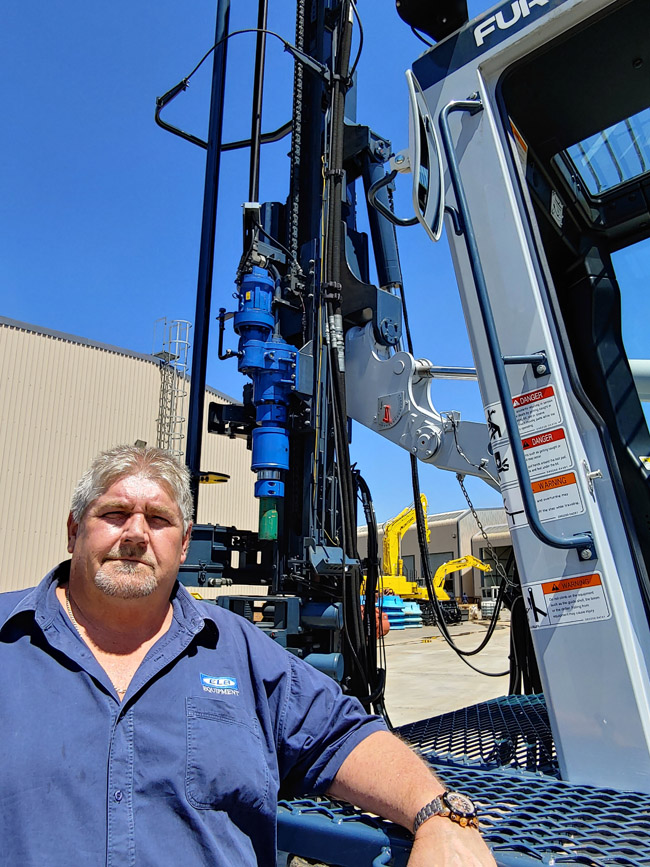
The new Furukawa DCR22 is a collaboration between a South African copper mine, distributor ELB Equipment and Furukawa, the manufacturer, which led to the development of a claimed world-beating, rugged and fast new down-the-hole drill rig that is specially designed for tough, hard rock conditions.
According to Jimmy Linton, ELB Equipment product manager for Furukawa, due to the massive strides made and success of the developments of this drill, Furukawa has actually adopted the new machine and launched it globally for countries where hard rock and tough operating conditions occur.
“The copper mine provided its requirements to us and we worked with Furukawa to begin developments. It actually took input from all quarters in terms of production requirements from engineers, operations personnel and operators to develop a machine that meets real world requirements for production, safety, reliability and long-term durability.
“The end result was good enough to pique the interest of buyers across the globe and we are proud of the fact that our collaboration was immediately industrialised and offered to the global market with the first shipment being consigned to all corners of the globe, including South Africa as the launch customer.
“Weighing in at a hefty 24 500kg the Furukawa DCR22 will be put into service with the launch customer and will in future be stocked alongside our tried and tested Furukawa DCR20 which is a smaller machine and blueprint the new model,” says Linton.
Linton explains that the new drill rig’s backbone and mechanical equipment is designed to last in back-breaking African conditions, while its engine and hydraulics have been designed to be efficient and simple for servicing and maintenance on remote sites.
However, the new CAN Bus operation transforms the rig into a highly effective and efficient production tool with semi-automated operation providing the operator with all the relevant information required for effective drilling.
With touchscreen and redesigned ergonomic controls, the Furukawa DCR22 puts the operator in full command and able to complete shift productively with less fatigue than traditional equipment. This is complimented by its powerful engine and compressor combination that provides its modern hydraulic systems the ability to cycle quickly and accurately in order to undertake drill operations more quickly.
The production related specifications make for good reading including the machines large air volume that enable fast drilling cycles due to quicker cleaning of holes (up-hole velocity). Its large track frame provides improved ground pressure for stability which means operators spend less time seating the machine.
This brings the mast into action with an effective rod changer that handles 114mm to 127mm drill pipes making it ideal for deep drilling. It can also carry eight 114mm rods of 6m four 127mm rods. On top it has a robust new rotary head for better rotation torque with 4200nm of torque for more constant power drilling. This not only assists in improving metres drilled but plays an important role to increase breakout force and as a result increases overall reliability.
From an operator’s point of view, the Furukawa DCR22 is said to be at the forefront of health and safety developments with a protected cabin that also includes reduced noise and improved interior comfort.
CAN Bus system (controlled area network) operation allows for improved data gathering to control all operations with real time drilling information and provides the operator and control room with the kind of information that is needed for better drilling and blasting.
“In the 37 years that I have been in the drilling game this is without doubt the most exciting development that I have witnessed, because it merges tough, simple equipment with high-technology controls that really dramatically improve production and efficiency.
“It is certainly the most versatile drill rig available with the ability to drill more quickly and deeper than before in operations ranging from production blast hole drilling to presplit highwall support,” concludes Linton.