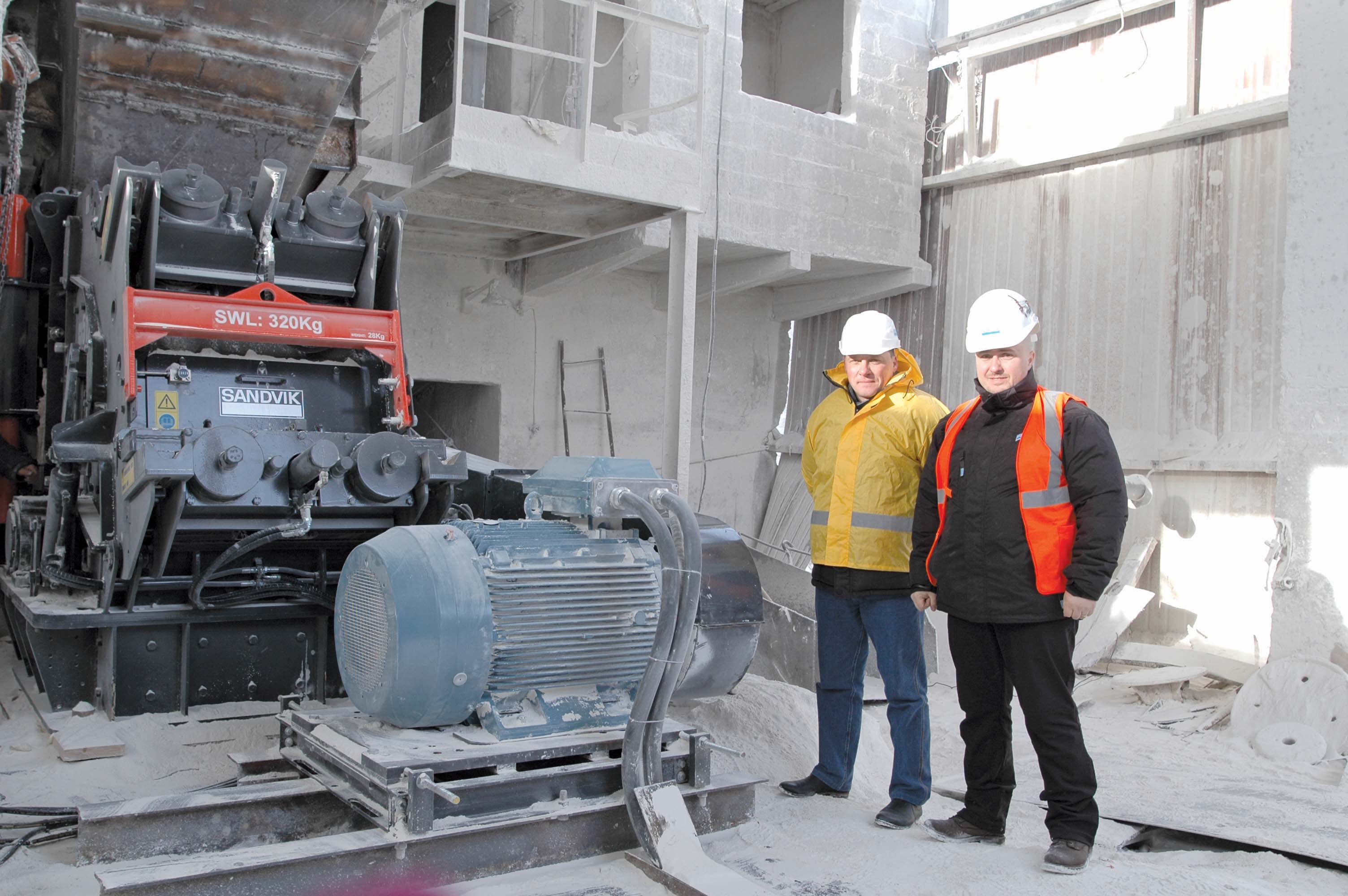
The striking Cathedral of Christ the Saviour on the northern bank of the Moskva River in Moscow, the Russian capital, is clad in it. A few blocks south-west of the Kremlin, the cathedral has an overall height of 103m and is the tallest Orthodox Christian church in the world. It joins the Russian Academy of Sciences, the Academy of Social Sciences, the Ministry of Defence, the Memorial Complex of Poklonnaya Hill, over 100 subway stations in Moscow and St Petersburg, and hundreds of other buildings throughout Russia which have been constructed incorporating Koelga marble.
Koelga settlement, Chelyabinskaya oblast, about 1,500km east of Moscow, is famous for its marble quarry, the largest in Russia, and one of the largest in the world.
Inside the huge quarry, which looks like an archaeological excavation site, the pit is much warmer than outside: the white marble reflecting the sun’s rays.
The Koelga Marble company which produces marble products and aggregates is this year celebrating its 90th anniversary, and is one of the leading Russian producers of marble micro-powder, a product with a number of uses.
The marble that is quarried at the Koelga Marble quarry is said to be similar to the world-famous Italian Bianco Carrara marble, and the company says that in order to stay at the top in its industry, Koelga Marble is constantly renewing its equipment range with the emphasis on higher productivity and quality.
To this end, it has acquired the first
Supplied by Sandvik’s Russian distributor, Quarry Service, the CI512 Prisec operates 24hours/day, and is said to have improved the cubicity of the end product and increased productivity by up to 50% while decreasing noise pollution.
Sandvik Construction recently launched the all-new range of CI500 Prisec HSI crushers, a new generation of crushers that provide customers “with a low capital cost solution, optimum performance and good cubical shape, while ensuring the lowest operating cost per tonne for a wide range of materials and applications.”
The new HSI crushers possess the ability to be configured into either a primary or secondary crusher operating mode, and with this exclusive Sandvik-patented design, offers customers adaptability.
The marble products produced at the quarry are used widely in building, construction and decoration all over Russia and, increasingly, abroad.
In fact the company is the acknowledged market leader in the production of micro-powders, producing, and selling, 40,000tonnes of such materials each month, as well as 25,000tonnes of various rubble fractions. The latter, when crushed, is used in the production of home building panels or concrete floors with marble chips.
It is due to the nature of the marble itself, and the high quality products that they are required to produce, that made Koelga Marble realise they required a new, modern, highly productive, yet adaptable and environmentally-friendly, crushing solution.
It experimented with various cone crushers but this “had proved unsatisfactory, with low production and low end product quality resulting.”
However following discussions with Sandvik Construction in Russia, as well as crushing specialists, together with Sandvik’s distributor for stationary crushing and screening products, Quarry Service, the company made the decision to buy the CI512 Prisec HSI crusher.
Scheduled and proactive service stops have meant that productivity has been increased, and operational efficiency maximised as only one operator is needed to supervise the process.
“Furthermore through the use of the revolutionary attributes of the CI512, Koelga Marble has managed to increase the quality of the end product in terms of the cubic shape, and decrease the noise pollution by significant amounts. At the same time the productivity of the production process has increased by 40-50%,” says Sergey Lebchenkov, head of innovation Koelga Marble.
Sandvik’s revolutionary all-new design of the crushing chamber is said to ensure even greater reduction ratios than have been previously obtainable.
The company is now able to produce a consistent 0-2.5mm fraction, which it says was not possible using their existing cone crushers. Koelga Marble produces different types of materials from marble chips to micro-powder, with fraction sizes varying from 5-10mm to 20-150mm.
The Prisec crushers are able to easily produce impressive reduction ratios through the use of two specially-designed curtains, which have traditionally required a three-curtain configuration crusher. As well as enhanced productivity, this means fewer wear parts and reduced maintenance.
The CI512 Prisec used by Koelga Marble is equipped with an infinite hydraulic curtain adjustment combined with a brake positioning system which relieves pressure, and setting, when uncrushable objects enter the crusher.
No hydraulic power is required during normal operation, thus saving on operating power and reducing total power consumption. Both first and second curtains are infinitely adjustable via Sandvik’s patented adjustment/braking system which is located on the cross beams of the crusher. This system gives hydraulic adjustment of both curtains, via the standard supply electric hydraulic power pack.
Crusher blockages have always historically been a problem at Koelga Marble, especially when operating in a primary mode. Removal of the blockage, with the combined downtime and health and safety risks encountered, are now eliminated with the new generation Sandvik Prisec crusher.
“Due to the exceptional features of the CI512 no stopping of the crusher is necessary, with no operator intervention inside the crusher, no heavy lifting gear required, all resulting in maximum uptime and reduced health and safety problems. This has allowed the Koelga Marble CI512 to be operated by a single person,” says Sandvik.
The rotor and hammers can be considered as the heart of the crusher, and this is why those used on the Prisec range are robust and efficient.
“Rotors have superior weight and design, essential for delivering the high inertia required for optimum crusher performance, thus ensuring stability and smooth operation during production. The banana-shaped self-sharpening hammer design helps to keep the contact heads sharper during operation, resulting in more effective shearing of the incoming material, and hence improved production.”
A key safety interlock system ensures safe maintenance of the crusher and prevents accidental opening of the crusher and inspection doors, even in multiple installations.
It also allows the ability to raise curtains during operation without stopping the crusher to clear blockages, and reset automatically to operating setting. This maximises uptime and reduces the need for heavy lifting gear and operator/maintenance intervention, thereby reducing further health and safety risks.
Through the modularised nature of the Prisec range, wear parts can be turned for maximum life/usage with the same size being used across the whole range of crushers. In addition, Sandvik’s world leading technology in the hammer and liner material composition provides options far surpassing the old industry standard of manganese, resulting in even lower operating cost per ton and the ability to operate efficiently in a variety of materials.
Extraction process
The marble is extracted by sawing the rock. First the blocks are separated and these are perfect for use as modular plates; outer and inner lining materials; monuments, and architectural elements.
The rest of the rock goes into the crusher for aggregates and micro-powder production, and for this purpose Koelga Marble uses the blocks with fractures or natural inclusions that wouldn’t be used for high-quality solid products.
When cut, marble is transported to the crusher by tippers and then fed in the crusher with screening being performed by two screens.
“In the mid-1960s the plant put into operation its first rotary crusher, but this failed very soon. Then the crushing process was entrusted to a cone crusher which has not met expectations in terms of productivity and product quality,” says Sergey Lebchenkov.
“Only in 2013 did Koelga Marble decide to return to a concept of rotary crushing when Quarry Service offered the completely new Sandvik PriSec CI512 HSI crusher, a perfect solution for primary or secondary crushing of soft rock.
“The CI512 is the first Sandvik unit purchased by Koelga Marble. Specialists of Quarry Service helped with operator training and the machine launch.”
At the quarry each shift lasts for 11 .hours, followed by one hour for unit lubrication and required maintenance. Then the crusher is back in operation.
“In order to support increased production volumes provided by the new crusher Koelga Marble has widened the conveyors and made a few other improvements in the production chain.
“Compared to previous crushers the CI512 allowed obtaining high quality materials with a good cubic shape while reducing the noise level. The overall production boost is 40-50%. Thanks to low abrasiveness of marble, wear parts do not require frequent replacement.
“Koelga Marble has registered a stable growth in production volumes from 5-10% each year. The demand for its products is always very high: that is why recurrent economy downturns do not affect annual results,” says Sergey Lebchenkov.
While Koelga Marble products are exported its aggregates and micro-powder are intended only for the internal market.
“The company is interested in raising [its interest in] the domestic economy, and it is known that Russia lacks quality marble fractions for construction.”
The crushing process is controlled by one operator who is responsible both for bulk material unloading and for the feeding. During the shift a constant laboratory control of obtained particles is performed. The closest attention is paid to 0-2.5mm fraction which is later used in micro-powder production. Depending on the raw material quality the fines are inspected from two to four times a day.
Indeed, Koelga Marble says it is aims to maximise the level of automation of the whole production process.
“The higher the automation level, the better the final product. This makes the company more competitive in the market.
“At present the company employs some 1,000 people, but with higher automation brought into the production chain the number of employees was naturally reduced. These measures are unavoidable.”
Until 2000 Koelga Marble produced microcalcite, and then the company had to think about proper waste disposal. Now the production is very close to non-waste as it uses the dust in the production of micron fractions as well.
However, health and safety is still a priority with every staff member being provided with personal protective equipment (PPE). The company has its own safety code, which is respected by each and every member of the team.
“Abrupt changes in staffing levels are not for Koelga Marble. Sometimes, when a colossal project is being planned, such as the restoration of a large memorial, the company hires third-party specialists in sufficient quantity.
“The operators at Koelga Marble have been working in the industry for decades. Their experience is sufficient to provide quality unit maintenance and organise an effective production process.”
The company says that the main goal of Koelga Marble for the future is to meet growing market demands by implementing new types of innovative equipment.
“PriSec CI512 has proved to be a reliable solution, therefore Koelga Marble sees the possibility of of purchasing further equipment from Sandvik Construction,” says Sergey Lebchenkov.