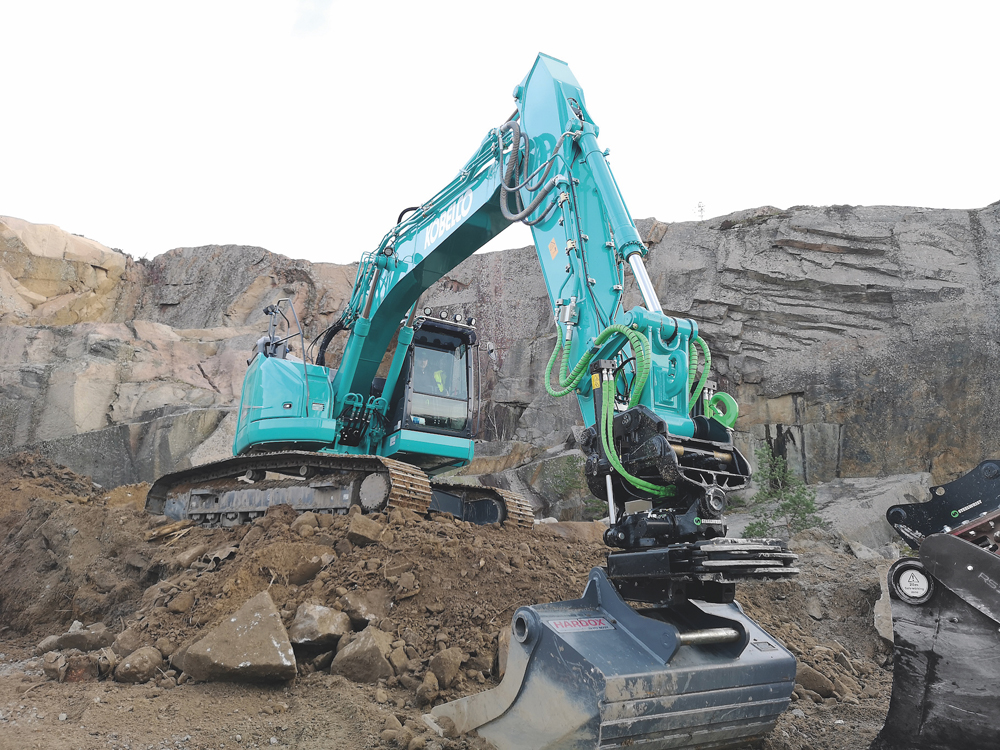
Swedish tiltrotator manufacturers Steelwrist and Rototilt have launched Open-S, which they describe as an open standard for fully automatic quick couplers for excavators.
The two companies say the standard they have jointly developed means that machine operators can combine machine couplers, tiltrotators and tools from different manufacturers which are in compliance with the standard and be confident that they will be compatible with each other.
Products that comply with the standard are to be marked “Open-S”, and the partners said they hope the first products bearing the standard will be on the market shortly.
“Open standards make everyday life easier, whether it’s plugs for electrical sockets, computer connectors or excavator quick couplers,” said Stefan Stockhaus, CEO for Steelwrist. “Open-S also builds on the independent and established standard that already exists for quick couplers, the S Standard.”
Stockhaus said that the S Standard enabled quick couplers to be used between products from different manufacturers, but did not include the oil connection. The new Open-S standard will encompass the oil connection between different tools.
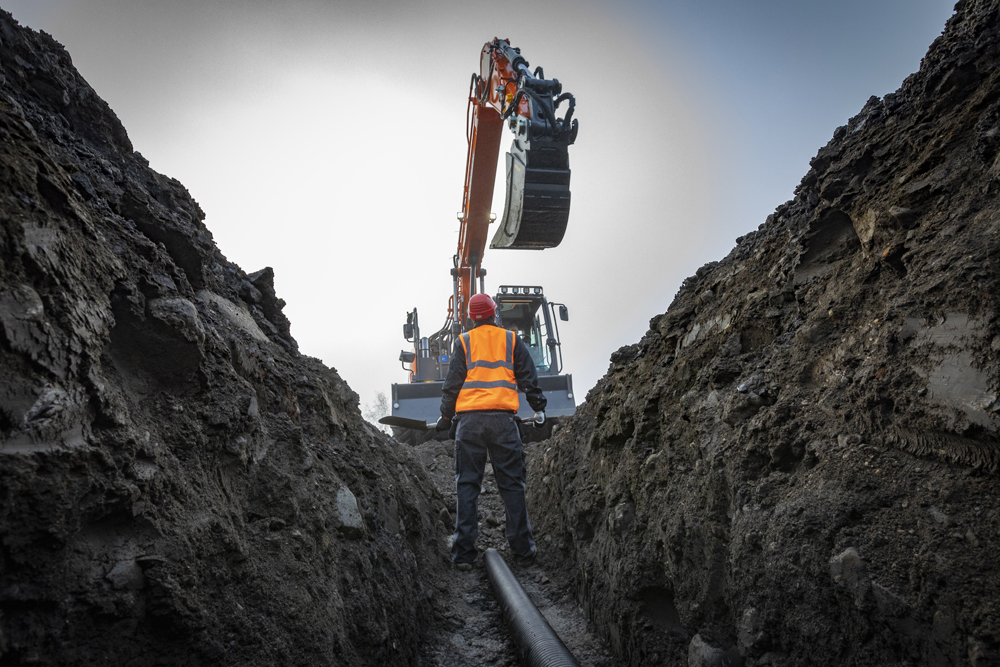
Steelwrist and Rototilt claim that together they account for around 50% of the global tiltrotator market. The pair say they would like as many other tiltrotator manufacturers as possible to join the Open-S standard, which has a website at opens.org.
Commenting at the launch of the standard in late September 2020, Rototilt CEO Anders Jonsson said: “We believe in healthy competition, where the industry’s players compete to have the best products.
“We don’t want to lock customers into a closed interface. When customers buy a tiltrotator from Rototilt, they should feel confident that any hydraulic tool that complies with the Open-S standard will fit the tiltrotator.”
The standard is based on three pillars: Freedom for end-customers to choose the preferred equipment, with reliable safety solutions, and to benefit from continued technological development.
“Because we have agreed on how to connect the products, customers can freely choose from the product portfolio from the manufacturers that comply with the standard,” said Jonsson. “It becomes clearer what fits together and which warranty provisions apply.”
Steelwrist and Rototilt say they are both seeing that more customers are adopting this type of solution, and that the Open-S standard makes it easier for contractors to take the first step towards a fully automatic quick coupler system.
Open-S is owned and managed by an independent organisation, Open-S Alliance, which in turn is led by a council of engineers from the member companies, currently Steelwrist and Rototilt. The two companies say they have had expressions of interest from other manufacturers about the initiative.
“Interchangeability is the point,” said Stockhaus. “Any reputable manufacturer who believes in the usefulness of a common standard is welcome. We are already in talks with more manufacturers who want to join in the Open-S standard.”
Sweden-based tiltrotator manufacturer Engcon has introduced additional smart features on its tiltrotators’ quick-hitch mechanism. The quick hitch had previously been adapted for installation of the detachable GRD grab cassette and SWD rotating sweeper. Engcon is now replacing nearly all the hoses in the quick hitch under the tiltrotator with a simple modular system. The company says the hose-free design reduces wear and maintenance needs, increases service life and has the flexibility of adding more hydraulic functions which makes it easier for both customer, reseller and service partner.
The new quick hitch is modular with only two hoses remaining for the locking cylinder. It will now be easier to install Engcon’s EC-Oil quick-hitch system in the lower bracket, as the hydraulic blocks are now bolted directly into a distribution block without any hoses.
The new hose-free design makes it simpler to install and retrofit hydraulic extra outlets to Engcon’s detachable tools: tool such as the grab cassette and the rotating sweeper, with the opportunity to add future tools from Engcon.
”With the new modular system, it becomes easier to maintain, supplement and replace components in the hitch. You get rid of almost all the hoses, that otherwise can be quite demanding to replace in a tight tool bracket,” said Fredrik Jonsson, development manager at Engcon.
The new design also means an upgrade to the high-flow swivel which gets larger channels for increased hydraulic flow. The manufacturer says this is a much-valued function for those who need oil capacity, for example to operate a flail mower or similar tools by choosing to ‘directly feed’ one of the extra outlets, without going through valves as before.
”Thanks to the possibility to get both the quick-hitch system and manual extra outlets in the same hitch, our customers can now choose to use their existing hydraulic tools with EC-Oil or manual couplings,” Jonsson said.
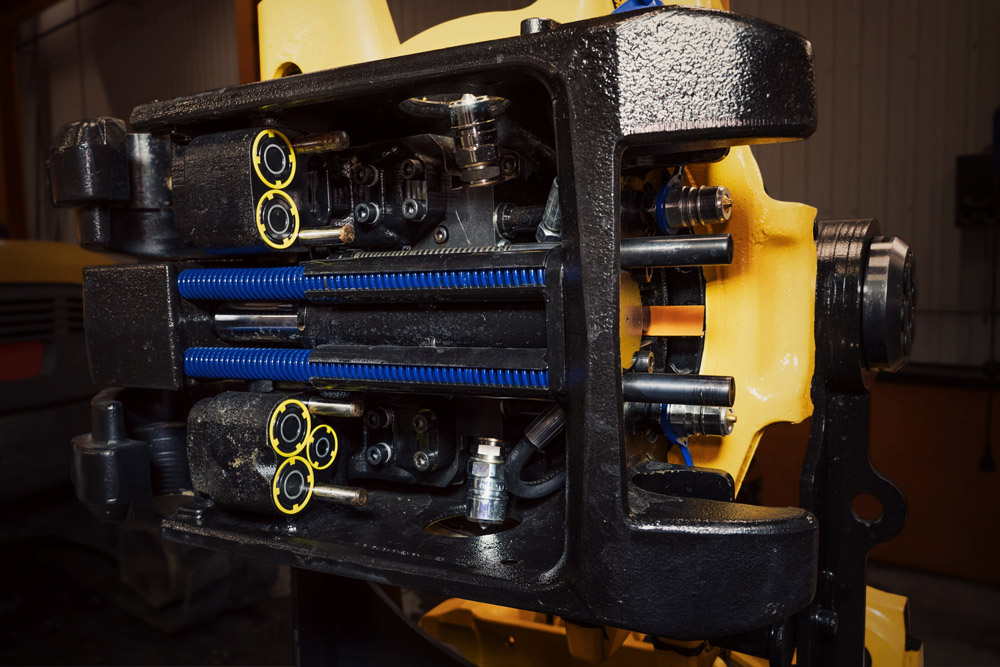
“What is unique about our system is that the customer can start with a ‘simple’ solution and then build on it themselves as and when there is a need for new tools for new assignments. It will also be very easy for the retailer to stock a ‘basic product’ that can be easily adapted to the customer’s wishes.”
Engcon’s hose-free quick hitch is available for all markets and has been developed for EC209, EC214, EC219, EC226 and EC233. Sizes EC206 and EC204 are coming soon.
Engcon has also announced that it is continuing its ‘Dig Smart. Dig Safe’ global safety initiative which started in 2019 to highlight the use of smart technology in accident prevention. The company says the aim of the initiative is to create discussion around safety issues, and to establish an industry-recognised vision of zero accidents due to buckets coming loose because of incorrect handling. The company says that its goal is a vision of zero bucket-related accidents but adds that there is a long way to go, with the issue needing to be higher on agendas around the world.
Ulrica Hellström, marketing director at Engcon, said that the launch of the initiative in 2019 had a positive impact, with as many as 38 in-depth articles being reproduced in media all over the world including the Nordics, Europe, North America and Asia.
She added that the issue has been in the spotlight in Norway, with the Norwegian Machinery Wholesalers’ Association taking an important step in the right direction. They are issuing recommendations to apply safety requirements higher than international standards. The Norwegian construction consortium Veidekke demanded, effective from January 2020, that all excavators over five tonnes must have safety quick hitches.
”A vision of zero accidents due to dropped buckets is a challenge, one that can’t be solved with the attention of just a few players,” says Hellström. “All the industry actors need to be involved. So, we will continue to repeat the campaign ‘Dig Smart. Dig Safe’ for many years to come.
“We’ll try as much as possible to make safety systems a part of our standard range. We don’t want the excavator operator to consider cost as an obstacle to investing in a safe workplace. In the autumn, we started delivering our smart locking panel and safe locking function under the tiltrotator as a standard and this can easily be compared to an automatic braking system on a car. We help the driver to do the right thing. Hopefully we can offer further developments in the spring.”
Italian crusher bucket manufacturer MB Crusher has highlighted some of the most offbeat and innovative uses of its products by contractors over the last year.
One such case was carrying a crusher into position by helicopter. With the Bavarian Alps in the background, a lodge at a 1,844m (6,050ft) summit needed to be partially demolished and rebuilt. The lodge is also the starting point of a very long hiking trail. Traditionally the demo waste material would have to be hauled downstream and discarded.
The solution arrived at was to utilise a BF60.1 MB mobile crusher to process the material and use it as road base for the surrounding paths. How did they bring it to the lodge when a helicopter can only carry a max of 1200 kg (2,645 lb)? A few of the crusher bucket’s heavier components were removed and then reassembled quickly on site.
The result was significant savings on both waste disposal and hauling fees, in addition to reuse of the resulting material directly on site.
An MB Crusher bucket was also used in the centre of a large city in Japan, where the goal was to tear down a 16-floor reinforced concrete building, surrounded by other properties and city life. Compact and agile machines were required to work on the roof of the building to demolish it one floor at a time. The demo waste was then tossed down a hole that was opened in the centre of the building, to protect the surrounding area.
The contractor chose a BF70.2 MB mobile crusher that processed reinforced concrete in a narrow space. The crusher bucket was lifted to the sixteenth floor with a crane, and due to the unit’s size and weight this task was very easy.
The process resulted in material hauling time being saved, and a significant reduction of dust and sound emissions.
On another job to build an underground drainage canal in Southern California, the contractor needed to avoid flooding a high traffic road. The long, difficult and dark tunnel didn’t allow access to the traditional equipment used on similar projects, and the use of a hammer would have caused excessive vibrations.
The solution was to use a MB-R500 drum cutter to dig a tight and long tunnel. The compact machine is packed with power and resulted in no vibrations or cracked walls, and a precise removal of only the required material.
Saving thousands of dollars while developing more than 9,000km (5,592 miles) of surface in a vast area in Montana, in the United States, a contractor had the task of preparing the site of a new residential area. During the excavation phase they ran in to large amounts of river rock.
To solve the problem a BF120.4 mobile crusher was used to break down river rock for immediate reuse as fill. This resulted in an estimated tens of thousands of dollars in savings on hauling and material handling fees while eliminating buyback expenses.
A hazardous material recycling company in Latvia needed a tool to handle large drums containing diesel fuel and paint. As a solution they used a MB-G900 grapple to easily grab hold and position the containers. This saved on both time and trucking, more work in safety and with a higher profit.
Cutter heads, flexibility and the power of attachments
Italy-based Simex offers a range of cutter heads that comprises two different product lines: double-drum cutter heads, and chain cutters with continuous cutting.
The company’s TF double-drum cutter heads are suitable for quarrying, trenching, profiling rock and concrete walls, tunnelling, demolition, dredging, finishing operations and underwater works. Marco Garofalo, engineering geologist at Simex’s application department, says they are effective where conventional excavation systems are too weak and percussion systems have little effect, due to material characteristics. “Their quiet operation allows them to be put to work near sensitive areas such as residential zones, bridges and infrastructures,” Garofalo adds.
The TF double-drum cutter heads comprise seven models for excavators from 2.5 to 70 tonnes, and all feature Simex’s patented direct-drive technology. Hydraulic power is directly transmitted to the drums and the shaft is free from loads due to the double support bearings for each drum granting high torque and high performance. The direct-drive piston motor has no lubrication points and requires no ordinary maintenance.
In addition, the double security filter system preserves the excavator and the attachment from hydraulic system contamination, while the mechanical seals on drums protect against external agents, even when the attachment is submerged into water or muddy ground.
Finally, the shape of the frame, with a reduced distance between the drums, improves the total working width. The two sides of the frame have a symmetric shape which avoids rubble and stones becoming stuck between the drums and the frame.
Simex’s TFC cutter heads with continuous cutting range are characterised by the patented central chain that allows the whole width of the attachment to mill without gaps at centre or side footprints.
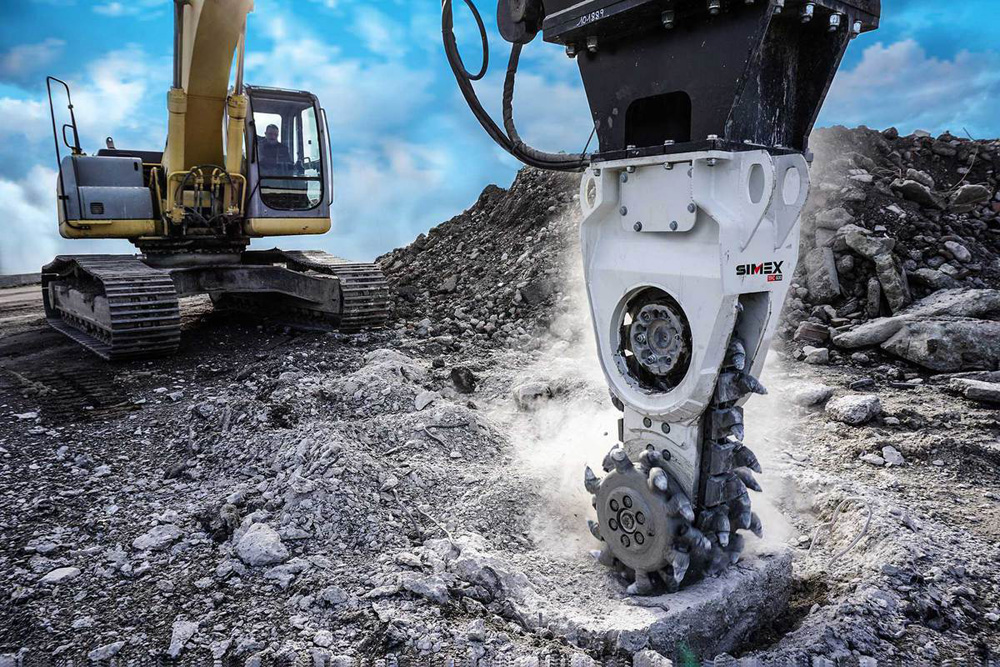
Garofalo says the benefits of this are many: “In finishing and profiling works there is a substantial saving of time along with high performances: while working on the material, thanks to continuous cutting, there is no un-milled portion left between a pass and the other.”
In the excavation process, continuous cutting allows the trench width to be kept as narrow as possible since there is no need to move the excavator boom laterally.
The Simex chain cutters with continuous cutting range comprise four models, the TFC 50 and TFC 100 for mini-excavators from 1.2 to 4.5 tonnes, and TFC 400 and TFC 600 for excavators from 6 to 12 tonnes.
“There is no doubt that milling in general is a profitable and low-impact option for excavating,” says Garofalo. “Surface mining as well proves that, whenever possible, milling rock is an appealing option. With many units deployed around the world the idea of milling rocks - as opposed to ‘drill & blast’ or hydraulic hammer -developed over the years to small-scale operations as well.
“Cutter heads, on the other hand, due to their flexibility can also be used in concrete demolition, trenching, wall profiling and many different applications.”