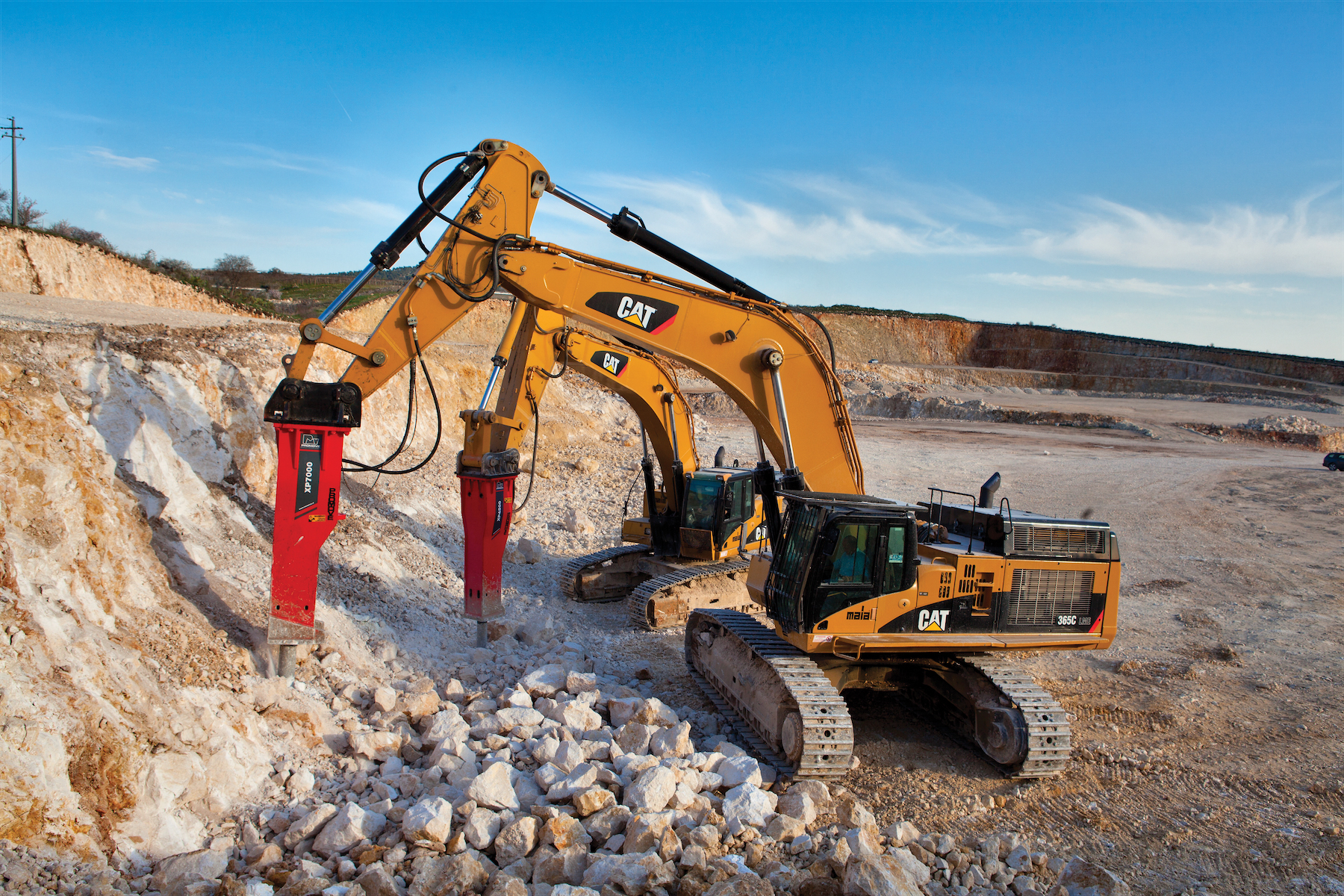
When blasting is not a viable option because of legal regulations or proximity of houses or other buildings, a large-sized excavator equipped with a heavy and powerful breaker is often the answer to get high productivity without the risk of excessive vibrations, noise and splinters dangerously flying away.
A
“When high productivity becomes a key driver, increased size of machines used on the front line is the only way to get adequate production keeping production costs under control,” says Antonio Cannao, commercial director of the Italian company, which is based in Barile, a town in the province of Potenza, in the southern Italian region of Basilicata.
“With this reference, the XP7000 shows positive features: productivity in an eight-hour shift can vary from 400 to more than 2,000m³ according to the hardness of the rock.
“A satisfying average daily production of 1,200m³ was gained in this quarry on the 1,300kg/cm2 stratified white limestone.
“The main use of this class of hydraulic hammer is primary breaking on the front line. In this application, heavy breakers can maximise the value of the combination of tool-machine-driver, delivering the highest value of production per capital invested.”
With its blank-firing prevention system the XP7000 can also be safely used for reducing oversizes.
The system prevents all Promove breakers from firing if no rock is present underneath the chisel, and therefore avoiding the energy of the piston, is transferred to the hammer itself rather than on the ground.
“Extremely dusty and hot environments (ambient temperatures inside quarries can go as high as 45°C in summer) are now exalting the technical features of this percussion giant, hitting with 17,700 joules on a 210mm chisel,” says Cannao.
“The breaker is a very important tool in the jobsite. It is always in the front line and has a complex and costly organisation behind its job: excavators, loaders, trucks, crushers and men. Its breaking performance (broken rock on the ground is money) and reliability must be at top level to keep the organisation running without costly downtimes.”
A low-pressure nitrogen chamber over the head of the piston absorbs excessive of vibrations returning energy to the percussion, and the power unit is completely insulated from the outside casing via a series of high quality and oversized polyurethane dumping elements. As a result, operator and carrier benefit from comfortable operation and substantially reduced risk of damages from excessive vibrations.
“The XP7000 fully represents Promove’s idea of ‘high quality’ in demolition equipment: the perfect combination of high breaking performance (productivity), outstanding reliability and low maintenance requirements and fast support to customers,” says Cannao.
“Thanks to accurate studies of the hydraulics’ efficiency, it requires less oil flow resulting in less fuel consumption and a lower cost per cubic metre.
“Technical features of the XP range of hammers are extended to this model, including combined gas and oil working principle; blank-firing prevention system; auto-greasing pump; adjustable frequency/energy; full square-section percussion body with tie-rods completely encased for extra-long life and reducing the risk of damages in the case of their breakage.”