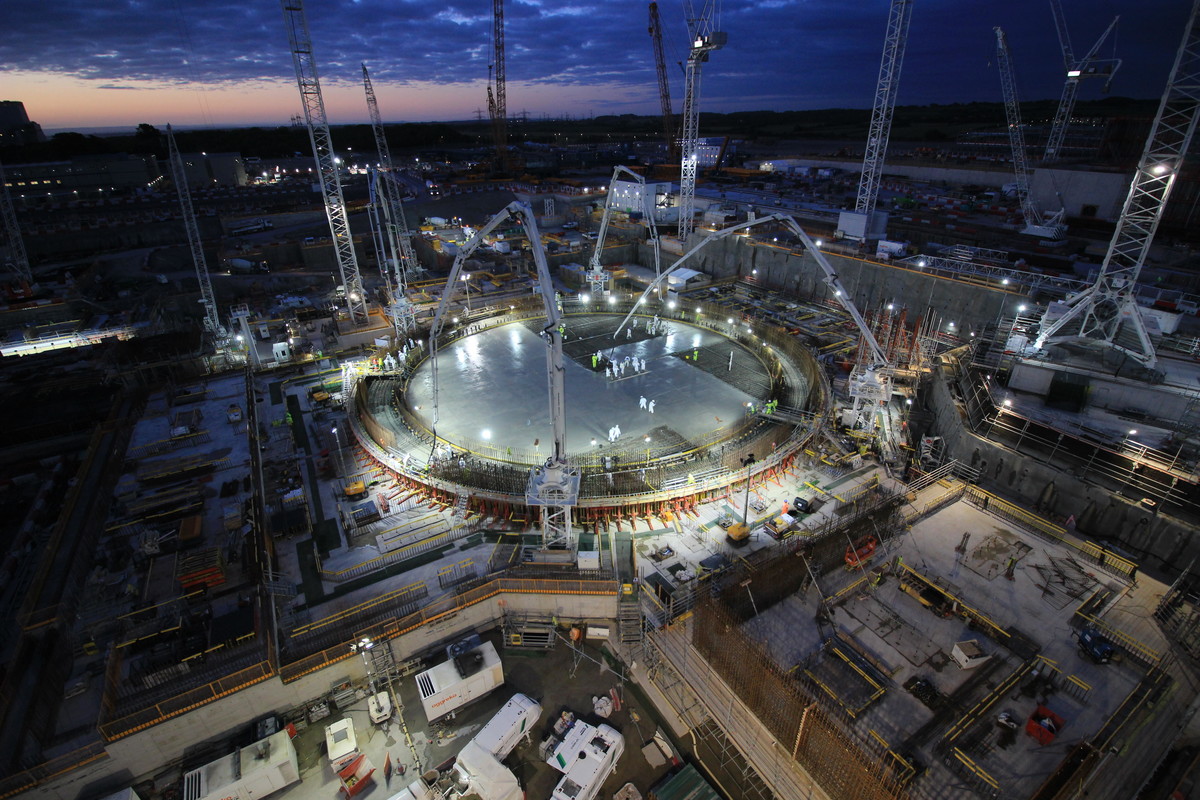
Since 2014, more than 230,000 tonnes of Regen GGBS has been supplied to EDF’s contractors from the company’s Port Talbot site in south Wales. This is sampled and checked at a dedicated on-site testing laboratory at Port Talbot and again on delivery to HPC’s site to ensure it meets the exacting technical specifications required before being used to make concrete for the project.
Adding Regen GGBS to the concrete mix provides a more sustainable alternative to other cement substitutes, such as fly ash, reducing the amount of embodied CO2. Using just one tonne of Regen GGBS in the concrete cuts embodied CO2 by around 850kg, compared to using one tonne of Portland Cement, making it less impactful on the environment.
Stewart Cameron, head of nuclear operations at Hanson UK, said: “Around 200,000 tonnes of CO2 have been saved in reaching this milestone Regen GGBS load. It is a credit to all those involved as we continue to meet the standards expected of this high-profile project.
As well as Regen GGBS, Hanson has also supplied other raw materials. To date, the company has produced just over 1,000,000 cubic metres of concrete from the client’s on-site batching plants and provided 5,000,000 million tonnes of aggregates; 443,000 tonnes of marine sand; 171,000 tonnes of cement and 150,000 tonnes of asphalt to the project.