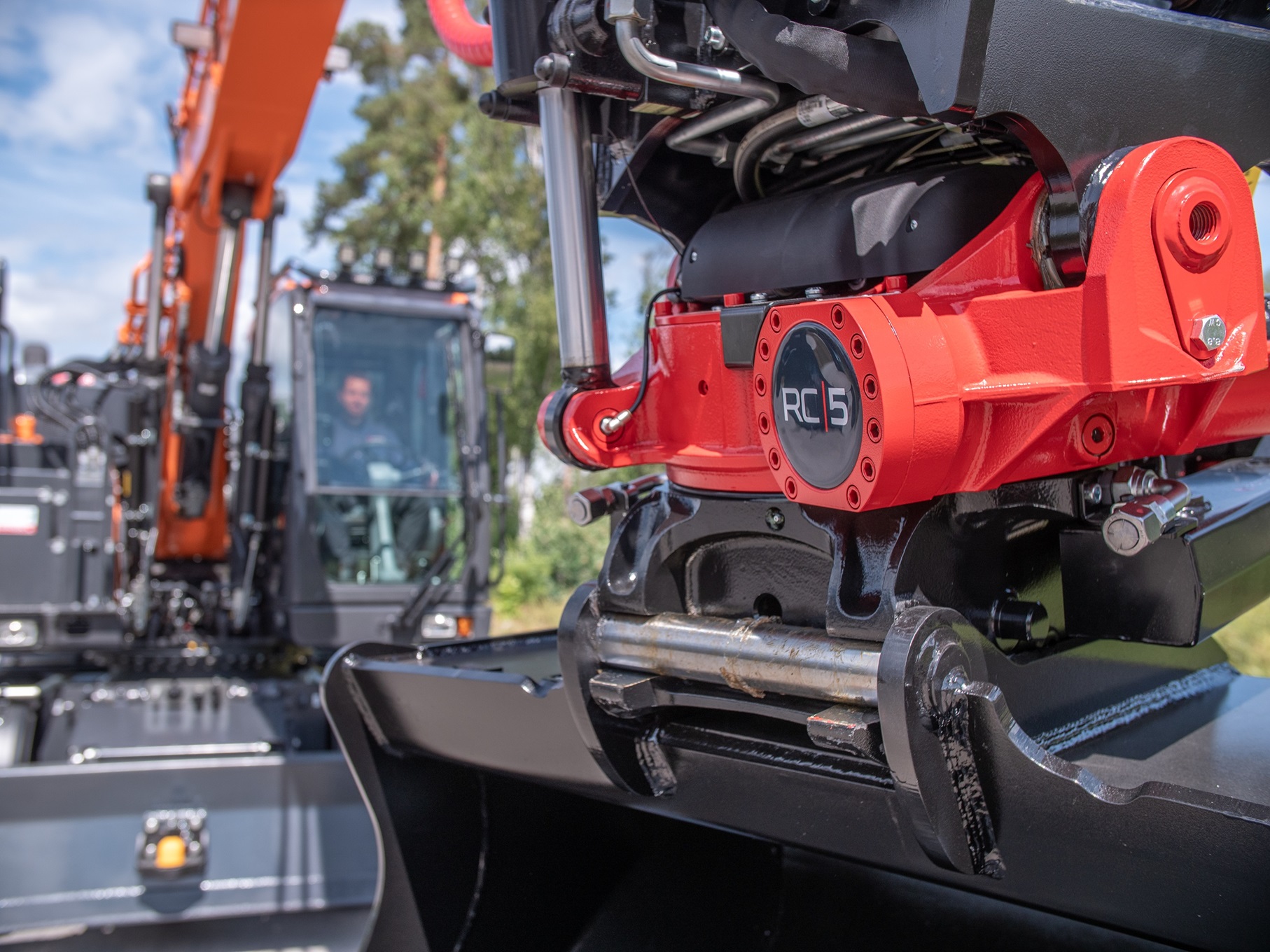
Swedish company Rototilt says working with a tiltrotator attachment can notably reduce your excavator's energy consumption while boosting your business's sustainability credentials.
"A tiltrotator makes it easier for you to work with an excavator, thanks to the increased flexibility of the work tool's movements. It enables you to adjust its angle and rotation, making it easier to carry out tasks with fewer machine movements. This saves fuel, but it has even more advantages in the long run," says Rototilt product manager Sven-Roger Ekström.
Ekström is pleased with "impressive" early tests that are said to indicate significant energy savings when using Rototilt's latest tiltrotator series.
"We call this the tiltrotator effect," he explains. "We have always known that there is a big difference between working with and without a tiltrotator. Not only do you need to use fewer machines, but you can also carry out the task at hand with fewer movements and position changes. This saves fuel and time and reduces the impact on the ground where you work. It, therefore, has a number of positive environmental effects."
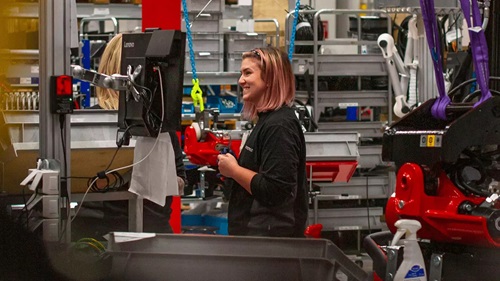
Headquartered in Vindeln, northern Sweden, Rototilt is a well-established global market tiltrotator manufacturer for industries including quarrying and construction. Ekström says the company's new RC Tiltrotator series further increases the positive impact thanks to its improved energy efficiency from Rototilt's proprietary pressure-compensated hydraulics.
"We have taken measurements comparing our previous series with the new, pressure-compensated hydraulics in the RC4-RC9," notes Ekström. "The results are impressive, to say the least. We have managed to improve the efficiency of our product, enabling it to perform the same task with reduced energy consumption."
Rototilt says the time saved by using a tiltrotator and the energy improvements in RC Tiltrotators can significantly impact a project's efficiency and energy consumption.
"Our lab tests indicate a reduction in fuel consumption of between one and two litres per hour for a 20-tonne machine, compared to our previous tiltrotator series," states Ekström. "Out in the field, the savings are affected by several factors, such as the type of machine and the job in question. In terms of diesel per year, this could mean savings of thousands of euros."
Rototilt is investing heavily in the future by expanding its factory in Vindeln, northern Sweden. The extensive investment includes the development of a state-of-the-art robotic welding facility, which will cost around SEK 35 million (€3.07mn).
"Even though the economic situation is challenging, we believe in continued growth and require greater flexibility and capacity to meet our customers' high demands. This investment is strengthening our position, enabling us to deliver with speed and precision, which is crucial in our market segment," says Anders Jonsson, Rototilt CEO.
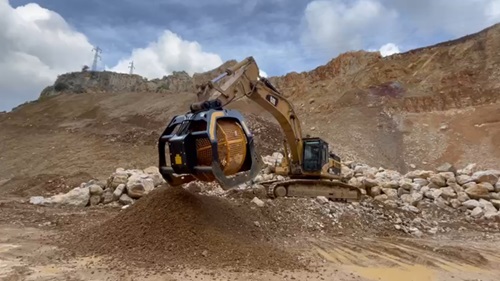
The new robotic welding facility links up handling robots and welding robots. Launched in October 2023, the project includes an expansion of the factory to 1080m², spread over two floors. The new welding section will be ready for final inspection in May 2024.
"The global situation is placing new demands on us, and we are dealing with this while attempting to develop our business. We are now creating the conditions to improve our delivery precision, which we are constantly focusing on since we know how important it is to our customers," says Jonsson.
Rototilt's production facility is powered by fossil-free energy, and the extended factory is being built with an advanced energy-recovery system. The heat from the welding process is recovered via the ventilation system, reducing energy consumption and the climate footprint. The factory's primary heating source is district heating, produced from local biofuel.
"The new welding facility will contribute to a lower proportion of goods transport. All the contributing elements are important, and we are constantly thinking about reducing our climate footprint," says Ida Skaring, sustainability strategist at Rototilt.
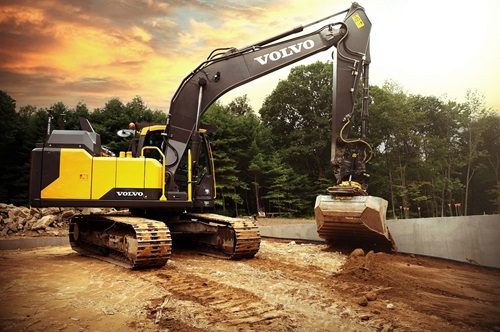
During the autumn, Rototilt has also invested in one of Sweden's largest private charging parks, with 178 vehicle spaces outside the factory in Vindeln. All the parking spaces have sockets for engine heaters and electric car charging.
"We are proud to create a greener workplace and support the ongoing transition to sustainable travel. Half of our employees commute from other municipalities, and this development is making it easier for anyone who drives an electric car to get to the workplace. It will hopefully also encourage more people to switch to an electric car. Our aim is not only to offer innovative products but also a production facility that aligns with the highest sustainability standards," says Jonsson.
engcon, another leading global manufacturer of tiltrotators, has secured an important order in the DACH region, including Germany, Austria, and Switzerland. Worth SEK 12 million (€1.06mn), this order marks the first step of collaboration with ZD – Solution KG, engcon's new distributor in the region. The primary focus of this partnership is the sale of tiltrotators.
"This is a strategically important order for us," states Krister Blomgren, CEO of the engcon Group. "The partnership with ZD – Solution KG allows us to expand our market presence in Germany, Austria, and Switzerland without creating unnecessary challenges to our sales and production lines. Taking this crucial initial step in that direction is a positive indicator for the future."
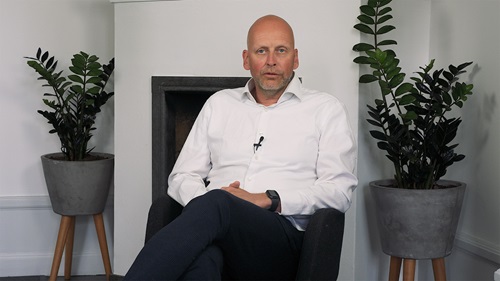
The collaboration agreement was signed in October 2023. Under this agreement, ZD – Solution KG commits to purchasing engcon's tiltrotator bodies and installing them on quick couplers not offered by engcon, such as Lehnhoff, Likufix, System Martin and other widely used couplers in the DACH region.
At its Sicilian quarries, the Bruno Group's Inerti Bruno and Nord Sud Impianti companies process limestone and soil using MB Crusher's MB-S23 screening bucket attached to a Cat 345 excavator. The MB-S23 is solving a big problem by removing clay waste from some of the extracted rock, allowing more material to be efficiently processed on-site. This saves time and cost and eliminates potential damage to the fixed limestone-processing plant.
The MB-S23 is thought to be the largest screening bucket in the world. It is well suited to 35-tonne-plus excavators and ideal for use before or after crushing. MB Crusher says the MB-S23 will reduce crushing time by up to 60% and offers convenient on-site screening of any natural materials (quarry residues, dry soil, and river stones).