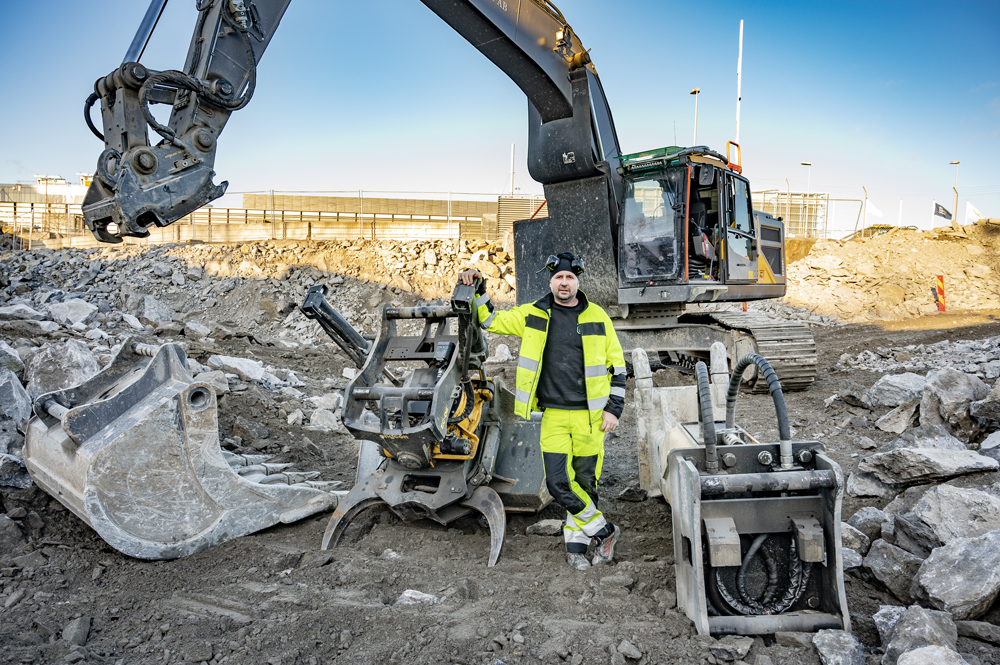
Michael Nordqvist unloads blasted rock into a construction pit at Stockholm Arlanda airport. When he gets ten minutes to spare between truckloads, he uses the time to hammer rocks that are too big to scoop up. To have time, he must be able to switch between the bucket and hydraulic hammer quickly. This made his choice simple. He equipped his 30-tonne Volvo EC300 EL tracked excavator with an Engcon QS80 quick coupler and an EC-oil automatic quick hitch system.
Terminal 5 at Arlanda is getting an additional pier. It will add capacity, increase airport flexibility and meet both today’s and tomorrow’s passenger volumes. Although the new pier will begin construction in February 2021, preparatory work is already underway.
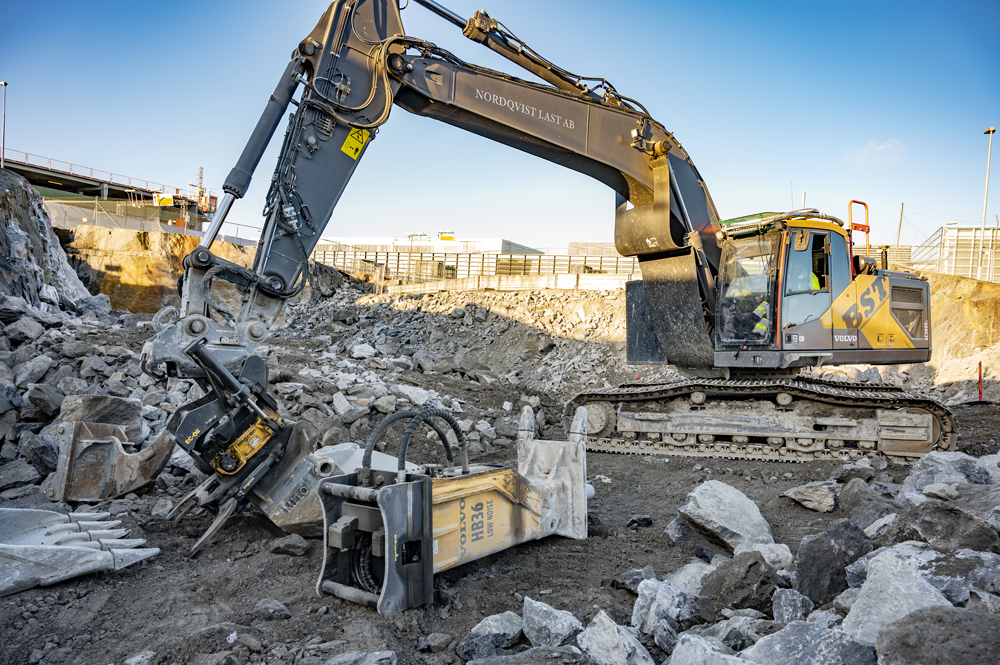
Among other things, a road down to a service tunnel must be moved 90° to make way for the new pier. The site, which is located right next to Terminal 5 at Arlanda, is surrounded by roads, and beneath it, there are service tunnels and railway tunnels. This means there is very little space. After each blast, Nordqvist sorts and positions the rock for efficient loading. He also has to keep the site uncluttered so that trucks can negotiate the confined spaces.
“If there’s a lot of big boulders after a blast, I switch to a hammer and break them up into smaller rocks before I let the trucks into the pit. This way, I don’t have to move the boulders aside.”
Because Nordqvist has to quickly switch between a tooth bucket and hydraulic hammer to make time for breaking up boulders between truckloads, he has chosen to equip his Volvo EC300 EL with Engcon’s biggest automatic quick hitch, the QS80, with EC-oil.
“I do a lot of work with hydraulic hammers. When it was time to choose a new machine, I learned all about EC-Oil from Engcon. It means I skip having to mess with spanners and heavy hammer hoses and can switch tools really quickly. It was not a hard choice to make,” confides Nordqvist.
Previously, he had to leave the cab to switch tools. If his tiltrotator was fitted, he first had to get out to disconnect hoses and cables manually before getting back in the cab again to release it.
“Then when it was time to attach the hammer, I had to get out again and mess with big, heavy hoses and screw them securely into the hammer hydraulics. Every time I changed tools, it took at least 10 minutes.”
Thanks to EC-Oil, Nordqvist now switches tools and hoses in 30 seconds without leaving the cab.
“This makes it easy to fit things in whenever someone needs help with the hammer, something I couldn’t do before. I’d spend a day loading and then another day just breaking up boulders that were put aside because they were too big.”
Also, the confined spaces in the construction pit at Arlanda mean there’s no space to set aside large boulders until later.
“Some very big rocks can be put on a truck bed, but it’s easier on both my machine and the truck if I’m able to break the rocks down before loading.”
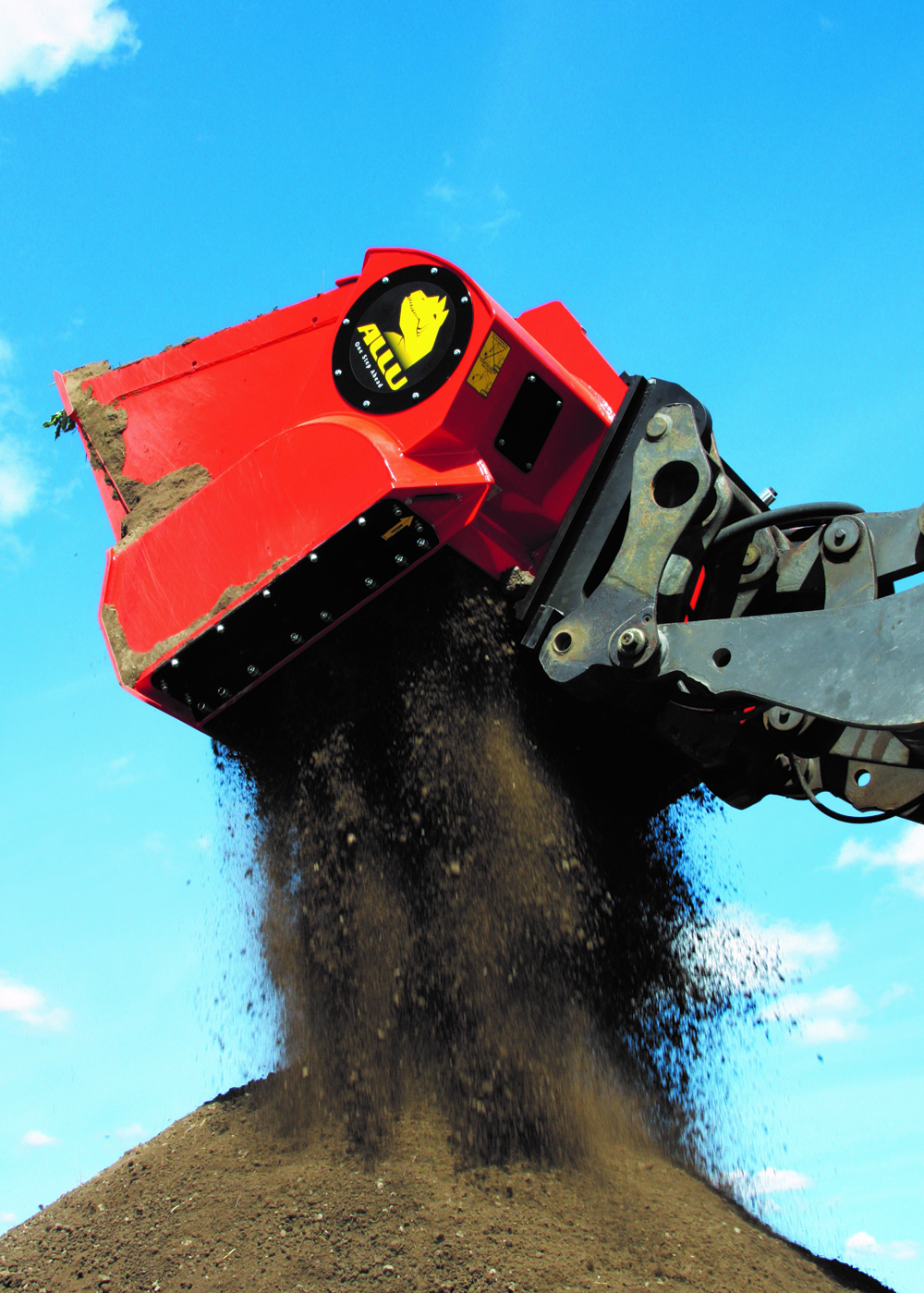
Nordqvist points out that there’s no reason to have the tiltrotator mounted when loading rock, as this results in lower lift height and lower breakout force. It also means extra weight, which affects fuel consumption and machine stability.
“But above all, it puts too much stress on the tiltrotator and risks breaking it. The tiltrotator should only be used when needed. We’ll use it a lot later in the project during rough grading, ditch excavation and supporting wall construction. That’s when it’ll come in really useful,” declares Nordqvist.
The Allu Transformer is a hydraulic attachment for wheeled loader, excavator, skid steer or similar equipment. The concept and design have been developed over many years, effectively making quarrying and aggregates production easier and more efficient. When using the Transformer, there is no longer a need to bring both a wheeled loader/excavator and a crusher on site. Instead, the Transformer screens, crushes, pulverises, aerates, blends, mixes, separates, feeds and loads materials transforming the materials accurately, efficiently and cost-effectively.
Finland-based Allu’s technology is said by the company to transform everything around it, making quarries, surface mines and aggregate plants more productive, more environmentally friendly, and more profitable. With versatility at its core, the Transformer will process soft rocks and minerals, with the new Allu Crusher now enabling hard rock to be efficiently reduced and processed as well. Available in sizes to suit excavators and loaders from eight to 160 tonnes, the Transformers facilitate the reuse of material on-site, such as difficult-to-get-to parts of the quarry. Furthermore, when dealing with secondary or pre-used aggregates, there is no need to purchase virgin material due to the recycling and utilisation of leftover materials and the generation of an income from it if it is resold as secondary or recycled aggregate.
Allu equipment is said to be focused on helping businesses transform their green credentials. This is achieved as less material is transported to the jobsite, through reusing aggregates on construction projects, for example, leading to a reduction in fuel consumption, less material to landfill and the more efficient utilisation of waste materials to support sustainability. Allu equipment helps transform any carrier - excavator, wheeled loader, skid steer etc. - into a multifunctional tool that will screen, crush, mix, pulverise and load all in a one-step operation.
Allu’s M-Series Transformers have found a real niche in processing rocks and ores for the global aggregates, quarrying and surface mining industries. They can be fitted with different drum configurations resulting in differing fragment sizes being processed with high productivity in ‘one step’. The entire process is fully mobile and can replace conventional crushing and screening plants in many cases. The M-Series has been designed to fit excavators from 50 to 160 tonnes, and wheeled loaders from 8 tonnes to 100 tonnes, benefitting users by being essentially a combined loading and processing solution.
Two examples perfectly illustrate the effectiveness of the Allu M-Series operating within the mineral and rock reduction and handling industries. Firstly, an M-Series Transformer was brought in to deal with a problem at a Scandinavian phosphate mine. The unit was put to highly effective use separating waste rock (which could be used as aggregate) from the phosphate ROM (run-of-mine) while loading in one step prior to transporting out from the mining cells for further refining. This was due to a production problem, as large ‘waste’ rock found in the ROM was causing blockages at the dump-truck unloading stations, thus causing interruptions to the flow of material. By separating the rock at the source, the problem was eliminated.
Another Nordic mine also faced dilemmas, as the mined 0-8mm crushed ore was creating problems in the iron ore pelletising process, large saturated and frozen lumps being especially problematic. This was exacerbated by the fact that no pieces larger than 100mm could enter the production chain to ensure a free flow of material. Using the M-Series Transformer has radically transformed the processing and handling of the ore and removed bottlenecks in the flow of material. Production is back to over 1000 tonnes per hour to meet the required demand for full iron ore pelletising production. The ore is no longer ‘lumped’, but rather loose and thus easily transported.
Allu technology has become very much appreciated by owners and contractors when quarrying soft rock or being used in surface mines and open-cast coal operations. Essentially the material is screened, reduced and contaminants removed. Recent developments from Allu now enable its advanced technology to deal with hard rock (as well as reinforced concrete).
The global launch of the new Allu crusher series has initially seen three crusher models be introduced for excavators in the 10-tonne to 33-tonne range. All have purpose-developed features that ease their use and optimise performance while providing easy maintenance in the field. Amongst the many features developed to benefit customers included on the new Allu Crushers is reversible crushing which reduces the potential for jamming, blockages, or obstruction with rebar while delivering greater levels of production and reducing the need for any manual involvement in the crushing process. Furthermore, the feed plate design is also built into the jaw, ensuring that the feeding function in a fully loaded chamber delivers high rates of production with minimal risk of bridging. In addition, a simple mechanical pin adjustment for output size regulation makes the entire crushing process easy and safe with quick adjustment for various output specifications.
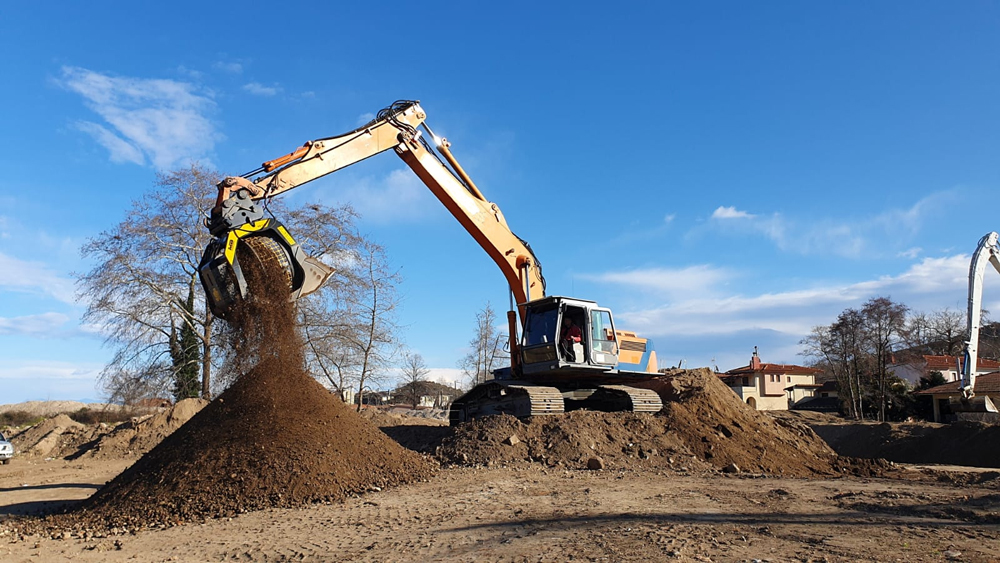
Jeroen Hinnen, vice president of sales for Allu Group says of Allu’s latest development: “By bringing this new product line to the market we will be able to provide customers with what they have been looking for. The Allu Transformer range offers unique productivity and efficiency benefits on soft rock and other materials, whilst the Allu Crusher range enables hard rock, and often troublesome demolition materials, to be effectively reduced.”
In order to provide customers with even greater levels of choice to suit their specific application, the Transformer Series also includes the compact D and DL Series. The DL Series, designed to be mounted on 12-tonne loaders and 8-tonne tractors and backhoe loaders, is ideally suited to the requirements of companies requiring limited, yet profitable, material separation, shredding, crushing, and processing. The basis of the DL bucket is the unique top screen where the screening blades spin between the top screen combs with the end material size being defined by the space between the combs. Likewise, the Transformer D Series, the ‘work horse’ of the Allu Transformer ranges, comprises a highly reliable screening bucket ideal for a variety of screening and crushing projects. Whilst their versatility sets them apart, they share the DL-Series’ use of innovative fine-screening TS drum construction with standard blades.
The DL Series has been recently updated with one notable development seeing the use of rigid TS blades for more precise size control and quick change blades for the TS blade.
Italy’s Civil Protection force recently had to tackle a problem in a valley in the north of the country. The job involved rapidly containing an escarpment, where it wasn’t possible to build reinforced concrete retaining walls due to the vertical drop of 15 metres.
They contracted the company G.M. Scavi e Miniscavi (GMSM) to build a wood and rocks retaining wall. The firm’s owner, Grudina Morris, was then faced with several logistics and timing issues. GMSM needed a lot of drainage gravel, but the nearest supplier was an hour away. Furthermore, the delivery trucks could only arrive 150 metres from the construction site. From there, the aggregate needed to be brought in with a skid steer, a process that would have taken days. Morris and his GMSM team knew the job needed to be done as soon as possible to secure the valley, so needed to identify a solution. It came in the decision to reclaim and use all of the material already available at the site, therefore eliminating procurement expenses, haulage costs and drastically reducing processing time.
GMSM got in touch with MB Crusher and bought two of the company’s attachments. By installing an MB-S10 screening bucket to the excavator they had used to dismantle the previous rotten barrier, GMSM began to select and clean the gravel. The extra grit needed they made with the aid of an MB-C50 crusher bucket reducing to size stones in the area. This was followed by a final screening stage with the screening bucket to make a state-of-the-art drainage system.
With the help of MB Crusher, the emergency job was done faster than anyone could anticipate.
MB Crusher also recently helped a Greek contractor client who was keen to limit a flood control project’s cost. Christos Tsaligopoulos’ company S.A.E.E. had been hired to install urgent riverbank protection after a river overflowed its banks twice in a short amount of time.
Tsaligopoulos opted to use gabion retaining walls as they are heavy and, as such, able to resist the river during a flood. The job specification required that the stones should be roughly the same size. However, the cost of stone acquisition on top of the cost of delivery to what was an arduous-to-reach area would have increased the project’s bottom line.
Tsaligopoulos managed to cut back on expenditure by filling the gabions with locally sourced and cleaned up stones, after using MB Crusher’s MB-S18 rotary screening bucket to separate soil from the small rocks. Once again, an emergency was dealt with by eliminating procurement expenses and haulage costs, while, at the same time, reducing processing time.