’s plans will create more space for passengers, making the journey from train to plane easier, improving accessibility and supporting a more reliable train service. They will double the space for passengers and support movement around the station and in and out of the airport.
The project is being managed by Network Rail in partnership with the Department for Transport and Govia Thameslink Railway. Gatwick Airport Ltd and Coast to Capital Local Enterprise Partnership are co-funding the project with £37 million and £10 million, respectively. Costain is delivering the project.