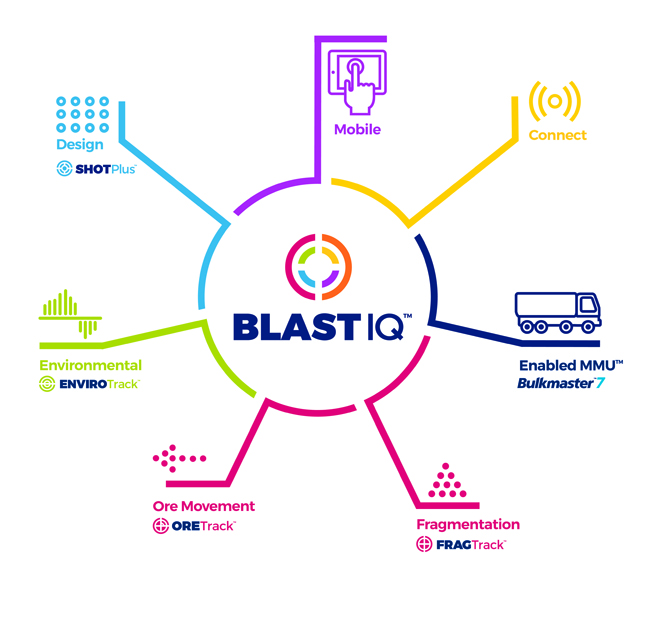
One major global quarry blasting systems firm has launched a new state-of-the-art solution, while augmented reality is being used by another leading sector name as an important education tool. Guy Woodford reports.
As one of the world’s leading providers of commercial explosives and innovative blasting systems, Orica has a vision to transform how drill and blast is used to unlock mining value, utilising digital and automated technologies to create safer and more productive blast outcomes for customers.
At the core of the company’s vision is the digital transformation of the blasting process, where rock recognition informs intelligent and dynamic blasting to deliver predictable and consistent outcomes. Orica says the downstream impact of variable and poorly controlled blast outcomes today impact as much as 80% of the total cost of operation (TCO) of a mine or quarry. The firm says this presents an enormous opportunity to deliver value to the industry with intelligent, data-driven blasting optimisation technology.
Orica has released its next generation BlastIQ Platform, its latest version of a cloud-based platform designed specifically to optimise blasting outcomes by integrating data and insights from digitally connected technologies at every stage of the drill and blast process, driving continuous improvement for customers.
Orica chief commercial officer, Angus Melbourne, describes how the company is leading the digital blasting transformation with its next generation BlastIQ Platform, saying: “Orica is uniquely positioned to unlock the value that digitally enabled blasting can deliver to the global mining industry. Building on more than 140 years of experience and innovation in blasting, we have enhanced our ability to deliver value for customers by adding world-class digital expertise and solutions to our existing suite of market-leading products and services.”
“The BlastIQ Platform will enhance blast performance and outcomes for customers by seamlessly connecting data related to the entire drill and blast process under a single platform, linking geoscientific, blast modelling and design data with measured field operations data, optimised blast delivery and advanced learning for continuous improvement.”
A complete Blast Control solution, enabled by BlastIQ, is said by Orica to deliver sustainable improvements that reduce the overall cost of drill and blast operations by eliminating rework, excess drilling and explosives consumption. BlastIQ is also said by the firm to enable greater productivity through autonomous and seamless data transfer between blast engineers and field crews. It also facilitates regulatory compliance. Orica says the information management component of the platform allows blast engineers to collate data from across the drill and blast process into a secure, centralised online location to speed up planning, analysis and auditing of blast data to meet regulatory requirements.
Optimised blast designs are developed using Orica’s market-leading SHOTPlus 3D design software. SHOTPlus, which has proven capability to manage simple and complex blast designs, integrates seamlessly with the BlastIQ Platform, allowing blast loading instructions and rules to be communicated to the field to ensure the right explosives are used in the right place and initiated at the right time, every time.
Improved in-field blast quality control and assurance is said to be achieved using the new BlastIQ Mobile device, enabling the efficient capture of auditable data direct from the bench. Blast hole condition data is captured with the BlastIQ Mobile device in real time, allowing data to be shared between operations and engineering personnel from anywhere on site, empowering rapid decision-making and better operational efficiencies.
Orica says that in a world-first for the industry, accuracy and efficiency of explosives delivery is significantly enhanced through the new BlastIQ-enabled delivery system, with loading and delivery to design now fully integrated. Orica’s Mobile Manufacturing Unit (MMU) delivery system, Bulkmaster 7, can be integrated into BlastIQ to wirelessly receive blast designs updated with near real-time blast hole quality data, while on bench. Using this data, Orica’s delivery systems load the correct explosive type and quantity according to the original design, adjusted based on blast hole condition measurement and the automated application of a defined set of rules managed by the drill and blast engineer. This innovative, direct integration with the delivery control system automates process control, thereby eliminating interpretation and product selection errors, and reduces overall loading times.
Where a BlastIQ-enabled delivery system is not available, a BlastIQ Mobile device can be used to capture and record as-loaded data during the delivery process, with the system still updating instruction to the delivery system operator based on updated processing of design and in-field hole condition measurement that precedes loading.
Rounding out the BlastIQ Control solution is the powerful insights and analytics engine incorporated into the BlastIQ Platform. Data is presented visually to the various users, delivering insights and analytics to help the drill and blast team seamlessly measure and manage blasting key performance indicators (KPIs), thereby providing the tool with which to improve blasting outcomes.
In addition to the new functionality and enhanced user experience in the next generation BlastIQ Platform, a comprehensive training, support and Customer Success Program is being introduced. The program aims to tailor each BlastIQ implementation specifically to a customer’s needs, increasing the speed of the implementation and importantly, maximising customer’s productivity, cost reduction and regulatory compliance.
Following sustained use at a selection of key pilot sites around the world, the next generation BlastIQ Platform was due to be officially released to the market from October 2018. Multilingual support will be added by the end of the year, as well as the addition of enhanced functionality to support vibration control and optimal fragmentation, by integrating third-party drilling and fragmentation data as well as predictive modelling to deliver even greater blast control.
At the
A combination of virtual reality and the real world, AR takes the form of live video imagery, which is enhanced with computer-generated graphics, immersing the user in a specific environment – such as a quarry while a blast is being conducted. The state-of-the-art technology also adds labels, captions and other helpful overlays to the user’s view, making it an ideal teaching tool.
Speaking ahead of the major industry exhibition, Ben Williams, managing director of EPC-UK, said: “Augmented reality is a way of placing a person in a situation they would not normally be able to experience. By bringing it to Hillhead, we hope to engage visitors within the quarrying environment and get a true feel for what we do.
“However, AR is not just for entertainment. It has a number of practical applications, the most important of which is training. Within our industry it is extremely difficult to realistically recreate certain scenarios, from both an economical and safety standpoint. However, AR is changing this. It is enabling us to take learning out of the classroom and into the quarry – virtually.”
Williams said that although it has limitations, AR allows students to learn at their own pace, giving them the ability to rewind training videos to help aid the retention of information.
Alongside the AR demonstrations, EPC-UK showcased its innovative EPC-Metrics service. Launched in 2017, the service, developed in partnership with Datum Monitoring Services, aims to facilitate the immediate access of event data, via state-of-the-art fixed monitoring stations, removing the need to travel to and from a monitoring location, and the time-consuming manual download of results in the field.