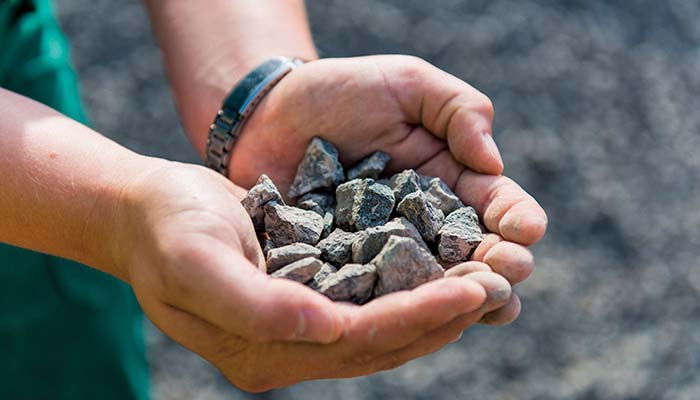
The Republic of Karelia in Russia is an origin of many mineral raw materials, such as iron ore, titanium, precious metals and diamonds. Sunsky Karier, a local producer and supplier of aggregates, is working on developing Suna field, one of Karelia’s main field deposits with natural resources.
The Republic of Karelia is a region known for its rich natural resources. At the moment, more than 50 types of mineral deposits and hundreds of mine fields and mineral occurrences are explored. Suna field is considered amongst Karelia’s most unique field deposits due to its richness in natural resources that amount to 42.7 million m³.
In 2011 Sunsky Karier purchased a
The technical solution included a complete set of Metso innovations in the field of production of crushing and screening equipment as well as its experience in electric and automation systems. The unit comprises four crushing and screening stages supplying high-quality crushed stone with the production capacity of the unit exceeding 1.5 million tonnes/year for crushed stone that equals up to 2.5 million tonnes/year for aggregates.
The Sunsky Karier site can be considered a unique production facility which incorporates the latest engineering innovations.
Among others, the site being developed fully meets the requirements for industrial and environmental safety effective in Russia. The flexibility of the crushed stone production process parameters as well as the reliability and ease of operations are the distinctive features of the site.
The unit has also an effective logistic system – the site is located in proximity to Petrozavodsk and Kondopoga cities, to a railway station and to a federal highway.
This makes the product supply smooth to users all over European Russia. The site is also located near the Metso service centre in Petrozavodsk city – specialists at the centre provide technical support for the project by responding to any questions the customer might have.
The unit concerned comprises four crushing and screening stages supplying high-quality crushed stone of 40–70mm, 25–60 mm, 20–40mm and 5–20mm grades.
1. The primary stage is represented by Metso’s Nordberg C145 stationary jaw crusher. The primary product is supplied to a storage site by a conveyor and transported for further processing.
2. The secondary stage uses a Nordberg HP500 cone crusher which feeds a Metso TS 5.3 screen, producing high-quality crushed stone of 25–60 mm or 40–70 mm grades.
3. The third stage includes a Nordberg HP4 cone crusher and a Metso TS 3.3 screen producing 20–40 mm grades.
4. The fourth stage uses a Barmac 9100 VSI crusher and a TS 3.3 screen to produce fine cube-shaped 5–20 mm grades.