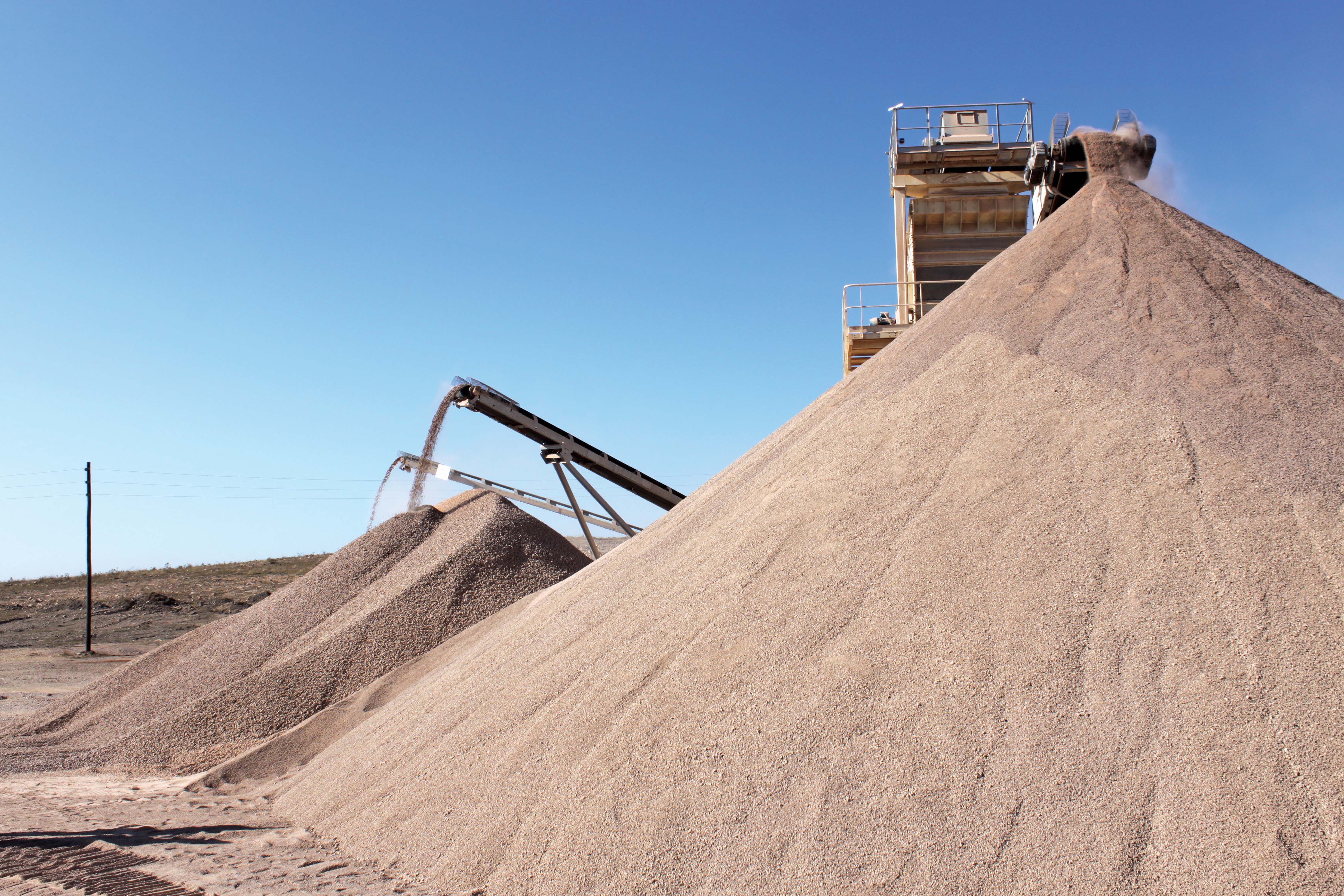
A new modular Metso crushing and screening solution is allowing a quarry company to overcome Mozambique’s tough operational environment and meet growing national aggregate demand, as Munesu Shoko reports.
Having posted a robust real GDP growth of 7% in 2013, Mozambique’s economy is on a path of exciting expansion. The unprecedented growth in coal production and the implementation of mega infrastructure projects, coupled with budgetary expansion, are projected to continue swelling growth, estimated at about 8.5% this year and 8.2% in 2015, according to the African Development Bank.
The main drivers of growth are foreign direct investment, underpinned by Mozambique’s vast natural resources, largely coal and natural gas reserves. Construction ranks among the most dynamic sectors of this growing economy, broadly related to infrastructure development and large-scale projects as the country battles its infrastructure gap. Government spending is projected to increase by 10% as the country tries to address infrastructure shortcomings.
For a quarry owner operating in Mozambique, the current scenario represents both concern and confidence. Transport projects worth a whopping US$17 billion in the pipeline, comprising better rail links to ports to cater for growing exports, as well as increased road transport network links, are turning quarry owners’ heads as demand for aggregate is rising.
However, of concern is the harsh reality of power outages that quarry operators have to contend with. While most of its electricity capacity is exported to South Africa, less than a quarter of Mozambicans are connected to the grid. National electricity utility Electricidade de Moçambique estimates power demand to grow by 15% to 20% per year in the next few years, against a generation capacity increase of only 10%.
JRC, a young quarry located about 40km south of Maputo, commenced operations in October 2013. It is located in the vicinity of 12 other quarries. Traditionally a road construction contractor for about 17 years in Mozambique, Jose Repolho, owner of JRC, decided to capitalise on the growing demand for aggregates in Maputo, primarily due to ongoing road projects in the country’s capital, and ventured into quarrying. Business is booming for quarry operators in the area, but the major setback is rampant power blackouts, which are downgrading quarries to half-a-week operations.
New plant
Facing the dilemma of having to operate two-and-a-half days a week against this rising demand, JRC’s investment in a new
The plant is producing four aggregate sizes consisting of 17A-25mm, 5A-17mm, OA-5mm and 25A-37.55mm, supplied to road contractors and concrete producers in the Maputo area. The modular plant is made up of a Nordberg VF561-2V primary feeder, a Metso C120 jaw crusher for primary crushing, a Nordberg NP1213 impact crusher for secondary crushing and a Nordberg CVB2661 four-deck screen.
The Nordberg VF561-2V primary feeder was chosen for its high capacity and the ability to process abrasive material often encountered in the quarry pit, according to Repolho. The 1300mm x 6100mm feeder accepts a maximum feed size of 900mm. Speed and stroke are adjustable for better feed control of the primary crusher. “If the crusher is running empty, the speed variators automatically change the speed of the feeders,” says Leitao.
Its long stroke capability allows for better scalping efficiency when the feed contains a high ratio of flaky material, says Paulo Seica Leitao, general sales manager of construction at Metso’s Portugal, Angola and Mozambique branch. Its individual grizzly bars are adjustable, allowing for easy and fast scalping adjustability.
The C120 jaw crusher is one of Metso’s latest launches this year, according to Eric Maricot, vice president of sales and services of Metso Southern Africa. Repohlo says this choice was necessitated by the heavy duty crusher’s ability to be mounted without bolts between the crusher and the structure. It is installed using mounting pads, which absorb vibration forces, thereby significantly lowering dynamic loads diffused to structures below. For higher production capacities, the crusher’s nip angle is located high up in the cavity, along with a linear stroke at the bottom. For safer maintenance, the C120 was supplied with lifting tools for items such as jaw dies, toggle plate and cheek plates.
To achieve its target of four aggregate sizes in one pass, JRC opted for the Nordberg CVB2661 four-deck screen. Together with an adjustable slope angle from 12° to 22°, the 2630mm x 6100mm screen’s circular motion is said to give greater screening efficiency for various types of applications ranging from primary, secondary to final screening. The machine comes with an automatic greasing unit which allows for very low maintenance, requiring one annual check. Its side plates come without any welding and huckbolt assembly. This makes it safe and reduces potential fatigue stress.
Autonomous operation
Operation of JRC’s crushing and screening plant is by means of push buttons from a centralised control room. It has two operation modes, manual interlocked or manual sensors employed for plant management, allowing it to be operated by a single person. It also has level sensors over the hoppers and crushers to detect the level of material. The quarry employs a total of 15 people, with only three manning the whole plant.
This plant forms part of Metso’s drive to introduce its Nordplant turnkey modular solutions in Africa. Maricot says that the medium-term plan is to fully automate these plants. The current operating environment in the African market is not conducive for this type of technology due to governments’ drive for labour intensive operations to address the damning high unemployment in the region.
Dr Declan Vogt, director of the Centre for Mechanised Mining Systems at Wits University in South Africa, believes that technically, mechanisation is not feasible yet on African quarries. However, he stresses that emphasis should now be on modernising, which means improved operations by using more modern means.
This may be mechanisation in the long term or just improved conventional techniques. He argues that a mechanised environment will offer a shift in jobs, from traditional lower skilled jobs to more highly skilled operator jobs. “There will also be a shift in jobs away from the quarry to the maintenance depot for the equipment,” he says. Vogt says the primary challenge to employing autonomous machinery on African quarry sites is the unavailability of skills. “We need the skills to operate the machinery, the skills to maintain it and the skills to manage mechanised operations. All these skills exist in Africa, but not in the numbers that are going to be required in the long term.” Drilling
1 x Atlas Copco ROC D7 drill rig
Loading
1 x Caterpillar 345CL hydraulic excavator
1 x Volvo L150G wheel loader
Hauling
2 x Volvo A30D articulated dump trucks
Crushing
1 x Nordberg VF561-2V primary feeder
1 x Mesto C120 jaw crusher
1 x Metso NP1213 impact crusher
Screening
1x Nordberg CVB2661 four-deck screen
Tried and tested fleet
For JRC, power cuts already pose enough challenges, and any form of further downtime through broken down equipment is out of question. For this reason, the quarry opted to invest in premium equipment brands.
JRC operates an
Drilling and blasting is undertaken once a month. To increase margins in Mozambique’s difficult operating conditions, JRC is also a drilling and blasting contractor, providing this service to the 12 quarries nearby.
A
Also key to sound operational savings is the positional efficiency of the quarry. The distance from the pit to the tipping point is 100m, while a kilometre will be the furthest haul distance when the pit expands in size. This translates into short hauling distances from the pit to the crusher. The short distances are significantly cutting overall diesel burn on site. The two Volvo A30D ADTs are achieving 10-minute cycle times, hauling from the pit to the crusher at a 100m distance.
Meanwhile, a Volvo L150G wheeled loader is used to stockpile. It is also used to load customer trucks at stockpiles .