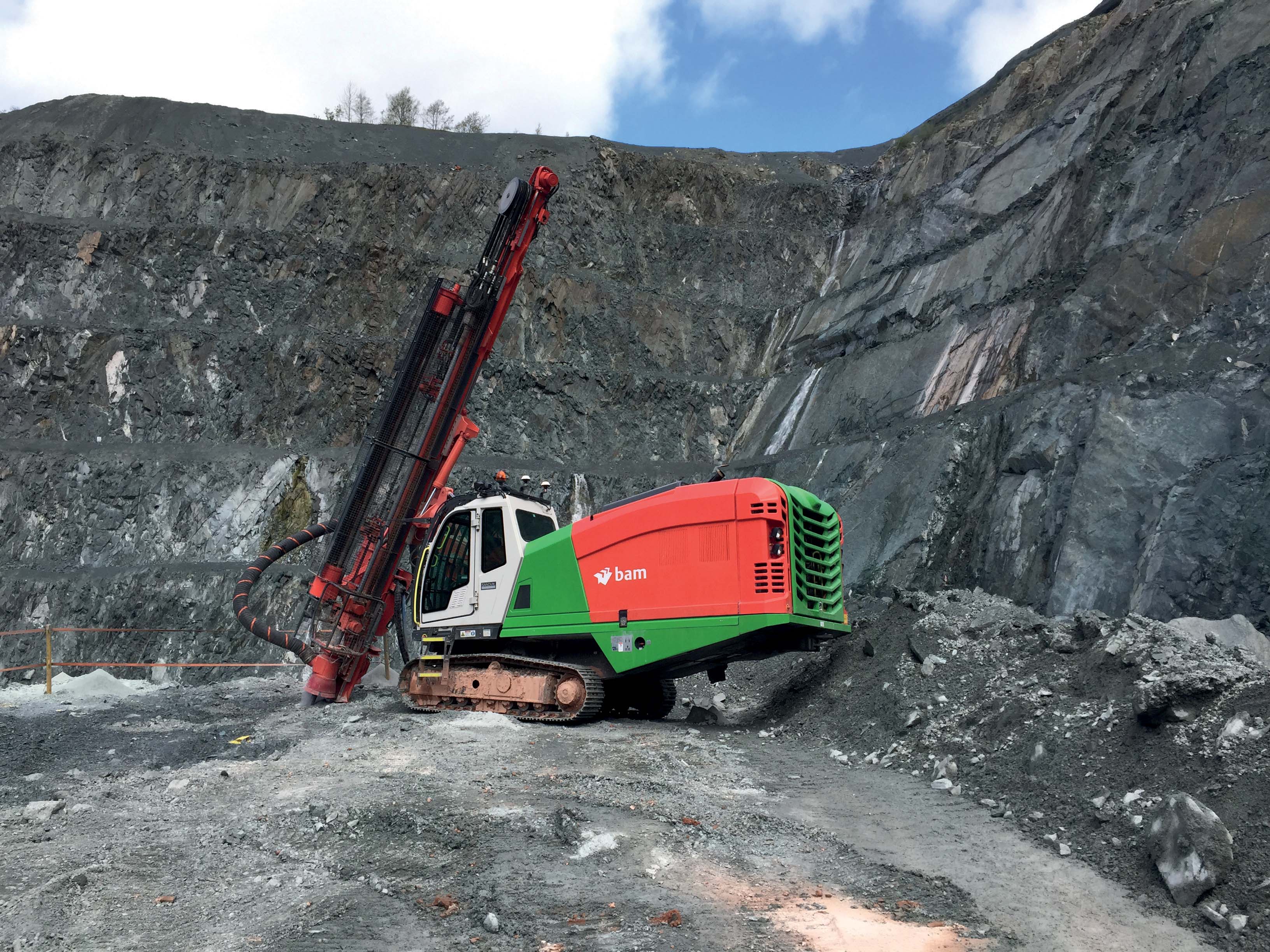
In just a few seconds, some 20,000tonnes of rock at the Quenast Quarry near Brussels in Belgium had been blasted from the quarry face and was ready for processing.
An
The quarry, run by
The process of blasting is commonplace in quarries worldwide, although alternatives are available and are being increasingly used where the conditions are right. These include hydraulic breakers, surface miners and rippers (see separate story), used with bulldozers and hydraulic excavators
Atlas Copco, which offers equipment for drill and blast and other methods, says that for operations with an output of up to 600,000tonnes/year, feasibility studies should be carried out to show whether the use of heavy-duty hydraulic breakers represent an economic alternative to drilling and blasting, and that higher annual volumes may require additional units.
Meanwhile, three new DI550 drill rigs from Sandvik Construction are said to have given BAM Ritchies’ UK drill and blast operation a major boost. The drill rigs will operate on a number of quarrying drill and blast contracts throughout the north of England and Scotland.
The DI550 is the first of Sandvik’s new generation down-the-hole drill rigs, designed for large and medium-sized quarries and contractors, “matching perfectly with 4” and 5” hammers, making the rig productive while keeping fuel consumption and operating costs to a minimum.”
BAM Ritchies, part of
Over the years the organisation has developed a reputation for assisting the aggregates industry, drilling and blasting over 40 million tonnes in the UK alone in 2014. However, its expertise and versatility allows its services to be provided in other related areas.
These include larger civils contracts which sometimes require hard rock excavation by blasting or require site-sourced aggregates. This varied and extensive work is undertaken worldwide, with the provision of solutions wherever they are required, and thus BAM Ritchies now finds itself involved in a variety of projects which include aggregate production; rock armour production; pre-split blasting for smooth slopes; underwater blasting where the rock is too hard for dredging; non-explosive rock breaking; road widening and realignment; and re-profiling and trench blasting.
“What all these operations have in common is that they are undertaken with the company’s overriding mission of creating a sustainable future by bringing engineering to life, being at the fore of its operations,” says the company.
A series of newly-won drill and blast projects located at quarries throughout the north of England, reaching as far as Ayr in Scotland, required a drilling solution and BAM Ritchies turned to
The three new DI550 drill rigs are equipped with powerful down-the-hole (DTH) hammers, being designed specifically for high-capacity rock drilling in quarries, opencast mines and construction projects. They are now working at various quarries, on a variety of materials.
“They are completely self-contained, with on-board compressors, efficient dust suppression, and a comfortable cab with ergonomic controls and excellent visibility. Meaning that from the very beginning of the design process they are focused on delivering high productivity with low life cycle costs,” says Sandvik Construction.
The DI550 itself is the first of Sandvik’s new generation down-the-hole drill rigs, designed for large and medium-sized quarries and contractors, with the operator handling drilling and the automation taking care of all machine controls.
With a 328kW diesel engine and a 24.4m³ compressor airflow at 24bar pressure, it is said to be a perfect match for the 4” and 5” DTH hammers although the rig also performs efficiently and economically with 6” hammers. In quarrying, rock fragmentation is of the essence since the rock sizes produced by a blast must be able to fit in post-process machinery such as hauling trucks and rock crushers, says Swedish company Royex.
“Normally, close space blasting patterns are used to obtain good fragmentation but this also implies an increase in a number of risks such as fly rock, rock vibration, noise and other issues associated with high explosives,” says Royex.
“As a quarry blasting technique the Royex rock-breaking system can be used both as a primary and secondary blast or rock-breaking alternative. Since the system is very precise and causes minimal rock vibrations and fly rocks, drilling and blasting operations can be done simultaneously. It also means that efficient quarrying is possible close to other structures and in cities. Royex can also be used for secondary blasting of rocks too big to be managed by the haulers or crushers.
“Royex can be used in a multitude of quarrying applications such as limestone, granite or marble quarries as it is perfectly possible to control breaking of slabs such as marble.”
The Royex rock-breaking system comprises cartridges, deployment accessories and coverage. The cartridge is based on a non-detonating propellant enclosed in a plastic housing with electrical ignition, and during ignition the burning propellant generates a fast-expanding gas volume consisting mainly of nitrogen, water steam and carbon dioxide.
The company says that if properly applied inside a drill hole, the expanding gas will expand the natural weaknesses of the rock into the nearest free face, forcing the rock to break. Another company,
Dutch company Hydraram, which also offers products such as hydraulic breakers to break rocks or concrete, says the AutoStem pyrotechnic blasting cartridges are designed to be used without stemming.
“This is a whole new revolution in the world of pyrotechnical cartridges that are used for rock and concrete breaking applications.
Besides all of the benefits that these pyrotechnical products have such as less noise pollution, less vibrations and less permits needed we have some other really big advantages,” says Hydraram.
During last year, an excavator equipped with an
The main source of raw material is the company’s gypsum quarry a few kilometres away, and blasting was used as the main mining method. To decrease blasting impacts on the environment around the quarry for its mining operations the company now uses the breaker.
Although new to the operators, blast-free mining has become the main method at the site and the daily production of the breaker unit reached the target level of 1,100tonnes.
The company invested in a
“Blast-free mining is a chain of logistics in which all the links must fit together. An efficient loading machine with a skilled operator and enough transportation capacity can increase the productivity because the breaker unit can focus on breaking the rocks. After loading, the surface is clean and levelled for the next work-cycle of the breaker,” says Atlas Copco.
“When the breaker is well positioned and stable the operator can optimise excavated rock size for the capacity of crusher and excavation costs. Minimising the breaking means higher productivity and less costs thanks to reduced fuel consumption and less wear on consumables. “Brittle stones on a thin layer are ideal for blast-free mining. When stone quality varies between the layers or there is undesired material between them, the breaker method enables selective mining.”
Maptek’s BlastLogic for blast management
“We’ve developed BlastLogic in collaboration with industry and it is relied on to track, quickly understand and act on all factors impacting drill and blast at critical stages,” says Mark Roberts. MapTek’s blast accuracy solutions manager.
“BlastLogic accelerates the process of creating and implementing accurate blast designs. At the same time it provides measurements and reports on blast execution accuracy.”
Roberts says this is achieved through real-time data integration, reporting and 3D visualisation which can be viewed by users throughout the blast design and execution process.
“Customers are integrating drill and blast design with our Vulcan grade control and Eureka drill-hole geophysical interpretation tools in order to validate the resource model and increase the recovery of minerals. Maptek I-Site 3D laser scanning systems are being used to track the accurate extraction of resources and maximise mine safety through remote survey and precision geotechnical analysis.”