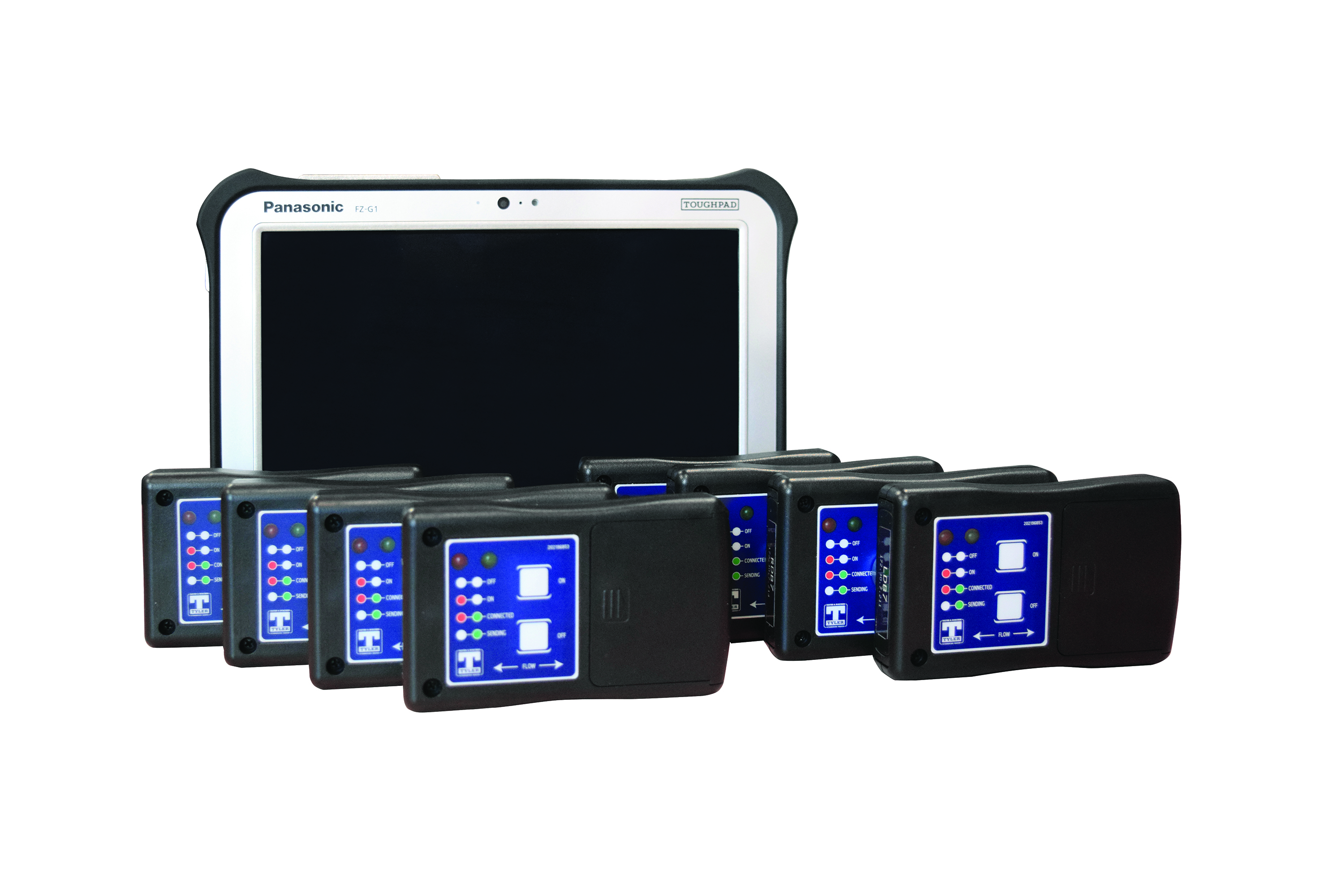
Vibrating screens work hard. Like all equipment, they require proactive maintenance, wear part replacement and periodic upgrades to more efficient technology to maintain reliability and productivity. Duncan High, processing equipment technology division manager, Haver & Boecker, gives some pointers on how well-maintained vibrating screens can help you make the most out of your aggregates materials processing year.
Take the screen’s Pulse
Conducting a vibration analysis, such as
Some manufacturers send technicians to a site to conduct vibration analysis to assess the ‘health’ of a vibrating screen and screen media. They then follow up with recommendations for improving the vibrating screen’s performance, including ways to reduce maintenance costs.
Leasing options are sometimes also available, making this productivity-enhancing technology available to every size operation.
Pay attention to the cross beams
Consider lining cross beams with polyurethane to extend their life and the life of screen media. Polyurethane protective liners reduce the impact of passing material and prevent harmful wear, a simple step that will result in an extended equipment service life.
Haver & Boecker’s Zip Guard, for example, is designed for maximum longevity. It’s simple to install on a vibrating screen’s cross beams and can be removed just as easily. The half-inch-thick polyurethane material does not adhere directly to the cross beam like its rubber counterparts, making it much easier to check the beam for deterioration and cracking.
Plan ahead for faster screen change-outs
Upgrades to speed up screen media change-outs are another way to improve productivity. Quick-tensioning systems, such as Haver & Boecker’s Ty-RaiI, solve an age-old problem of time-intensive screen media change-outs by cutting replacement time in half, providing a fast return on investment (ROI).
As producers know, replacing tension rails is a notoriously meticulous process, requiring the removal and replacement of many pieces of hardware per screen section. Washers or bolts are often dropped or lost in the process, which adds to downtime and parts costs. Some quick-tensioning systems feature each rail as a single, removable piece. The bolts remain attached to the rail and the angle boxes stay fastened to the vibrating screen.
Contact a vibrating screen manufacturer for information on these types of products or other ways to improve screening profitability. Taking time to assess the operation and make improvements can result in a more productive and profitable 2018.
About Duncan High
Duncan High is the division manager of processing equipment technology at Haver & Boecker Canada, formerly known as W.S. Tyler. His 27 years of experience with the company helps him lead a team focused on providing customers processing equipment solutions that help them get the highest possible production rates and reliability.