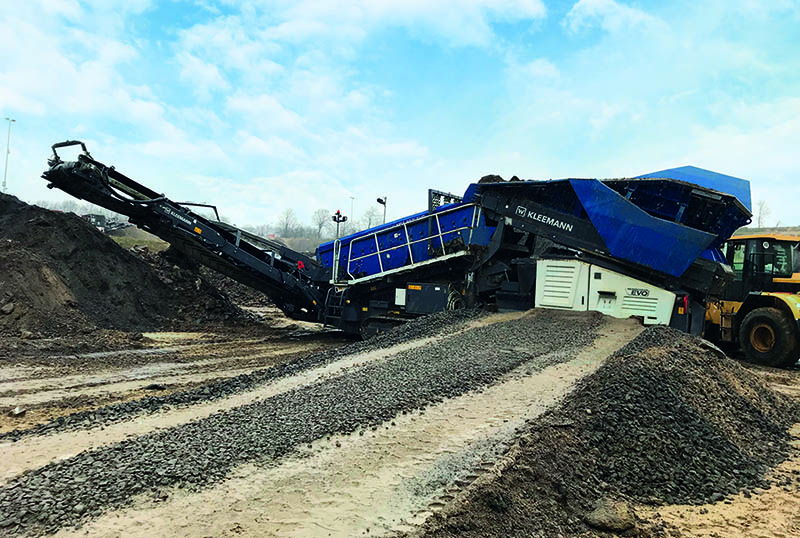
The first practical quarry site application for Kleemann's new MOBISCREEN MSS 802i EVO has been taking place over recent months at Ernst Krebs & Co.'s gravel quarry in Neumünster, Germany.
Owned and run by Caren Krebs and her son André, Ernst Krebs & Co. operates several gravel quarries between Hamburg and Kiel in northern Germany. The company portfolio includes demolition and recycling, earthwork, roadbuilding and a transport and logistics section.
Last year, André was in the market for a flexible new screening plant that could comfortably switch from processing sand and fine-grained material in a gravel quarry to handling particularly cohesive topsoil and recycling rubble and rail ballast at the company's recycling site.
André took his request to his contact partner at Wirtgen Germany, Henning Lüdtke, who he had worked with for many years. After hearing how Ernst Krebs & Co. wanted to use their new plant, it was clear to Henning Lüdtke that the new Kleemann screen for coarse elements, the MOBISCREEN MSS 802i EVO, was an ideal fit.
At the time, the machine was not yet available on the German market. So, Henning Lüdtke found an unconventional solution. He offered André a pilot series model of the plant, which André happily accepted. "Even though it was a bit like buying a pig in a poke. There were hardly any documents on the product", said the business operator, smiling.
Given that Ernst Krebs & Co. had been long-term Kleemann customers, André knew that taking the pilot screen was not really a gamble. "In our gravel quarries and our recycling, we have been using Kleemann machines for a long time. I was, therefore, fully confident that this machine would also do a good job and based on the description from Henning, I knew that this was exactly the machine we needed here.
"It's obvious that with this new MOBISCREEN, Kleemann has once again looked at what makes work more effective in practice. Everything is so much quicker: set-up times are shorter, and output is higher. All in all, it pays off."
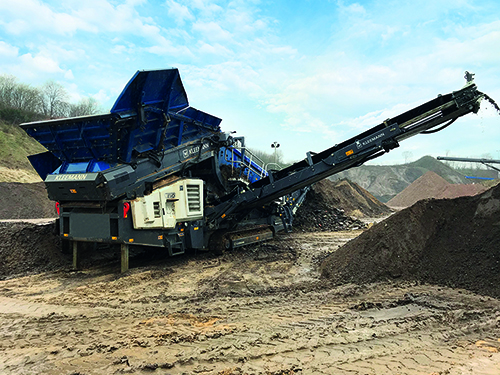
The flexibility begins with the MOBISCREEN MSS 802i EVO's large feed hopper. The hopper rear wall and the filling aids can be folded variably so that loading from different heights, from both sides and the rear, can proceed optimally. The screen surface change is comparatively easy even in the lower deck because the screen casing can be completely horizontal. The screening parameters can be adjusted precisely, and even conversion, for example, from three to two final grain sizes, is uncomplicated.
Transport from one work site to another is also fast: the discharge conveyors can be folded in without disassembling parts. Thanks to the stepless driving control, the plant can also be moved and placed precisely.
Ernst Krebs & Co. places a high emphasis on jobsite safety. André believes that the company is in the best of hands with Kleemann, with all relevant functions of the MOBISCREEN MSS 802i EVO operable from a safe distance. "Everything is set up practically and logically. For example, the display can be plugged in at different points on the machine. The user is always near the function currently being executed – a real advantage." With the new MOBISCREEN model, the blind operation of levers arranged remotely from the component to be folded is a thing of the past. Apart from the increased safety, this also simplifies operation during set-up and service. The numerous well-thought-out details all make the plant user-friendly and thus safer.
During a few months of practical testing, the MOBISCREEN MSS 802i EVO demonstrated its qualities. André continues: "One of the real challenges for us is, for example, gravel extraction. We have to deal with a lot of sand with a relatively small proportion of stone. This means that the fine-grain side discharge conveyor has a real tough job. Other screening plants would soon reach their limits. This is no problem for the new plant."
A further positive surprise for Ernst Krebs & Co. has been that the new MOBISCREEN's casing can be set over 20% steeper than many other screens for coarse elements. This guarantees a great cutting effect for separating fine material such as sand, and significantly higher output.
André is completely satisfied with the new acquisition, and he has already ordered another plant.
Metso Outotec has launched an upgraded version of Metrics, an innovative cloud-based tool for real-time monitoring of aggregates customers' Lokotrack mobile crushers and screens.
The new remote-monitoring solution will significantly improve connectivity and optimisation benefits to aggregate customers' crushing processes. The solution has been developed with distributors and customers and offers several state-of-the-art features supporting customers to achieve their sustainability and operational targets.
The new Metrics features include C02 tracking for sustainability benefits, 24/7 access to real-time data, a maintenance module, critical dashboards for utilisation, and geolocation. Furthermore, the new Metrics allows remote troubleshooting, and the user interface can be tailored to address different customer needs. New features and functions can be also updated remotely.
By combining the new Metrics with its global service footprint, Metso Outotec and its distributor partners can support customers in making data-driven decisions that impact their crushing and screening operations.
"We wanted to develop a next-generation solution that will bring quantifiable value and deliver more production hours and tons to our customers. The key to building sustainable operational efficiency is having the correct information to make decisions and select the right combination of services to lift the bar. Metso Outotec Metrics for aggregates connects mobile crushers and screens, providing increased real-time data visibility and analytics to improve availability, performance, reliability, and profitability," says Merja Tyyni, vice president, Standard Crushers, Metso Outotec.
The Metrics solution is part of Metso Outotec's Planet Positive portfolio.
In addition to the improved data transmission speed, new features will continually be developed. One currently in development is integrated mass flow measurement for tracking production and waste to help customers quantify their production performance.
Metso Outotec Metrics for aggregates generates a strong link between customer operations, product management, and product development.
"The new Metrics will enable us to take equipment features and customer experience to a new level by improving our customers' equipment's performance and increasing both uptime and the overall machine life-cycle," says Kimmo Anttila, vice president, Lokotrack solutions, Aggregates business area, Metso Outotec.
While newer Lokotrack machines come equipped with Metso Outotec Metrics, legacy equipment can, in most cases, be modernised and integrate digital connectivity equipment with a Retrofit Kit. In the initial launch phase, the Retrofit Kit is available for certain Lokotrack crushers and screens.
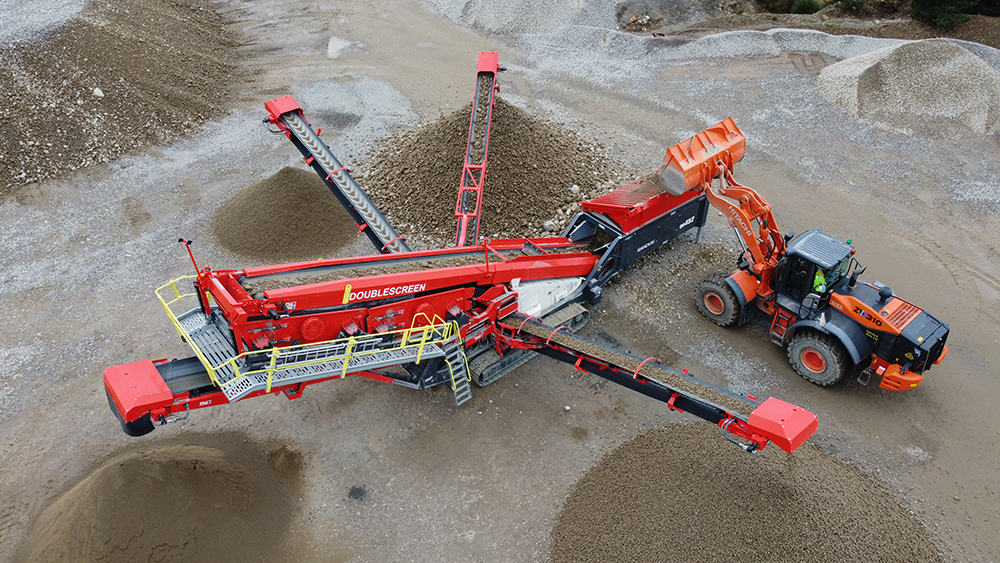
Sandvik Mobile Crushers & Screens (Sandvik) says its new QA452 mobile plant is the latest evolution of its QA Series products and three-deck Doublescreen technology. Doublescreen technology is said to typically outperform traditional screens by up to 30%, offering a tailored rock-processing solution for the quarrying, recycling & mining industries.
Featuring a host of innovations, Sandvik's new QA452 solution offers independent screen angle adjustment and hydraulic screen separation. The model also features two triple-deck inline screen boxes with equal-sized screen decks, each providing 9m³ of screening area.
Screen enhancements on the QA452 include an 11% longer bottom screen deck to extract more fines. Featuring independent screen angle adjustment, the primary screen can be independently adjusted from the secondary screen, allowing operators to optimise their throughput, screening efficiency, and product gradations. The primary screen performs as a fines extractor, while the secondary screen performs as a grader. Two processes on one plant, offering exceptional flexibility, excellent separation, accurate grading and massive throughput.
Sandvik offers a hybrid 'e' drive with electric plug-in, which means you can choose the most economical and efficient energy source for your materials-processing plant. The QA452 provides a lower environmental impact due to reduced fuel consumption, and the latest powerpack onboard offers less operating noise and low emissions. In addition, the hydraulic system has been enhanced to reduce energy wastage. Its hydraulic oil change intervals have been extended from 2000 to 4000 hours, meaning up to 50% less hydraulic oil is said to be consumed over 10,000 hours of machine usage (subject to oil sampling).
The QA452's primary screen can also be hydraulically separated to gain better access for maintenance and screen media changes. The addition of a new oversize cross conveyor means greater oversize material extraction. This cross conveyor can also be reversed to allow the plant to function like a two-deck screen with oversize and mid overs discharged together.
Each screen deck features end-tension screen media using Sandvik's unique mesh tensioning system. This means faster screen mesh tensioning and removal when you need uptime.
Sandvik's new range of WX rubber media combines the high accuracy of wire screens but with the durability of rubber, said to offer up to 10x longer wear life and up to 50% faster installation time than wire mesh. Having equal-sized panels also means the screen media is interchangeable between decks.
The QA452 comes with Sandvik's My Fleet telemetry system and seven-year data subscription as standard. This offers 24/7 fleet management, geo-fencing and remote support.
Sandvik says safety is its top priority, and the QA452 has several features as standard to improve operator and onsite protection. Dust-suppression spray bars, onboard water pump, safety pull cords and lighting mast are now fitted for extra peace of mind. AB